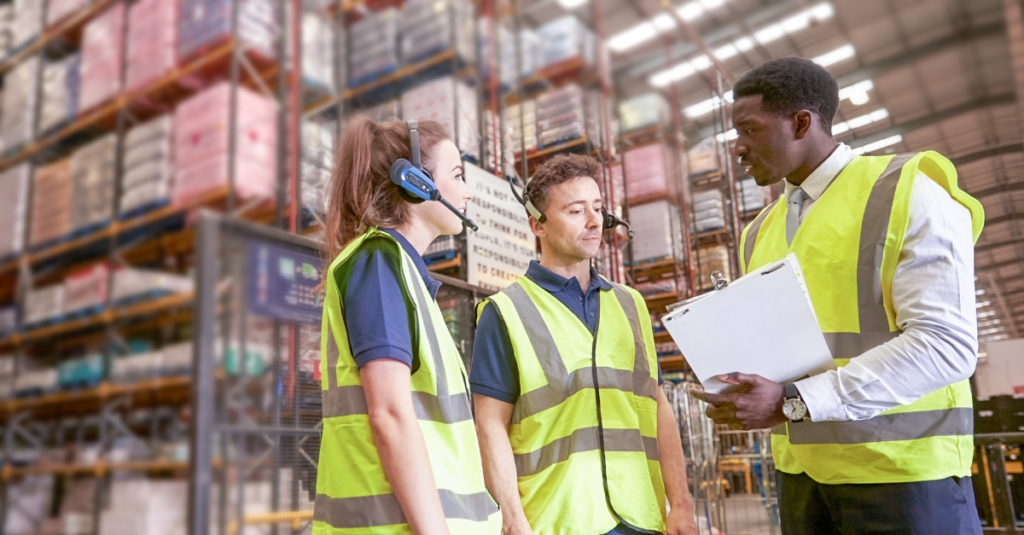
In the rapidly changing landscape of American manufacturing, leaders at all levels must adapt and develop their leadership skills to remain competitive, bolster against economic uncertainy, and improve the bottom line.
Over our many years working as manufacturing leaders to improve productivity, we’ve experienced firsthand the importance of strong frontline leadership in driving organizational success. That’s why at POWERS, it is a requirement to have been a frontline leader to work on our team and why frontline leadership development is one of our primary focus areas.
In the rapidly changing landscape of American manufacturing, leaders at all levels must adapt and develop their skills to remain competitive. As the economy continues to present challenges at many levels, American manufacturing will come up against new obstacles that will strain its resources and burden leaders out on the front line.
In this article, let’s look at ten of the frontline leadership skills that, in our experience, will be most important for US manufacturers to stay ahead of market stressors in the short term and over the long haul. We’ll also cover four skill areas that are often overlooked but can be the difference makers in increasing your value and improving the bottom line.
10 Essential Leadership Skills to Develop in Your Frontline Managers and Supervisors
- Adaptability and flexibility: The manufacturing industry constantly evolves, with new technologies, materials, and processes emerging rapidly. As such, leaders must be able to adapt to change and embrace new ways of doing things. This includes being open to new ideas and approaches, as well as being flexible in the face of challenges and setbacks. Leaders who are more adaptable to change increase their value to the organization and are more likely to be satisfied in their work and more productive.
- Collaboration and teamwork: In the modern manufacturing environment, it is increasingly common for organizations to work in cross-functional teams and with external partners. As such, leaders need to build and maintain strong relationships with team members and stakeholders and foster a culture of collaboration and teamwork.
- Communication and interpersonal skills: Effective communication is key to any leadership role, and this is especially true in manufacturing, where leaders may need to communicate with a diverse group of individuals, including team members, customers, and suppliers. This includes conveying information clearly, listening actively, and resolving conflicts effectively.
- Problem-solving and decision-making: Leaders in manufacturing are often faced with complex problems that require innovative solutions. Leaders need to be able to think critically and creatively and to be able to make sound decisions based on data and analysis.
- Emotional intelligence: Emotional intelligence is the ability to recognize and manage one’s own emotions, as well as the emotions of others. This is an essential skill for leaders in manufacturing, as it enables them to build strong relationships, communicate effectively, and resolve conflicts out on the shop floor that can stifle productivity.
- Leadership development: As the manufacturing industry continues to evolve, it is critical for leaders to develop their skills and knowledge continuously. This includes staying up-to-date on industry trends and best practices, as well as investing in the development of their team members.
- Innovation and creativity: Organizations must continuously innovate and differentiate themselves from their competitors in a competitive industry like manufacturing. Leaders who can encourage and support creativity and innovation within their teams will be well-positioned for success. A recent study cited in Forbes found this: as an organization’s creativity and innovation increases, so do critical performance metrics. 67% showed above-average revenue growth, 70% exhibited above-average returns to shareholders, and 74% scored above-average net enterprise values.
- Process improvement: Lean manufacturing principles have long been a staple of the manufacturing industry, and for good reason. Leaders who can identify and eliminate waste, and streamline processes, will be able to drive efficiency and improve the bottom line.
- Quality and continuous improvement: Ensuring high-quality products is essential for any manufacturing organization. Leaders who drive a continuous improvement and quality culture will be well-positioned for success.
- Safety: Ensuring the safety of team members is not only the right thing to do, but it is also essential for the success of any manufacturing organization. Leaders who can prioritize safety and implement effective safety programs will be able to reduce accidents and injuries and improve overall productivity.
4 Additional Frontline Leadership Skill Areas Often Overlooked But Vital to Manufacturing’s Future
But beyond the above ten essential skill areas to develop in your frontline leaders lies four more that can be real game changers. Fostering these skills can position your organization for the future, increase your competitive advantage, and help you adapt more quickly to rapidly changing market conditions like we’ve seen over the past few years. Readying your frontline leaders for the future of manufacturing is essential for your continued success and a healthy bottom line.
- Digital literacy: With the increasing use of digital technologies in manufacturing processes, leaders need to be proficient in computer systems, software, and other digital tools. This skill set includes using these tools effectively and understanding how they can be used to improve processes and increase efficiency. Frontline leaders in manufacturing with a complete digital skill set are the new standard.
- Lead and manage diverse teams: As the manufacturing industry becomes more globalized, it is increasingly common for organizations to have team members from a variety of cultural backgrounds. This diversity can bring a wealth of knowledge and perspective to the organization, but it also requires leaders to communicate and manage a diverse group of individuals effectively. A recent HBR article shows that leaders that effectively manage diverse teams increase the creativity and innovation of the organization and be a significant competitive strength.
- Strong business acumen: In addition to technical skills, it is also essential for leaders in the manufacturing industry to have strong business acumen. This includes understanding financial principles, like budgeting and forecasting, and making strategic business decisions. The more your frontline leaders understand the business ramifications of their daily decision making, the stronger your organization becomes financially.
- Building relationships with external stakeholders: Another essential leadership skill in manufacturing is building relationships with external stakeholders, such as customers, suppliers, and regulatory agencies. Strong relationships with these stakeholders can help an organization secure new business, negotiate favorable terms, and navigate regulatory challenges. Better supplier and vendor relationships lead to lower costs and improved efficiency. If the last few years have taught us anything, it’s that supply chain resiliency depends on solid supplier relations.
Conclusions for Senior Leaders
The frontline leadership skills that will be most important for US manufacturers in the coming year and into the future include adaptability and flexibility, collaboration and teamwork, communication and interpersonal skills, problem-solving and decision-making, emotional intelligence, leadership development, innovation and creativity, process improvement, quality and continuous improvement, and safety. By developing and honing these skills, leaders in manufacturing will be well-equipped to drive organizational success in the years ahead.
For future-proofing your organization, your frontline leaders will need digital literacy to gain every technological advantage. In addition, effectively leading a diverse group of people, strong business acumen, and the ability to build strong external stakeholder relationships will contribute heavily to the success of your organization and carry it into the coming years and through any economic conditions.
And yes, that is a long list of leadership skills to develop in your people. And there are certainly more. The key is to start. Assess where your leaders are in their development and where they may need the most training and support, and begin there. Being concise and surgical, rather than taking a shotgun approach to your leadership development, is critical to its success, sustainability, and scalability. You want a leadership development program that is strategic, ongoing, forward-looking, and perfectly suited to your values and purpose as a company. We can help you build that program. That’s what we do.
The POWERS Difference
At POWERS, we focus on Leadership Engagement and Development to transform operational performance and prepare your leaders for the future. We help you build a performance culture that operates at peak levels to lower costs, increase productivity, build agility, and sustain that performance over the long haul.
Our team has helped executive leadership across many industries operationalize their culture for rapid and sustained performance improvement, increased competitive advantage, greater value, and a stronger bottom line.
To put our experienced team and proven track record to work for you, schedule an initial discovery and analysis by calling +1 678-971-4711, or emailing us at info@thepowerscompany.com.