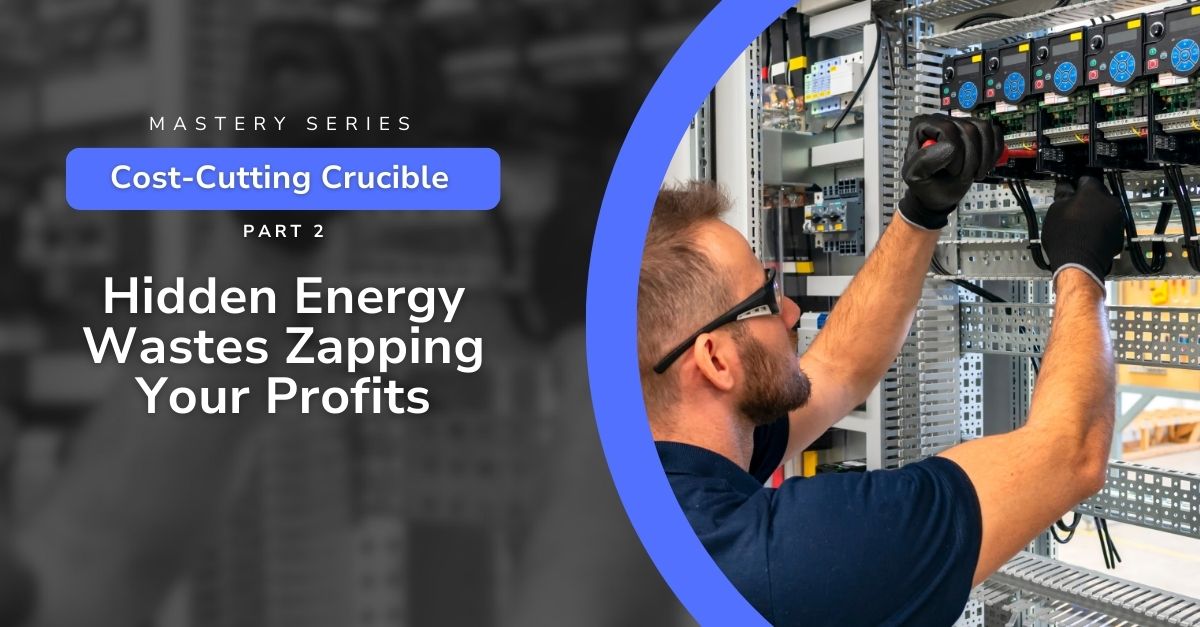
Profit leaks in manufacturing often hide in plain sight, and nowhere is this more evident than in energy inefficiency.
What appears to be minor power overuse or overlooked equipment settings can, in reality, become a significant drain on profitability.
The secondary symptoms compound this issue, surfacing in ways managers may not immediately connect to energy inefficiency but undeniably erode the bottom line.
One less common example is how unoptimized equipment efficiency can lead to inconsistent product quality. When machinery operates inefficiently, it creates subtle variations in temperature, pressure, or speed, affecting production precision. For a facility that manufactures temperature-sensitive adhesives, for instance, inefficient heat control could result in batches that fail to meet specifications. These quality inconsistencies drive costs through increased waste, product rework, and potential customer dissatisfaction. Even if energy costs are budgeted, the downstream consequences—additional labor, resource consumption, and disrupted production schedules—represent overlooked expenses that silently chip away at profitability.
Understanding these unseen drains on profit requires a holistic approach. It’s not just about saving on energy bills but recognizing how inefficiencies create a domino effect of hidden costs that ripple through the entire operation. From inflated maintenance budgets to reduced asset lifespan, each inefficiency has a measurable impact that demands attention. In this post, we explore ten ways that high energy wastage manifests on the shop floor, along with practical strategies to mitigate these issues and uncover hidden savings.
1Overuse of Auxiliary Equipment That Drains Power Unnecessarily:
Auxiliary equipment like air compressors, chillers, and fans often run continuously, regardless of production needs. This excessive use can draw significant power, leading to inflated energy bills. Auxiliary systems are frequently left unchecked, draining resources even when minimal energy is required. Managers on the shop floor may find it difficult to optimize auxiliary equipment because energy demand varies widely between shifts and operational tasks.
Solution: Implement smart sensors and automatic power control systems that activate auxiliary equipment only when necessary. Energy management platforms can be set up to monitor auxiliary loads and adjust power consumption in real-time. Training staff to recognize and minimize energy drain during non-peak hours can also lead to significant cost savings.
2Unoptimized Conveyor Systems Leading to Energy Waste:
Conveyor systems are vital to the flow of materials but can be major energy wasters if not properly optimized. Running conveyors at maximum speed during slow production periods or when only partially loaded leads to inefficient energy use and faster component wear. Unoptimized conveyor systems also increase the risk of unexpected breakdowns, causing production delays and quality issues.
Solution: Introduce variable frequency drives (VFDs) that adjust conveyor speed based on real-time production needs. Linking VFDs to a centralized monitoring system allows energy consumption to be dynamically optimized. In addition, regularly auditing conveyor settings and updating maintenance protocols ensures systems run as efficiently as possible.
3Suboptimal Use of Power Factor Correction Equipment:
A poor power factor can result in high reactive power consumption, which utilities often penalize, significantly increasing energy costs. Suboptimal use of power factor correction equipment limits the capacity of electrical distribution systems and causes voltage drops, disrupting other sensitive machinery. Many facilities lack regular monitoring systems to maintain an optimal power factor, leading to inefficiencies that managers may overlook until costs have ballooned.
Solution: Install automated power factor correction equipment and conduct regular audits to monitor and adjust reactive power levels. Strategically placed high-quality capacitor banks can stabilize electrical loads. Using energy consultants to optimize power factor strategies ensures facilities operate efficiently, reducing energy use and operational disruptions.
4Overheating of Machines from Neglected Lubrication Practices:
Inadequate lubrication causes friction, making machines overheat and consume more energy. This inefficiency can also increase the risk of equipment failure, resulting in costly downtime. Overheating due to poor lubrication not only drives up energy consumption but also decreases the precision of machinery, impacting product quality and the overall reliability of production lines.
Solution: Develop a robust lubrication management plan that includes regular checks and advanced lubrication monitoring systems. Smart sensors can track temperature and friction levels, alerting maintenance teams to potential issues. Investing in high-quality lubricants that minimize friction can reduce energy usage, extend equipment life, and improve production efficiency.
5Failure to Seal Energy Leaks from Worn-Out Equipment Components:
Worn-out seals, loose fittings, and air leaks are frequent culprits of energy loss. For instance, a single air leak in a compressed air system can cost thousands of dollars annually in wasted energy. Leaks in heating, cooling, or fluid transfer systems compound this problem, often going undetected and eroding profitability over time. The sporadic nature of such leaks makes them difficult to diagnose without specialized equipment.
Solution: Invest in ultrasonic leak detection tools and conduct quarterly energy audits to identify and seal leaks. Once detected, promptly replace worn seals with high-quality, energy-efficient alternatives. Preventative maintenance schedules should include regular inspections to catch potential leaks before they become costly problems.
6Using Oversized Pumps and Motors Unnecessarily:
Pumps and motors are often oversized to accommodate worst-case scenarios, but this conservative approach leads to inefficiencies. Oversized equipment consumes excessive energy and operates inefficiently under normal loads, increasing the risk of frequent cycling and reduced equipment life. This issue is particularly challenging in facilities that lack up-to-date load analysis data to make more informed decisions.
Solution: Conduct an energy audit to evaluate the sizing of pumps and motors. Consider retrofitting existing equipment with variable speed drives (VSDs) that optimize energy use based on actual demand. An energy audit can highlight opportunities to replace oversized systems with right-sized, high-efficiency models, generating energy and cost savings.
7Delay in Adopting Energy-Efficient Technologies:
Many manufacturers hesitate to upgrade aging equipment due to budget constraints or concerns about production disruption. However, this delay in adopting energy-efficient technologies increases energy costs and puts facilities at a competitive disadvantage. Older equipment uses more energy and requires more frequent maintenance, compounding operational inefficiencies.
Solution: Develop a capital improvement plan prioritizing energy-efficient upgrades, focusing on areas with the highest return on investment. Take advantage of government incentives and utility rebates to offset upfront costs. Phased implementation strategies, where critical equipment is upgraded first, minimize disruption and ensure a smooth transition to energy-efficient operations.
8Poor Training on Energy Conservation Best Practices:
Employees often lack training on how their daily activities impact energy consumption. For example, workers may leave lights, machinery, or auxiliary systems running even when not used simply because energy-saving practices haven’t been emphasized. This lack of awareness results in systemic inefficiencies, making energy conservation a missed cost-saving opportunity.
Solution: Launch an energy conservation awareness campaign with interactive workshops and visual reminders on the shop floor. Encourage employees to take ownership of energy-saving initiatives and reward those identifying new efficiency opportunities. Regularly updating training programs ensures all staff stay informed about energy conservation best practices
9Inadequate Insulation Maintenance Causing Excessive Heating or Cooling Loss:
Proper insulation is crucial for maintaining energy efficiency, yet it is often overlooked in regular maintenance. Degraded or poorly installed insulation can lead to heat loss in winter and cooling loss in summer, causing HVAC systems to work overtime. The fluctuating temperatures can also create an uncomfortable working environment, lowering employee productivity and impacting equipment reliability.
Solution: Conduct an annual thermal audit using infrared cameras to identify heat or cooling loss areas. Re-insulate critical areas using high-performance materials like spray foam, mineral wool, or reflective insulation. Ensuring adequately insulated pipes, tanks, and HVAC ductwork can reduce energy waste and stabilize facility temperatures.
10Mismanagement of Energy Recovery Systems:
Energy recovery systems, such as heat exchangers and waste heat recovery units, are investments meant to reduce energy use. However, poor integration, lack of maintenance, and insufficient training on leveraging these systems can lead to underperformance. When energy recovery is mismanaged, facilities fail to capitalize on opportunities to reuse energy, missing out on significant cost savings.
Solution: Integrate energy recovery systems into a facility’s overall energy management plan and use monitoring tools to track performance. Schedule regular maintenance checks to ensure all components are working as intended. Training employees on the purpose and function of energy recovery systems can improve usage and maximize efficiency, contributing to a greener and more cost-effective operation.
Conclusions for Operations Leaders
High energy wastage due to poor equipment efficiency represents a silent but significant drain on manufacturing profitability. From inflated utility bills to the downstream consequences of quality inconsistencies, these inefficiencies can impact your operations. Addressing energy waste is not just about reducing costs; it’s about transforming your processes for sustained productivity and long-term gains.
Our approach extends beyond traditional consulting. Our advanced Digital Production System (DPS) provides AI-driven insights and real-time data that empower your team to optimize energy use and improve overall efficiency.
Here’s how POWERS and DPS can elevate your manufacturing operations:
- Precision Maintenance Scheduling: Use predictive analytics to minimize energy wastage by ensuring equipment operates at peak efficiency, reducing unexpected breakdowns.
- Intelligent Resource Allocation: Optimize production schedules and energy use based on AI-driven forecasts to maximize output and minimize waste.
- Seamless Communication: Facilitate cross-departmental collaboration to address energy inefficiencies collectively, using integrated platforms that share data and insights instantly.
- Continuous Improvement Initiatives: Leverage DPS for ongoing energy audits and efficiency projects, fostering a culture of data-driven optimization.
Ready to elevate your manufacturing operations with real-time data and AI-driven insights? POWERS and our DPS platform are here to help you reduce hidden costs and unlock new levels of productivity and profitability. Connect with us today to transform your energy management strategies into a competitive advantage.
- Speak to an Expert: Call +1 678-971-4711 to discuss your specific challenges and goals.
- Email Us: Get tailored insights by emailing info@thepowerscompany.com
- Request an Assessment: Use our online contact form, and one of our expert manufacturing consultants will reach out to schedule an in-depth analysis of your operations.
Continue Reading from this Mastery Series
- Part 1 – How Poor Scheduling Burns Through Your Profit Margins
- Part 2 – How Hidden Energy Wastes Burn Through Your Bottom Line
- Part 3 – How Dead Weight in Your Safety Stock Undermines Your Bottom Line
- Part 4 – The Hidden Costs of Ignoring Preventive Maintenance Programs
- Part 5 – Mismatched Skills and Wasted Workforce Potential
- Part 6 – Poor Quality Control is Dragging Down Your Productivity and Profits
- Part 7 – Being Slow to Market Undermines Your Bottom Line
- Part 8 – Supplier Missteps That Drain Profitability
- Part 9 – The Cost of Continuing to Use Manual Processes
- Part 10 – The Financial Fallout of Fragmented Compliance