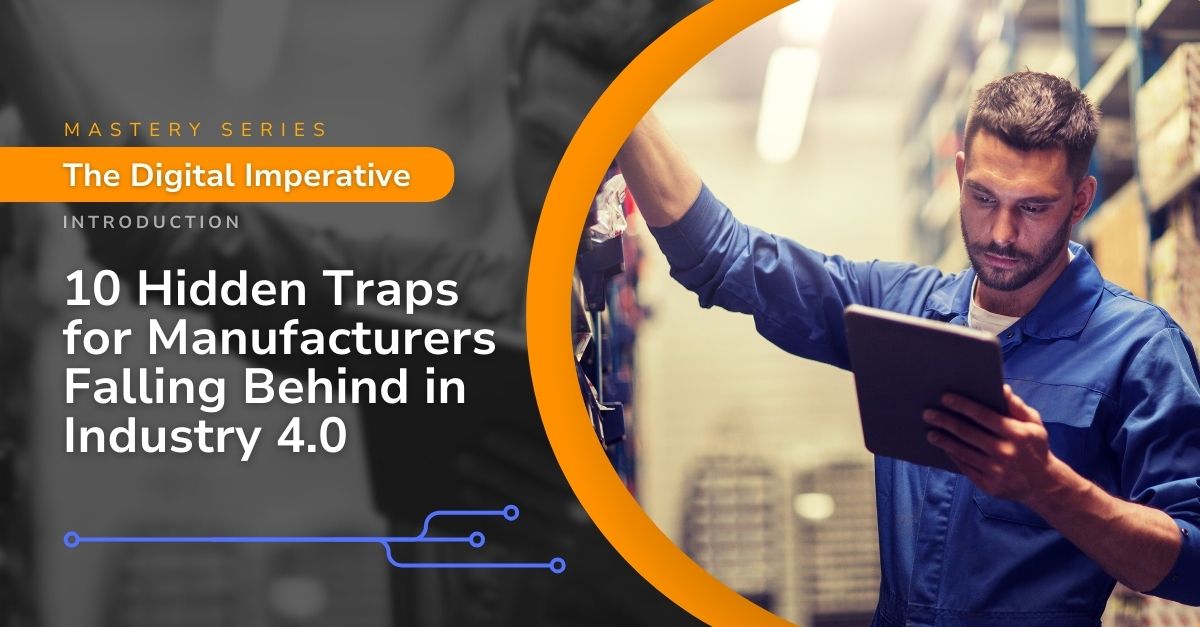
The manufacturing landscape is amid a profound transformation driven by the convergence of digital technologies and physical processes.
We are now in the era of Industry 4.0, where smart factories, interconnected systems, and data-driven decision-making are reshaping how we design, produce, and deliver goods.
What is Digital Transformation?
Digital transformation in manufacturing goes beyond adopting new technologies. It’s a fundamental shift in how a company operates, leveraging digital tools and data to optimize processes, enhance efficiency, drive innovation, and generate new customer value. This shift touches every value chain stage, from product design and development to production, supply chain management, and customer service.
Despite its clear benefits, many manufacturers struggle to fully capitalize on digital transformation. According to IDC, while 70% of manufacturers have implemented or plan to implement a digital strategy, less than 30% have fully scaled these initiatives. This gap presents serious risks for those who lag behind.
The State of Digital Transformation in U.S. Manufacturing
In the U.S., manufacturers are making progress, but they are doing so cautiously. A 2023 McKinsey report found that only 20% of industrial companies could be considered “digital champions”—those that have achieved significant operational and financial benefits from digital initiatives. In contrast, countries like Germany, a leader in Industry 4.0 adoption, boast a much higher percentage of digital champions. U.S. manufacturers must accelerate their digital efforts to remain globally competitive.
Here are ten critical but often overlooked traps that manufacturers face when they fail to embrace Industry 4.0:Neglecting digital transformation has far-reaching consequences, many of which may not be immediately visible. Here are ten critical but often overlooked risks manufacturers face when they fail to embrace Industry 4.0:
1Inability to Attract and Retain Younger Workers:
Gen Z, the first fully digital-native workforce, expects a tech-driven work environment. According to a 2023 study by The Manufacturing Institute, 77% of Gen Z workers consider technology a critical factor in choosing an employer. Manufacturers who fail to modernize their workplace risk losing out on this crucial talent pool, stifling future growth and innovation.
2Increased Risk of Cybersecurity Breaches Due to Legacy Systems:
Legacy systems, often outdated and unsupported, pose significant cybersecurity risks. A 2023 IBM study found that manufacturers face an average data breach cost of $3.86 million, making them a top target for cybercriminals. Companies that fail to upgrade to more secure, modern IT infrastructure are more susceptible to cyberattacks that could disrupt operations and damage their reputation.
3Missed Opportunities for Predictive Maintenance:
Predictive maintenance powered by data analytics can substantially reduce downtime and maintenance costs. A study by PwC shows that predictive maintenance can reduce maintenance expenses by 12% and increase equipment uptime by up to 9%. Manufacturers who fail to adopt these technologies will suffer from more unplanned downtime, leading to increased costs and lost productivity.
4Ineffective Collaboration and Communication:
Collaboration across multiple locations and departments is crucial in today’s globalized manufacturing ecosystem. Cloud-based platforms and digital collaboration tools eliminate silos and foster more efficient communication. A McKinsey report estimated that poor communication costs the average company over 20% in lost productivity, a loss that could be mitigated through the right digital tools.
5Slower Time-to-Market for New Products:
Technologies like digital twins, virtual prototyping, and advanced simulation software enable companies to shorten product development cycles. For example, General Electric (GE) used digital twin technology to cut the development time of its jet engines nearly in half. Manufacturers who fail to invest in these tools risk missing critical market windows and potentially losing out to faster-moving competitors.
6Limited Ability to Leverage Real-Time Data for Process Optimization:
Real-time data from IoT sensors and smart machines is a cornerstone of Industry 4.0. This data can provide actionable insights to identify bottlenecks, optimize machine performance, and improve overall efficiency. A World Economic Forum report highlights that real-time analytics can boost manufacturing productivity by up to 25%. Manufacturers without the ability to harness this data will miss out on valuable opportunities for continuous improvement.
7Increased Difficulty Complying with Evolving Regulations:
The regulatory environment for manufacturers is growing more complex, with stringent requirements around sustainability, safety, and product quality. Digital compliance management solutions can help manufacturers navigate this evolving landscape. For example, the Environmental Protection Agency (EPA) suggests that using digital tools can reduce compliance costs by up to 15%. Companies that fail to adapt to shifting policies risk falling behind or incurring penalties for non-compliance.
8Inefficient Inventory Management and Increased Carrying Costs:
Optimizing inventory levels through digital systems can drastically cut carrying costs and minimize stockouts. A 2023 report by the National Institute of Standards and Technology (NIST) found that real-time inventory management could reduce excess inventory by up to 25%, freeing up significant working capital. Manufacturers who rely on outdated manual systems will experience inefficiencies that eat into profitability.
9Limited Ability to Offer Customized Products and Services:
Today’s consumers increasingly expect personalized products. Digital platforms and technologies enable mass customization, allowing manufacturers to cater to specific customer preferences without sacrificing efficiency. A 2023 study by Capgemini found that manufacturers embracing customization see up to a 10% boost in revenue. Those who fail to adopt this approach will struggle to compete in a market where personalized experiences are in high demand.
10Failure to Scale Pilot Projects:
Many manufacturers launch promising digital transformation pilots but struggle to scale them enterprise-wide. This often results from a lack of cohesive strategy, insufficient investment, or resistance to change, leaving successful pilots isolated and unable to deliver full value. To avoid this, companies need a clear roadmap prioritizing scalability, with leadership support and resources to turn pilot successes into broader operational gains.
The Path Forward: Embracing Digital Transformation
The risks are clear, but the potential rewards are equally compelling. Manufacturers that embrace digital transformation are not just avoiding pitfalls, they are also better positioned to enhance operational efficiency, optimize the supply chain, and foster innovation. By leveraging Industry 4.0 technologies, they cannot only stay competitive but also thrive in a rapidly evolving market.
Ready to Elevate Your Manufacturing Operations with Real-Time Data and AI-Driven Insights?
At POWERS, we don’t just offer consulting services—we provide a comprehensive solution for manufacturers eager to thrive in the digital era. We specialize in guiding you through the complexities of digital transformation and optimizing critical areas across the value chain to drive sustainable productivity and profitability.
DPS is the culmination of decades of manufacturing expertise combined with the latest AI-powered technology designed to empower your operations like never before.
Here’s what POWERS DPS can do for you:
- Complete Visibility: Monitor production in real-time, identify inefficiencies, and streamline operations with intuitive dashboards and analytics.
- Enhanced Collaboration: Foster seamless communication across your team with instant data sharing and collaborative insights that drive continuous improvement.
- Data-Driven Decision Making: Utilize advanced AI to predict challenges, optimize scheduling, and make smarter decisions at every stage of production.
- Boosted Productivity and Efficiency: Minimize downtime, maximize resource allocation, and unlock your workforce’s full potential.
Schedule a free consultation with a POWERS expert and discover how our proven methodologies and cutting-edge technology can help reduce costs, optimize production, and achieve sustainable and scalable growth.
- Speak to an Expert: Call +1 678-971-4711 to discuss your specific challenges and goals.
- Email Us: Get tailored insights by emailing info@thepowerscompany.com
- Request an Assessment: Use our online contact form, and one of our expert manufacturing consultants will reach out to schedule an in-depth analysis of your operations.
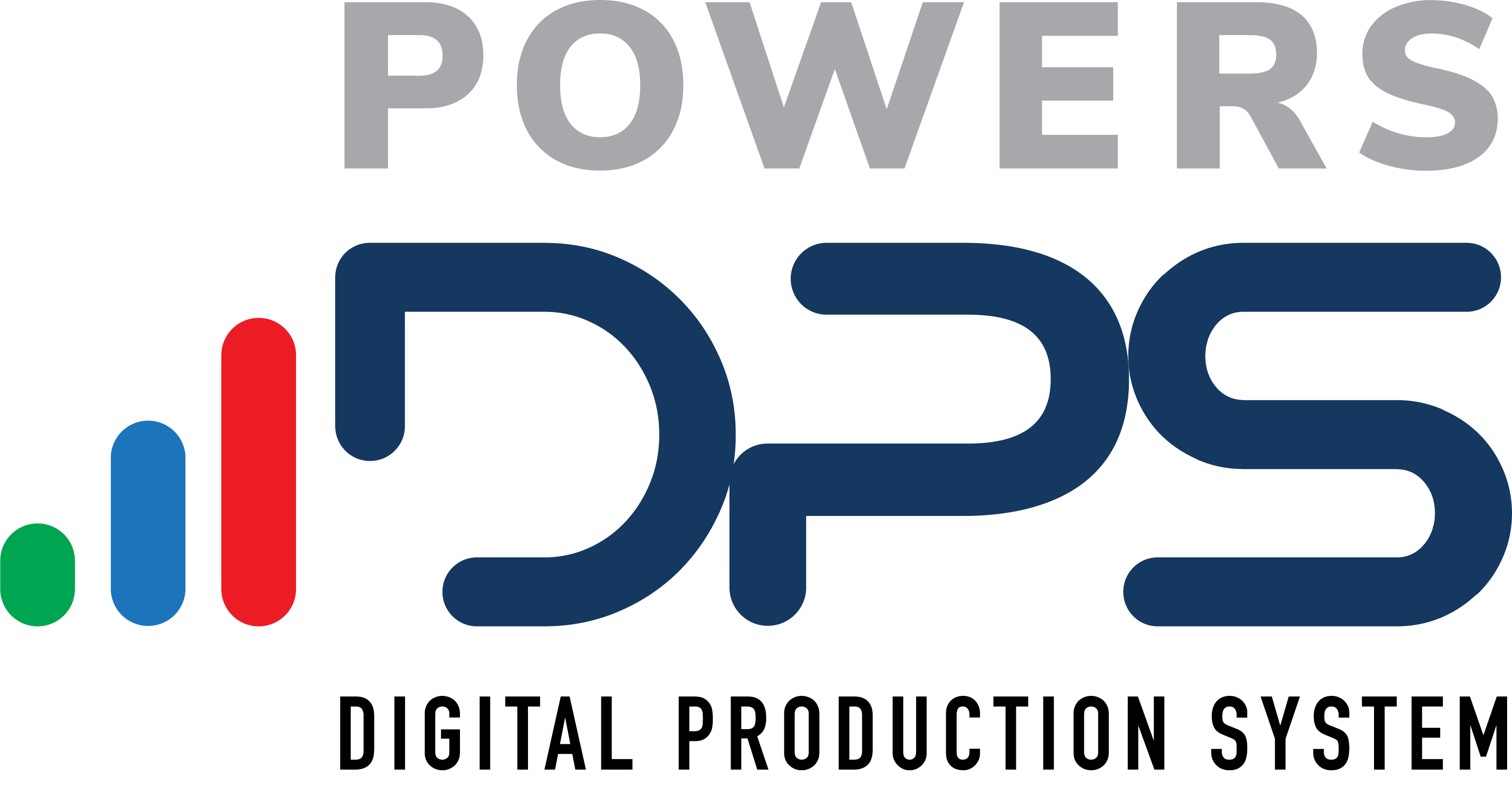
Start transforming your operations today with POWERS DPS. Contact us for a free consultation and see how digital transformation can revolutionize your manufacturing future. Learn More about DPS