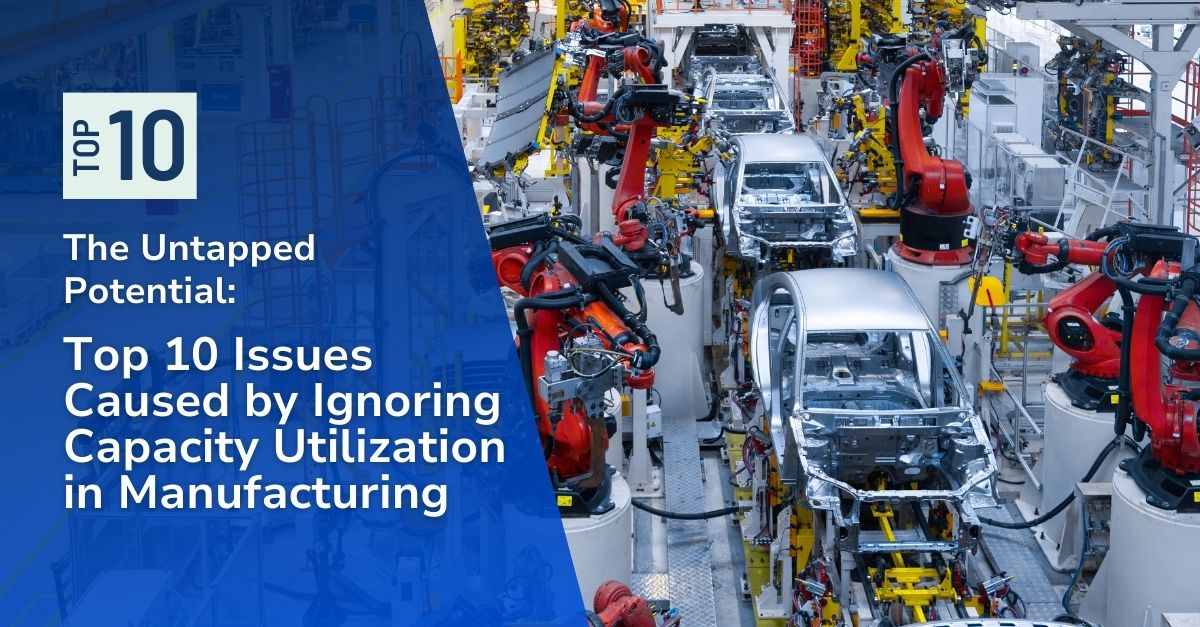
Achieving peak operational output is paramount in manufacturing. Every decision, from production planning to resource allocation, is crucial in maximizing efficiency and profitability.
Among these critical factors, capacity utilization stands out as a key performance indicator (KPI) deserving constant attention. But what exactly is capacity utilization, and why is it so important?
Simply put, capacity utilization refers to the percentage of your available production capacity that is actively being used.
It’s a crucial metric defined as the ratio of actual production to maximum sustainable production. It reflects how effectively you leverage your resources – your people, equipment, and facilities – to generate output.
For operations executives and frontline supervisors alike, understanding and optimizing capacity utilization is essential. Ignoring or underperforming in this area can have a significant ripple effect, impacting various aspects of your manufacturing operations. Here, we explore 10 critical issues that can arise from neglecting capacity utilization:
1Lost Revenue and Eroded Profit Margins:
Even slight fluctuations in capacity utilization can translate to significant revenue losses for large-scale manufacturers. A recent study revealed that companies operating below 75% capacity experience an average 10% revenue loss compared to their high-utilization counterparts.
This translates to a direct erosion of profit margins, hindering your ability to reinvest in growth initiatives and technological advancements and maintaining a competitive edge in the market.
Imagine the impact on a company with a million-dollar production line operating at 70% capacity. Over a year, that translates to a potential loss of $300,000, a significant sum that could have been invested in expanding production capabilities, acquiring new technologies, or enhancing employee training programs.
2The Burden of Increased Production Costs:
While it might appear logical that lower production volume leads to lower costs, the reality within large-scale manufacturing is more nuanced. Fixed costs like rent, salaries, and machinery depreciation remain constant regardless of the output level. Spreading these costs over a smaller production volume leads to higher unit costs, making your products less competitive and impacting profitability.
This phenomenon, known as the “fixed cost trap,” can significantly squeeze your profit margins and hinder your ability to compete with manufacturers who have optimized their capacity utilization. Imagine a large-scale factory with a fixed monthly cost of $1 million for salaries and equipment depreciation. If it operates at 50% capacity, it is essentially paying for the full cost of production for only half the output. This translates to doubling the unit cost, making its products significantly more expensive and potentially less attractive to customers.
3The Inefficiency Trap: Underutilized Resources, Wasted Potential:
Ignoring capacity utilization can lead to a poor allocation of resources within large-scale manufacturing facilities. Underutilized resources like highly skilled personnel, cutting-edge equipment, and vast production floor space create significant inefficiencies. This manifests in idle time for employees, underutilized machinery, and wasted storage space, all of which contribute to higher operating expenses.
Imagine a production line staffed with 20 skilled workers and equipped with ten state-of-the-art machines. If the line only operates at 60% capacity, that translates to eight idle workers and four underutilized machines. This not only incurs unnecessary labor costs but also hinders the potential production output and extends lead times, potentially impacting customer satisfaction.
4Quality Concerns and Compliance Risks:
Operating below capacity in a complex production environment can lead to increased pressure to meet deadlines, potentially compromising quality control measures. This can manifest in rushed work, reduced focus on meticulous inspections, and an increased risk of errors. A 2022 Harvard Business Review article highlighted the correlation between low capacity utilization and higher defect rates, impacting customer satisfaction and brand reputation and potentially exposing you to compliance risks and regulatory scrutiny.
Imagine a large-scale pharmaceutical manufacturer operating at 70% capacity, facing pressure to meet production quotas for a life-saving medication. This pressure can lead to rushed inspections, potentially missing critical quality control checks, and putting patients at risk. Such instances can result in product recalls, hefty fines, and reputational damage.
5Demoralized Workforce and Increased Turnover:
Working in an environment with underutilized capacity can be demotivating for employees in large-scale manufacturing facilities. They might experience boredom, frustration, and a lack of challenge, leading to reduced productivity, increased absenteeism, and higher employee turnover. This disrupts production flow, creates additional costs associated with recruitment and training, and hinders the overall efficiency of your operations.
Imagine a production line where employees spend half their time waiting for tasks due to underutilized capacity. This can lead to dissatisfaction, decreased engagement, and ultimately, a higher likelihood of seeking employment elsewhere.
6Missed Growth Opportunities: Limited Ability to Respond to Market Demands:
Failing to optimize capacity utilization can limit your ability to capitalize on market opportunities in the fast-paced world of large-scale manufacturing. New customer demands can arise quickly, and the ability to scale production effectively is crucial. Being at or near capacity can hinder your ability to respond to such demands, leading to lost business and hindering long-term growth prospects.
Imagine a large-scale electronics manufacturer operating at 80% capacity. A sudden surge in demand for their latest tablet computer emerges. Due to limited capacity, they are unable to ramp up production quickly enough to meet the increased demand. This translates to lost sales, dissatisfied customers, and an opportunity captured by their more agile competitors. In the long run, this can hinder their ability to capture market share and achieve their growth objectives.
7Supply Chain Disruptions: A Domino Effect:
Large-scale manufacturing operations are often deeply embedded in intricate global supply chains. Even minor fluctuations in capacity utilization can have cascading effects throughout the chain. Underutilized production can lead to inventory shortages for downstream businesses, impacting their operations, potentially damaging your reputation as a reliable supplier, and creating further disruptions within the ecosystem.
Imagine a large-scale auto parts manufacturer operating at 60% capacity. This can lead to inventory shortages for car manufacturers who rely on these parts, delaying their production lines and impacting their ability to meet customer demands. This domino effect can create significant disruptions within the entire automotive industry.
8Environmental Impact: Concerns Beyond Profitability:
Large-scale manufacturing processes often have a significant environmental footprint. When operating below capacity, you might be using the same amount of energy and resources to produce a lower volume of goods. This translates to higher per-unit environmental impact, potentially exposing your company to increased scrutiny and regulations related to sustainability and carbon emissions.
Imagine a large-scale steel factory operating at 75% capacity. Although it produces less steel, it still uses the same amount of energy to power the furnaces and machinery. This results in higher carbon emissions per unit of steel produced, putting your company at risk of stricter regulations and potential public backlash.
9Difficulty Attracting and Retaining Top Talent: A War for Skills:
In today’s competitive talent market, large-scale manufacturers need to create an engaging work environment that fosters professional development. Working in a facility with underutilized capacity might not offer employees the challenges, growth opportunities, and sense of purpose they seek. This makes attracting and retaining top talent difficult, further impacting operational efficiency and innovation. Imagine a talented engineer seeking a position in a large-scale manufacturing facility. They are likely to choose a company that offers them the opportunity to utilize their skills and contribute to solving challenging problems, something that a facility with underutilized capacity might not be able to provide.
10Lack of Visibility and Control: A Recipe for Inefficiency:
Ignoring capacity utilization signifies a lack of visibility and control over your complex production processes in large-scale manufacturing. This makes it difficult to identify areas for improvement, anticipate future challenges, and make informed decisions about resource allocation, production planning, and investment strategies.
Imagine a large-scale food processing plant operating without proper capacity utilization monitoring. It might be unaware of bottlenecks in its production line, hindering its ability to optimize production flow and meet customer demands efficiently. This lack of visibility can lead to missed opportunities for improvement and hinder its ability to make strategic decisions for future growth.
Conclusions for Manufacturing Operations Leaders
These ten issues highlight the far-reaching consequences of neglecting capacity utilization in manufacturing. By actively monitoring and optimizing this critical metric, operations executives and frontline supervisors can work together to maximize efficiency, minimize waste, and unlock the full potential of their manufacturing operations.
By optimizing capacity utilization, manufacturers can ensure they are prepared to respond to unexpected market fluctuations and capitalize on emerging opportunities, ultimately driving sustainable growth and profitability.
In subsequent articles, we will explore these issues more deeply, exploring practical strategies and actionable steps you can implement to improve capacity utilization and achieve operational excellence in your manufacturing business.
Unlock Peak Capacity and Dominate Your Market: Partner with POWERS
Stop leaving money on the table due to underutilized capacity. POWERS empowers large-scale manufacturers to achieve and sustain peak capacity utilization, unlocking unprecedented profitability and a competitive edge.
Our proven methodology goes beyond traditional solutions. We work hand-in-hand with your team to identify and eliminate inefficiencies, optimizing every aspect of your operations to maximize output and minimize costs.
Imagine:
- Boosting revenue by 10% or more through optimized capacity utilization, as seen by industry leaders.
- Eliminating the "fixed cost trap" by efficiently utilizing your skilled workforce, advanced equipment, and production space.
- Empowering your employees with engaging, efficient workflows leading to increased productivity and reduced turnover.
- Gaining the agility to respond swiftly to market demands and capitalize on new opportunities.
POWERS isn’t just about efficiency; it’s about transformation. We’ll equip you with the tools and strategies to outperform your competitors and be an industry leader.
Ready to unlock the full potential of your manufacturing operations? Contact POWERS today:
- Call: +1 678-971-4711
- Email: info@thepowerscompany.com
Don’t wait. Start your journey to operational excellence and achieve peak capacity utilization with POWERS.