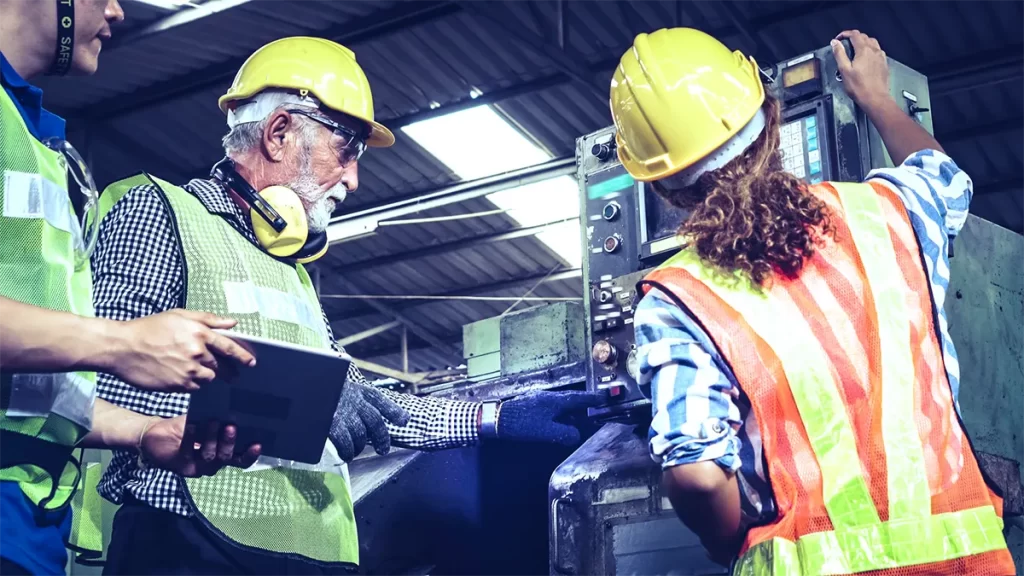
The widely reported and persistent skilled labor shortage has significantly impacted the US manufacturing sector over the last several decades. A recent IndustryWeek article lays out the facts about the “skills gap” in the manufacturing labor market. These are the types of jobs requiring what is often termed “middle skills” or those job qualifications that require more than a high school diploma but less than a four-year college degree.
While qualified workers are becoming more challenging to find, demand in manufacturing continues to grow. The Institute for Supply Management’s semiannual economic forecast predicts that US manufacturers will record a healthy net increase in revenues totaling 6.9 percent for 2021. These figures reverse a 1.3 percent decline in 2020 attributed mainly to the pandemic. According to ISM, 15 of the 18 industry sectors they track are expected to record increases, including the computer and electronic products segment. Heightened and often shifting demand for manufactured goods will further increase skilled labor demand, exacerbating an already tight labor market.
A significant contributor to the labor shortage is that baby boomers are retiring. Now, the pace of those aging out of the labor force is speeding up. The Pew Research Institute indicates that baby boomers are retiring at an even more accelerated rate, likely due to the pandemic. They are taking their many years of experience and specialized technical skills with them. A recent Forbes article puts it succinctly, “… the US has fundamentally failed to prepare Americans to do all the jobs it creates.” This skilled labor gap is especially true in manufacturing.
Another key reason for the labor shortage is that factory jobs have evolved and become far more sophisticated over the last several decades. The proliferation of technology in nearly all aspects of manufacturing means it now takes more than the physical skills typically associated with factory work. Even entry-level manufacturing jobs may require rudimentary technical skills to operate the customized, computerized equipment on today’s factory floors. The remaining jobs that do not involve technology, such as factory maintenance, often require advanced trade skills like welding or other trade technical knowledge that takes time to learn and master.
Today’s typical factory is an extensively automated and connected environment. It is normal to have programmable logic controllers, computers, robots, palletizers, and a host of other automated processing and packaging equipment. Operating, troubleshooting, and maintaining this kind of advanced manufacturing equipment requires a training pathway, from apprentice-style training to a journeyman’s skill level. These are some of the skills that automated factory work can involve:
- Mechanical abilities such as assembly, drilling, tapping, welding, assembling bearings, sprockets, chains, and sub-assemblies.
- Working knowledge of pneumatics and hydraulics.
- The ability to read and understand mechanical and electrical drawings, schematics, and blueprints.
- The ability to troubleshoot all equipment in the plant.
- An understanding of all programmable logic controllers, including troubleshooting ladder logic and re-programming.
- The skills to rewire machines and understand variable drives, device net, Ethernet, and control network systems.
- Practical use of software such as Word, Excel, and PowerPoint to train customers and write reports.
Year after year, large manufacturing operations have invested in automating and connecting their equipment and systems to reduce labor. But the investment required to train employees with the right skills to operate, troubleshoot, maintain and repair this advanced equipment is lagging far behind. The result is that many of the millions of Americans whose jobs were destroyed by the pandemic, even if they were in manufacturing, cannot simply apply for open factory positions.
A Manufacturing Institute survey revealed that it takes an average of seventy days to recruit skilled production workers. Additional on-the-job training to operate and maintain the sophisticated, automated, and customized production line equipment can result in a much deeper investment in training time before new employees are adequately prepared to integrate onto the manufacturing floor.
Onboarding new hires into a stringent workplace safety culture also takes time and can be a critical reason to retain existing skilled workers. They have gained significant experience in the company’s safety culture and can transfer that valuable knowledge to new hires. A study by Travelers Insurance indicates that almost 28% of workplace injuries occur within the first year of employment. A recent study estimates that as much as 60% of skilled-labor positions may go unfilled or take much longer to fill, forcing organizations to look for alternative solutions. This severe shortage of skilled candidates could mean hiring less qualified workers to fill the positions, creating new risks in safety, capacity, and customer satisfaction.
Technical skills are not the only barriers between the millions of unemployed or underemployed Americans and the thousands of unfilled manufacturing jobs. Significant socio-economic barriers also prevent willing workers from applying for and filling available manufacturing jobs. These challenges include reliable transportation to and from work, childcare options, and basic training in workplace behavior. Young workers are also eschewing the potential long-term career stability and advancement opportunities of factory work for short-term, higher-wage gigs at distribution warehouses or driving trucks.
But there is some hope on the horizon. Recent reports from SME.org indicate that young people are taking a hard look at the four-year college pathway that has been ingrained in our society for decades and instead choosing 2-year programs and technical training institutes. This shift started before the pandemic and will be a boon to the manufacturing labor pool.
So, what can your organization do to attract and retain the talent you need to keep your operation at optimal performance?
Invest in Training Your People
Invest in training your people, especially your front-line leaders. From Harvard Business Review to SME.org, to The Manufacturing Institute: virtually every credible business information source has promoted this for years. A recent SHRM.org article sums it up. To attract and retain a younger workforce with the right skills, manufacturing companies should emphasize that they offer their employees more than a job. The kind of culture and opportunity for growth your organization exhibits are readily apparent to younger workers.
And companies are responding, discussing career trajectory, opportunities for further training, and advancement as an integral part of job postings and the entire hiring process, even for hourly wage earners. Many companies are doing a better job of posting the skills or cross-training needed and available for advancement to their existing employees, helping them precisely understand how to move up in the organization. It is not always the best move to give the job to the worker with the required skills. Instead, it can pay dividends to train the willing worker who does not possess the skills yet or involve the skilled worker in preparing their under-skilled co-workers. Both methods can instill a sense of worth and value in the employee and aid in long-term retention.
Focus on Employee Retention
Keeping your skilled workers on board and happy, once you find and employ them, is as high a priority as finding them. To address employee retention, some manufacturers are implementing benefits programs and quality-of-life practices that are not typically offered to hourly employees, including:
- Flexible work schedules
- Flexible shift start times
- Flexible and extended vacation time
- Compensation for unused vacation time
- Shift swapping
- Incentive days off
- Continuing education opportunities
- Educational scholarships
- Awards and recognition
- Team-building and cultural events
- Paid community volunteering opportunities
These kinds of incentives pay off in the short term and over the long haul, building a sense of community, strengthening workplace culture, and contributing to a significantly lower than industry average turnover rate.
Of course, competitive pay is always an effective retention tool. But that alone is not enough anymore, particularly for younger workers impacted by newly established, highly-visible corporate cultural norms introduced by big tech firms such as Apple and Google. Employees want to know they are appreciated. They want clear opportunities to advance, good leadership and management, and they want their ideas to be heard. Ultimately, attracting and retaining your middle-skills workforce comes down to how you treat them.
Get Creative and Look for Innovative Approaches
There are ways to get creative in filling your labor talent pool as well-a recent article from Census.gov details a case study concerning manufacturing hiring in Connecticut. To fill skilled labor positions, the companies involved in the survey have developed and implemented high school apprenticeship programs, open houses, plant tours, and training programs to fast-track students from the local community and technical colleges into manufacturing careers. They have also found ways to involve and retain their older workers through incentives to put off retirement. Establishing a succession training program where older workers train and develop younger workers can maintain continuity and facilitate the much-needed transfer of knowledge and skills.
Beyond the traditional and even the most creative methods, there are additional ways to innovate skilled employee acquisition and retention. A recent article published by the National Association of Manufacturers details the practice of “second chance” hiring to fill open factory positions. It is an innovative approach to be sure and led to increased employee loyalty and retention. A pilot program is transporting willing and skilled workers to and from distant factory jobs and seeing much success in Michigan. This innovative transportation program conducted by the Michigan Transportation Authority is connecting willing workers to factory jobs in a fundamental way, providing reliable transportation to those that need it, and a connected workforce to factories with positions to fill. This kind of lateral thinking and creative problem-solving is necessary if the manufacturing industry intends to fill the skilled labor gap that is only increasing with each passing year and as new products, marketplace demand, and technological advancements take hold.
Two of the primary focuses at POWERS are on the training and development of your front-line leaders and helping you build the kind of substantive operational culture that is attractive to young workers and leads to long-term engagement and retention. We also have programs specifically designed to fill key leadership roles and help your organization meet unplanned hiring requirements.
To schedule an initial discovery and analysis with our dedicated management consulting team, please call us at +1 678-971-4711, email us at info@thepowerscompany.com, or provide your contact information here.