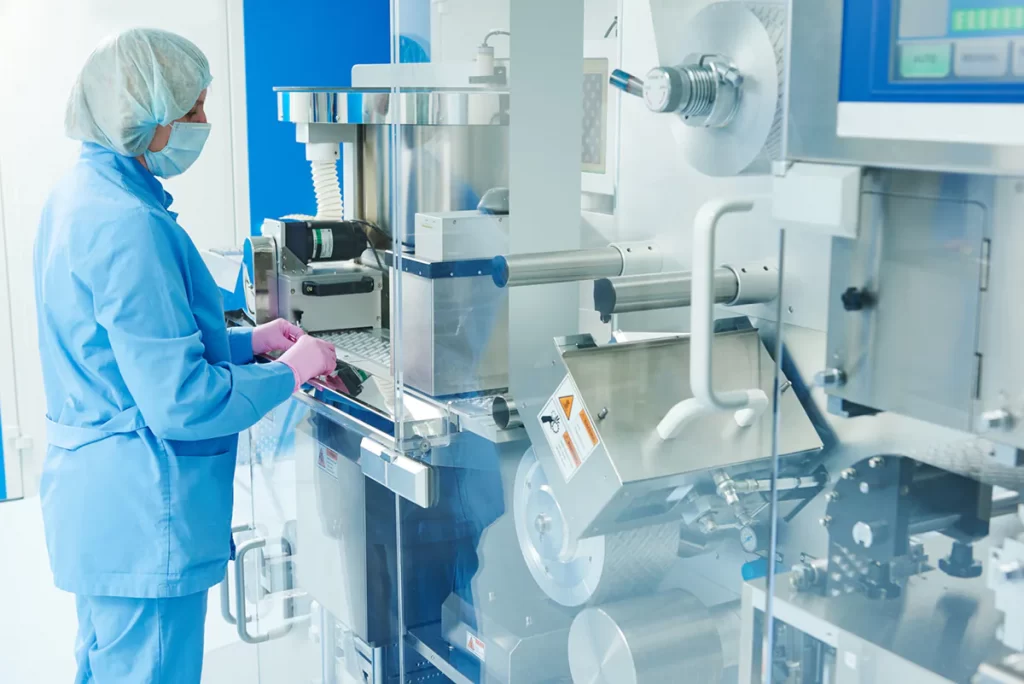
As the COVID-19 pandemic continues, there doesn’t seem to be one person or business that hasn’t been affected. Over the past few weeks, we’ve been taking a look at how the pandemic is impacting different industries. Specifically, we’ve examined the food and beverage industry as well as the paper industry. Today, we want to take a look at how this public health crisis has affected the medical device manufacturing industry.
Recently, medical device manufacturing has been in the spotlight as hospitals and healthcare workers all across the country have been in need of ventilators and other supplies to treat patients who have been infected with COVID-19. Shortages have been described throughout the country. There was the story of Dr. Sun, an ER doctor in New York, who has had to wear ski goggles and a ski jacket as personal protective equipment. Also, a pulmonary surgeon in Manchester, Connecticut has designed a device that allows two or more patients to utilize a single ventilator in the event of a spike in the hospitalization rate. There have even been physicians throughout the country who have had to make heartbreaking decisions about which patients to save.
No one was prepared for the COVID-19 pandemic, and the number of patients requiring treatment led to this shortage. The reasons we were not prepared as a nation to face this crisis have been debated, but the most important thing is where we go from here.
Manufacturers Ramp Up Production
The Advanced Medical Technology Association recently stated that its member respiratory device companies–including Draeger, Hillrom, Philip, and Medtronic among others–“have dramatically expanded the limits of their present production capacity.” Company officials are expected to ramp production up to somewhere between 5,000 and 7,000 ventilators per week.
Other manufacturers–like Indianapolis-based Genesis Plastics Welding Inc.–have increased production of hyperbaric oxygen hoods. These efforts are said to help to free up ventilators for coronavirus patients who are the most critically ill. The president and chief executive officer of Genesis Plastics Welding, Tom Ryder, recently stated, “At our core, we are makers, and America’s critical medical device manufacturing infrastructure has an important role to play in keeping essential products flowing into our hospitals. We’re all in this together, and I’m proud to be able to leverage our expertise to meet rising market demand for oxygen hoods amid the worldwide pandemic.”
Manufacturers who serve multiple industries have made medical devices their main priority. Protolabs, a quick-turn manufacturer in Maple Plain, Minnesota, has recently seen an influx of medical components that need urgent production due to COVID-19. These range from ventilators to test kits to respirators. A spokesperson for the company recently said, “We are urgently putting internal protocols in place to be able to prioritize these orders ahead of all others and waiving expedite fees in order to quickly get critical medical supplies into the market.” Additionally, Web Industries has dedicated production at their 6,500-square-foot facility in Holliston, Massachusetts to LFI tests specifically for COVID-19.
Is This a Wake-Up Call for Domestic Production of Medical Devices?
Many have argued that this shortage has exposed how we need to reshore medical device manufacturing jobs to the United States. Medical supplies accounted for approximately $53 billion worth of imports last year. Reshoring production for even half of those supplies could add $54 billion to GDP and generate an additional 302,000 jobs. Jeff Ferry of MarketWatch argues, “The United States is the world’s largest economy and needs to have the capability to make these vital health-care supplies at home. Only 30 years ago, we did have that capability. However, the rush to globalize — and to abandon key manufacturing sectors — has left the nation vulnerable during this crisis. It’s time to restore our capability to manufacture at home.”
Many countries have stopped exporting essential medical devices to other countries. In late March, for example, the European Union announced that it would be restricting the export of personal protection equipment, and the Indian government banned the export of both sanitizers and ventilators since March 24th. There are also quality issues that can come from importing medical devices. The Netherlands, for instance, recalled nearly half of a shipment of 1.3 million masks from China as they did not meet quality standards. The domestic manufacturing of these essential medical devices can ensure product quality and overcome any trade barriers that may occur.
Other Industries Step Up to Help
It’s been inspiring and uplifting to see how everyone has stepped up to help out during this public health crisis. Manufacturers from other industries are now manufacturing medical devices. Voodoo Manufacturing, a 3D printing company, got clearance from the US Food and Drug Administration (FDA) to produce medical devices. They are part of a private-sector push that has seen fashion designers, distilleries, automakers, and perfume producers manufacturing medical devices and health care supplies that aren’t being provided fast enough by traditional supply chains.
On March 30th, Ford announced that it would be collaborating with General Electric Healthcare as well as medical device manufacturer, Airon, to utilize its Rawsonville Components Plant located in Ypsilanti, Michigan to produce ventilators. The goal is for the company to produce 50,000 machines within 100 days and then 30,000 every month as needed. Ford has a history of stepping up to help, manufacturing iron lungs in the 1940s for polio patients.
The innovation we have seen from other companies and individuals has also been inspiring. For example, Tesla engineers have designed a ventilator prototype that utilizes parts from electric vehicles. We have also seen a great deal of innovation with 3D printing in the medtech space.
As the COVID-19 pandemic continues, it will be interesting to see how medical device manufacturers are able to increase production. In the meantime, it’s definitely a piece of positive news to see other industries step up to provide for the urgent needs of healthcare workers. And that’s something we could all use more of.