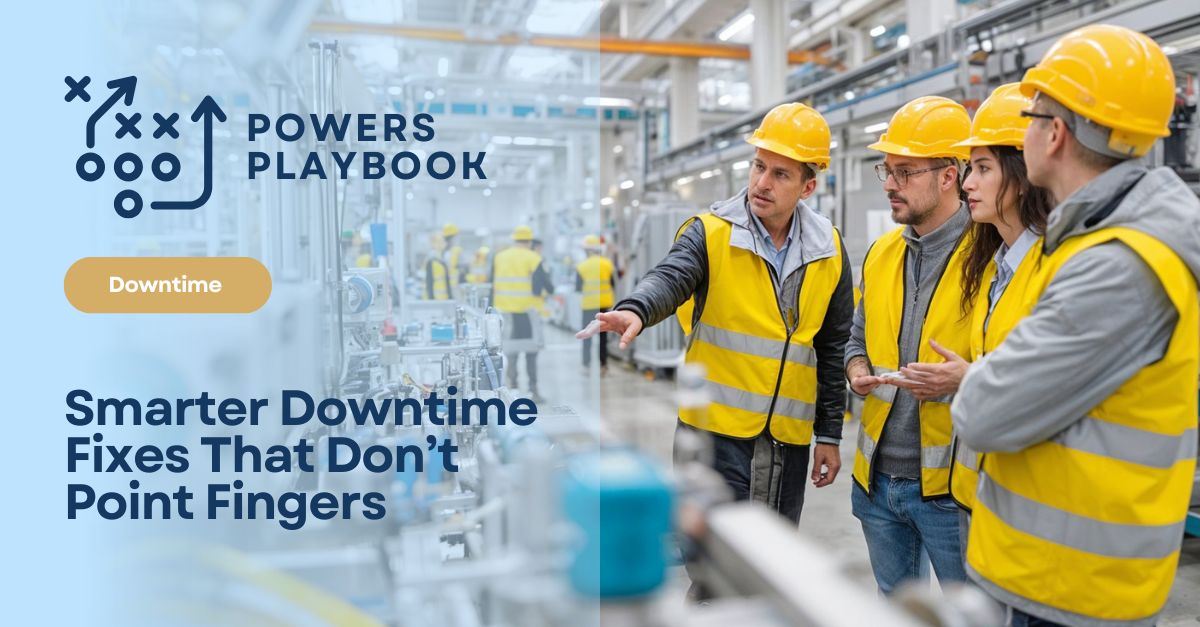
When a line goes down or a machine fails, the first reaction on the floor is usually: “What happened?” But all too often, that quickly turns into: “Who messed up?”
If you’re a frontline leader, you’ve probably felt this pressure firsthand. You’re stuck between hitting production numbers and sorting out a problem with little time, limited information, and a team looking to you for answers.
This playbook is built for you. It’s about using Root Cause Thinking in real-time, without turning it into a finger-pointing session. No spreadsheets, no overcomplicated analysis, just a smarter way to lead.
Root Cause Thinking in Plain Terms
Forget the big meetings and binders. Root Cause Thinking is just a way of saying:
It’s not about blame. It’s about asking better questions, staying curious, and looking at the system around the problem.
This doesn’t mean you need to run a full-blown investigation every time something goes wrong. But you do need to stop and look beyond the obvious.
Top 5 “Blame Game” Moments and What to Ask Instead
Here’s what supervisors run into every day, and how to shift the mindset on the fly:
- “They didn’t follow the procedure.”
👉 Ask: Was the procedure clear, easy to find, and up to date? Did we train it right? - “Maintenance didn’t fix it fast enough.”
👉 Ask: Was the issue reported properly? Did we give them the right details or flag the urgency? - “Operator made a mistake.”
👉 Ask: Was there a check in place to catch it before it caused downtime? Do we rely too much on memory? - “Nobody told me.”
👉 Ask: Where did the communication break down? Do we have a clear way to flag issues before shift change? - “That’s just how it is here.”
👉 Ask: What’s one small thing we can change today to test a better way?
This kind of thinking helps you get to the real issues, without shutting people down.
Simple Tools That Actually Work
You don’t need to be a Six Sigma black belt to put Root Cause Thinking to work. These tools are simple, visual, and meant to be used right on the floor, even during a hectic shift.
Here’s what works in the real world:
- 5 Whys (Start Here)
When something breaks down, ask “Why?” five times. Don’t stop at the first answer, dig until you hit the process issue behind it.
🛠️ Use it during shift huddles or right after a line stoppage. - Fishbone Diagram (Ishikawa)
This tool helps you and your team map out possible causes across categories like materials, machines, methods, and manpower.
🧠 Great when the issue isn’t obvious and you need to see the bigger picture.
➡️ Use our Fishbone Diagram guide - Fault Tree Analysis (FTA)
FTA flips the script, you start with the failure, then map out all the ways it could have happened. It’s perfect when you’re dealing with repeat downtime or safety issues.
🔍 Helps supervisors uncover hidden process weaknesses or logic failures.
➡️ Explore FTA examples - Failure Mode and Effects Analysis (FMEA)
FMEA helps you think ahead. Instead of reacting to a failure, you list out all the ways a process could fail, and then focus on the ones with the biggest impact.
⚙️ Use it before starting a new line, process change, or product launch.
➡️ See how FMEA works - Pareto Analysis (80/20 Rule)
Not all problems are equal. Pareto Analysis helps you focus on the 20% of issues causing 80% of your downtime. It’s a quick way to prioritize.
📊 Use it with your downtime logs or defect data to spot what’s really eating your time.
➡️ Learn how to run a quick Pareto
Every one of these tools is about making your job easier, not harder. Pick one that fits the issue at hand. Use it with your crew. Keep it visual and conversational. You’ll get better answers and less frustration.
Lead the Shift by Example
Root Cause Thinking only works if you set the tone. That means showing your team how to handle problems without panic or blame.
Start by:
- Staying curious: Ask more questions, give fewer lectures.
- Repeating the right message: “Let’s fix the process” goes further than “Let’s find the person.”
- Praising effort, not just outcomes: If someone brings you a process fix, even if it’s not perfect, celebrate it.
- Training your leads: Show them how to guide the team with questions instead of pressure.
How You Know It’s Working
- You stop seeing the same issues over and over.
- Recovery time after downtime gets shorter.
- Your operators start bringing up ideas instead of going silent.
- The mood shifts, from defensive to productive.
Wrap-Up: Start Small, Stay Consistent
You don’t need to overhaul your whole plant to use Root Cause Thinking. Just start with the next breakdown. Ask better questions. Involve the team. Track the tweaks. Praise what works.
POWERS Can Help You Cut Downtime and Keep Production Moving
POWERS specializes in helping manufacturing teams reduce unplanned downtime, solve recurring problems at the root, and keep production on track. Our hands-on approach aligns frontline leaders and workforce behaviors with operational goals, so you get higher efficiency, fewer slowdowns, and lasting gains in performance.
To support that effort, we developed DPS, our next-generation manufacturing operating system. DPS combines lean principles with real-time data and simple tools your team can actually use on the floor. From downtime tracking to root cause analysis, DPS gives frontline leaders the visibility they need to act fast, solve problems early, and drive consistent productivity, without adding headcount or overcomplicating your day.
Want to stop fighting the same fires every shift?
Contact POWERS today to see how our team and DPS platform can help you minimize downtime and unlock smoother, more reliable operations.
- Speak to an Expert: Call +1 678-971-4711 to discuss your specific challenges and goals.
- Email Us: Get tailored insights by emailing info@thepowerscompany.com
- Request an Assessment: Use our online contact form, and one of our expert manufacturing consultants will reach out to schedule an in-depth analysis of your operations.