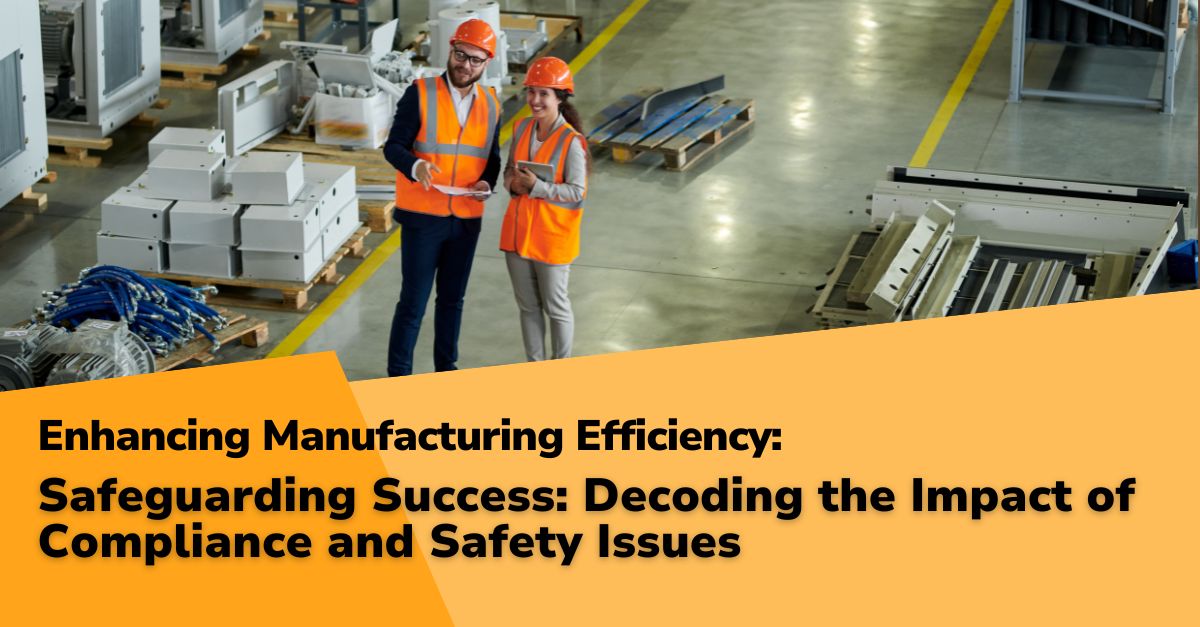
As our series has explored, a well-implemented Management Operating System (MOS) is pivotal in manufacturing, particularly in navigating the complex interplay of compliance and safety.
Compliance and safety transcend regulatory adherence and are integral to operational excellence and sustainability.
This article dissects how a deficient MOS leads to significant operational and financial setbacks in compliance and safety.
From escalating legal liabilities to stifling innovation and market growth, we delve into the top ten detrimental outcomes of neglecting these crucial components in manufacturing, underlining the indispensable need for a robust and fully integrated MOS.
1Increased Legal Liabilities:
Non-compliance often results in substantial legal consequences, including hefty fines. For instance, OSHA violations can result in penalties amounting to tens of thousands of dollars per incident, profoundly impacting a company’s financial standing and reputation.
2Elevated Safety Incidents:
Inadequate safety measures can significantly increase the incidence of workplace accidents. The Bureau of Labor Statistics reports that manufacturing sectors see more injuries than other industries, leading to increased worker’s compensation claims and operational downtime.
3Heightened Regulatory Scrutiny:
Failing to comply invites more rigorous oversight from regulatory bodies. This increased scrutiny often results in regular inspections and audits, requiring substantial time and resources that could be better utilized in productive operations.
4Disruption in Supply Chain:
Compliance issues can cause severe disruptions in the supply chain. Delays in clearing compliance checks can lead to backlogs, impacting production schedules and time-to-market.
5Impact on Employee Morale and Productivity:
Safety and compliance concerns can significantly lower employee morale. Studies have shown that a safe and compliant work environment boosts employee productivity and retention rates.
6Barriers to Market Access:
Non-compliance can lead to restrictions in market access. For instance, failure to meet industry-specific regulations can prevent a company from entering new markets or continuing operations in existing ones.
7Increased Insurance Costs:
Companies with a history of safety and compliance issues often face higher insurance premiums. According to insurance industry reports, these costs can increase by as much as 10-30%, depending on the severity and frequency of incidents.
8Resource Drain in Managing Compliance Issues:
Addressing non-compliance consumes considerable resources. Rectifying compliance failures requires investment in time, personnel, and capital, diverting these resources from core business activities.
9Compromised Product Quality and Consistency:
Non-compliance often concerns quality issues. Regulatory standards are usually in place to ensure consistent product quality, and failing to meet these can result in variable product standards and reduced customer satisfaction.
10Hindered Innovation and Growth:
Compliance and safety issues can significantly slow down a company’s ability to innovate and grow. The diversion of resources towards resolving these issues often means less investment in research and development, hindering long-term growth and innovation.
Conclusions for Manufacturing Operations Leaders
As we explore the vital significance of compliance and safety risks in manufacturing operations, the undeniable importance of a robust Management Operating System (MOS) comes into sharp focus.
The consequences of overlooking compliance and safety are far-reaching, impacting not just the operational aspects but also the foundation of a manufacturer’s credibility and sustainability.
For manufacturing leaders, addressing these risks is not merely about meeting regulatory requirements; it’s about strategically embedding compliance and safety into the core of their operations.
Doing so protects the company from legal and financial repercussions and enhances overall operational integrity, employee safety, and market competitiveness.
Maximize Compliance and Safety with POWERS
At POWERS, we specialize in tackling the intricate challenges of systems, processes, and behaviors in today’s multifaceted manufacturing environments.
Our expertise, grounded in real-world experiences, is centered on strengthening Management Operating Systems to manage compliance and safety risks effectively.
- Customized Compliance Solutions: We craft tailored strategies that align with each manufacturing operation's needs, focusing on practical MOS solutions that reinforce compliance and safety.
- Data-Driven Safety Strategies: Leveraging cutting-edge data analytics, POWERS transforms data into strategic solutions that bolster compliance and workplace safety.
- Comprehensive Approach: Our methodology extends beyond technical MOS aspects, emphasizing leadership, employee safety training, and a culture of compliance and continuous improvement.
- Innovative Risk Management: We integrate innovative approaches to risk management, ensuring proactive identification and mitigation of potential compliance and safety issues.
- Strategic Regulatory Alignment: Our team stays abreast of regulatory changes, aligning strategies to ensure clients are compliant and ahead of industry standards.
Start your journey towards excellence in compliance, safety, and operational efficiency with POWERS. Contact our expert team at +1 678-971-4711 or via email at info@thepowerscompany.com.
Continue Reading from this Mastery Series
- Part 1 - Identifying Key Inefficiencies in the Absence of a Management Operating System
- Part 2 - Top 10 Pitfalls: Lack of an MOS Derails Productivity
- Part 3 - Top 10 Quality Issues at Risk Without a Robust Management Operating System
- Part 4 - The High Cost of an Ineffective Management Operating System
- Part 5 - Without an Optimized Management Operating System, Decision-Making is Severely Impaired
- Part 6 - Scaling Challenges of an Inadequate Management Operating System
- Part 7 - The High Price of Low Engagement: Unpacking the Operational Impact of Employee Discontent
- Part 8 - Safeguarding Success: Decoding the Impact of Compliance and Safety Issues
- Part 9 - Examining the Cost of a Slow Response to Market Shifts
- Part 10 - Charting Success: Understanding the Costs of Losing Competitive Advantage