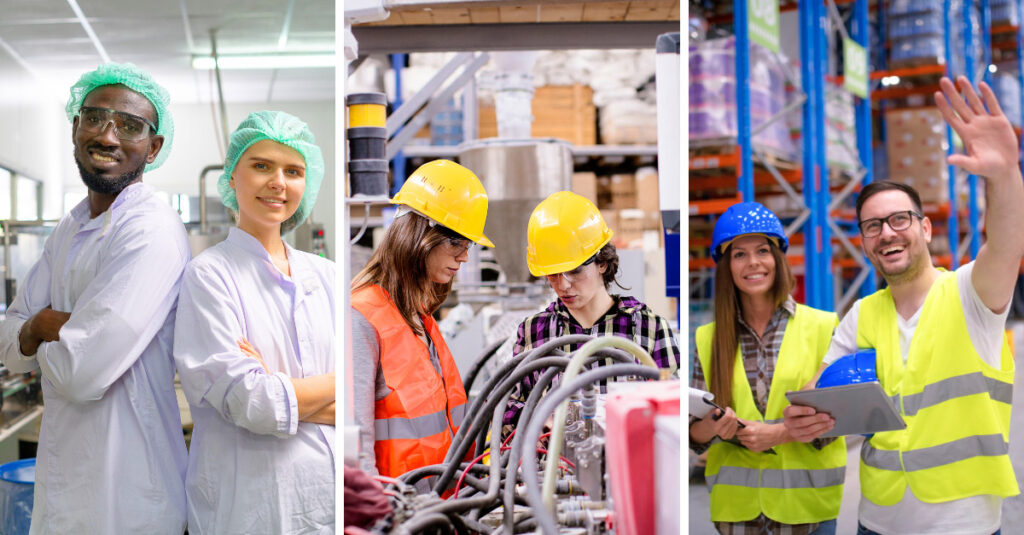
In the highly competitive and rapidly evolving sphere of manufacturing, productivity and process improvement are not just buzzwords—they form the crux of operational efficiency and profitability. Yet, what really gives these elements their true value and enables them to be truly transformative and drive sustainable growth is an often-underappreciated factor: a strong workplace culture.
More specifically, the fostering of a workplace culture rooted in excellence and continuous improvement can be the ultimate determinant of the long-term sustainability and scalability of productivity and process improvements.
The Power of Productivity and Process Improvement
Productivity, or the efficiency of production, is a fundamental objective for any manufacturing organization. Greater productivity can lead to lower operating costs, an enhanced competitive position, and ultimately, increased profitability.
Integral to achieving this objective is process improvement—a systematic approach to refining and optimizing operational procedures.
Yet, these improvements can’t exist in a vacuum. Their long-term sustainability and scalability are intricately tied to the organization’s workplace culture—a factor sometimes overlooked amidst the hard metrics. In the words of Peter Drucker, “Culture eats strategy for breakfast.” This is where an organizational focus on building a culture of excellence and continuous improvement comes into play.
Workplace Culture: The Secret Ingredient
Amid the quest for hard metrics and tangible outputs, the role of workplace culture can be overlooked, despite its vital importance. Workplace culture encapsulates the shared values, behaviors, and practices that shape the work environment and define how things get done within an organization.
In a culture of excellence, the bar is set high. Employees are encouraged not just to meet expectations, but to exceed them, and to do so consistently. This involves continually learning, adapting, and improving.
Research indicates that a strong culture of excellence can boost employee engagement, commitment, and performance. When employees feel a part of something bigger, they are more likely to take ownership of their work, leading to heightened productivity and better-quality outputs. In other words, a company’s culture can become a significant enabler of sustained productivity and process improvement.
Continuous Improvement: A Driving Force for Sustainable Growth
When we talk about continuous improvement, we refer not only to the ongoing refinement of processes and systems, but also to a culture that encourages innovation, learning, and problem-solving. In a culture of continuous improvement, employees at all levels are empowered to question the status quo, identify issues, and propose solutions.
Continuous improvement plays a pivotal role in an organization’s long-term sustainability. By instilling a mindset of continual evolution and adaptation, a company can ensure that it remains nimble and responsive to shifts in market dynamics, technological advances, and customer expectations. This culture of continuous improvement serves as a powerful engine for innovation, driving the company towards sustainable growth.
Laying the Groundwork for a Culture of Excellence and Continuous Improvement
So how can a manufacturing company cultivate a culture of excellence and continuous improvement? This transformation doesn’t happen overnight, and it requires a well-thought-out approach. Here are some crucial steps:
1Leadership Commitment
A shift towards a culture of excellence and continuous improvement must start at the top. Leaders need to demonstrate their commitment to this transformation in both their words and actions.
2Effective Communication
The vision, values, and strategies associated with the culture shift need to be communicated effectively throughout the organization. This includes clearly articulating the benefits of the change for both the organization and its employees.
3Employee Engagement
Encouraging employee participation in process improvement initiatives can foster a sense of ownership and commitment. Employees should feel empowered to suggest improvements, challenge existing practices, and contribute to problem-solving.
4Recognition and Rewards
Recognizing and rewarding employees for their contributions can boost morale, encourage further participation, and reinforce the behaviors and attitudes that support a culture of excellence.
5Training and Development
Ongoing training and development programs can equip employees with the necessary skills and knowledge to drive continuous improvement. This may involve training in specific process improvement methodologies, as well as in soft skills such as problem-solving, critical thinking, and communication.
6Measurement and Feedback
Regular monitoring and feedback mechanisms can help ensure that improvements are being effectively implemented and are yielding the desired results. Feedback, both positive and constructive, should be shared openly and regularly to promote ongoing learning and improvement.
Conclusion for Business Leaders
While productivity and process improvement are undoubtedly crucial for manufacturing organizations, the key to achieving sustainable and scalable improvements lies in developing a strong culture of excellence and continuous improvement.
It’s about creating an environment where every employee is committed to doing their best, continually learning, and striving for excellence at all levels. This is the magic glue that binds everything together, propelling organizations towards sustainable growth.
The POWERS Difference
We are a dedicated and results-driven management consulting firm uniquely positioned at the intersection of workplace culture and operational performance. We partner with growth-oriented organizations to cultivate a culture of excellence that fuels productivity, drives efficiency, and strengthens competitive advantage.
Leveraging our deep industry expertise and innovative methodologies, we build synergies between people and processes, creating holistic, sustainable change that translates into measurable business outcomes.
Our team has helped executive leadership across many industries operationalize their culture for rapid and sustained performance improvement, increased competitive advantage, greater value, and a stronger bottom line.