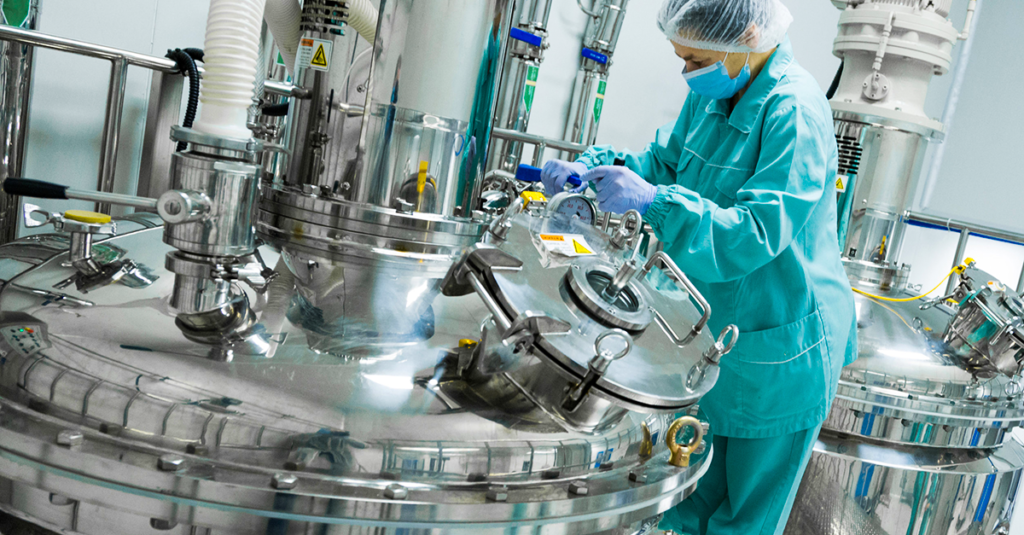
Maintenance Performance Plays a Vital Role In the Overall Productivity of Pharmaceutical Manufacturing
The pharmaceutical industry is one of the largest industries in the world, and over 45 percent of the global market is held by the United States, according to Statista. Pharmaceutical companies play a considerable role in the lives of individuals everywhere. However, many people still have a negative view of the pharmaceutical industry.
Still, the fact is that pharmaceutical companies have worked diligently to develop life-saving drugs, as the industry’s global pandemic can attest. There is little doubt that the pharmaceutical industry’s contributions to society have resulted in people living longer, more fulfilling lives. European citizens, for example, are now able to live 30 years longer than they did a hundred years ago.
Pharmaceutical plants are not without their challenges, however. There are regulations that must be followed, there are economic pressures, costs are accelerating, and technology is advancing rapidly, which means a pharmaceutical manufacturing plant must always be adapting and evolving. Given all of these obstacles, it can be difficult for a pharmaceutical manufacturer to stay competitive.
Good Manufacturing Practices (GMP) Must Be Followed at All Times in a Pharmaceutical Plant. If They Are Not, it Can Result in Tragedy.
There are many influences in the industry that demand higher quality, more efficient practices, greater industry collaboration, and superior manufacturing design. But as a pharmaceutical manufacturing facility advances to stay competitive and cost-efficient, executive management and frontline leadership must pay close attention to the organization’s maintenance performance.
While often overlooked or operating under a “run till it breaks” approach, maintenance performance is crucial in many industries, but it is critically important for pharmaceutical manufacturing. One of the most important things to avoid in a pharma plant is contamination, which can easily occur if old equipment isn’t maintained correctly.
It’s imperative that plant and facility directors, and everyone involved in plant management and leadership, follow Good Manufacturing Practices (GMP) in their manufacturing facilities. If they don’t, it can result in tragedy. An example of this would be the fungal meningitis outbreak in the United States in 2012, when a compounding pharmacy distributed contaminated vials to medical facilities in 23 different states. This complete maintenance failure and catastrophe led to 48 deaths and 720 patients requiring fungal infection treatment.
The Average Manufacturer Faces 800 Hours of Downtime Annually.
To avoid such tragedies, effective cleaning, sanitizing, and maintenance tasks must scheduled and performed diligently. Whenever there is new equipment, maintenance Standard Operating Procedures (SOPs) must be updated, and both cleaning and maintenance protocols must be followed strictly.
In addition to causing tragic contamination, improper maintenance can lead to unexpected downtime, which can cost a pharmaceutical plant quite a bit. Downtime is a problem that affects many different companies across a number of industries. The average manufacturer faces 800 hours of downtime annually. In the automotive industry, for example, this can cost (on average) $22,000 per minute of downtime. In the manufacturing field in general, IndustryWeek reports that unplanned downtime costs businesses $50 billion annually.
With unplanned downtime, there will of course be a loss of productivity, which can lead to a loss of customer trust. With pharmaceutical plants, downtime or maintenance performance issues can lead to drug shortages. It has been reported that 23% of drug shortages are caused by manufacturing issues.
Spending More Time Adequately Training of Maintenance Staff Can Prevent Downtime and Maintenance Performance Issues
Of all the unscheduled equipment downtime, operator error causes 18% of it, according to Plant Engineering. When staff and contractors are trained properly, it is less likely that there will be detrimental errors and mistakes that can cost hundreds of thousands of dollars.
So what is the key to preventing costly downtime as well as tragic contaminations in pharmaceutical plants? Maintenance performance improvement. One of the most important things that all maintenance departments should implement is working on preventive maintenance. On average, businesses will spend 80% of their time responding to maintenance issues that come up as opposed to preventing them (eMaint). According to Mintek, if a company focuses on preventive maintenance as opposed to reactive maintenance, they can save 12-18%. In addition, preventive maintenance can also decrease machine downtime by 30-50% and increase the life of a machine by 20-40%, according to McKinsey.
Pharmaceutical plants can also improve their maintenance performance in a number of ways:
Pharmaceutical Plants Can Also Improve Their Maintenance Performance in These Four Critical Ways:
Using a Risk-Based Approach to Maintenance
While many pharma plants treat all equipment equally, it’s more effective to classify each piece of equipment according to how much of an impact it has on product quality. It’s helpful to use four categories to assess each piece of equipment: direct impact (equipment that will affect product quality if it fails); indirect impact (equipment that will indirectly affect product quality if it fails); safety impact system (equipment that affects safety if it fails); and no impact (equipment that won’t affect product quality or safety if it fails).
Using Computerized Maintenance Management Systems (CMMS)
A CMMS will typically perform GMP-critical tasks such as assigning Unique Identifying Numbers (UINs) to each piece of equipment, scheduling maintenance activities, and holding records of any maintenance activities. A Plant Maintenance Study from 2016 showed that 51% of manufacturing facilities were using a CMMS, and according to ReliabilityWeb, a CMMS can improve the reliability of your equipment by as much as 35-50%.
Updating Maintenance Plans as a Part of a New Equipment Introduction
While engineers can get excited about new equipment, the maintenance plans should not be overlooked in the excitement. Update the maintenance department schedule and SOPs to include any new equipment. Train frontline leaders, and operators on the new procedures and scheduling requirements. This is also the time to determine if maintenance is adequately staffed to handle the workload or technical requirements of the new equipment and mmake any necessary adjustments in personnel.
Training Maintenance Staff Properly
It’s essential to ensure that all maintenance staff and contractors have the appropriate tactical skills and technical training before entering GMP areas. A complete approach to maintenance performance improvement includes looking at all labor and resources dedicated to maintenance, your MMOS (Maintenance Management Operating System), CMMS (Computerized Maintenance Management System), and more. If you do not have an MMOS or CMMS, it’s crucial to at least begin documenting all maintenance activities required for your business. Describe the who, what, when, and how of your company’s maintenance activities. And finally, be sure to consider the maintenance requirements when purchasing equipment. For many companies, maintenance is often the last thing considered when purchasing new equipment, but it should be given weight considering its impact on OEE (Overall Equipment Effectiveness), ROA (Return on Assets), reliability, quality, and uptime.
POWERS AMP (Advanced Maintenance Performance)
Transforming manufacturing operational performance requires analyzing the systems, processes, and behaviors woven into the fabric of an organization, from inputs to outputs, from the top floor to the shop floor. One area that should be on every organization’s radar for improvement is maintenance performance or MRO (Maintenance, Repair, and Operations). No other area of your operation can take such a big bite out of the bottom line. That’s why POWERS has launched a new end-to-end solution for maintenance performance improvement.
Our AMP (Advanced Maintenance Performance) Program improves both the tactical and technical aspects of maintenance in your operation. On the tactical side, we focus on improving your strategic approach to maintenance and your Maintenance Management Operating System: how you manage the people and resources devoted to maintaining your assets and equipment.
We also focus on the technical aspects of maintenance and provide hands-on training in Maintenance Fundamentals, Mechanical Concepts, Electrical Power, and Electrical Control. Nearly 60% of the current manufacturing maintenance workforce does not possess the skills and training necessary to keep the assets and equipment functioning at optimum levels. Improving your maintenance team’s skills unlocks OEE (Overall Equipment Effectiveness) bottlenecks in uptime, throughput, capacity, quality, and more.
The POWERS Difference
At POWERS, we focus on Leadership Engagement and Development to transform operational performance and prepare your leaders for the future. We help you build a performance culture that operates at peak levels to lower costs, increase productivity, build agility, and sustain that performance over the long haul.
Our team has helped executive leadership across many industries operationalize their culture for rapid and sustained performance improvement, increased competitive advantage, greater value, and a stronger bottom line.
Find out about our new AMP (Advanced Maintenance Performance) Program and put experienced team and proven track record to work for you. Schedule an initial discovery and analysis by calling +1 678-971-4711, or emailing us at info@thepowerscompany.com.