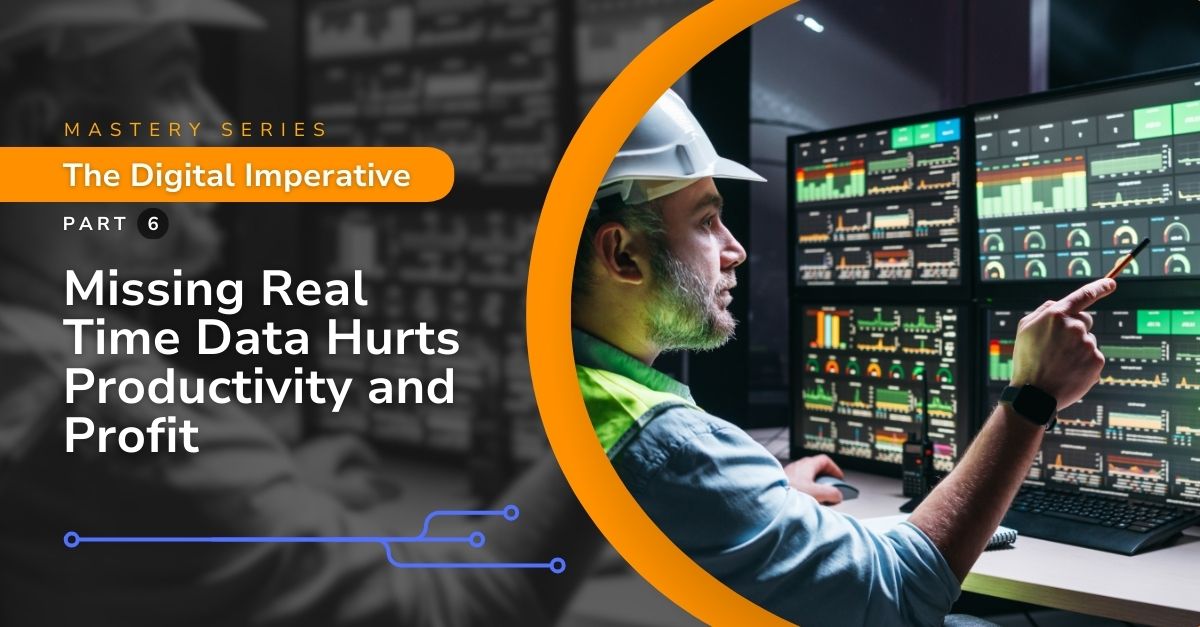
Manufacturers that fail to fully embrace Industry 4.0 often struggle to keep pace with evolving demands, especially when leveraging real-time data for process optimization.
The shift to digital transformation is more than just upgrading equipment or software; it’s about fully integrating smart technology into everyday operations to enhance decision-making, efficiency, and productivity.
One less common yet impactful example is the inability to adjust real-time production line configurations based on actual data. Without real-time performance analytics, manufacturers often rely on outdated or estimated figures to make decisions. This results in suboptimal machine configurations and inefficient material flow, particularly in fast-paced, high-variability production environments.
For example, a facility producing custom automotive parts might struggle to adjust its production line to accommodate sudden shifts in order quantities or material availability. This leads to prolonged bottlenecks, wasted materials, and increased downtime—all preventable if real-time data were leveraged to make immediate adjustments to machine settings or reallocate resources efficiently.
Neglecting digital transformation limits a manufacturer’s ability to respond swiftly to operational changes and creates blind spots in identifying potential inefficiencies before they grow into larger issues. The lack of real-time data inhibits the optimization of key processes, resulting in missed opportunities to improve productivity, reduce waste, lower costs, and stay competitive in a market increasingly driven by smart, data-driven operations.
1Inconsistent Machine Performance Monitoring:
When real-time data collection is absent, machine performance is often evaluated using outdated methods, leading to inconsistent monitoring. Managers may only identify performance issues during scheduled checks, missing critical inefficiencies that arise in between. This inconsistency leads to equipment underperformance going unnoticed for extended periods, reducing productivity across the board.
Mitigation: Implementing an Industrial Internet of Things (IIoT) system allows real-time tracking of machine performance data. IIoT sensors provide continuous feedback on key parameters such as temperature, vibration, and throughput, enabling managers to detect performance dips immediately. With real-time alerts, issues are identified and resolved faster, ensuring equipment operates at peak efficiency and minimizing downtime.
2Delayed Identification of Process Inefficiencies:
Without access to real-time data, identifying process inefficiencies becomes a reactive, rather than proactive, exercise. Shop floor managers may rely on periodic performance reports, which provide historical data rather than live insights. This delay in identifying bottlenecks and inefficiencies allows productivity drains to continue longer than necessary.
Mitigation: Real-time data analytics systems pinpoint inefficiencies as they happen, allowing immediate corrective action. For example, machine learning algorithms can analyze production flow in real-time and highlight deviations from optimal performance. This early detection ensures faster resolution of inefficiencies and keeps production lines running smoothly.
3Limited Insights into Production Line Bottlenecks:
Bottlenecks in production lines significantly hamper throughput and increase lead times. When real-time data is unavailable, managers must rely on anecdotal evidence or wait for full-scale breakdowns to understand where issues occur. This reactive approach can result in prolonged bottlenecks, causing delays and reduced overall output.
Mitigation: Utilizing real-time process visualization tools, such as digital twin technology, enables managers to identify bottlenecks as they occur. These tools simulate and monitor the entire production line, offering real-time insights into where flow is slowing down and why. Managers can quickly adjust workflows, optimize resource allocation, and balance production loads to eliminate bottlenecks before they escalate.
4Inability to Optimize Equipment Usage in Real-Time:
Without real-time data, equipment utilization often falls short of its potential. For example, machines might be underutilized due to insufficient coordination between production schedules and actual machine availability. The inability to adjust equipment usage in real-time means opportunities to optimize production throughput are missed.
Mitigation: Implementing real-time production scheduling systems enables more dynamic resource allocation. These systems automatically adjust equipment assignments based on machine status and production needs. Real-time adjustments ensure equipment is utilized to its fullest potential, maximizing throughput and minimizing idle times.
5Inaccurate Forecasting of Maintenance Needs:
Without real-time data, maintenance schedules are often based on fixed intervals or reactive repairs after breakdowns occur. This approach leads to under-maintenance, where minor issues are ignored until they cause significant damage, and over-maintenance, where equipment is serviced unnecessarily. Both scenarios result in productivity losses.
Mitigation: Predictive maintenance systems leverage real-time data to forecast when machines require maintenance. Predictive models can accurately determine when maintenance is needed, reducing unplanned downtime and avoiding unnecessary servicing by analyzing trends in machine performance data, such as vibrations, temperatures, or pressures.
6Poor Response Times to Machine Failures:
When machine failures occur, the lack of real-time monitoring delays the response. Often, managers are only aware of a failure when it’s too late to prevent significant downtime. Manual checks and delayed notifications extend the time it takes to diagnose and fix the problem, compounding productivity losses.
Mitigation: By integrating real-time machine monitoring systems with automated failure alerts, managers can receive immediate notifications when a machine malfunctions. These systems provide detailed diagnostics, allowing maintenance teams to quickly identify the issue and take corrective action, minimizing downtime and its impact on productivity.
7Limited Understanding of Real-Time Workforce Productivity:
Without real-time data, measuring workforce productivity is often based on output volume at the end of a shift or workday, missing opportunities to make in-shift adjustments. This lack of insight can result in imbalanced workloads, inefficient task prioritization, and unproductive time slipping through the cracks.
Mitigation: Workforce management systems that track real-time performance metrics, such as task completion rates and idle times, provide managers with the insights needed to optimize labor allocation on the fly. This immediate feedback allows for dynamic task reassignment, better alignment of team capacity with production needs, and more accurate performance evaluations.
8Inaccurate Analysis of Production Cycle Times:
Accurate cycle times are critical for evaluating the efficiency of production processes. However, when managers rely on post-process data collection or estimates, cycle time analysis is prone to inaccuracies. This can lead to false assumptions about productivity levels, further entrenching inefficiencies.
Mitigation: With real-time cycle time monitoring systems, every aspect of the production process is continuously recorded, providing accurate and up-to-the-minute data. Managers can track the time taken for each production cycle and identify outliers that may indicate inefficiencies, enabling more precise process improvements.
9Delayed Implementation of Corrective Actions:
In traditional setups, corrective actions are often delayed due to the time it takes to gather data, analyze it, and decide on a course of action. During this delay, production continues to suffer from the same issues that could have been resolved earlier, further reducing overall productivity.
Mitigation: Real-time data collection and analysis platforms enable managers to implement corrective actions immediately. These systems can automatically flag when a process deviates from its set parameters and suggest corrective measures, allowing managers to make informed decisions immediately, thus minimizing the negative impact on production.
10Inconsistent Tracking of Production Waste:
Inefficient processes that generate excess waste are hard to identify without real-time data. Manual tracking of production waste often fails to capture the full picture, leading to continued resource wastage that could otherwise be minimized. This waste contributes to higher production costs and lower profitability.
Mitigation: Real-time waste tracking systems provide continuous data on scrap rates, rejected parts, and material usage. By giving managers immediate insight into waste trends, these systems enable quick adjustments to reduce material loss and improve overall production efficiency, leading to significant cost savings and enhanced productivity.
Conclusions for Operations Leaders
Manufacturers operating without fully embracing Industry 4.0 technologies are falling behind in an increasingly competitive landscape. The inability to leverage real-time data for process optimization creates significant blind spots, leading to inefficiencies, wasted resources, and lost productivity. Neglecting digital transformation means missing valuable insights that could improve machine performance, streamline operations, and enhance decision-making.
Our Digital Production System (DPS) is designed to bridge the gap, empowering your operations with the real-time data and AI-driven insights needed to thrive. DPS is more than just a tool; it’s a complete approach to improving productivity and optimizing your entire value chain.
Here’s how POWERS DPS can elevate your operations:
- Complete Visibility: Monitor every aspect of your production in real time, quickly identifying inefficiencies and opportunities for optimization.
- Seamless Collaboration: Share data instantly across teams, fostering collaboration and driving continuous improvement throughout your organization.
- AI-Driven Insights: Leverage advanced AI technology to predict challenges, streamline scheduling, and make smarter decisions at every stage of production.
- Maximized Resource Allocation: Optimize equipment usage and workforce deployment, minimizing downtime and boosting productivity.
POWERS doesn’t just provide consulting services; we offer the tools and expertise to ensure your manufacturing operations are positioned for long-term success in the digital era. Ready to elevate your operations and embrace real-time data for lasting improvements? Contact POWERS today and discover how our DPS can help you stay ahead of the curve.
- Speak to an Expert: Call +1 678-971-4711 to discuss your specific challenges and goals.
- Email Us: Get tailored insights by emailing info@thepowerscompany.com
- Request an Assessment: Use our online contact form, and one of our expert manufacturing consultants will reach out to schedule an in-depth analysis of your operations.
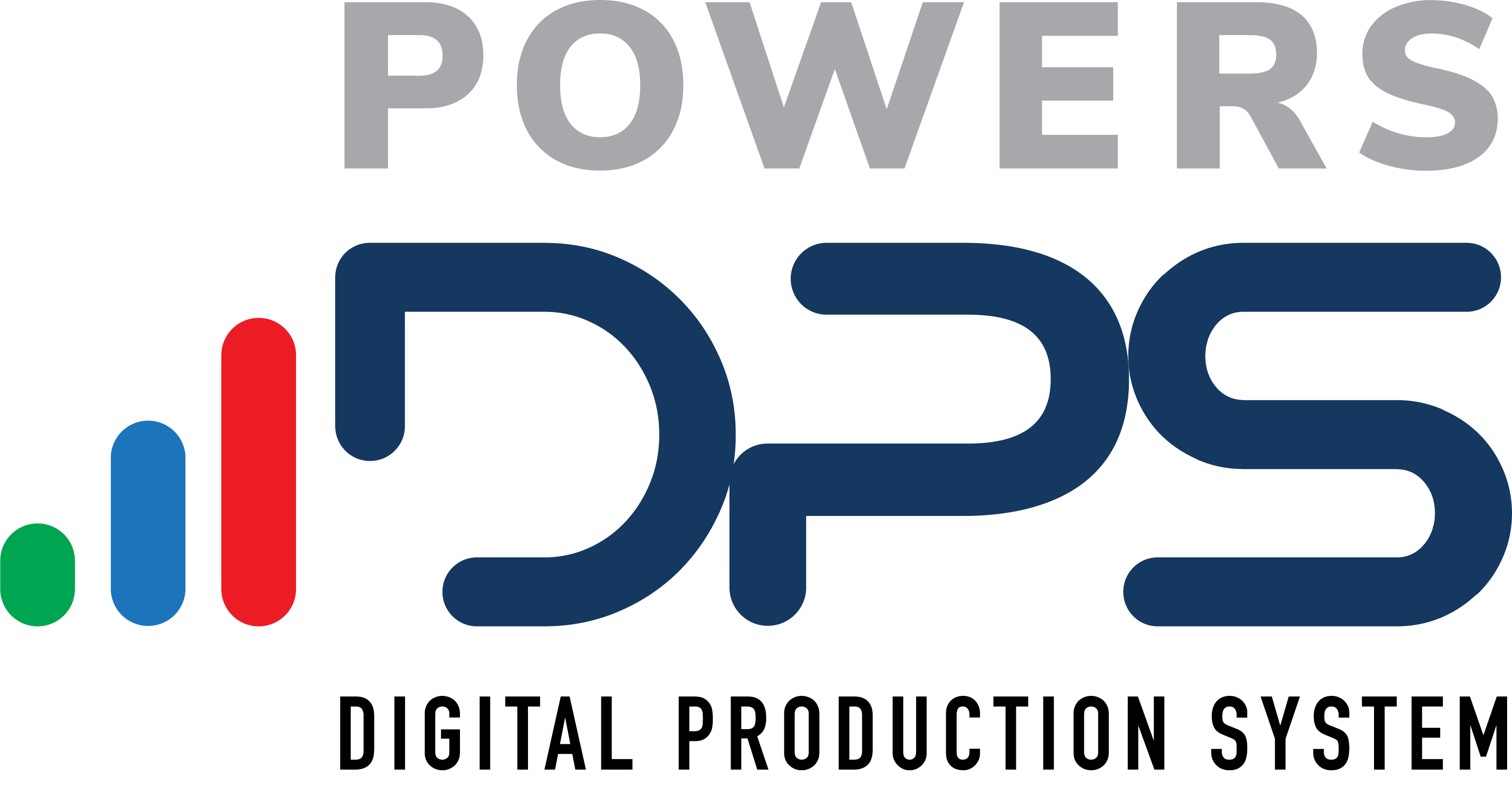
Start transforming your operations today with POWERS DPS. Contact us for a free consultation and see how digital transformation can revolutionize your manufacturing future. Learn More about DPS
Continue Reading from this Mastery Series
- Part 1 – Outdated Tech is Weakening Your Talent Pipeline
- Part 2 – How Legacy Systems Sabotage Your Cybersecurity and Productivity
- Part 3 – How Ignoring Digital Tools Leaves You Vulnerable to Downtime
- Part 4 – When Digital Stagnation Leads to Poor Communication and Production Chaos
- Part 5 – The Real Cost of Trying to Keep Up in the Market Without Digital Transformation
- Part 6 – Missing Out on Real-Time Data Drains Productivity and Profit
- Part 7 – How Failing To Go Digital Jeopardizes Regulatory Compliance
- Part 8 – How Outdated Inventory Practices Sabotage Your Operations
- Part 9 – Limited Customization Options are Driving Your Customers Away
- Part 10 – The Productivity Trap of Failing to Scale Digital Initiatives