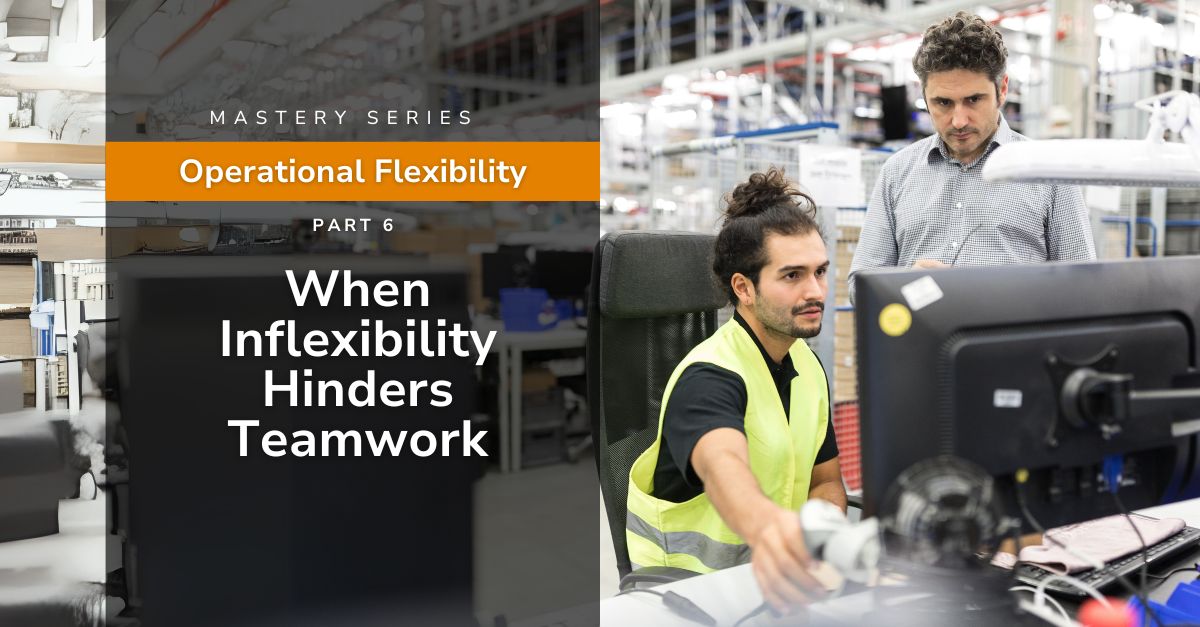
Inflexible operations create significant challenges that often go unnoticed until they become substantial barriers to productivity and efficiency.
One of the most insidious consequences is the development of siloed departments and poor collaboration, which can quietly erode operational performance across the organization.
For example, consider a manufacturing facility where maintenance and production teams operate independently, each focusing solely on their immediate responsibilities. Maintenance might track equipment performance metrics while production monitors output, but critical patterns are missed without shared communication channels or integrated systems. A recurring equipment failure might be viewed by maintenance as a repair task, while production sees it as a scheduling issue, leading to delays, increased costs, and preventable downtime. This disconnect affects immediate operations and makes it nearly impossible to proactively address the root causes of inefficiency.
These misalignments are not isolated occurrences—they are direct outcomes of rigid operational frameworks that lack mechanisms for fostering collaboration and shared accountability. Inflexibility in operations limits the ability to adapt, share insights, and leverage cross-departmental expertise, allowing inefficiencies to persist. As siloed departments become entrenched, organizations face compounding challenges such as repeated troubleshooting of identical problems, misallocated resources, and missed opportunities for innovation.
Addressing these issues requires more than simple process improvements; it demands a cultural shift toward operational flexibility and collaborative problem-solving. The sections that follow will explore the ten most critical ways inflexible operations foster silos and poor collaboration, as well as actionable strategies to overcome them.
1Repeated Troubleshooting of Identical Issues Across Departments:
When departments work in isolation, they often unknowingly face and solve identical problems, duplicating efforts without realizing solutions already exist. For example, purchasing, production, and logistics teams may address a recurring issue with a supplier’s delivery schedule separately. Each department troubleshoots without benefiting from shared knowledge, wasting valuable resources and time.
Mitigation: Establish a centralized knowledge repository where all departments can log solutions and best practices. This database, paired with regular cross-departmental review sessions, ensures that once a problem is solved, the solution is available to everyone. Additionally, promoting collaboration through shared platforms like Slack or Teams can reduce the likelihood of redundant troubleshooting.
2Overlapping Procurement Efforts Leading to Waste:
Departments operating independently often purchase similar materials or services without coordination, leading to overstocking, inflated costs, and wasted resources. For example, one team may negotiate a discount for bulk purchases while another order the same items at a higher price.
Mitigation: A unified procurement system ensures visibility and coordination across teams. Implementing an enterprise resource planning (ERP), system can track procurement activities in real time, allowing departments to consolidate orders. Regular procurement audits can also highlight areas of overlap, leading to cost-saving opportunities.
3Prolonged Resolution Times for Quality Issues:
When quality issues arise, poor collaboration between departments can delay resolution. For instance, a defect identified on the shop floor may not be promptly communicated to design or production teams, prolonging the time it takes to address the root cause. This not only affects product quality but also erodes customer trust.
Mitigation: Cross-functional quality control teams, composed of representatives from key departments, can streamline the resolution process. Investing in real-time communication tools and automated alerts ensures that everyone involved is immediately notified of quality issues. Weekly or biweekly quality review meetings can also help prevent recurring problems.
4Fragmented Access to Real-Time Operational Data:
Siloed operations often result in fragmented data systems, where departments only have access to partial information. For example, production may lack visibility into inventory levels, leading to overproduction or stockouts. This lack of transparency hinders decision-making and timely responses.
Mitigation: Integrate data systems into a single, centralized platform that provides all stakeholders with a real-time operational dashboard. Digital transformation tools like manufacturing execution systems (MES) and IoT sensors can further enhance data visibility. Regular training on interpreting and utilizing these systems ensures that teams can make informed decisions quickly.
5Missed Insights from Unshared Customer Complaints or Returns Data:
Customer feedback is a goldmine for process and product improvement, but its potential is lost when it is trapped within the customer service or sales department. For example, recurring complaints about a product defect might never reach the engineering or production teams responsible for addressing the issue.
Mitigation: Implement a customer feedback loop that ensures all relevant teams can access complaints, returns, and suggestions. Use software solutions to categorize and distribute feedback to the appropriate departments automatically. Regular interdepartmental meetings to review customer feedback can drive meaningful improvements and prevent recurring issues.
6Poor Utilization of Employee Skills in Collaborative Roles:
In siloed organizations, employee skills are often underutilized due to limited cross-departmental visibility. For instance, an employee with expertise in lean manufacturing principles might be restricted to their department, missing opportunities to contribute to broader organizational improvements.
Mitigation: Conduct a skills inventory and encourage cross-training initiatives to make employees’ capabilities more visible across the organization. Assign employees to cross-functional projects where their expertise can be leveraged and foster a culture of collaboration by incentivizing team-based accomplishments.
7Overloaded Communication Channels with Irrelevant Updates:
Attempts to improve communication across departments can sometimes lead to information overload, where irrelevant updates flood employees’ inboxes. For example, a shop floor supervisor might receive emails about sales projections that have little bearing on daily operations, leading to overlooked important messages.
Mitigation: Establish communication protocols that define the type and frequency of updates each department receives. Segment communication channels by relevance, using platforms like Slack with dedicated channels for specific topics. This approach ensures employees only receive information pertinent to their roles.
8Difficulty in Forecasting Due to Fragmented Data Inputs:
Forecasting accuracy depends on comprehensive data from all departments. When departments operate in silos, incomplete data sets lead to errors in demand planning, resulting in overproduction, stockouts, or missed sales opportunities.
Mitigation: Standardize data collection practices across departments to ensure consistency and accuracy. Integrated forecasting tools from shared data sources can provide a more holistic view. Regular interdepartmental forecasting reviews help align efforts and improve accuracy.
9Inconsistent Application of Lean Principles Across Departments:
While one department may excel in implementing lean principles, others may lag, leading to conflicting practices and inefficiencies. For example, one team may optimize workflow for minimal waste while another unknowingly creates bottlenecks that negate those improvements.
Mitigation: Provide company-wide training on lean principles to ensure consistent application. Establish a centralized lean management team to oversee initiatives and share successful departmental strategies. Regular workshops and interdepartmental process reviews can foster alignment and continuous improvement.
10Missed Cost-Saving Opportunities from Shared Operational Insights:
Departments often develop innovative ways to save costs or improve efficiency, but these insights remain isolated without collaboration. For example, a maintenance team might discover a way to extend equipment life, but this knowledge might not reach production teams that could benefit.
Mitigation: Create cross-functional task forces to identify and implement cost-saving initiatives. Monthly innovation forums where departments present their ideas can encourage sharing and organization-wide adoption of best practices. Recognize and reward teams for collaborative success to reinforce the importance of sharing insights.
The Bottom Line For Operations Leaders
Siloed departments and poor collaboration are not merely operational inconveniences—they are productivity bottlenecks caused by inflexible operations. Left unaddressed, they can lead to inefficiencies, miscommunications, and lost opportunities across your organization. Manufacturers can reclaim valuable time and resources, reduce costs, and improve overall efficiency by adopting flexible, integrated systems and fostering a culture of cross-departmental collaboration.
How POWERS Can Help
At POWERS, we don’t just identify the issues—we help you solve them. We specialize in empowering manufacturers to overcome operational inflexibility, eliminate silos, and improve collaboration through customized strategies and innovative tools.
With the DPS (Digital Production System), we bring real-time data and insights to every level of your operations, enabling you to achieve sustainable productivity and profitability.
Here’s how POWERS and DPS can elevate your manufacturing operations:
- Unified Operational Insights: Gain real-time visibility into production metrics, enabling quick identification and resolution of inefficiencies.
- Streamlined Communication: Break down departmental silos with tools that ensure seamless data sharing and collaboration across teams.
- Proactive Problem Solving: Use AI-driven analytics to predict potential bottlenecks and optimize resource allocation before issues arise.
- Integrated Workforce Solutions: Improve the utilization of employee skills through cross-functional training and optimized workflows.
- Continuous Improvement: Leverage intuitive dashboards and data-driven insights to support Lean initiatives and enhance process efficiency.
With decades of experience and cutting-edge technology like DPS, POWERS provides manufacturers with the expertise and tools to build adaptable, collaborative operations. The result? Reduced downtime, maximized resource efficiency, and a stronger foundation for long-term success.
Ready to Take the Next Step?
Let POWERS help you transform inflexible operations into a competitive advantage. Contact us today to learn how we can empower your team and drive measurable results.
- Speak to an Expert: Call +1 678-971-4711 to discuss your specific challenges and goals.
- Email Us: Get tailored insights by emailing info@thepowerscompany.com
- Request an Assessment: Use our online contact form, and one of our expert manufacturing consultants will reach out to schedule an in-depth analysis of your operations.
Continue Reading from this Mastery Series
- Part 1 – How Stubborn Systems Sabotage Competitive Advantage
- Part 2 – Unadaptable Workflows Lead to Talent Turnover
- Part 3 – Why Inflexible Operations Fail to Innovate
- Part 4 – How Operational Inflexibility Undermines Your Resilience
- Part 5 – When Rigid Operations Cause Decision-Making Bottlenecks
- Part 6 – How Inflexibility Obstructs Collaboration
- Part 7 – How Inflexible Operations Sabotages Scaling Initiatives
- Part 8 – How Inflexible Operations Fuel Resistance to Change
- Part 9 – How Inflexible Operations Leave You Vulnerable to Cyber Threats
- Part 10 – Why Operational Inflexibility Undermines Your Brand Reputation