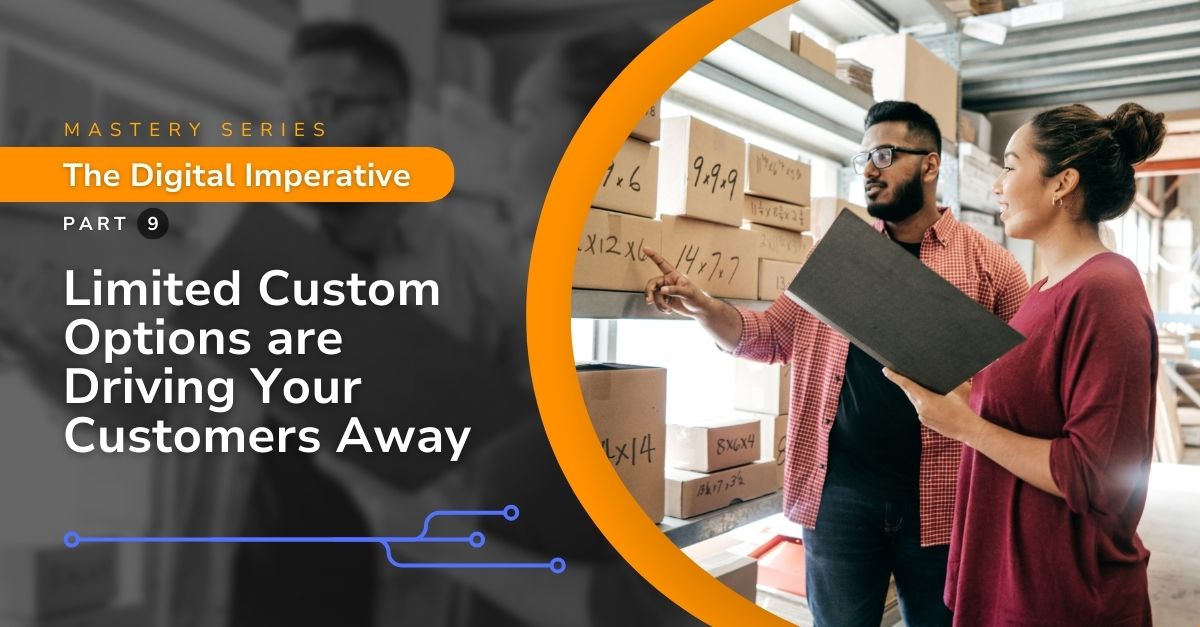
Customer expectations have shifted dramatically, with more demand for highly customized products and services.
Failing to embrace Industry 4.0 technologies and neglecting digital transformation puts manufacturers at a disadvantage in meeting these demands. Companies that rely on outdated processes and systems often find themselves stuck in inefficient workflows, unable to keep pace with the need for personalization.
One less common example of this issue is the inability to adapt quickly to last-minute design modifications from customers. For instance, a manufacturer working with automotive parts might receive a client’s request to slightly alter a component design just before the production cycle begins. In a facility lacking digital tools like computer-aided design (CAD) integration or automated production lines, this seemingly minor change requires manual reconfiguration of machines, recalibration of quality control systems, and a delay in other scheduled production tasks. The result is wasted time, longer lead times, and inefficient use of resources, ultimately reducing the manufacturer’s ability to deliver customized solutions efficiently.
This inability to pivot quickly and incorporate customizations without sacrificing productivity directly results from neglecting digital transformation. By not adopting Industry 4.0 innovations—such as real-time data analytics, automation, and smart manufacturing systems—manufacturers face numerous secondary symptoms, including increased downtime, inconsistent quality, and inefficient use of materials. These issues compound the challenges of customization, making it clear that digital transformation is no longer optional but essential for maintaining competitiveness in a rapidly evolving market.
1Lack of Flexibility in Production Lines for Custom Orders:
Traditional production lines are often built for high-volume, standardized products. When faced with custom orders, these rigid systems struggle to pivot, causing delays and inefficiencies. Managers frequently encounter bottlenecks during changeovers between product types, as legacy systems and manual processes make it difficult to adjust equipment and workflows quickly. This lack of flexibility forces downtime or reduces throughput, hampering productivity.
Mitigation: Embracing smart manufacturing technologies, such as modular production lines and automated retooling systems, can dramatically reduce changeover downtime. Digital systems enable quicker transitions by reconfiguring equipment automatically, with minimal human intervention. Additionally, predictive maintenance tools can help identify and address potential issues before they cause disruptions, keeping the line running smoothly even with custom orders.
2Increased Lead Times for Customized Products:
Customization often requires additional planning, setup, and adjustments, which increases lead times. Without digital tools to streamline these processes, managers frequently struggle to balance high-volume production with custom orders, leading to delays. These delays frustrate customers and create inefficiencies as resources are shifted between different tasks.
Mitigation: Implementing digital twins and simulation tools can help optimize the production process for customized orders. Managers can foresee bottlenecks and allocate resources more efficiently by simulating different production scenarios. This technology shortens lead times by ensuring that machines and workers are prepared for custom orders without disrupting the workflow.
3Limited Ability to Adjust Batch Sizes for Custom Requests:
Inflexible legacy systems often limit manufacturers’ ability to adjust batch sizes efficiently. Managers struggle to balance small custom orders with larger production runs, as traditional systems are optimized for large, uniform batches. The inability to produce smaller batches without causing inefficiencies leads to excess inventory or longer lead times.
Mitigation: The integration of flexible manufacturing systems (FMS) allows for rapid changes in production volume. Digital transformation through automation and real-time data analytics can help manufacturers adapt batch sizes on the fly, enabling more efficient use of materials and resources. This shift improves productivity and enhances the company’s ability to meet customer-specific needs without inflating costs.
4Inconsistent Product Quality Due to Varying Specifications:
Maintaining consistent quality becomes a significant challenge when product specifications vary from order to order. In manual processes, the risk of human error increases, and equipment may not be calibrated properly for different product variations. This inconsistency leads to rework, waste, and delays, all eroding productivity.
Mitigation: Adopting advanced quality control systems like machine vision and AI-based inspection tools can ensure consistent quality across customized orders. These systems can automatically adjust for varying product specifications, detecting anomalies in real time and minimizing the need for manual intervention. By catching defects early, manufacturers can reduce rework and maintain a steady production flow, even with diverse product requirements.
5Inability to Efficiently Manage Diverse Material Requirements:
Customization often involves using different materials, which can be difficult to manage efficiently using outdated inventory and supply chain systems. Managers frequently face delays and material shortages when switching between custom orders that require unique or non-standard materials, further hindering productivity.
Mitigation: A digital supply chain management system enables real-time tracking of material inventories and better coordination with suppliers. Advanced planning systems that integrate with production schedules can ensure that the necessary materials are available just in time, reducing the risk of delays or shortages. This enhances productivity by ensuring that custom orders can be fulfilled without causing disruptions to other production activities.
6Difficulty in Scaling Customization Efforts Without Disrupting Workflows:
Scaling customization efforts without disrupting standard workflows is a common challenge. The lack of digital tools to streamline the production of both standardized and customized products leads to inefficiencies. Managers often struggle to balance the two, resulting in delays, resource mismanagement, and increased operational complexity.
Mitigation: Investing in Industry 4.0 technologies like robotics and smart production lines allows manufacturers to scale customization efforts without compromising their core production capabilities. By leveraging digital platforms that integrate data from across the production process, manufacturers can achieve a more seamless transition between standard and custom orders, minimizing disruptions to overall productivity.
7Inefficient Use of Data to Anticipate Customer Customization Needs:
Many manufacturers still rely on historical data or manual processes to anticipate customer customization needs, which can lead to inefficiencies and missed opportunities. Managers are often left guessing when forecasting demand for custom products, resulting in overproduction, excess inventory, or delayed deliveries.
Mitigation: Data analytics and AI-driven forecasting tools can significantly improve demand planning accuracy for customized products. Manufacturers can better predict customization needs by analyzing customer behavior, market trends, and historical data and adjusting production accordingly. This proactive approach reduces the risk of inefficiencies and ensures that resources are allocated optimally, boosting productivity.
8Poor Alignment of the Supply Chain with Fluctuating Customization Demands:
Customization often requires a more flexible and responsive supply chain, but many manufacturers struggle to align their supply chains with fluctuating customization demands. Managers frequently deal with stockouts or excess inventory due to the inability to adjust procurement and logistics quickly, which impacts cost efficiency and productivity.
Mitigation: A digitized supply chain, powered by real-time data and advanced analytics, can provide the flexibility needed to respond to changing customization demands. Manufacturers can use digital platforms to track supplier performance, monitor inventory levels, and adjust procurement strategies in real-time. This reduces lead times, improves resource allocation, and meets custom orders without disrupting overall production.
9Challenges in Maintaining Standardization Alongside Customization:
Maintaining standardization in processes and products while offering customization is a constant balancing act. Managers often face the challenge of preserving the efficiency of standardized production while accommodating custom requests, which can lead to process inefficiencies and increased operational costs.
Mitigation: Using modular production systems and digital manufacturing platforms can help manufacturers maintain standardization while allowing customization. These technologies enable seamless transitions between custom and standard orders, reducing the need for manual interventions. Manufacturers can minimize disruptions and maintain high productivity by integrating customization into a standardized process.
10Increased Production Downtime Due to Frequent Setup Changes:
Frequent setup changes for custom orders often lead to increased downtime, as machines must be recalibrated or reconfigured between different product runs. This is particularly problematic in legacy systems where manual setup processes are still prevalent. The resulting downtime not only reduces overall productivity but also increases costs.
Mitigation: Automation and smart factory technologies can significantly reduce the time required for setup changes. Automated setup systems integrated with digital production schedules can streamline the process, allowing machines to reconfigure based on the next order’s specifications. This reduces downtime, minimizes manual intervention, and improves overall productivity.
Conclusions for Operations Leaders
Failing to embrace Industry 4.0 and neglecting digital transformation puts manufacturers at a significant disadvantage in offering customized products and services. Without the flexibility, speed, and data-driven insights digital technologies provide, manufacturers are left with inefficiencies that hinder productivity. These inefficiencies—from increased lead times to difficulty managing diverse material requirements—create real challenges on the shop floor, impacting everything from production timelines to quality control.
Manufacturers can overcome these challenges and optimize their operations by implementing digital transformation strategies.
How POWERS Can Help
At POWERS, we offer consulting services and a comprehensive solution for manufacturers ready to thrive in the digital age. Our approach focuses on transforming your production processes, increasing efficiency, and driving sustainable improvements across the entire value chain. Our DPS (Digital Production System) offers AI-driven insights that empower your operations in real time, helping you stay ahead in today’s fast-paced market.
What POWERS DPS can do for you:
- Complete Visibility: Monitor every aspect of production in real-time, identifying inefficiencies with intuitive dashboards and actionable insights.
- Enhanced Collaboration: Seamlessly integrate data across teams, improving communication and ensuring alignment on production goals.
- Data-Driven Decision Making: Leverage advanced AI to predict demand, optimize production schedules, and swiftly respond to customer needs.
- Increased Productivity and Efficiency: Streamline workflows, reduce downtime, and better use resources to unlock higher levels of productivity.
POWERS can help you navigate the complexities of digital transformation, delivering lasting productivity improvements through real-time data, automation, and AI-powered decision-making. Whether you’re looking to streamline custom orders, reduce lead times, or increase overall efficiency, DPS offers the solutions to make it happen.
If you’re ready to elevate your manufacturing operations and stay competitive in the age of Industry 4.0, let POWERS be your partner in driving change.
- Speak to an Expert: Call +1 678-971-4711 to discuss your specific challenges and goals.
- Email Us: Get tailored insights by emailing info@thepowerscompany.com
- Request an Assessment: Use our online contact form, and one of our expert manufacturing consultants will reach out to schedule an in-depth analysis of your operations.
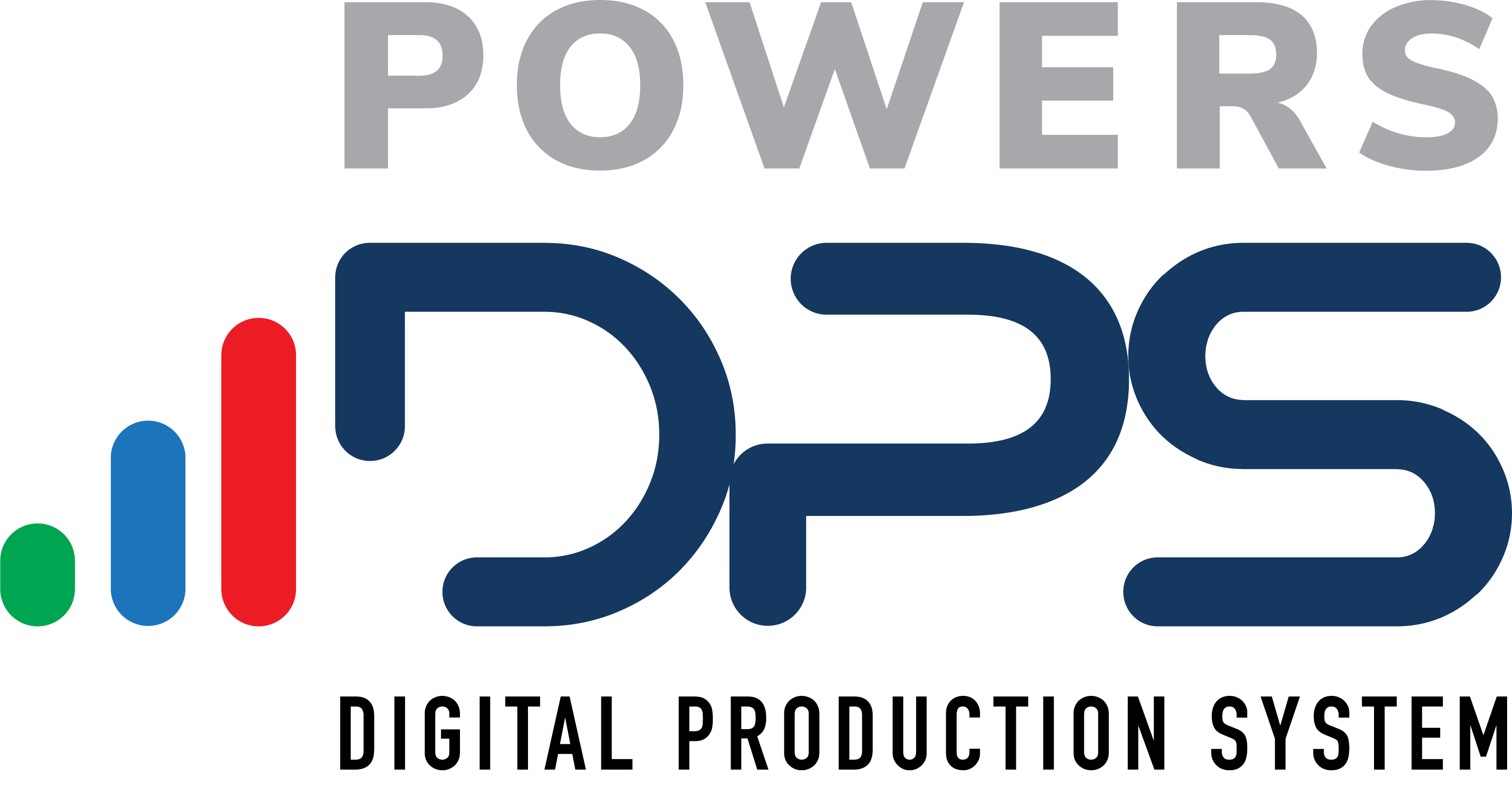
Start transforming your operations today with POWERS DPS. Contact us for a free consultation and see how digital transformation can revolutionize your manufacturing future. Learn More about DPS
Continue Reading from this Mastery Series
- Part 1 – Outdated Tech is Weakening Your Talent Pipeline
- Part 2 – How Legacy Systems Sabotage Your Cybersecurity and Productivity
- Part 3 – How Ignoring Digital Tools Leaves You Vulnerable to Downtime
- Part 4 – When Digital Stagnation Leads to Poor Communication and Production Chaos
- Part 5 – The Real Cost of Trying to Keep Up in the Market Without Digital Transformation
- Part 6 – Missing Out on Real-Time Data Drains Productivity and Profit
- Part 7 – How Failing To Go Digital Jeopardizes Regulatory Compliance
- Part 8 – How Outdated Inventory Practices Sabotage Your Operations
- Part 9 – Limited Customization Options are Driving Your Customers Away
- Part 10 – The Productivity Trap of Failing to Scale Digital Initiatives