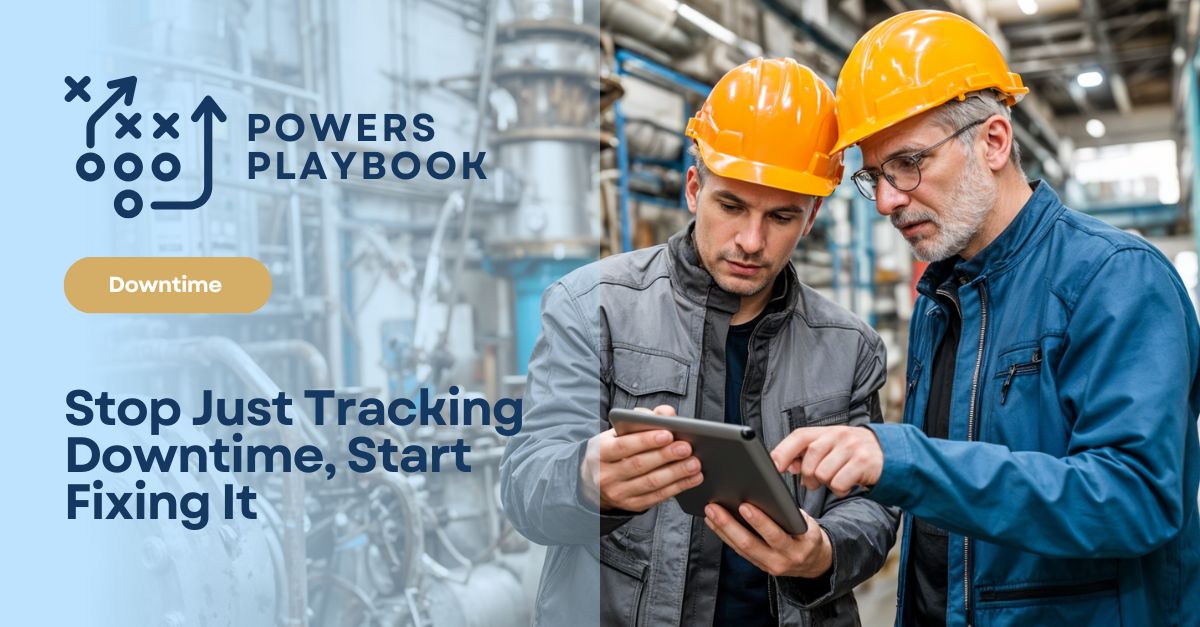
Downtime is one of the easiest things to track on the shop floor, yet one of the hardest things to act on consistently.
You know the drill: a machine stops, someone logs the time, maybe picks a downtime code, and that’s it. The line starts back up, but the cause and the fix? It gets lost in the noise of the day. Then the same issue shows up again next shift, next week, or next quarter.
And if no one’s tracking what happened next, it becomes impossible to learn from it, fix the root cause, or prevent the same thing from happening again.
The Real Problem Isn’t Downtime, It’s What Happens After
Frontline supervisors are already pulled in ten directions, managing people, keeping production moving, responding to issues, and trying to hit shift targets. In the rush to restart the line, downtime logs become a checklist item, not a conversation starter.
Here’s what that often looks like:
- You’ve got hours of downtime recorded, but no details on what was done to fix the issue.
- The same machine fault keeps popping up, and nobody notices because no one looks past the codes.
- Operators stop bothering to log minor stops, they don’t see the point.
It’s not just about collecting data. It’s about using it to make the job easier tomorrow than it was today.
The Quick Win: Add One Simple Step
Don’t just track the stop. Track what happens next.
What action was taken? Who responded? Was the problem fixed, patched, or ignored? Did it escalate to maintenance? Or did the team just power through?
It doesn’t need to be complicated or time-consuming:
- Add a second column or field in your log for “Action Taken” or “Follow-Up.”
- Keep it simple: “reset breaker,” “swapped part,” “called tech, no response,” or “temporary fix, needs maintenance review.”
- Make this part of your shift change: “Here’s what went down, here’s what we did, here’s what still needs eyes on it.”
This one small habit builds accountability and creates visibility across shifts.
It’s Not About Blame, It’s About Building Patterns
Once you start tracking both the stop and the response, patterns start to emerge.
For example:
- A conveyor motor throws the same error every third shift. Action taken: “reset and restart” every time. That’s a red flag, this is more than just a glitch.
- A sealing machine has five different minor stops, all related to film loading. The actions logged point to setup inconsistencies, not mechanical failure.
- No action logged at all? You may be dealing with training gaps, communication issues, or unclear roles.
These are the insights that help you move from fire-fighting to problem-solving.
Quick Win in Action: Small Fixes, Big Impact
Scenario:
- Line 3 goes down mid-shift. Again.
- The log shows: “stop, cleared jam manually.”
- This time, the operator adds: “jammed at sensor 7, film pulled off-track.”
- Same issue happened three days ago, same sensor.
What Changed:
- Supervisor flags it to maintenance. Quick inspection finds worn sensor bracket causing misalignment.
- Replaced in under 15 minutes.
- No more jam. No more mid-shift downtime.
That’s a five-minute log note that prevented hours of future lost time.
Don’t Let Lost Time Become Normal. Let’s Fix It.
POWERS helps manufacturing teams move beyond just tracking downtime, we help you reduce it for good. That means aligning frontline behaviors with operational goals and building a system where every stop has a follow-up, and every fix gets shared.
With our DPS platform, your team captures more than just when and where downtime happens, they document what was done, what worked, what didn’t, and what needs to happen next. This information is added to a growing knowledge base, accessible to everyone, not buried in notebooks or locked in someone’s head.
That means:
- Operators and techs don’t waste time repeating work that’s already been done.
- Supervisors don’t start from scratch every shift.
- Maintenance doesn’t get surprised by recurring issues no one flagged properly.
The DPS knowledge base becomes your team’s go-to resource for real-time troubleshooting, smarter handoffs, and fewer repeat failures—all of which cut down on one thing: lost time.
✅ Less chasing info.
✅ Faster fixes.
✅ Smarter decisions, without increasing headcount.
Ready to stop logging and start solving?
Contact POWERS today to see how our team and the DPS platform can help you build a frontline knowledge base that keeps your operation moving.
- Speak to an Expert: Call +1 678-971-4711 to discuss your specific challenges and goals.
- Email Us: Get tailored insights by emailing info@thepowerscompany.com
- Request an Assessment: Use our online contact form, and one of our expert manufacturing consultants will reach out to schedule an in-depth analysis of your operations.