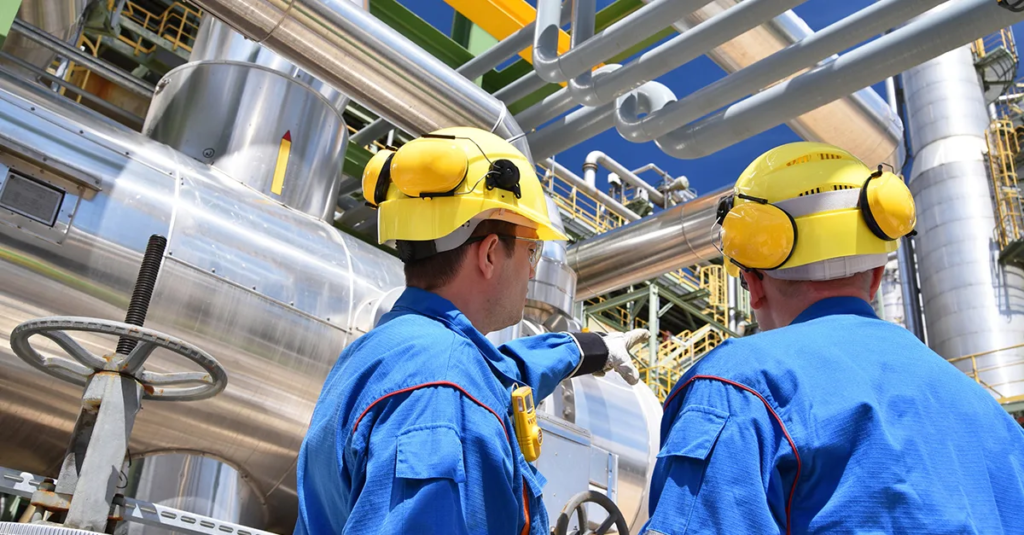
Maintenance performance excellence can be a key to unlocking supply chain bottlenecks and uncovering added capacity and throughput. Getting maintenance performance right can be like “found” money and dramatically impact your bottom line.
As is always the case with our approach to transforming manufacturing performance, we analyze the systems, processes, and behaviors woven into the fabric of an organization, from inputs to outputs, from the top floor to the shop floor. One “thread” we consistently pull on and put under the microscope is maintenance performance or MRO.
MRO stands for Maintenance, Repair, and Operations (or sometimes Maintenance, Repair, and Overhaul). MRO refers to the equipment, tools, and activities associated with performing daily business operations. MRO doesn’t include materials, products, and services used directly in production but instead acts as the glue that holds everything together. s.
MRO is often divided into four repair and maintenance categories:
Infrastructure
Production
The equipment used to process the inputs and outputs throughout the value chain.
Material Handling
Tooling and Consumables
This category of MRO covers any smaller, handheld tools required in day-to-day operations.
The types of MRO management adopted by organizations fall into these four categories, whether planned or unplanned:
- Corrective maintenance – Replace components upon failure. Only repair when there are errors.
- Preventive maintenance – Replace components before failure, repair equipment before the date of expected failure, prevent errors before they happen.
- Predictive maintenance – Monitor components, often with the advent of technological advancements like CMMS (Computerized Maintenance Management System), IIoT (Industrial Internet of Things), and Digital Twins. When problems are detected, take corrective action.
- Proactive maintenance – Identify and correct root causes of failure to help avoid maintenance issues.
Thomasnet.com has an excellent rundown of the entire MRO topic and is worth a read if you’re unfamiliar with its scope in your organization.
Expertly managing the reliability of every asset used to deliver along each link in your value chain involves transforming your MRO mindset from reactive to proactive to excellence. But with each departmental area and practically every production line straining under the current global supply chain and market demand pressures, how do you make maintenance a priority?
What we’ve found is this: maintenance performance excellence can be a key to unlocking supply chain bottlenecks and uncovering added capacity and throughput. Getting maintenance performance right can be like “found” money and dramatically impact ROA (Return on Assets).
In this economic climate, manufacturing facilities and operations managers constantly battle to increase profitability and minimize costs. Increasing production is often one of the corrective measures taken to decrease the unit cost. Unfortunately, this “lever” is sometimes pulled without considering the added maintenance requirements or impact on plant or production line reliability. Instead, production is ramped up without considering how long the equipment can sustain the increased output without going down or breaking entirely.
According to data from WSJ, unplanned downtime costs industrial manufacturers an estimated $50 billion annually. Equipment failure is the cause of 42% of this unplanned downtime.
When downtime and production losses increase, management sees it as a maintenance problem. However, the issue originated in management’s failure to assess the risk before the production increase and act accordingly. Whether senior managers realize it or not, minimizing cost while maximizing profit is dependent on equipment operating safely and reliably. That’s why maintenance has a big part to play in the overall health of your organization.
In a world where supply chain, cost reduction, and market demand pressures are through the roof, doesn’t it make sense to find any additional reliable and safe capacity and throughput from your existing assets? Maintenance performance excellence can be that key.
For example, we partnered recently with a world-class, 7th generation family-owned and operated meat processing company to improve performance. After our detailed “boots-on-the-ground” discovery and analysis, we uncovered that their MRO systems, processes, and behaviors presented significant opportunities for improvement.
This firm is squarely in the mix of delivering its products to a marketplace rupturing with demand pressures. After our initial findings, we implemented an MRO plan that helped increase productivity in their high-value line by 47%, yields across all lines by .41%, and an 85% improvement in maintenance labor utilization.
Your maintenance plan (or lack thereof) impacts every area of your operational performance.
Your maintenance plan (good, bad, or otherwise) impacts every area of your operational capacity, from production to transportation to distribution. For example, a “run-till-it-breaks” maintenance plan for your top-performing production line will certainly diminish capacity, throughput, and yields if it goes down unexpectedly.
Likewise, poor maintenance on your trucking fleet, lifts, loaders, and jacks can tremendously impact transporting inputs and outputs from one production stage to another. And maintaining refrigeration units for optimal storage (in the food industry, for example) can most certainly affect spoilage, warehousing, and distribution performance.
Every asset that your organization uses in your value chain, from initial material inputs to output and distribution of your finished goods, has been under the care of a maintenance technician. Whether you think about it often, have a plan, are looking to improve MRO, or not, maintenance impacts capacity, quality, lead-time and underpins the financial health of your operation.
So, what are the first steps to improving MRO and pursue maintenance performance excellence starting today?
1. Assess Where You’re At With Maintenance Performance
Like any improvement plan, the first step is understanding where you stand today. If you’re going to go on a diet, the first step is usually onto a scale. Undertaking a thorough analysis of your maintenance systems, process, and behaviors can be painstaking, but as we pointed out earlier, can result in a big payoff. Our approach to maintenance operations excellence involves a holistic discovery, assessment, and plan, touching vital MRO areas such as:
Systems
- CMMS
- IIoT
- Digital Twins
Processes
- Quality Control
- Planning & Scheduling
- Safety
- Maintenance Staffing
- Corrective, Predictive, or Preventative Identification
- Work Cycle
- Maintenance Business Impact
- Asset Analyses
- Management Structure
- Parts Management
- Change Management
- Equipment & Tools
- Lubrication
Behaviors
- Organizational Climate
- Training & Growth
Having an experienced team of “fresh eyes” uncovering your maintenance challenges can make a significant difference. Your frontline managers, maintenance technicians, and operators may be stressed to keep up with demand. Having an unbiased team of industry experts, well versed in managing and navigating the nuances of manufacturing facilities at the “shop floor” level, is vital to success.
Download our FREE Maintenance Performance Assessment Guide and find out where you stand.
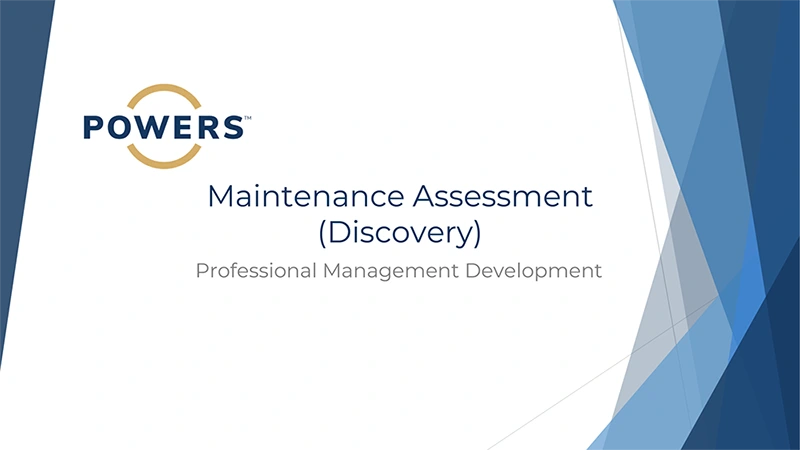
2. The Next Step: Moving Your Organization Toward Total Productive Maintenance
In many organizations, Total Productive Maintenance (TPM) is used. This holistic approach to equipment maintenance involves all stakeholders in maintaining the production asset, from managers to maintenance technicians to operators. The goal of TPM is to achieve perfect production with no breakdowns and where only small stops, accidents, or defects will occur.
There are eight supporting activities in TPM:
- Autonomous maintenance – Placing the responsibility for routine maintenance on the operators.
- Planned maintenance – Scheduling maintenance tasks based on measured and predicted failure rates.
- Quality integration – Integrating detection and prevention into production processes.
- Focused improvement – Encouraging small groups of employees to work together proactively to achieve regular, incremental improvements in equipment operation.
- Early equipment management – Directing understanding of equipment towards improving new equipment designs to include maintenance and preventive maintenance, safe access for technicians and operators, service and part replacement safe and efficient accessibility, ease of cleaning, lubricating, diagnostics, etc.
- Training and education – Filling in knowledge gaps to achieve TPM goals.
- Safety, health, environment – Maintaining a safe working environment.
- TPM in administration – Applying TPM techniques to administration functions ensures that your current or future CMMS system can track and generate equipment life history and prompts.
The Benefits of TPM
Total Productive Maintenance empowers employees and other stakeholders in your value chain to take responsibility for productivity and equipment maintenance. This approach can be incredibly beneficial to manufacturers, particularly in the areas of:
- Efficiency – It requires manufacturers to look at quality over quantity and prioritize efficiency over output.
- Morale – By empowering employees to be responsible for the upkeep of equipment, employees can have more pride in their work.
- Safety – Focusing on preventive and proactive maintenance can bring more order to the workplace, increasing employees’ safety.
- Satisfaction – By increasing quality, efficiency, and employee morale, manufacturers will see more customer satisfaction.
- Profit – Total Productive Maintenance can help minimize cost and maximize profit throughout your value chain.
3. Go Beyond TPM in Pursuit of Maintenance Performance Excellence
At POWERS, we use the principles of TPM, which can be incredibly effective. However, we also take these improvement principles a step further in pursuit of maintenance performance excellence. Here’s what we add to TPM:
- We make sure what the operators are doing is tied to specific qualifications and skills. For example, some maintenance jobs need to be done by qualified workers (electricians, in the case of electrical work). We identify which parts of the work the operators should perform and provide training as necessary. This process would include capturing work in the CMMS and providing them prompts to conduct timely.
- We maximize the utilization of maintenance technicians and equipment availability, as planned maintenance must be performed when equipment is available.
- We go beyond equipment uptime to ensure that equipment is not only running smoothly but making quality products.
- We analyze equipment history and link that information to timing to predict how long equipment will last, such as tracking mean time between failures driving root cause and elimination.
- We go beyond skills, training on the concept of preventive maintenance so that equipment is so reliable, maintenance workers can be used to do other things.
The POWERS Difference
We’re not your typical management consulting firm. Instead, our “shop floor to top floor” approach is designed to uncover opportunities to minimize cost and maximize profit. First, we analyze your current maintenance processes to develop a plan customized to meet your organization’s immediate and long-term needs. Then, we help you implement the plan so that your maintenance team can become accustomed to any new processes. Our team is “hands-on,” providing training and coaching along the way. With the improvement of maintenance performance and the implementation of best practices, overall productivity will increase.
As an external presence in your organization, we can analyze your maintenance processes objectively and help drive maintenance performance improvement. When improving a manufacturing maintenance optimization, you need to talk to an expert. We hold a mirror up to your organization, providing an unbiased view of your current processes. We identify the areas where your maintenance department is performing well and the areas where there could be some improvement. Then, we work with your organization to develop a plan, implement the training across your plant, and empower you to see a maintenance performance improvement.
Our focus areas at POWERS include frontline leadership training, supply chain management, maintenance performance improvement, and shop floor excellence. Our unique approach aligns your workplace culture with performance outcomes in these vital areas of your business. We call it “operationalizing your culture,” and it’s a game-changer.
To schedule an initial discovery and analysis with our dedicated management consulting team, please call us at +1 678-971-4711, email us at info@thepowerscompany.com, or provide your contact information here.