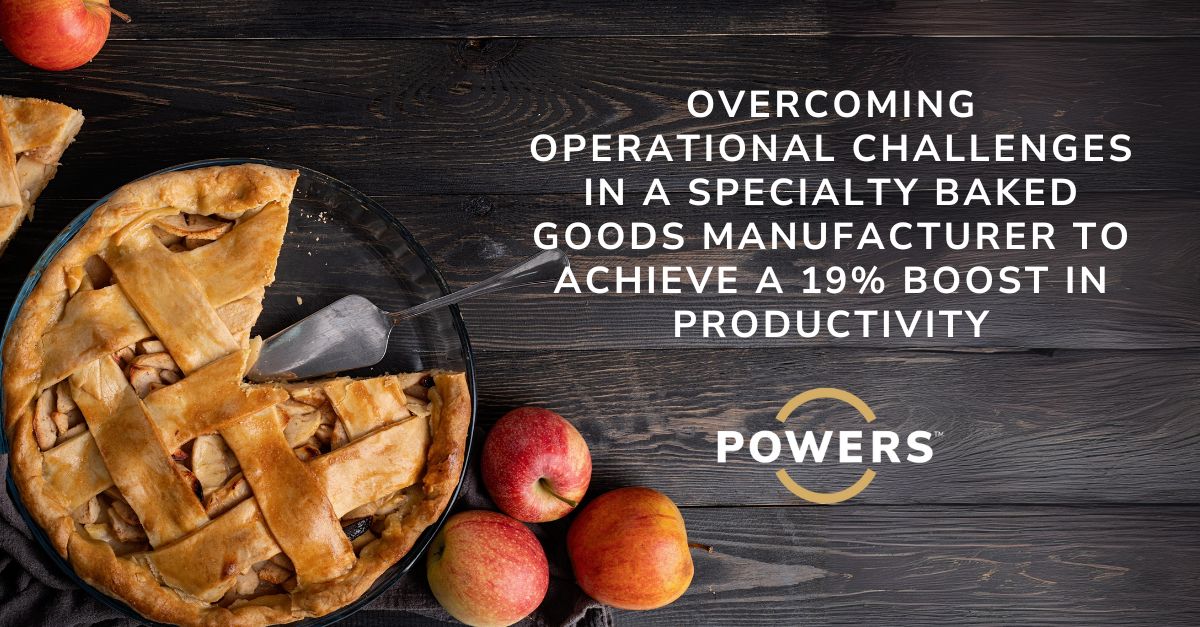
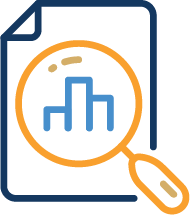
Project Overview
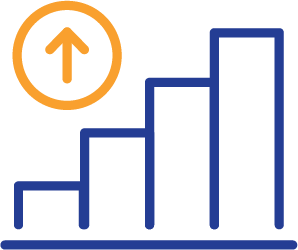
Performance Results
Executive Summary
A prominent specialty baked goods manufacturer with a rich history of success and a wide-reaching presence sought to address operational inefficiencies that had emerged in the wake of global disruptions. With a commitment to quality and innovation, the company recognized the need for external expertise to regain its competitive edge. The company was experiencing a notable decline in productivity due to various challenges. These included maintenance reliability issues, a lack of cohesive leadership, and workforce skill gaps, all exacerbated by the fluctuating demands of a post-crisis environment.
Background
Founded several decades ago as a small local bakery, the company quickly became a major player in the specialty baked goods sector. Over the years, it expanded its operations to support a successful restaurant chain, eventually establishing multiple production facilities to meet increasing demand. This expansion allowed the company to serve domestically and international markets, solidifying its reputation as a leader in its industry. Despite its history of success, the company has faced significant operational challenges in recent years. Productivity had declined, and the company struggled with maintenance issues, inefficient use of labor, and a lack of visibility into its profitability. The absence of a predictive maintenance program and the prevalence of siloed decision-making further hindered its ability to operate efficiently.
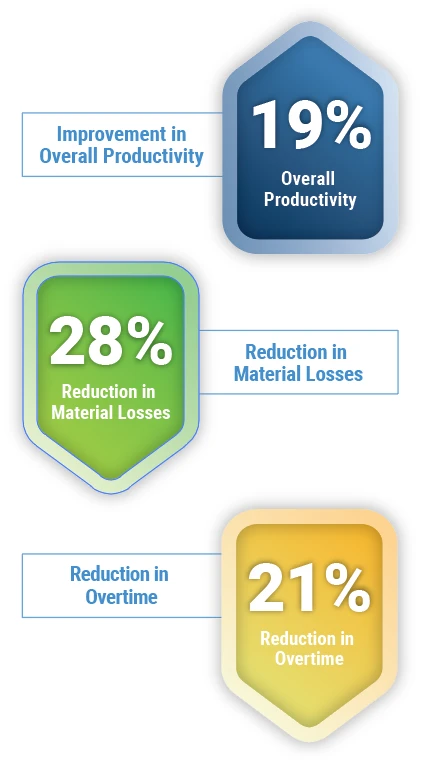
Read the Full Case Study Here
Challenges and Analysis
The specialty baked goods manufacturer grappled with significant operational challenges that severely impacted its performance. A major issue was the decline in equipment effectiveness, driven by a lack of a predictive maintenance program and a reliance on a reactive “run to failure” approach. This led to frequent equipment breakdowns, unscheduled downtime, and higher maintenance costs, disrupting production schedules and decreasing overall efficiency.
Leadership deficiencies further exacerbated these issues, as the team operated in silos with little coordination or communication across departments. This disjointed approach resulted in poorly executed production plans, excess labor hours, and a weakened organizational culture. Additionally, critical skills had eroded across the workforce due to high turnover and insufficient training, leaving frontline leaders overwhelmed and reactive rather than proactive in managing operations.
These challenges were compounded by gaps in upper-level management, which led to inadequate oversight and inconsistent performance. The lack of visibility into key performance indicators (KPIs) made it difficult for the company to assess profitability and make informed decisions, further hindering its ability to improve operational efficiency. Overall, the interconnected nature of these issues created a cycle of inefficiency that the company struggled to break.
Intervention by POWERS
The POWERS team conducted a comprehensive and time-sensitive assessment to address these issues. This assessment identified key areas for improvement and led to the development of a cross-functional performance partnership to enhance communication and daily execution across all departments. Several targeted interventions were implemented to restore operational efficiency:
- Standardization of Startup Routines: Our on-site team introduced standardized startup routines to reduce preventable downtime and minimize operator errors.
- Filling Critical Skills Gaps: The company’s critical skills and leadership needs were identified, and targeted training programs were introduced to address these gaps.
- Leadership Training and Coaching: Frontline supervisors were trained and coached to better manage daily operations, identify inefficiencies, and eliminate wasteful practices.
- Implementation of a Management Operating System: A sustainable management operating system was established to ensure ongoing improvements in performance and decision-making.
Results and Outcomes
The targeted interventions implemented by our team led to a profound transformation in the company’s operational performance, delivering quantifiable and qualitative improvements that have set the stage for sustained success.
Quantifiable Improvements:
- 19% Increase in Overall Productivity: The standardized startup routines and improved cross-functional communication directly contributed to a significant uplift in productivity. By eliminating preventable downtime and ensuring more efficient daily operations, the company achieved a 19% increase in overall output.
- 28% Reduction in Material Losses: By identifying and eliminating inefficient processes, particularly those related to material handling and production line changeovers, the company achieved a 28% reduction in material waste. This improvement reduced costs and supported the company’s commitment to sustainability.
- 21% Reduction in Overtime: By filling critical skills gaps and enhancing the effectiveness of frontline leadership, the company could optimize its labor utilization. This led to a 21% reduction in overtime hours, providing substantial cost savings and improving employee work-life balance.
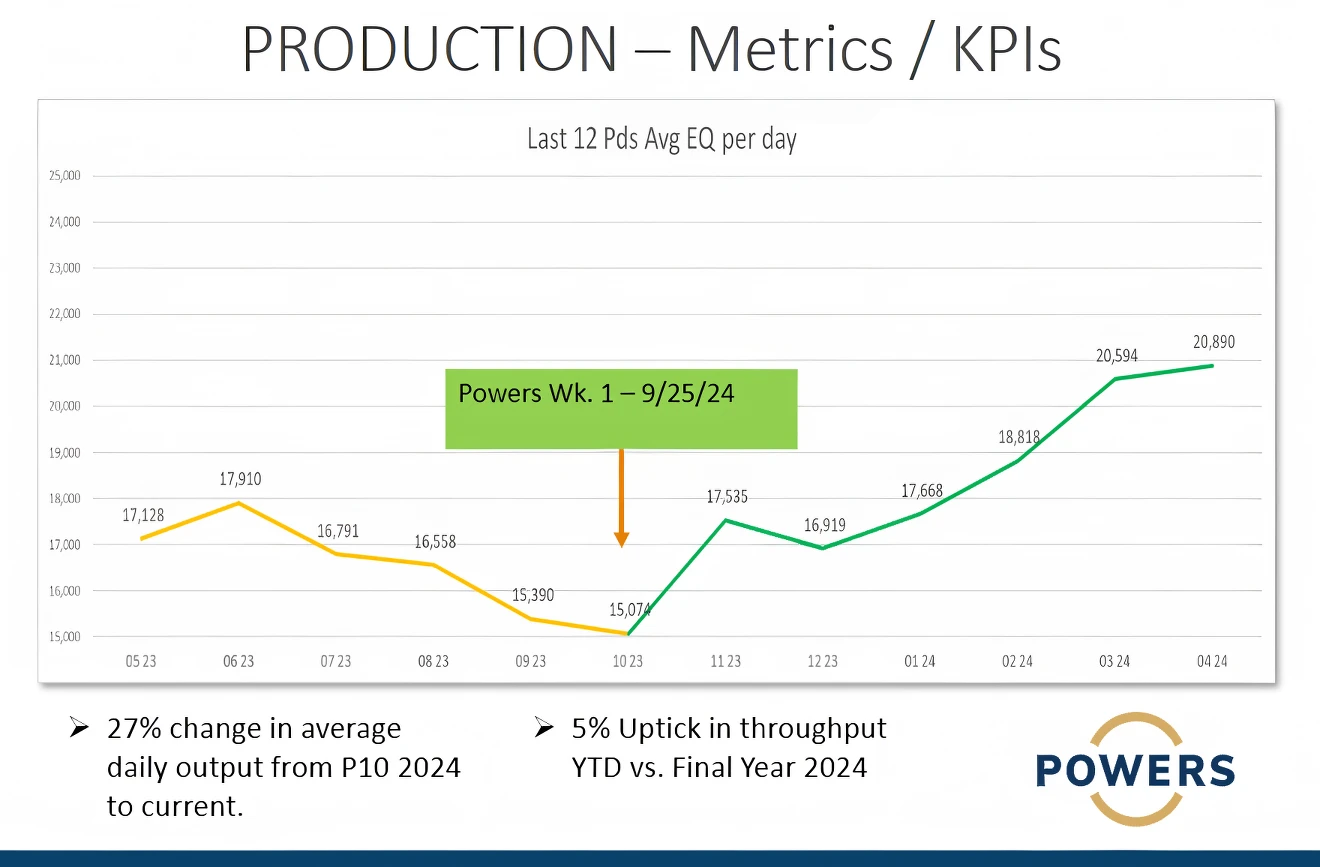
Qualitative Improvements:
In addition to these measurable outcomes, the company experienced several qualitative improvements that have had a lasting impact on its operations and organizational culture:
- Increased Workforce Engagement: The company’s frontline employees, empowered by improved training and clear expectations, became more engaged. This increased engagement translated into higher job satisfaction, lower turnover rates, and a more motivated workforce committed to continuous improvement.
- Sustainable Management Operating System: Implementing a sustainable management operating system has provided the company with a reliable framework for ongoing performance management. This system ensures that the improvements made are maintained and built upon, allowing the company to continue enhancing its operations over time.
- Improved Decision-Making: The company has seen a marked improvement in daily operational decision-making by equipping frontline leaders with the skills to identify inefficiencies and make informed decisions. This has led to more consistent performance, reduced waste, and a more agile response to production challenges.
These results underscore the effectiveness of POWERS’ approach to operational improvement. By focusing on the technical and human aspects of the company’s challenges, the POWERS delivered comprehensive solutions that have had a lasting positive impact on the business.