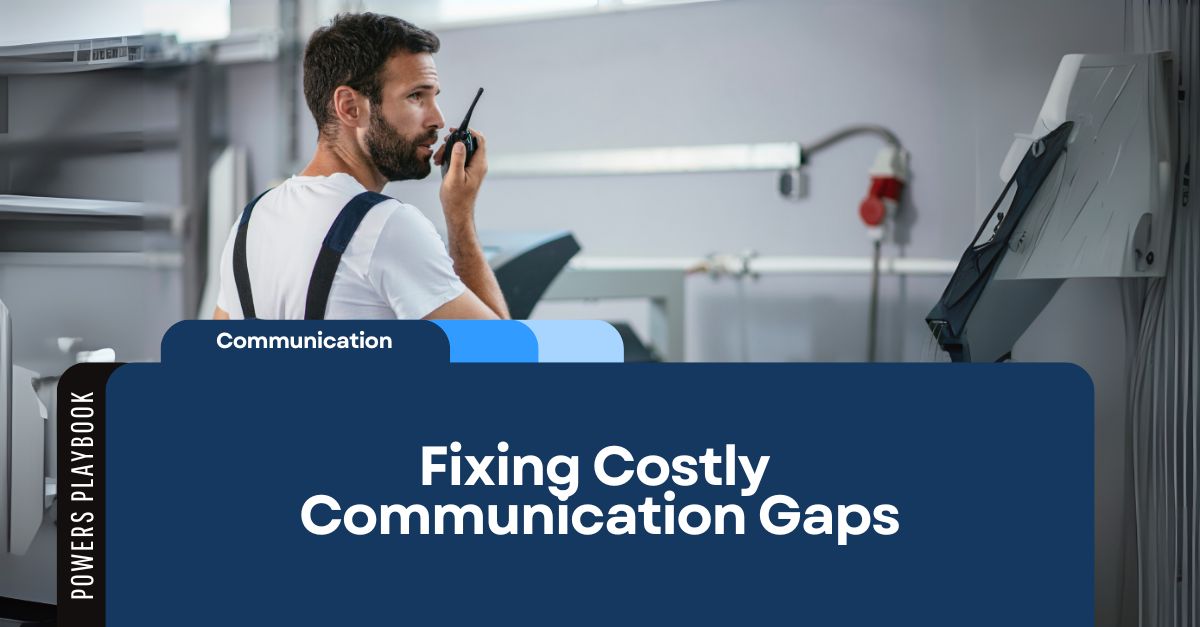
Why Communication Breakdowns Are Costing You More Than You Think
Ask any factory supervisor what slows them down the most, and you’ll hear the same frustrations:
- “Nobody told me we ran out of material, so now we’re stuck waiting for replenishment.”
- “Operators keep running this part the wrong way because they weren’t updated on the change.”
- “I only found out about the machine issue when it was already too late to fix it before the next order.”
These are all communication breakdowns, and they’re happening in factories every single day.
But here’s the thing: communication gaps aren’t always obvious. They don’t show up on a balance sheet, and they aren’t easy to measure. Instead, they appear in the form of missed deadlines, production delays, unplanned downtime, quality issues, and safety concerns—all of which cost manufacturers real money.
Most facilities think they have some form of communication system in place—daily meetings, emails, reports, or shift change notes. But if those systems aren’t clear, consistent, and connected, then information is still falling through the cracks. And when it does, small problems snowball into major production losses.
This article is designed to help you identify where these gaps exist, understand the real impact they have, and take action to close them for good.
Where Communication Breaks Down on the Shop Floor
Communication issues don’t come from people not wanting to share information—they come from not having a system in place that makes sharing information easy and effective.
Here are the most common areas where communication falls apart in manufacturing:
1Shift Change Chaos
- Outgoing operators don’t properly document machine performance or issues.
- Incoming teams start their shift without a clear picture of what’s changed overnight.
- Issues that happened in the previous shift don’t get relayed, so the same mistakes continue.
- Unexpected material shortages or setup errors delay production.
- Critical safety warnings don’t get passed along, leading to potential hazards.
2Disconnect Between Leadership and the Shop Floor
- Management makes changes to production schedules without informing the frontline.
- Operators receive orders without knowing why priorities have shifted.
- Supervisors get blamed for poor performance when they weren’t given the full picture.
- Leadership assumes things are running smoothly because they aren’t getting real-time feedback from the floor.
3Silos Between Departments
- Production, quality, and maintenance teams aren’t working in sync.
- One team fixes an issue, but it creates a new bottleneck elsewhere.
- Scheduling changes don’t get communicated, leading to wasted labor hours.
- Inventory teams don’t get updates on demand shifts, causing stockouts or overages.
4Poor Coordination Between Maintenance and Production
- Operators don’t report small issues until they turn into major breakdowns.
- Maintenance is scheduled at the worst possible time, disrupting production.
- Repeated equipment failures occur because maintenance doesn’t get full details on past issues.
- Maintenance fixes a problem without realizing it causes inefficiencies elsewhere.
5Data That Doesn’t Reach the Right People
- Operators track important production details on paper logs that never get read.
- KPI reports are generated, but teams aren’t given clear action steps based on the data.
- Different departments work with different sets of information, leading to misalignment.
- Key updates are shared through email, but nobody actually sees them in time.
How These Gaps Hurt Production
When communication is unreliable, the entire operation suffers. Here’s what happens when these gaps go unchecked:1Scrap & Rework Skyrocket
- Operators run jobs with outdated instructions.
- Quality standards aren’t communicated, leading to out-of-spec parts.
- Machines aren’t set up correctly because the last shift didn’t update settings properly.
2Unplanned Downtime Increases
- Equipment issues go unreported until they become critical failures.
- Maintenance and production aren’t aligned, so repairs happen during peak production hours.
- Poor shift handoffs mean the next team doesn’t know about an ongoing breakdown.
3Production Targets Are Missed
- Work orders change, but nobody tells the operators.
- Material shortages aren’t reported in time, leading to stalled production lines.
- Machine settings are changed without everyone knowing, leading to delays and defects.
4Low Workforce Engagement
- Employees feel disconnected from leadership and left out of important decisions.
- Lack of transparency breeds frustration, leading to higher turnover.
- Workers stop reporting issues because they assume nobody will act on them.
What You Can Do to Bridge These Gaps
Fixing communication isn’t about adding more meetings or paperwork—it’s about creating simple, repeatable processes that make sure the right information gets to the right people at the right time.
Here’s how you can start fixing these gaps today:
1Standardize Shift Change Communication
- Implement a structured handoff process so key details don’t get lost.
- Require outgoing teams to log machine performance and material usage.
- Use digital logs instead of paper notes that get misplaced.
2Get Leadership More Involved on the Floor
- Have supervisors and managers conduct daily Gemba walks to hear operator feedback in real time.
- Open two-way communication channels between frontline teams and leadership.
- Make KPI tracking visible and actionable, not just another report in an inbox.
3Improve Coordination Between Departments
- Set up weekly cross-functional meetings so production, maintenance, and quality teams are aligned.
- Use a shared digital dashboard to keep everyone on the same page.
- Assign a point person for inter-department communication to prevent misalignment.
4Align Maintenance with Production Schedules
- Use predictive maintenance tracking to prevent equipment failures before they happen.
- Establish a real-time issue escalation system to flag equipment concerns early.
- Make sure maintenance schedules are planned around production priorities.
How POWERS Can Help
Communication breakdowns cost manufacturers time, money, and productivity every day. At POWERS, we take a data-driven, people-first approach to solving these challenges.
DPS, the Digital Production System built by POWERS, helps uncover hidden inefficiencies, helps uncover hidden inefficiencies, with the DPS Scorecard and Built-in Direct Messaging —whether it’s shift handovers, maintenance coordination, or leadership alignment.
We work directly with frontline supervisors, operators, and leadership to:
✔ Standardize communication processes so key details don’t get lost.
✔ Train teams to share information effectively, reducing downtime and rework.
✔ Eliminate bottlenecks caused by misalignment and poor data flow.
Take Control of Communication Breakdowns Before They Cost You More
Every day that communication gaps go unchecked, your plant is losing efficiency. The good news? You can fix it.
With the DPS Scorecard, Built-in Direct Messaging, and Company Knowledge Hub, we’ll help you build a reliable, repeatable system that keeps operations running smoothly.
- Speak to an Expert: Call +1 678-971-4711 to discuss your specific challenges and goals.
- Email Us: Get tailored insights by emailing info@thepowerscompany.com
- Request an Assessment: Use our online contact form, and one of our expert manufacturing consultants will reach out to schedule an in-depth analysis of your operations.