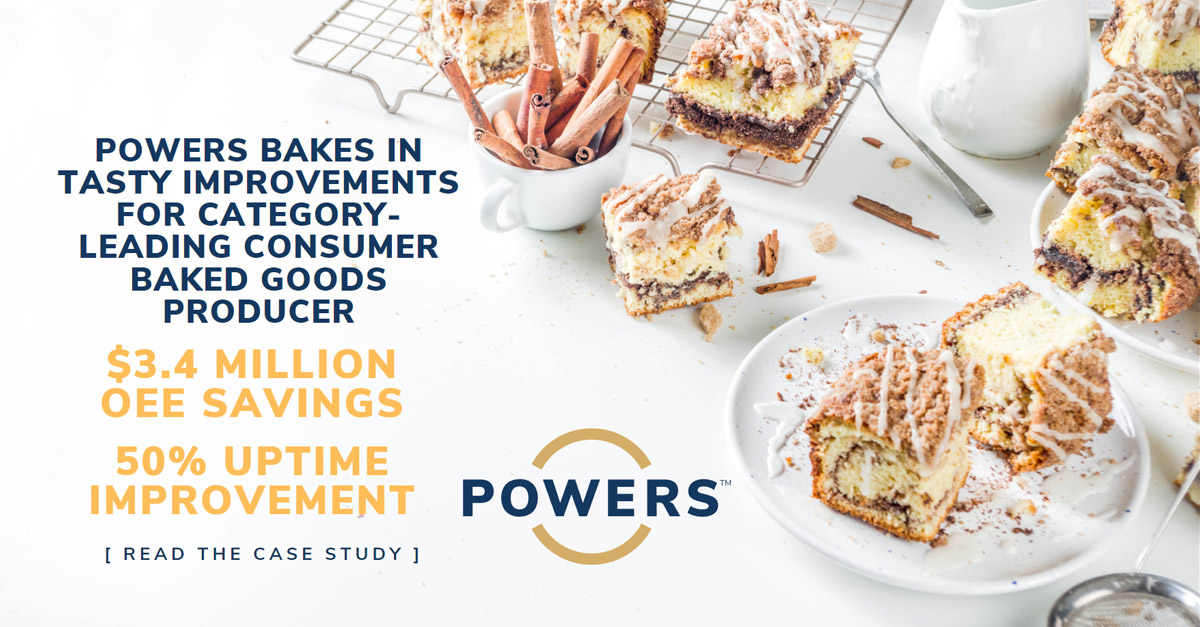
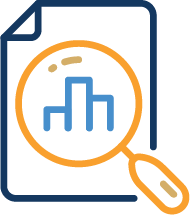
Project Overview
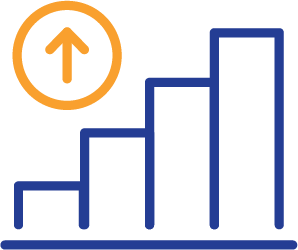
Performance Results
Background
Our client, a leading consumer baked goods producer, struggled with equipment uptime and poor OEE performance from a consistent failure of their bakery production line equipment. This is directly attributed to poor schedule adherence, excess downtime, excess overtime, and failure to meet customer delivery and service level agreements.
Before partnering with POWERS, plant daily startup up (Power Hour) was at 50%, equipment uptime at 69%, schedule attainment at 50%, and 63.5% OEE.
Analysis
At the heart of the issues was a need for more clarity and consistency in the maintenance department’s operations. Inconsistent startup support, a heavy reliance on tribal knowledge from a limited number of technicians and outdated or non-existent pre-flight forms for certain lines contributed to unpredictable startups.
Roles and responsibilities remained ambiguous, causing deviation from established best practices. Moreover, there was a significant discrepancy in understanding what constituted a “successful” day for a maintenance supervisor, coupled with the absence of consistent metrics to measure and drive success. Supervisors needed to be more present on the shop floor.
When they were present, their follow-up approaches varied widely, often missing structured discussions about technician activities and goals for the shift. This inconsistency in leadership practices was evident throughout the maintenance department.
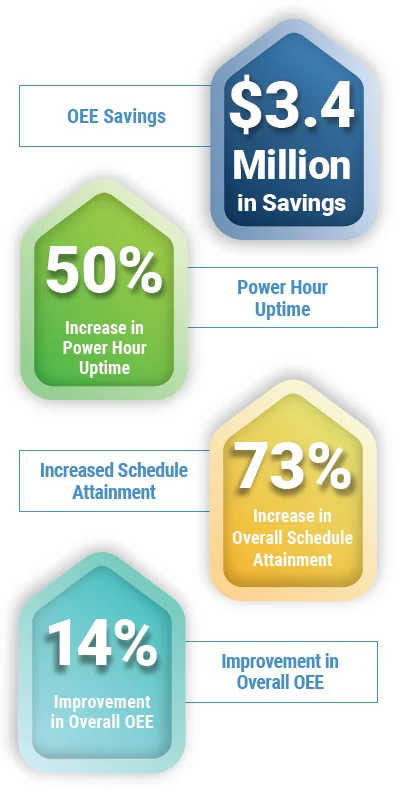
Technician training and evaluation became another sore point. The evaluation methods were outdated, and technicians were also not regularly assessed. This led to critical skills gaps, resulting in excessive downtime, repeated mistakes, and misallocation of tasks. The facility's Preventative Maintenance (PM) approach further highlighted these inefficiencies. PM tasks, while published, had little to no follow-up.
The quality, frequency, and adherence to PM procedures were not regularly assessed. Moreover, there needed to be a mechanism to ensure that technicians performed their PM tasks to the set standards.
Communications and inter-departmental collaborations were notably lacking. Daily touchpoints, which could have improved operational efficiency, were absent. Key meetings like the DDS3 Production ones only involved some necessary stakeholders, causing a siloed approach to problem-solving. Additionally, a lack of familiarity with modern tools like Tableau meant data-driven decisions were not being made. Many supervisors lacked targeted leadership development, and there was no formal process to provide them with developmental feedback outside their annual reviews.
Key Take Aways
- Inconsistency in maintenance department operations and startup support.
- Lack of clarity in roles and measurement metrics for success.
- Critical skills gaps among technicians due to outdated training and infrequent evaluations.
- Inefficient PM processes with little accountability and regular assessment.
- Siloed approach to problem-solving due to lack of inter-departmental collaborations.
- Underutilization of modern tools and lack of leadership development for supervisors.
Project Goals
- Reduce downtime by 25-30% to provide an uplift in available run time
- Provide uplift in equipment Uptime/Availability
- Improve OEE by 5.5%, equivalent to approximately $2.7 Million in annualized savings.
- Transition from the reactive, firefighting, and run-to-failure maintenance program to a proactive and preventative one.
- Revamp and refocus the preventative maintenance program to ensure timely and thorough completion, directly correlating to uptime and increased equipment availability.
- Incorporate and enhance Power Hour initiatives and best practices.
- Full integration and utilization of the Fiix CMMS system.
The Plan
In our plan to address the operational challenges identified in the case study, our primary focus will be on fortifying the capabilities of Frontline Leaders. Recognizing the current inconsistencies and inefficiencies, we aimed to establish ownership of results at the frontline leadership level. This approach ensures that individual team members are directly accountable for outcomes, promoting proactive management behaviors.
The POWERS plan:
- Frontline leaders will shift from being reactive problem-solvers to proactive people managers.
- Frontline leaders will take ownership of the essential metrics that underscore accountability.
- All tiers of management will collaborate to assist the frontline leaders in addressing daily challenges.
- Clear roles and responsibilities will be defined for leadership above the frontline, eliminating ambiguities that may currently exist.
- Instead of allowing issues to be passed up the chain, leadership will ensure that problem-solving is primarily driven by the frontline manager, fostering an environment of ownership and immediate action.
Solution
Through our collaboration, we primarily focused on streamlining operations, improving technician utilization, enhancing interdepartmental coordination, and bolstering leadership capabilities.
With the establishment of weekly planning and scheduling meetings, we ensured systematic equipment availability, backlog management, and resource allocation. A daily/weekly schedule was set up to monitor adherence, emphasizing the importance of proactive technician involvement, which included a commitment to recording unplanned work.
A vital element of this restructuring was the continuous feedback loop for reactive maintenance, enabling the fine-tuning of Preventive Maintenance (PM) activities and frequencies. Leadership roles and responsibilities were delineated clearly, from team leads to senior supervisors, and each tier of leadership was provided a thorough understanding of their duties based on the Maintenance Management Operating System.
A comprehensive mechanic skills baseline was introduced to address skills gaps and integrated into the planning and scheduling process. Leaders began to emphasize proactive management, moving away from a reactionary approach. Standardized leader work became a beacon of accountability, helping to shape leadership behavior as an exemplar of best practices.
- Structured Scheduling: Weekly planning & scheduling meetings were established for better resource allocation and equipment availability.
- Proactive Technician Involvement: Emphasis on recording unplanned work and focusing on preventive measures.
- Enhanced Leadership Clarity: Clear roles and responsibilities across all leadership levels and regular 1:1 meetings for alignment.
- Skill Set Optimization: Identification of critical skills and gaps, allowing for targeted training and efficient task assignments.
- Emphasis on Proactive Management: Shift from reactionary 'firefighting' to strategic, proactive management through structured leader work and routine evaluations.
- Data-Driven Decisions: Utilize tools like Tableau and Redzone to inform decisions and strategy.
- Efficiency Boosts: Integration of the Fiix CMMS system led to significant time savings and more effective planning.
Results
- 22% improvement in Power Hour from baseline (50%) for FY2023
- Best demonstrated weekly Power Hour at 75% in week 9, representing a 50% improvement from the baseline
- A 5.7% increase in uptime availability from the time uptime was formally tracked within the maintenance department.
- Best demonstrated week in uptime availability at 79% in week 11, representing a 14.5% improvement over the baseline
- 3% improvement from baseline
- Best demonstrated OEE, a 13.3 percentage improvement over the base
- $3,371,796 million in annualized savings in planted weighted OEE savings