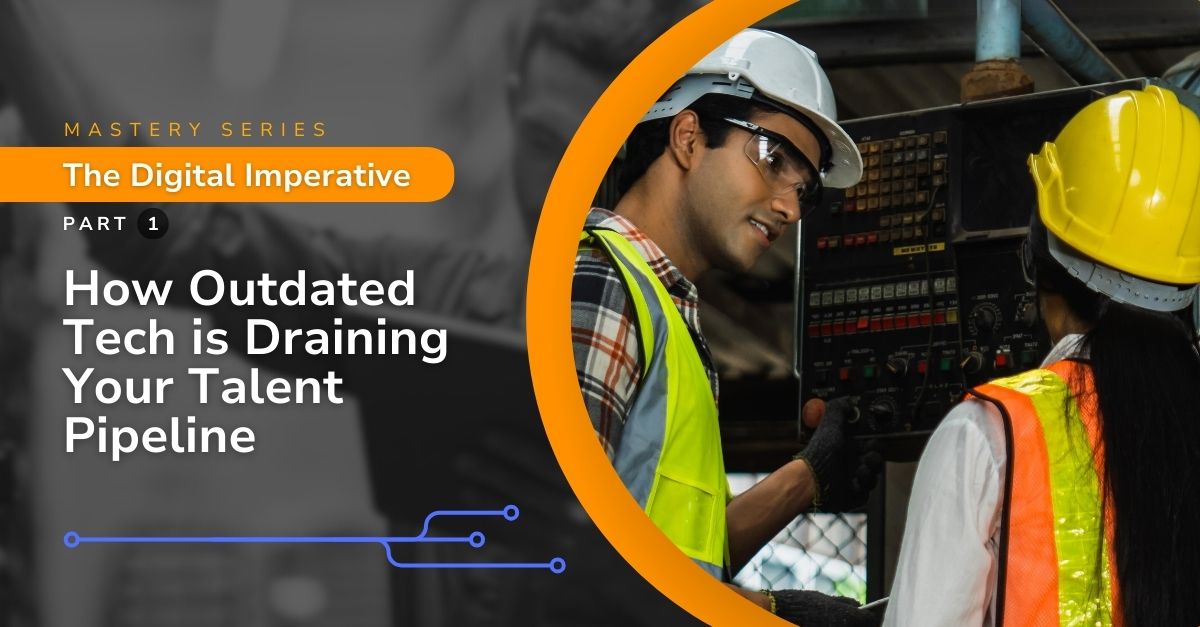
Neglecting digital transformation leads to interconnected challenges that often exceed the immediate scope of production inefficiencies.
One of the most pressing issues stemming from this is the inability to attract and retain younger workers, particularly those from Generation Z and Millennials, who expect technology to be an integral part of their work environment.
These generations grew up with rapidly evolving technology and are accustomed to smart devices, automation, and data-driven solutions in their personal and educational experiences.
A key consequence of neglecting digital transformation is that younger workers are often turned off by outdated processes and systems, making manufacturing less appealing as a career option. The absence of cutting-edge tools like real-time analytics, automation, and IoT-enabled machinery frustrates younger employees. It diminishes their perception of long-term growth and innovation within the company. Manufacturing environments that are slow to implement these technologies send an unintended message that they are not focused on the future, which can lead to higher turnover rates and difficulty in recruiting fresh talent.
One less commonly discussed example of this is the impact on knowledge transfer. When younger workers encounter legacy systems that are difficult to use or incompatible with modern technology, they struggle to integrate new insights or improvements into existing processes. This disconnect creates a barrier to cross-generational knowledge transfer, as younger workers are less likely to engage with or fully understand the older systems and senior employees may not be equipped to train them effectively.
As a result, not only is productivity affected, but valuable institutional knowledge also risks being lost as older workers retire, leaving behind poorly documented processes that are not easily digitized. The reluctance to adopt digital solutions makes it harder for the incoming workforce to bring innovation to the shop floor, contributing to a stagnant operational environment where employee retention and productivity suffer.
In a competitive labor market, manufacturers that fail to embrace Industry 4.0 find themselves at a disadvantage, unable to offer the modern, tech-driven workspaces that younger generations expect. Addressing these secondary symptoms is critical not only to improve day-to-day operations but also to secure the long-term viability of the workforce. Without digital transformation, manufacturing risks becoming an industry of the past, losing its appeal to the workers it needs to sustain its future growth.
1Lack of Cutting-Edge Technology Reduces Appeal:
Younger workers, particularly from Generation Z, grew up in an era where cutting-edge technology was an integral part of daily life. When entering the workforce, they expect the same level of sophistication in their tools and systems. Manufacturing environments that fail to invest in the latest machinery, software, or automation solutions struggle to appeal to this tech-savvy demographic. Outdated equipment can make potential hires feel like they are stepping backward in time rather than forward in their careers, making them more likely to seek opportunities elsewhere.
Mitigations: Investing in advanced technologies like smart machines, robotics, and AI-driven systems will improve operational efficiency and significantly enhance your company’s appeal to younger workers. Demonstrating a commitment to staying at the forefront of technology signals that your organization values innovation and growth.
2Delayed Automation Turns Away Tech-Savvy Workers:
Automation is a cornerstone of Industry 4.0, offering increased efficiency and precision. However, organizations slow to adopt automation inadvertently turn away younger workers, who are often eager to engage with new systems and technology. They are less interested in manual, repetitive tasks and more attracted to environments where automation frees up their time to focus on problem-solving and creativity.
Mitigations: Prioritizing the implementation of automation technologies can create more stimulating job roles, allowing younger workers to focus on higher-order tasks that require critical thinking. Encouraging their input on automation initiatives can also increase engagement and investment in the success of new systems.
3Slow Adoption of Data-Driven Processes:
Data-driven decision-making is a hallmark of Industry 4.0, yet many companies still rely on traditional intuition-based approaches. Younger generations, particularly those with technical backgrounds, are often frustrated by environments where real-time data is not utilized to optimize processes. This can lead to dissatisfaction, as they may feel their skills are undervalued or underutilized.
Mitigations: Implementing advanced analytics and data platforms to inform decision-making will appeal to younger workers and increase productivity. Ensure that shop floor managers can interpret and act on data insights, making data-driven approaches an integral part of the organization’s daily operations.
4No Cloud Systems:
Cloud-based systems enable flexibility, scalability, and real-time collaboration, which younger workers highly value. In contrast, organizations that still rely on outdated, on-premise systems may be seen as inflexible and behind the times. This creates inefficiencies and makes it difficult for younger workers to engage fully with their roles.
Mitigations: Transitioning to cloud-based solutions for data storage, project management, and operational control will enhance collaboration and provide a modern work environment. Cloud systems offer a seamless way to integrate various aspects of the business, from supply chain management to predictive maintenance, making work more dynamic and efficient for younger employees.
5Poor IoT Integration:
The Internet of Things (IoT) is integral to modern manufacturing, allowing machines, sensors, and systems to communicate in real time. However, companies that fail to integrate IoT into their operations risk alienating younger workers who expect smart, interconnected environments. The absence of IoT can create operational silos, reducing efficiency and creating frustration among tech-savvy hires.
Mitigations: Investing in IoT solutions allows for real-time monitoring, predictive maintenance, and increased machine uptime. Encouraging younger workers to help implement and optimize IoT systems will empower them and improve job satisfaction, making the work environment more attractive and forward-thinking.
6Outdated Communication Methods:
Younger workers, especially those from Gen Z, are used to communicating through digital channels like instant messaging and collaboration apps. Companies still reliant on traditional communication methods like emails, phone calls, or paper memos risk losing their appeal. This disconnect can make collaboration slow and cumbersome, resulting in frustration and disengagement.
Mitigations: Modernizing communication methods using Slack, Microsoft Teams, or other instant messaging platforms will facilitate better collaboration and engagement. These platforms streamline communication, allowing for quick decision-making and reducing the chances of miscommunication across the shop floor.
7Limited Digital Collaboration Tools:
In a world where remote work and digital collaboration are becoming the norm, the absence of digital tools for teamwork can alienate younger workers. They expect the same technological support at work as in their personal lives, especially regarding collaborative projects.
Mitigations: Implementing digital collaboration tools like project management software, video conferencing platforms, and shared digital workspaces will enhance teamwork and make younger employees feel more engaged. These tools enable real-time collaboration, even for geographically dispersed teams, aligning with the expectations of younger generations.
8Poor Digital Literacy Creates a Skills Gap:
The failure to provide ongoing training in digital tools can lead to a growing skills gap, particularly when onboarding younger workers. Digital natives expect workplaces to be fluent in the latest technologies. A lack of digital literacy among existing employees can frustrate new hires, who may feel they are working with outdated processes and colleagues not equipped to handle modern challenges.
Mitigations: Offering regular digital literacy training for all employees, regardless of age or experience, will close this gap. A digitally fluent workforce boosts productivity and shows younger hires that the organization is committed to continuous improvement and staying ahead of technological trends.
9Outdated Equipment:
Working with outdated equipment can be a major deterrent for younger workers. Modern manufacturing tools and machines should be optimized for efficiency and safety, but older equipment often fails in both areas. Younger workers, raised in a world of constant technological updates, may feel stifled by equipment that doesn’t reflect the latest advancements.
Mitigations: Regularly updating and upgrading equipment demonstrates a commitment to innovation and safety. This attracts younger talent and helps maintain a competitive edge in the market, improving worker satisfaction and overall productivity.
10Stagnation in Digital Tools:
If an organization is stagnant in adopting digital tools, younger workers may see little opportunity for personal or professional growth. In the fast-paced world of Industry 4.0, younger employees expect to work with the latest software, platforms, and tools. When they don’t, it signals that the company is not future-focused, leading to higher turnover rates.
Mitigations: Investing in new digital tools, platforms, and software will keep your organization competitive and attract younger workers eager to grow their careers. Creating an environment where innovation is encouraged will reduce turnover and ensure a more engaged and productive workforce.
Conclusions for Operations Leaders
Neglecting digital transformation doesn’t just lead to operational inefficiencies—it directly impacts your ability to attract and retain the younger, tech-savvy workforce that thrives in Industry 4.0 environments. These secondary symptoms discourage younger workers from joining or staying within your organization, from outdated machinery and limited automation to a lack of real-time data.
Ready to Transform Your Manufacturing Operations with Real-Time Data and AI-Powered Insights?
At POWERS, we understand the importance of embracing digital transformation to future-proof your operations, making them more sustainable and scalable. Our approach isn’t just about introducing new technology; it’s about providing a comprehensive digital solution that helps optimize every aspect of your value chain. By partnering with POWERS, you gain access to industry-leading insights, tools, and strategies that will help you tackle these digital challenges head-on.
With this in mind, we’ve introduced DPS, our Digital Production System, designed specifically to help manufacturers modernize and stay competitive in the digital era. DPS combines decades of industry expertise with advanced technology, offering you a seamless digital transformation.
Here’s how DPS can support your digital transformation:
- Complete Visibility: Gain real-time insights through intuitive dashboards, appealing to younger workers who expect data-driven, modern work environments.
- Enhanced Collaboration: Facilitate seamless communication with collaborative tools that engage digital-native employees and foster innovation.
- Data-Driven Decision Making: Use AI-driven insights to optimize operations, attracting younger workers who value smart, efficient decision-making processes.
- Boosted Productivity and Efficiency: Minimize manual tasks and embrace automation, creating tech-focused roles that are more appealing to younger, innovation-driven talent.
By implementing DPS and working with POWERS, your business will attract the next generation of digitally-minded workers and position itself as a forward-thinking leader in manufacturing. The future of manufacturing relies on digital transformation, and POWERS is here to guide you through every step, ensuring your operations remain productive, efficient, and ready for the challenges of tomorrow.
- Speak to an Expert: Call +1 678-971-4711 to discuss your specific challenges and goals.
- Email Us: Get tailored insights by emailing info@thepowerscompany.com
- Request an Assessment: Use our online contact form, and one of our expert manufacturing consultants will reach out to schedule an in-depth analysis of your operations.
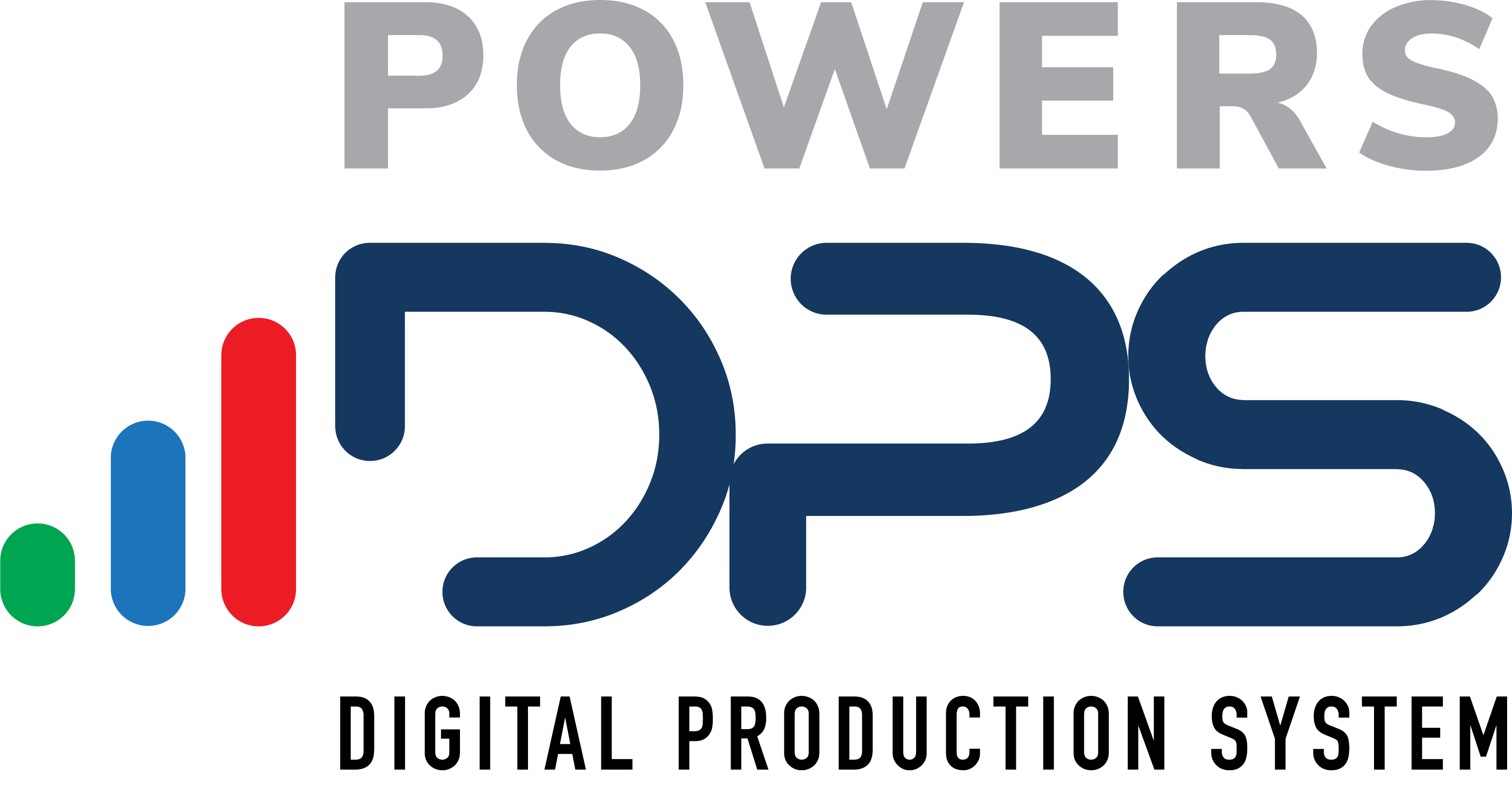
Start transforming your operations today with POWERS DPS. Contact us for a free consultation and see how digital transformation can revolutionize your manufacturing future. Learn More about DPS
Continue Reading from this Mastery Series
- Part 1 – Outdated Tech is Weakening Your Talent Pipeline
- Part 2 – How Legacy Systems Sabotage Your Cybersecurity and Productivity
- Part 3 – How Ignoring Digital Tools Leaves You Vulnerable to Downtime
- Part 4 – When Digital Stagnation Leads to Poor Communication and Production Chaos
- Part 5 – The Real Cost of Trying to Keep Up in the Market Without Digital Transformation
- Part 6 – Missing Out on Real-Time Data Drains Productivity and Profit
- Part 7 – How Failing To Go Digital Jeopardizes Regulatory Compliance
- Part 8 – How Outdated Inventory Practices Sabotage Your Operations
- Part 9 – Limited Customization Options are Driving Your Customers Away
- Part 10 – The Productivity Trap of Failing to Scale Digital Initiatives