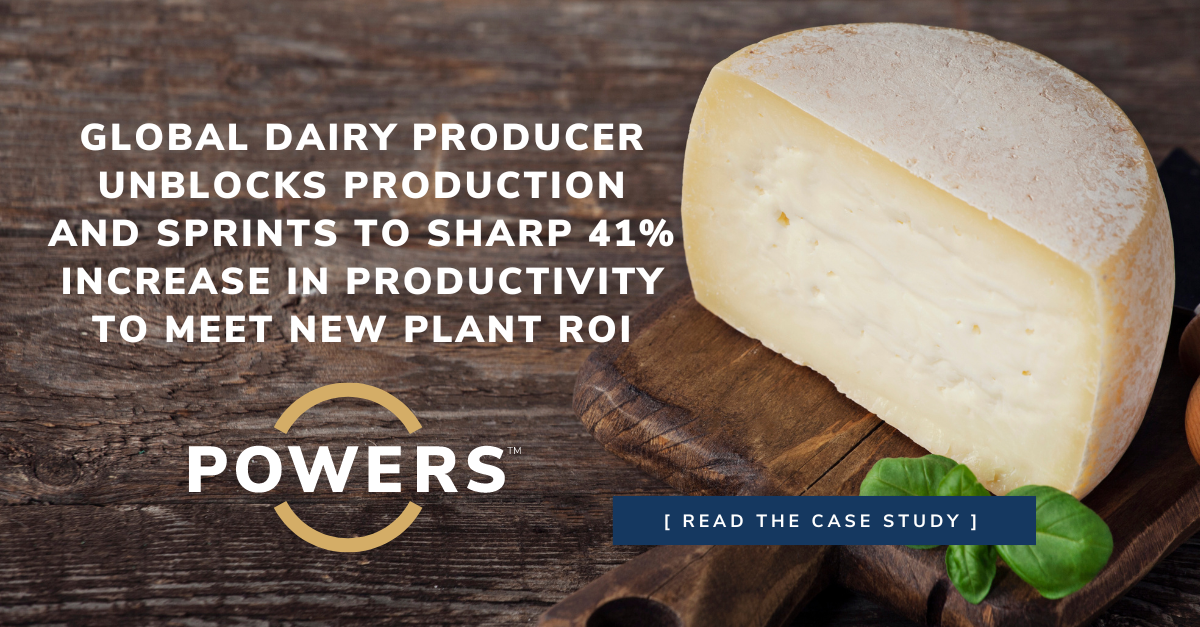
Established global dairy industry leader calls on POWERS to meet ROI from $150 million investment in new processing plant. Our team jumped in to immediately uncover production challenges and deliver a massive performance boost.
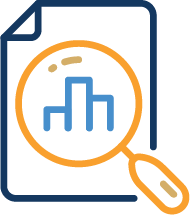
Project Overview
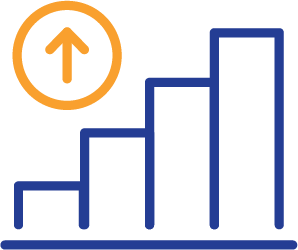
Performance Results
Background
Founded over eighty years ago, our Midwest-based client is one of the largest dairy producers in the world, producing 1 billion pounds of wholesome, high-quality cheeses annually for retail brands and the foodservice industry.
This global dairy industry powerhouse built a new, $150 million plant to increase production capacity and meet surging demand.
However, to meet the ROI goals of management, the new plant had to package 36,000 pounds of product per hour.
As a result, the POWERS team was brought on for an 8-week Sprint to improve plant performance and provide the roadmap to reach ROI performance goals.
Situation Analysis
Our team worked quickly with frontline leadership and the plant workforce to uncover the production bottlenecks hampering performance.
As always, we looked holistically at the business and examined the systems, processes, and behaviors that will maximize capacity most efficiently.
We found a lack of defined processes to optimize performance and efficiency. There were no checklists for personnel to follow at critical points like start-up and shutdown.
Beyond process issues, our team found many operators and line personnel without proper job-function training.
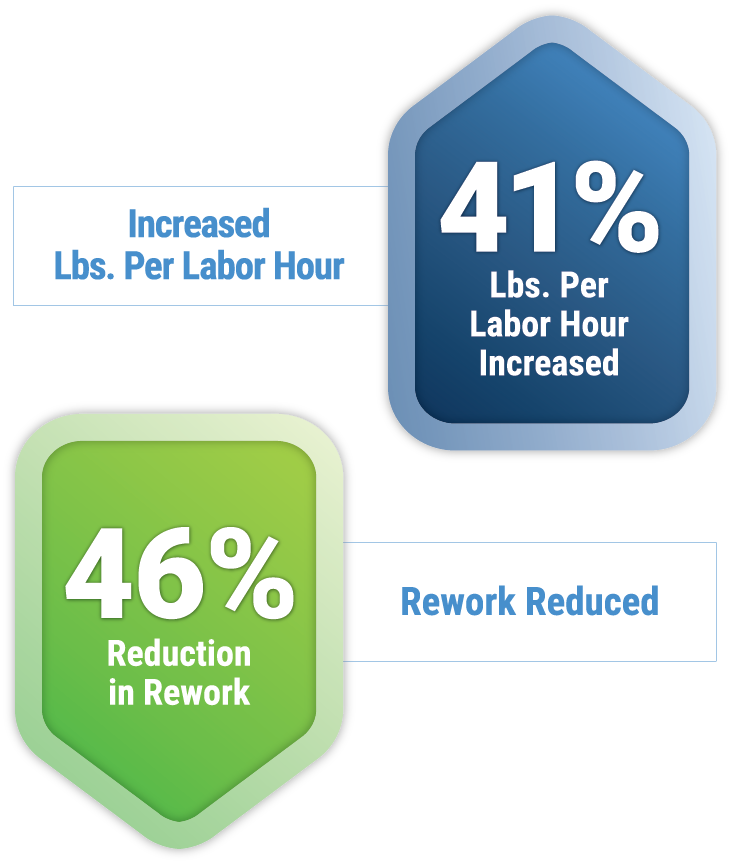
POWERS Helps Global Dairy Producer Unblock Production and Sprint to Sharp 41% Performance Boost to Meet New Plant ROI
Established global dairy industry leader calls on POWERS to meet ROI from $150 million investment in new processing plant. Our team jumped in to immediately uncover production challenges and deliver a massive performance boost.
Background
Founded over eighty years ago, our Midwest-based client is one of the largest dairy producers in the world, producing 1 billion pounds of wholesome, high-quality cheeses annually for retail brands and the foodservice industry. This global dairy industry powerhouse built a new, $150 million plant to increase production capacity and meet surging demand.
However, to meet the ROI goals of management, the new plant had to package 36,000 pounds of product per hour. As a result, the POWERS team was brought on for an 8-week Sprint to improve plant performance and provide the roadmap to reach ROI performance goals.
Situation Analysis
Our team worked quickly with frontline leadership and the plant workforce to uncover the production bottlenecks hampering performance. As always, we looked holistically at the business and examined the systems, processes, and behaviors that will maximize capacity most efficiently.
We found a lack of defined processes to optimize performance and efficiency. There were no checklists for personnel to follow at critical points like start-up and shutdown. Beyond process issues, our team found many operators and line personnel without proper job-function training.
As a result, cages were overloaded with product causing rework and unloading delays. Loaders had been instructed to load cages with 40+ blocks, while the system was only designed for 30 blocks. This overloading issue created a disparity between unloading and packaging. It also created staffing issues that increased labor costs.
Additionally, our team discovered a design flaw in the brine flume divider, mismatched brine exit conveyor speeds between packaging lines 1 and 2, and speeds not set to meet ROI goals.
Our Approach
In a Sprint situation, our goal is to uncover and correct the performance barriers as quickly as possible and “train in” the corrections to achieve rapid performance boosts that are also sustainable. Therefore, we implemented process changes and skills training for this client to meet the new plant’s performance goals and the ROI.
We created a skills flex and training plan from a leadership training perspective. For specific job-function training, loaders were trained to place 30 blocks per level in cages to meet equipment design specifications.
Our process improvements included creating checklists and training for start-up, shutdown, and unplanned downtime. Because of the design flaw in the brine flume divider, we worked with engineering to redesign the divider so employees could direct the product correctly.
In addition, we corrected the mismatched capacity between cage unloading and cheese packaging and the brine exit conveyor speeds on packaging lines 1 and 2 and set them to meet ROI goals. Our team also set/check speeds to ensure the 20 blocks per minute per line (for a total of 48,000 lbs. per hour) capacity was sustained.
The Results
The Sprint allowed our client to properly staff production, particularly in moving from processing to packaging, creating a more efficient labor allocation and lowering costs. Overall, because of addressing and correcting the cage overloading issue with proper guidelines and training, rework was reduced by a massive 46%. And through further skills and behavior training and process improvements across production, packaging pounds per labor hour improved by an astounding 41%.