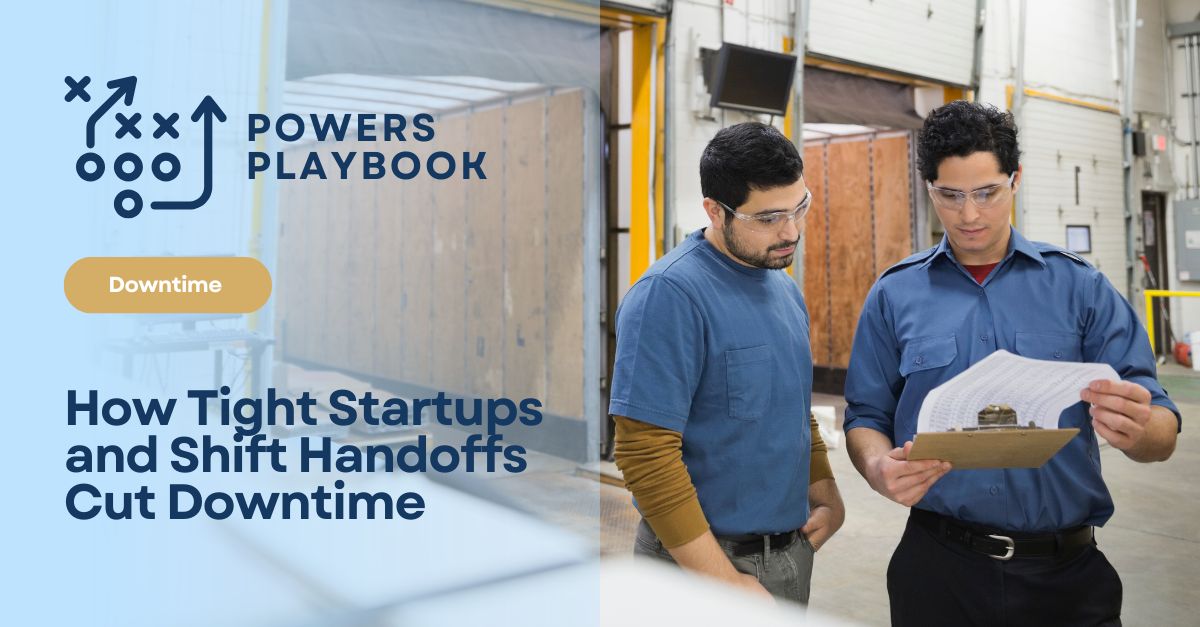
Every shift on the floor starts the same way: the team clocks in, the machines fire up, and the day gets moving.
But what happens in those first 15–30 minutes determines whether you’re on pace, or playing catch-up all day long.
Tight startups and smooth shift handoffs might not sound flashy, but they’re some of the most powerful tools supervisors have to reduce production interruptions. Done right, they prevent hours of avoidable slowdowns, confusion, and rework.
Where Downtime Really Begins
Downtime doesn’t always come from broken machines or missing parts. It often starts with small breakdowns in routine:
- The line’s ready, but the material isn’t.
- No one knows what the last shift did to fix an issue.
- Operators waste time getting up to speed.
- The team isn’t aligned on production targets or problem areas.
These small misses might not show up as a red flag in your downtime log, but they chip away at your output, quietly and consistently.
When this happens at the start of a shift or during handoff, the whole day gets dragged down. That’s productivity you won’t get back.
Structured Startups: Small Habit, Big Impact
Structured startup routines aren’t about paperwork, they’re about rhythm. When the first 15 minutes are focused, clear, and consistent, the rest of the shift runs smoother.
A good startup process:
- Creates alignment: everyone knows the plan, the goal, and their role
- Prevents delays: small issues are spotted early and dealt with quickly
- Builds momentum: teams start the day with energy and direction
And this doesn’t require a full-blown overhaul. Most teams just need a basic checklist, a short pre-shift huddle, and a little consistency to see improvements.
The Handoff: Where Good Days Can Go Bad
Shift handoffs are one of the most overlooked parts of the day — and one of the most critical. When done well, the next shift hits the ground running. When done poorly, the first hour becomes a scavenger hunt:
- What’s running?
- What’s broken?
- What did the last shift fix, and what still needs attention?
If the outgoing team is rushing to the door or the handoff relies on memory alone, chances are something’s getting missed.
That means operators waste time figuring out problems that were already solved, or worse, they assume something was handled when it wasn’t, leading to repeat issues and extended downtime.
Quick Wins You Can Use Right Now
If you’re a supervisor looking for something actionable today, start here:
Startup Checklist That Covers the Basics
Keep it short and sharp. Check for:
- Machine status and safety checks
- Raw material staging
- Known issues or alerts
- Staffing gaps or line changes
- Production goals for the shift
5-Minute Startup Huddle
Gather the team before the line starts. Talk through:
- What went wrong last shift (and what was fixed)
- What targets need to be hit today
- Any bottlenecks or areas to watch
- Operator suggestions or concerns
Consistent, Documented Handoff Notes
Use a whiteboard, handoff log, or digital tool to cover:
- Current state of each machine or cell
- Outstanding issues or repairs in progress
- Short-term workarounds
- What still needs verification
Face-to-Face Shift Lead Briefing
If possible, overlap shift leads for 2–3 minutes. A quick rundown of top-line items saves time and prevents confusion, especially on complex or fast-moving lines.
Visual Status Boards
Sometimes teams don’t need more talk, they need more visibility. Use visual boards or dashboards near the line to show:
- What’s running and what’s down
- Key targets and hourly progress
- Current blockers and who’s resolving them
You Don’t Need a New Line to Cut Unplanned Downtime
If you want better performance, don’t wait for a capital project or a new piece of equipment. Start by tightening the first 15 minutes.
Every productive day starts with a strong launch and a clean pass. Downtime loves disorganization, and that starts (or ends) at shift change.
Stop Losing Time Before the Line Even Starts
Lost time isn’t always caused by equipment failure, it often comes from slow startups, poor communication, and inconsistent shift changes. POWERS helps manufacturers take control of these hidden productivity drains.
We work directly with frontline leaders to improve routines, align daily behaviors with performance goals, and build consistency into every shift. Our practical, results-driven approach reduces downtime, improves accountability, and boosts throughput, all without increasing headcount.
To support these efforts, we developed DPS, a digital production system that provides the structure to:
- Standardize startup and handoff processes
- Capture real-time shift data and trends
- Turn insights into action, day after day
Ready to reduce downtime and reclaim lost time across every shift?
Contact POWERS today to see how our team and the DPS platform can help you drive stronger performance, starting with the first 15 minutes of every day.
- Speak to an Expert: Call +1 678-971-4711 to discuss your specific challenges and goals.
- Email Us: Get tailored insights by emailing info@thepowerscompany.com
- Request an Assessment: Use our online contact form, and one of our expert manufacturing consultants will reach out to schedule an in-depth analysis of your operations.