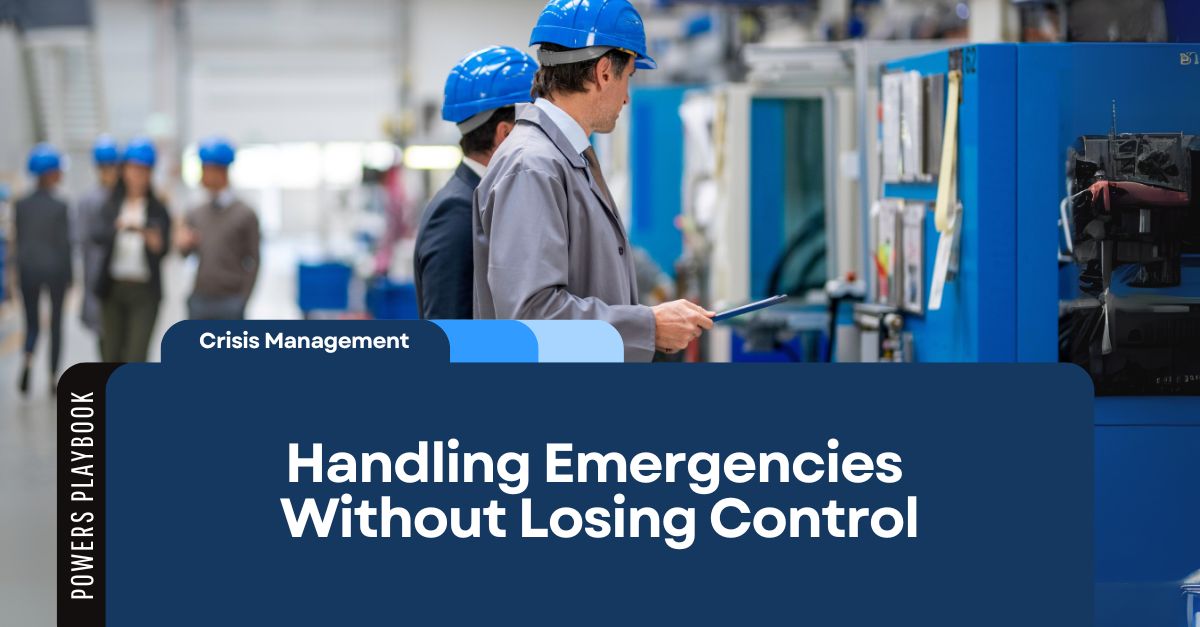
Emergencies Happen. What You Do Next Matters.
The factory floor doesn’t run on best-case scenarios. Machines break down. Employees get injured. A key shipment doesn’t arrived. When things go sideways, a frontline leader’s reaction sets the tone for how quickly and well the situation gets resolved.
Too often, frontline leaders react instead of taking control, and that’s when a small crisis or problem turns into full-blown disaster. The good news? You don’t need a 50-page emergency response plan to lead effectively under pressure. You just need a simple, repeatable process that keeps you in command when things go wrong.
This playbook gives you a three-step action plan for handling emergencies without losing control.
Step 1Assess and Stabilize the Situation
When something goes wrong, the first instinct is often to jump in and fix it. But acting too fast—without understanding the full picture—can make things worse.
Take a breath. Look at what’s happening.
- Is it a safety issue? A machine failure? A personnel problem?
- Does production need to stop, or can operations continue while the issue is addressed?
- Who’s affected, and what’s the immediate risk?
Lock down the problem before it spreads.
- If it’s a safety hazard, secure the area.
- If it’s an equipment failure, follow your plant’s shutdown protocols.
- If it’s a personnel issue, remove distractions and handle it privately.
Use a quick-response checklist.
- When stress is high, it’s easy to miss key steps. A simple checklist for different emergency types (equipment, safety, personnel) helps keep things organized.
Quick Win
Keep a printed crisis response checklist in the breakroom or at each workstation.
Step 2Execute the Right Response
Once you’ve stabilized the situation, it’s time to act. The key is to be decisive—but not impulsive.
Follow the escalation plan.
- Who needs to know? Maintenance? HR? Safety team? Plant manager?
- Who can actually fix the problem—and who just needs to be informed?
- Avoid unnecessary panic. Deliver clear, fact-based updates to your team.
Assign roles—don’t try to do it all yourself.
- Have someone document the issue.
- Send a team member to fetch tools, first aid, or a key contact.
- Keep one person monitoring the situation while others take action.
Stick to the plan—unless you absolutely have to pivot.
- Standard Operating Procedures (SOPs) exist for a reason. Use them.
- If no SOP exists, get input before making a big call.
- Keep communication clear, simple, and direct.
Quick Win
Post a predefined escalation path at key locations so everyone knows who to contact in an emergency.
Step 3Learn and Prevent the Next Crisis
The best leaders don’t just fix today’s problem—they make sure it doesn’t happen again.
Do a quick debrief.
- What caused the issue?
- Did the response go smoothly, or were there delays?
- What should be done differently next time?
Make training part of the routine.
- Walk the team through crisis scenarios so they know what to do.
- Make sure new hires are familiar with emergency protocols.
- Keep SOPs updated based on real-world situations.
Build confidence under pressure.
- The more prepared your team is, the calmer they’ll be when something goes wrong.
- No one should be “guessing” what to do in an emergency.
Quick Win
Hold "5-minute crisis huddles" at shift change to review past incidents and reinforce response strategies.
Lead with Control—Not Chaos
Emergencies aren’t avoidable. But panic and confusion are. A frontline leader’s job isn’t just to put out fires—it’s to lead through the storm. By using this simple Assess → Act → Learn framework, you’ll keep situations from spiraling out of control, build confidence in your team, and ensure a faster, more effective response every time.How POWERS Can Help You Take Control in a Crisis
When emergencies hit the factory floor, delays and miscommunication make bad situations worse. At POWERS, we help frontline leaders take control with clear processes, real-time visibility, and better decision-making tools.
DPS, the Digital Production System built by POWERS, gives frontline leaders the structure they need to respond effectively, reducing downtime, confusion, and costly mistakes. With the DPS Scorecard, Built-in Direct Messaging, and Company Knowledge Hub, we help teams:
- Standardize emergency response procedures so the right people get involved fast.
- Improve communication flow between shifts, maintenance, and leadership.
- Train teams for high-pressure decision-making so they stay calm and in control.
DPS isn’t just another off-the-shelf system—it’s a customized, hands-on approach to improving factory efficiency, productivity, and workforce confidence.
Be Ready Before the Next Crisis Hits
Every moment of hesitation in an emergency costs time, money, and trust. The good news? You can put a system in place before the next issue slows production.
Let’s build a crisis response process that works—backed by data, driven by people, and tailored to your plant’s real challenges.
- Speak to an Expert: Call +1 678-971-4711 to discuss your specific challenges and goals.
- Email Us: Get tailored insights by emailing info@thepowerscompany.com
- Request an Assessment: Use our online contact form, and one of our expert manufacturing consultants will reach out to schedule an in-depth analysis of your operations.