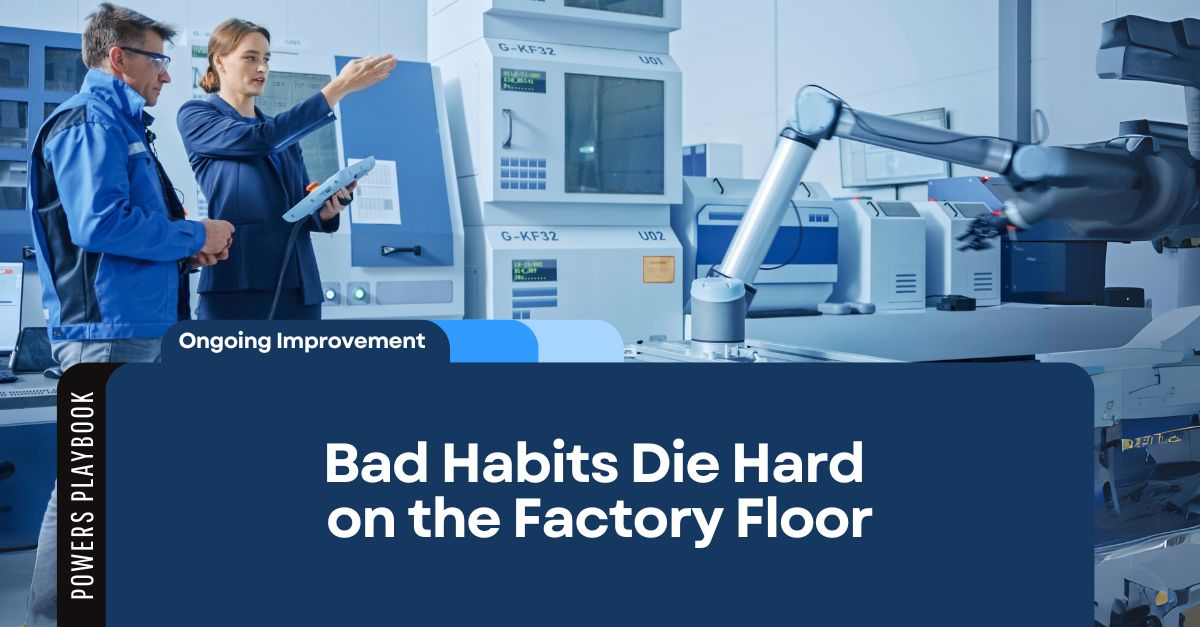
Old habits die hard—especially in manufacturing.
It starts small: skipping pre-shift meetings because “we’re too busy,” ignoring minor equipment issues that “don’t seem like a big deal,” or sticking with outdated processes because “that’s how we’ve always done it.”
Why Do Bad Habits Stick?
Bad habits on the shop floor don’t happen overnight. They creep in when:- People get comfortable – If no one calls out a bad habit, it becomes the norm.
- Shortcuts save time (until they don’t) – Skipping steps may speed things up today but leads to bigger breakdowns later.
- There’s no clear expectation – If leadership isn’t reinforcing the right way to do things, people fall back into old patterns.
A supervisor’s job isn’t just to set expectations—it’s to make sure they’re followed.
5 Common Bad Habits That Slow You Down
These are the everyday habits that chip away at productivity:
1Skipping Pre-Shift Meetings
- “We don’t have time.” → But time gets wasted fixing the same problems over and over.
- Pre-shift meetings set the tone, reinforce priorities, and prevent miscommunication.
2Ignoring Small Equipment Issues
- “It’s still running, so it’s fine.” → Until it isn’t.
- Small problems turn into unplanned downtime. Reporting and fixing issues early keeps production moving.
3Relying on Workarounds Instead of Fixing the Root Cause
- “That machine always does that.” → And it always will unless it gets addressed.
- Workarounds are temporary. Fixing the real issue saves time and frustration in the long run.
Learn how Root Cause Analysis can help you uncover and fix the real issues behind inefficiencies.
4Bypassing Safety Steps to Speed Things Up
- “I’ve been doing it this way for years.” → That doesn’t mean it’s safe.
- Cutting corners on safety isn’t just a risk—it’s a liability.
5Failing to Reinforce Good Documentation
- “We’ll remember.” → No, you won’t.
- Without proper logs, teams lose valuable information, repeat mistakes, and miss out on process improvements.
How to Break Bad Habits and Make Change Stick
Fixing bad habits isn’t about cracking down—it’s about resetting expectations and reinforcing them daily. Here’s how:Step 1Structured Onboarding & Training
- Don’t assume people know it’s a problem.
- Point out what’s happening, why it’s an issue, and what needs to change.
- Example: “We’ve been skipping pre-shift meetings, and it’s leading to confusion. That changes today.”
Step 2Make the Fix Simple and Repeatable
- Tackle one habit at a time.
- Give clear, specific instructions: “Starting now, pre-shift meetings will happen at 6:55 AM sharp—no exceptions.”
- Keep changes practical. If it’s too complicated, people won’t do it.
Step 3Use Daily Reinforcement
- Talk about the change every day until it sticks.
- Use pre-shift meetings as reinforcement.
- Example: “Yesterday, we caught a machine issue early because we had our pre-shift meeting. That’s why we do this.”
Step 4Hold the Team (and Yourself) Accountable
- If leadership doesn’t stick to the new habit, no one else will.
- Call out backsliding immediately.
- Example: If someone skips a step in the process, correct it on the spot—don’t wait until the next meeting.
Turning Short-Term Fixes into Long-Term Wins
Bad habits don’t disappear overnight, but with consistent reinforcement, they can be replaced. The key to lasting change:
- Be relentless – If you let things slide, bad habits creep back in.
- Celebrate wins – When the team adopts a new habit, acknowledge it.
- Tie changes to results – Show how the new habit improves safety, productivity, or downtime.
At the end of the day, a factory’s success isn’t built on massive overhauls—it’s built on small, daily improvements that stick. And it starts with leadership setting the standard.
Break Bad Habits for Good with POWERS
Breaking bad habits on the factory floor takes more than just a one-time fix—it requires consistent leadership, clear expectations, and the right tools to reinforce change. That’s where POWERS comes in.
Our team specializes in developing frontline leaders and optimizing workplace culture to drive sustainable operational performance improvements. We help manufacturing teams break unproductive habits, align leadership behaviors with business goals, and create a culture of continuous improvement—shift after shift, year after year.
To take it a step further, DPS, our next-generation manufacturing operating system, integrates lean manufacturing principles with digital technology to streamline processes, improve productivity, and drive lasting change.
Ready to strengthen leadership and improve factory performance? Contact POWERS today to learn how we can help your team build better habits, eliminate inefficiencies, and achieve long-term success.
- Speak to an Expert: Call +1 678-971-4711 to discuss your specific challenges and goals.
- Email Us: Get tailored insights by emailing info@thepowerscompany.com
- Request an Assessment: Use our online contact form, and one of our expert manufacturing consultants will reach out to schedule an in-depth analysis of your operations.