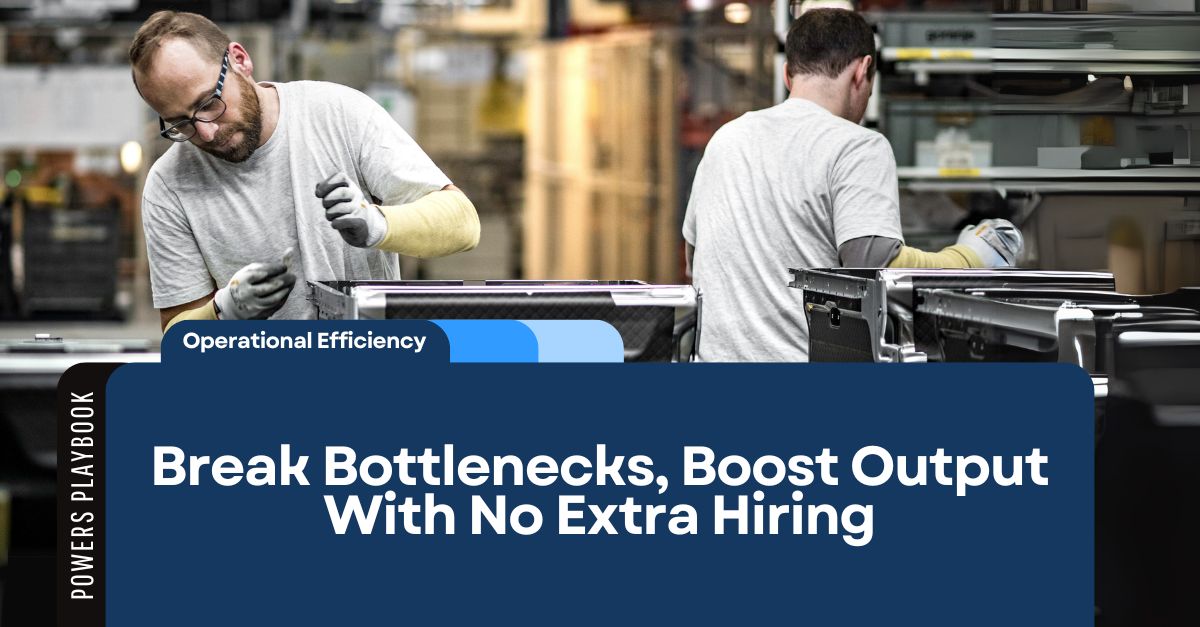
When production slows down, the first instinct is to hire more people. But in most cases, that’s not the real issue. Bottlenecks, those points in the process where work piles up and slows everything down, are usually caused by inefficiencies, not a lack of hands on deck. Adding more people might mask the problem temporarily, but it won’t fix it.
Instead, the key is to improve how work flows through your operation. That means identifying bottlenecks, eliminating waste, and making better use of the team and equipment you already have. Here’s how to do it.
Step 1Identify the Real Bottleneck
If work is backing up somewhere on the floor, don’t assume you already know why. The real bottleneck might not be where the slowdown is most obvious.
- Look at cycle times – Which step takes the longest? That’s a good place to start.
- Watch where work piles up – A backlog at one station often signals a slowdown at an earlier step.
- Talk to operators – The people on the floor see these issues every day. They know where the holdups happen.
- Check the data – Downtime logs, efficiency reports, and job tracking can help pinpoint problem areas.
The key is to diagnose the actual issue before throwing resources at the wrong fix.
Step 2Make Better Use of Your Current Workforce
Adding more people won’t help if the ones you already have aren’t being used efficiently.
- Reassign tasks – Are highly skilled employees spending time on low-value tasks? Could they be better utilized elsewhere?
- Cross-train workers – If only one person can do a key task, they become the bottleneck. Cross-training helps keep things moving.
- Cut unnecessary movement – Are employees spending too much time walking between stations, waiting on materials, or searching for tools? Those small delays add up.
Making small changes in how work is distributed can create more capacity without hiring anyone new.
Step 3Eliminate Waste in the Process
Many bottlenecks aren’t caused by people at all—they’re caused by inefficient workflows.
- Reduce redundant steps – Too many approvals? Unnecessary double-checks? Every extra step slows things down.
- Streamline material flow – Are raw materials or components getting where they need to be when they need to be there? If not, that’s an easy win.
- Shorten changeovers – If switching between jobs takes too long, look into quick-changeover techniques like SMED to cut setup time.
When processes run smoother, work moves faster—without adding staff.
Step 4Get More from Your Machines
Equipment bottlenecks can be just as damaging as labor bottlenecks, but they’re often fixable.
- Standardize work instructions – If operators run the same machine in different ways, it can cause delays and inconsistency.
- Preventive maintenance – Unplanned downtime is a productivity killer. Regular maintenance keeps machines running instead of waiting on repairs.
- Optimize scheduling – Could sequencing jobs differently reduce idle time or prevent bottlenecks? Small scheduling tweaks can make a big difference.
Better machine utilization means more output without needing extra hands.
Step 5Use Simple Automation & Digital Tools
You don’t need a massive tech investment to improve workflow. A few smart tools can make a difference.
- Real-time tracking – Knowing exactly where jobs are in the process helps catch bottlenecks before they become bigger problems.
- Barcode scanners or digital checklists – Small automations reduce manual work and speed things up.
- Better workstation layouts – If employees spend too much time reaching, walking, or searching for tools, reconfiguring their work area can eliminate wasted motion.
Even small process improvements can create extra capacity without hiring another shift.
Bottom Line: Fix the Process, Not Just the People Count
Hiring more staff is an expensive and often unnecessary way to deal with slowdowns. More often than not, the problem isn’t the number of people—it’s how the work is getting done. Take the time to find the real bottleneck. Optimize how tasks, materials, and machines are used. Eliminate wasted steps. You’ll be surprised how much more output you can get from the same team.Take a walk through your facility today. Pick one slowdown you’ve noticed and ask, “What’s really causing this?” Fix that first before thinking about adding headcount.
How POWERS and DPS Can Help Eliminate Bottlenecks and Boost Efficiency
Fixing bottlenecks isn’t about adding more people—it’s about improving how work flows. But identifying the real issues and making sustainable improvements takes the right tools and expertise. That’s where POWERS comes in.
Our proven approach aligns frontline leaders and workforce behaviors with operational goals, leading to higher efficiency, reduced costs, and long-term performance gains.
To further support manufacturing operations, POWERS developed DPS, a next-generation manufacturing operating system designed to integrate lean manufacturing principles with advanced digital technology. DPS helps factory supervisors make data-driven decisions, eliminate inefficiencies, and drive sustainable productivity improvements—without adding unnecessary labor costs.
Ready to eliminate bottlenecks and unlock your operation’s full potential? Contact POWERS today to learn how our expertise and DPS solutions can help you maximize output without increasing headcount.
- Speak to an Expert: Call +1 678-971-4711 to discuss your specific challenges and goals.
- Email Us: Get tailored insights by emailing info@thepowerscompany.com
- Request an Assessment: Use our online contact form, and one of our expert manufacturing consultants will reach out to schedule an in-depth analysis of your operations.