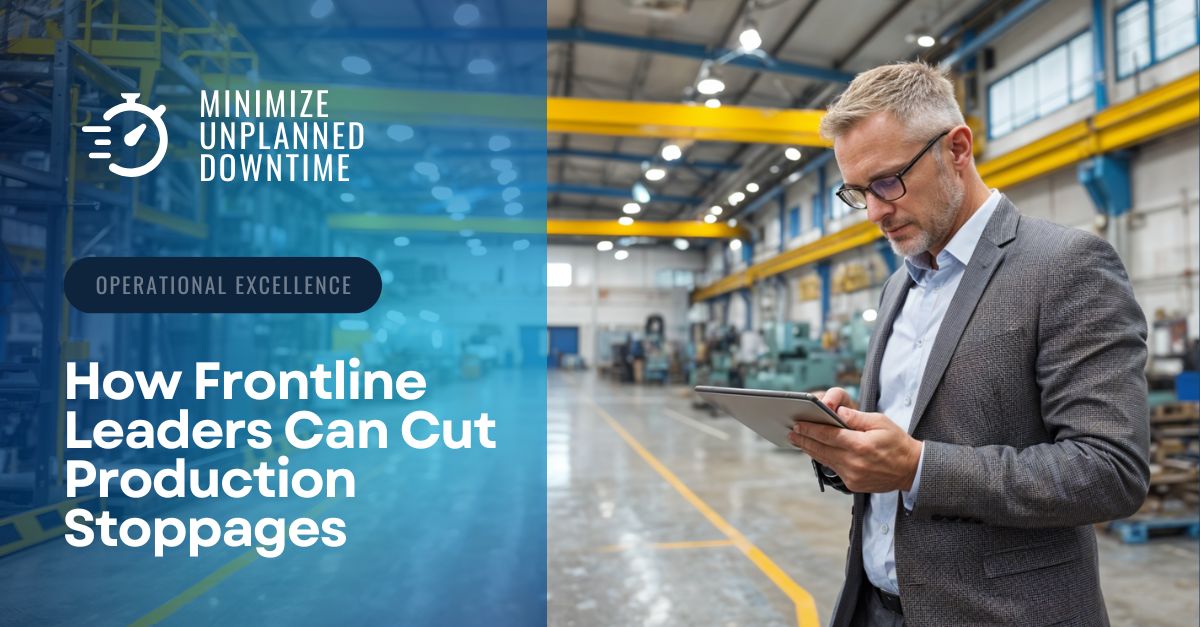
Sean Hart, Chief Executive Officer And Managing Partner, POWERS
Unplanned downtime, akin to a sudden jam in your production line, not only halts output but also incurs a staggering cost of $260,000 per hour, as per industry studies.
These unexpected stoppages, be it due to a machine breakdown or a delayed material delivery, are a significant source of production losses, contributing to lost time: any moment your plant isn’t running at capacity due to unforeseen issues or inefficiencies.
While you can’t prevent every pause—planned maintenance is part of the game—you can certainly address the unforeseen breakdowns and delays that disrupt your schedule—the key lies in fostering a proactive team mindset supported by structured processes.
We witnessed this transformation with a packaging client who significantly reduced unexpected stoppages by empowering leaders to anticipate problems and streamline operations, not just patch them.
Here’s how your frontline leaders can minimize unplanned downtime and keep production on track.
Spot Issues Before They Strike
Unplanned downtime often starts with subtle clues—a machine running rough, an operator skipping a step, or a part shipment running late. Leaders who overlook these signs end up with a stopped line. We train supervisors to catch these early warnings, coaching them to act before a hiccup becomes a halt.
One client we worked with reduced unforeseen downtime by 10% after leaders started flagging equipment wear during daily checks. Building a work environment where anticipation is routine helps cut production losses tied to unexpected stops.
Action Step
Run weekly coaching sessions to train leaders to spot warning signs. Have them walk the floor daily, note anything off, and follow up quickly.
Streamline Operations with an Optimized MOS
Disorganized processes fuel unplanned downtime. A vague SOP, a sluggish changeover, or a messy shift handoff can trigger delays that pile up. Our tailored Management Operating Systems (MOS) align your operations with clear KPIs and repeatable processes to minimize these surprises.
For example, we built a customized MOS for one manufacturer and used a SMED (Single Minute Exchange of Die) approach to shave 15 minutes off every changeover, cutting unforeseen delays by 12%.
Action Step
Review your changeover and startup processes with your team. Simplify and document them in a clear SOP, then train everyone to follow it.
Coach Teams to Stay Accountable
Your operators are your eyes on the line and must feel responsible for keeping it running. A work environment where everyone flags potential issues—like a worn part or a setup error—stops downtime before it starts. Our coaching programs teach supervisors how to build this team mindset, using feedback and recognition to drive accountability.
Thanks to regular coaching, one plant that engaged our team cut unplanned downtime by 20% after operators began reporting issues during pre-shift checks. Accountable teams mean fewer unexpected losses.
Action Step
Start daily 5-minute huddles where operators share observations and get feedback. Recognize those who catch issues early to make it stick.
Build Habits to Keep Downtime Low
A work environment grounded in consistent and effective habits is the best way to minimize unplanned downtime. A quick pre-shift huddle to spot risks. A daily equipment check to catch wear. A clear handoff to ensure smooth startups. These small steps, reinforced by a custom MOS, make a big difference.
A snack food plant we partnered with reduced unforeseen downtime by 25% by making pre-shift checks and clearer SOPs routine. That's fewer stoppages, more uptime, and a stronger bottom line.
Action Step
Pick one habit, like a 10-minute pre-shift huddle, to review risks and make it non-negotiable. Use it to keep your team aligned and proactive.
Keep Your Line Running
Unplanned downtime drives production losses, but a proactive work environment can keep it in check. You can minimize unforeseen stoppages and maximize output by training frontline leaders to spot issues early, using a customized MOS to streamline operations, coaching teams to stay accountable, and building smart habits.
At POWERS, we’ve helped manufacturers like you tackle these challenges with practical solutions that deliver—higher OEE, lower costs, greater profit, and teams that keep things moving. DPS, our Digital Production System, helps make those improvements scalable and sustainable over the long haul.
- Speak to an Expert: Call +1 678-971-4711 to discuss your specific challenges and goals.
- Email Us: Get tailored insights by emailing info@thepowerscompany.com
- Request an Assessment: Use our online contact form, and one of our expert manufacturing consultants will reach out to schedule an in-depth analysis of your operations.