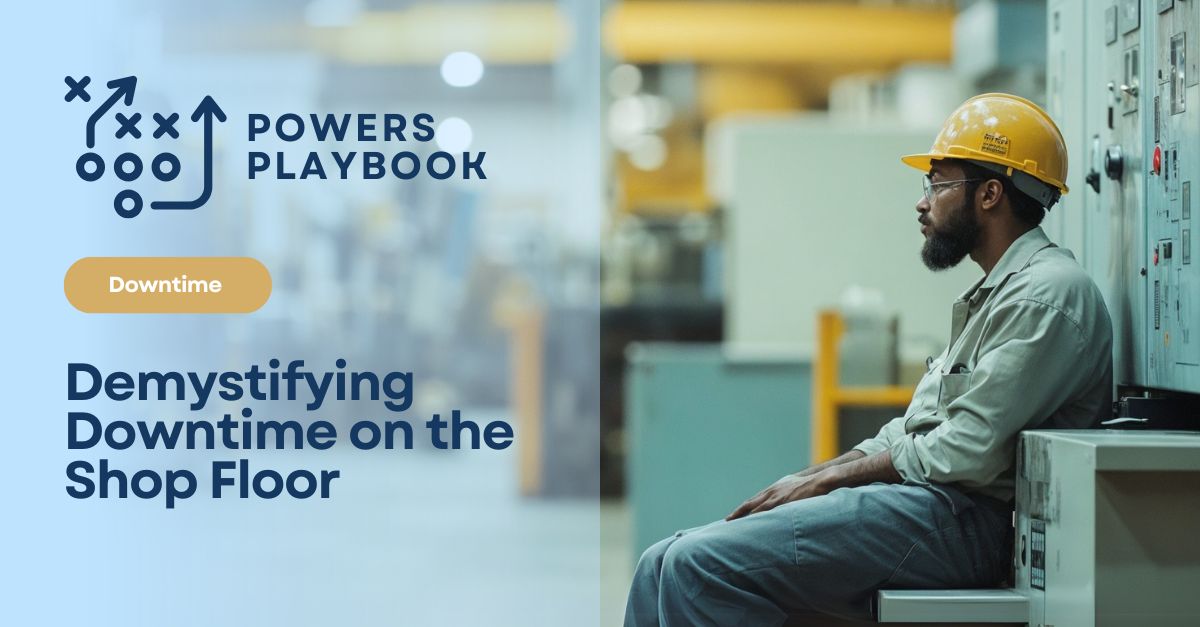
Downtime gets talked about all the time in manufacturing, but ask five people what it means, and you’ll get five different answers. Some think it’s when the machine stops. Others think it’s when the line stops. Some include setups and changeovers. Others only count breakdowns.
This playbook breaks down the four main types of downtime, planned, unplanned, microstops, and idle time, with real-world examples and quick actions you can take to reduce it starting today.
Downtime Is More Than a Stopwatch Problem
Let’s talk numbers.
If a production line is capable of running 1,000 units per hour across 3 shifts, 6 days per week (144 hours total), and those products sell for $1 each, that’s $144,000 per week in potential output.
Now take just 15% of that time away due to various forms of downtime. That’s $21,600 per week in lost output.
Multiply that by 50 weeks, and you’re looking at $1.08 million per year in unrealized revenue, from one line.
And here’s the thing: most of that downtime doesn’t come from big breakdowns. It’s the stuff that flies under the radar, short stops, miscommunication, waiting on the next step. It’s not just a maintenance problem. It’s a visibility problem.
The Four Faces of Downtime
Downtime doesn’t always look like a stopped machine. Sometimes it looks like a full pallet sitting in front of a bottlenecked process. Or an operator walking across the floor to find someone who knows what to do next. Here’s how it breaks down:
1Planned Downtime:
Planned downtime is anything scheduled in advance, like preventive maintenance, cleaning, changeovers, audits, or training.
It’s not the enemy. These activities are necessary. But when they’re poorly timed, take too long, or aren’t communicated clearly, they create unnecessary losses.
Examples:
- Changeover scheduled during peak demand window
- Maintenance doesn’t start on time because equipment wasn’t cleared
- Setup steps vary between teams and shifts
Create a basic, standardized checklist for common changeovers. Post it at the machine. No guesswork, fewer delays.
2Unplanned Downtime
Unplanned downtime includes anything that stops production without warning. This is usually where the most obvious pain shows up.
Examples:
- Machine breakdown
- Missing materials or wrong parts
- Operator call-outs or labor shortages
- Power outages or safety lockouts
Unplanned events are frustrating, but often, they’re not as “random” as they seem. Recurring breakdowns, repeat supply delays, and last-minute staffing issues point to patterns that can be fixed.
Start tracking downtime events with reason codes. Doesn’t have to be digital, just use a clipboard or whiteboard. Over time, patterns emerge.
3Microstops (The Silent Killers)
Microstops are short, frequent interruptions, usually under five minutes. Because they’re brief and things get moving again quickly, they’re rarely tracked. But they add up fast.
Examples:
- Box misaligned in feeder
- Tape head jammed
- Sensor tripped
- Operator pause to make a quick tweak
The machine might only stop for 2–3 minutes, but if that happens 15 times a day, you’re losing hours every week without realizing it.
Ask each operator to write down every stop, no matter how short, during one shift. Review the list with your team. You'll uncover low-hanging fruit that’s been hiding in plain sight.
4Idle Time (The Hidden Waste)
Idle time is when employees are ready to work, but can’t, because something else isn’t ready.
Machines might still be running, but no value is being added. Idle time is a major contributor to lost productivity, especially when no one’s tracking it.
Examples:
- Waiting for materials, tools, or instructions
- Standing by while a downstream process catches up
- Delayed response from quality or maintenance
- Confusion over who’s supposed to handle a task
Do a walk-through and look for signs of waiting, people pacing, leaning, standing at a machine with nothing to do. Ask what they’re waiting on. You’ll likely hear the same issues come up again and again.
What Supervisors Should Watch For
You don’t need software or a time study to start identifying downtime. Just watch and listen.
Here are signs that something’s off:
- Operators standing still or “looking busy” but not actually producing
- Frequent requests for the same fix or help on the same equipment
- Changeovers taking 30 minutes on one shift and 90 on another
- Breaks or lunch throwing the whole line off schedule
- Too many calls on the radio asking the same questions every day
If you see these patterns, you’ve got downtime hiding in plain sight.
Don’t Let Downtime Become Normal
Not all downtime is bad. Some of it is necessary. But too often, teams start accepting it as “just the way it is.”
That’s when you lose control of your performance.
Start simple:
- Pick one type of downtime to focus on this week, microstops, changeovers, idle time.
- Track it by shift for a few days.
- Bring it to your team and ask: What’s causing this? What can we do differently?
Even a small change, like a clearer checklist, a better supply handoff, or a 5-minute post-shift huddle, can make a big difference.
Cut Downtime. Boost Throughput. No Guesswork.
Downtime is costly, but the right tools and approach can change that fast. POWERS works side by side with manufacturing teams to identify where time is being lost and how to fix it for good.
Our DPS platform equips frontline leaders with real-time insights, clear metrics, and practical tools to reduce downtime, eliminate inefficiencies, and drive sustainable output gains.
Want to take control of your downtime?
Contact POWERS to learn how our team and DPS platform can help you keep production moving and performance rising.
- Speak to an Expert: Call +1 678-971-4711 to discuss your specific challenges and goals.
- Email Us: Get tailored insights by emailing info@thepowerscompany.com
- Request an Assessment: Use our online contact form, and one of our expert manufacturing consultants will reach out to schedule an in-depth analysis of your operations.