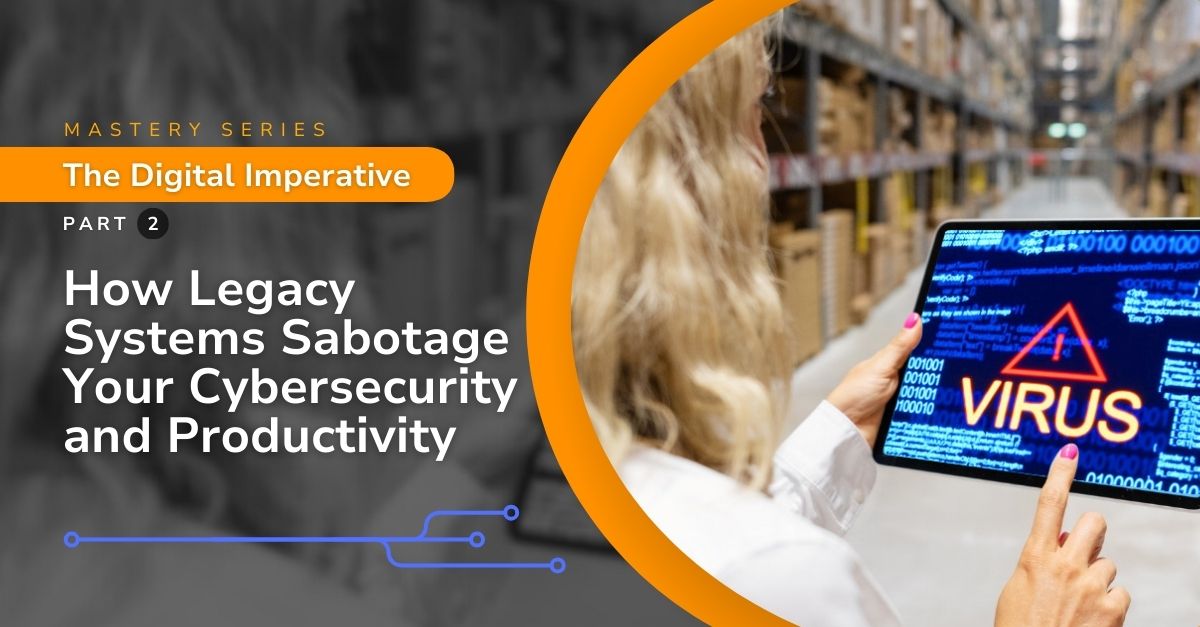
Neglecting digital transformation goes beyond missed opportunities for efficiency; it opens the door to significant cybersecurity risks, particularly in the case of legacy systems that are not equipped to handle modern threats.
Many manufacturers rely heavily on outdated systems designed long before today’s cyberattack strategies evolved. While functional, these legacy systems lack the necessary defense mechanisms to protect against increasingly sophisticated attacks, exposing the entire production ecosystem.
One less commonly discussed outcome of this oversight is the potential for disruptions in automated maintenance systems. For instance, some manufacturing plants use legacy systems to manage automated workflows, such as predictive maintenance for equipment.
When these systems are compromised due to a cybersecurity breach, they may fail to issue critical alerts about equipment malfunctions, leading to unplanned downtime, safety hazards, or even production halts. This increased risk of breaches doesn’t just affect IT systems—it threatens the entire manufacturing operation, from supply chains to product quality. For instance, in 2023, Clorox faced a devastating ransomware attack that forced the company to halt operations, impacting its supply chain and costing millions in lost revenue.
Neglecting digital transformation leaves manufacturers vulnerable to cyberattacks and the cascading disruptions these attacks cause in production. The result is a cycle where legacy systems increase risk and undermine the operational efficiency that digital transformation could bring. To maintain competitiveness, protect sensitive data, and ensure consistent productivity, manufacturers must upgrade their cybersecurity practices, starting with modernizing their systems.
1Over-reliance on Outdated Firewalls:
Outdated firewalls in legacy systems often lack the sophisticated threat detection capabilities required to defend against modern cyber threats. These firewalls, while once robust, fail to account for evolving malware and hacking techniques, leaving manufacturing systems exposed to breaches that could cripple operations. Managers relying on these outdated defenses may see a spike in unauthorized access attempts, compromising their production lines’ integrity.
Mitigation: Replacing outdated firewalls with next-generation firewalls (NGFWs), including advanced threat detection and real-time analytics, can provide a substantial defense upgrade. NGFWs can integrate seamlessly with modern systems and employ AI-driven insights to detect anomalies, ensuring a proactive rather than reactive approach to cybersecurity.
2Misinterpretation of Cybersecurity Protocols Due to Outdated Training:
Legacy systems are often paired with outdated cybersecurity training programs, leading to an ill-prepared workforce to combat modern threats. Employees may misinterpret the seriousness of phishing attacks, fail to recognize malware indicators, or simply follow antiquated protocols that no longer apply to today’s cyber landscape.
Mitigation: Regularly updating cybersecurity training to reflect the latest cyber defense strategies is key. Companies can ensure that their workforce is well-versed in identifying potential threats by focusing on real-world simulations. Implementing ongoing education for employees, especially those working directly with legacy systems, can reduce misinterpretation and increase vigilance against cyberattacks.
3Difficulty Integrating Newer Cybersecurity Tools with Legacy Systems:
Many manufacturers face the daunting challenge of integrating advanced cybersecurity tools with legacy systems, leading to incomplete or ineffective protection. These older systems often lack the APIs or protocols necessary to communicate with modern security solutions, resulting in gaps in coverage and creating weak points for attackers to exploit.
Mitigation: Implementing middleware or upgrading to hybrid systems that bridge the gap between legacy and modern systems can improve integration. Such platforms allow newer cybersecurity tools to operate effectively within older frameworks, ensuring that companies can gradually modernize without leaving their systems vulnerable during the transition.
4Difficulty Identifying Which Legacy Systems Are Most at Risk of Attack:
Manufacturers often struggle to identify which legacy systems pose the greatest risk due to a lack of centralized monitoring and the fragmented nature of older networks. Without clear visibility, managers may be unaware of vulnerabilities until it’s too late, exposing critical production systems.
Mitigation: Employing advanced risk management and vulnerability scanning tools can give manufacturers a clearer picture of their system’s weakest points. Combined with regular audits, these tools allow companies to prioritize security efforts and allocate resources where they are most needed, minimizing the chances of a catastrophic breach.
5Inability to Patch Vulnerabilities in Legacy Software Quickly:
Legacy systems often depend on outdated software, which is rarely patched or updated to fix newly discovered vulnerabilities. The slow pace at which patches are applied exposes systems for extended periods, providing attackers ample opportunity to exploit known flaws.
Mitigation: Establishing an automated patch management system that regularly updates legacy software can reduce the time systems remain exposed. Creating a dedicated cybersecurity team to handle patches and updates can help manufacturers avoid potential threats before they escalate into full-blown breaches.
6Outdated Encryption Methods Leading to Easier Data Breaches:
Older systems use outdated encryption methods that no longer meet modern security standards, making it easier for cybercriminals to intercept and decode sensitive information. This is especially concerning in industries where proprietary data or trade secrets are at risk.
Mitigation: Upgrading encryption protocols to comply with current standards (e.g., AES-256) is critical for securing data against modern decryption techniques. Integrating end-to-end encryption for data in transit and at rest further safeguards information, preventing unauthorized access and ensuring that data breaches do not result in significant operational disruptions.
7Misalignment Between IT and Operational Teams on Cybersecurity Priorities:
The gap between IT and operational teams often leads to misaligned cybersecurity priorities. IT departments may prioritize system security, while operations focus on productivity, leading to conflicts over resource allocation and a slower response to potential threats in legacy systems.
Mitigation: Fostering better communication and collaboration between IT and operations teams is essential. Establishing cross-functional cybersecurity committees that include representatives from both departments ensures that security measures are aligned with operational needs, allowing for faster and more cohesive responses to cyber threats.
8Inaccurate Risk Assessments Due to Outdated Risk Management Frameworks:
Legacy systems often operate under outdated risk management frameworks, leading to inaccurate assessments of cybersecurity threats. These frameworks fail to account for the complexity and speed of modern cyberattacks, resulting in underestimations of potential risks and a lack of preparedness.
Mitigation: Transitioning to modern, dynamic risk management frameworks incorporating real-time data and analytics can significantly improve the accuracy of risk assessments. These frameworks allow for continuous monitoring and adjustments, ensuring manufacturers can better anticipate and respond to cyber threats before disrupting production.
9Poor Incident Response Time During Security Breaches:
The fragmented nature of legacy systems can lead to delays in incident response during a security breach. Without a centralized platform to detect and respond to breaches, companies may experience significant downtime, impacting productivity and potentially compromising sensitive data.
Mitigation: Implementing a unified incident response platform that consolidates alerts from all systems—including legacy ones—can drastically reduce response times. These platforms allow teams to quickly identify the source of a breach, contain it, and minimize damage, ensuring that production can resume as quickly as possible.
10Difficulty Managing Security Updates Across Multiple Legacy Systems:
Legacy systems often require manual updates, which can be time-consuming and prone to human error. This difficulty in managing updates across various systems leaves networks exposed to cyber threats, as critical patches are missed or delayed.
Mitigation: Utilizing automated update management tools that can deploy patches across multiple systems simultaneously reduces the burden on IT teams and minimizes the risk of human error. Such tools ensure that all systems remain updated with the latest security measures, providing a more robust defense against cyberattacks.
Conclusions for Operations Leaders
Manufacturers that neglect digital transformation are putting their systems at risk of cybersecurity breaches and compromising their ability to maintain productivity in an increasingly competitive market.
Legacy systems, while functional, lack the resilience to withstand modern cyber threats, leaving companies vulnerable to costly disruptions and downtime.
Addressing these cybersecurity challenges is more than just about protecting data—it’s about safeguarding your entire production process from inefficiencies that can arise from these vulnerabilities.
At POWERS, we offer more than just advice; we partner with you to implement the tools and strategies necessary for a successful digital transformation. With decades of experience in manufacturing productivity and cutting-edge AI-driven technologies, we help you navigate the complexities of modernizing your operations.
Through our Digital Production System (DPS), we provide manufacturers an entire digital production management framework, with real-time visibility, collaborative tools, and data-driven decision-making capabilities that lead to sustainable improvements in both security and productivity.
Here’s what POWERS can do for you:
- Complete Visibility: Gain real-time insights into production processes, allowing you to monitor, identify, and address inefficiencies before they impact your operations.
- Enhanced Collaboration: Empower your teams with seamless data-sharing capabilities that facilitate better decision-making and continuous improvement across departments.
- Data-Driven Decision Making: Leverage AI-driven insights to predict challenges, optimize scheduling, and make informed decisions that improve efficiency.
- Boosted Productivity and Efficiency: Minimize unplanned downtime, streamline resource allocation, and enable your workforce to operate at its full potential.
Ready to elevate your manufacturing operations? With POWERS by your side, you can enhance your cybersecurity posture, embrace Industry 4.0, and unlock your company’s full productivity potential.
- Speak to an Expert: Call +1 678-971-4711 to discuss your specific challenges and goals.
- Email Us: Get tailored insights by emailing info@thepowerscompany.com
- Request an Assessment: Use our online contact form, and one of our expert manufacturing consultants will reach out to schedule an in-depth analysis of your operations.
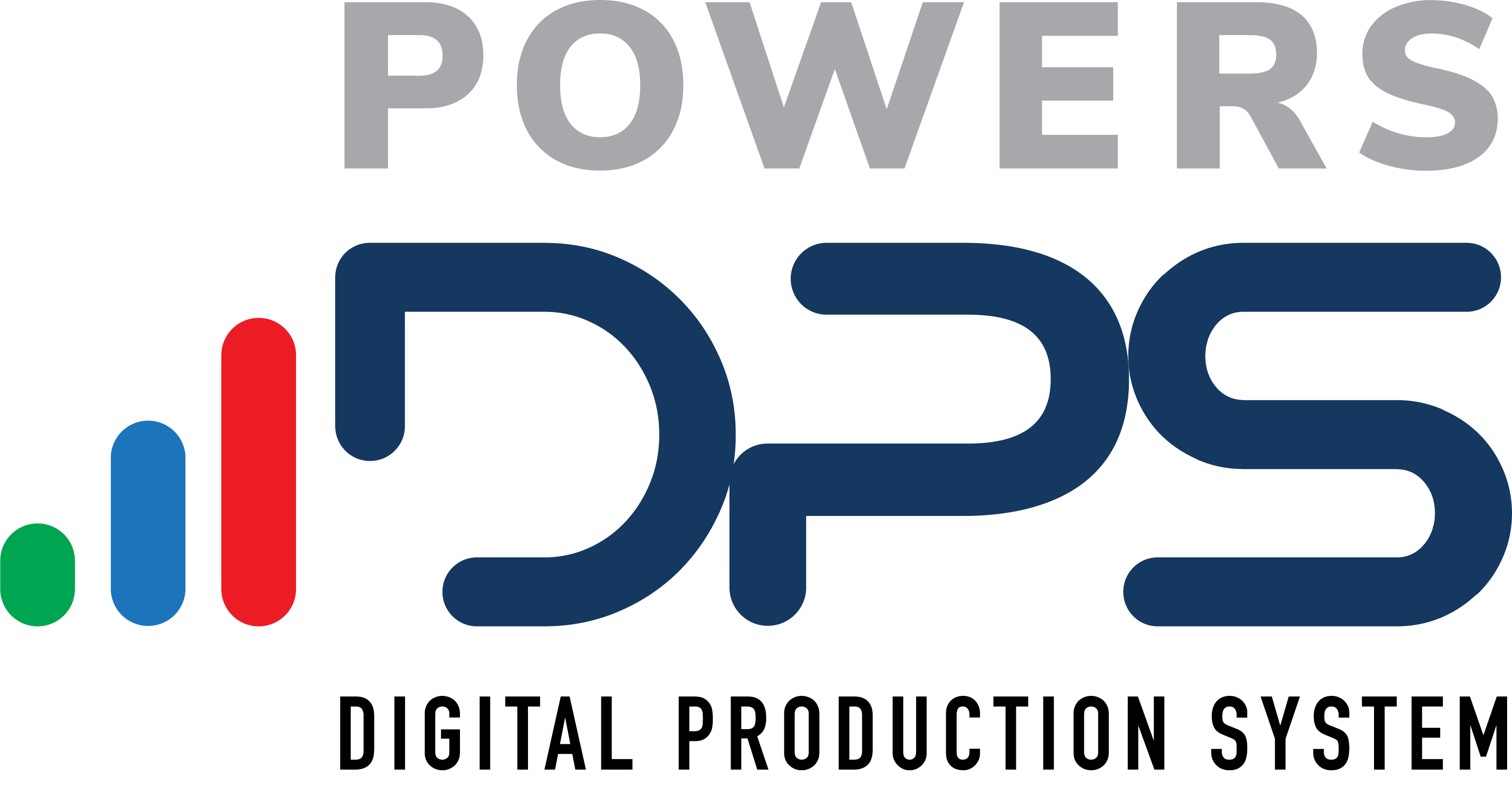
Start transforming your operations today with POWERS DPS. Contact us for a free consultation and see how digital transformation can revolutionize your manufacturing future. Learn More about DPS
Continue Reading from this Mastery Series
- Part 1 – Outdated Tech is Weakening Your Talent Pipeline
- Part 2 – How Legacy Systems Sabotage Your Cybersecurity and Productivity
- Part 3 – How Ignoring Digital Tools Leaves You Vulnerable to Downtime
- Part 4 – When Digital Stagnation Leads to Poor Communication and Production Chaos
- Part 5 – The Real Cost of Trying to Keep Up in the Market Without Digital Transformation
- Part 6 – Missing Out on Real-Time Data Drains Productivity and Profit
- Part 7 – How Failing To Go Digital Jeopardizes Regulatory Compliance
- Part 8 – How Outdated Inventory Practices Sabotage Your Operations
- Part 9 – Limited Customization Options are Driving Your Customers Away
- Part 10 – The Productivity Trap of Failing to Scale Digital Initiatives