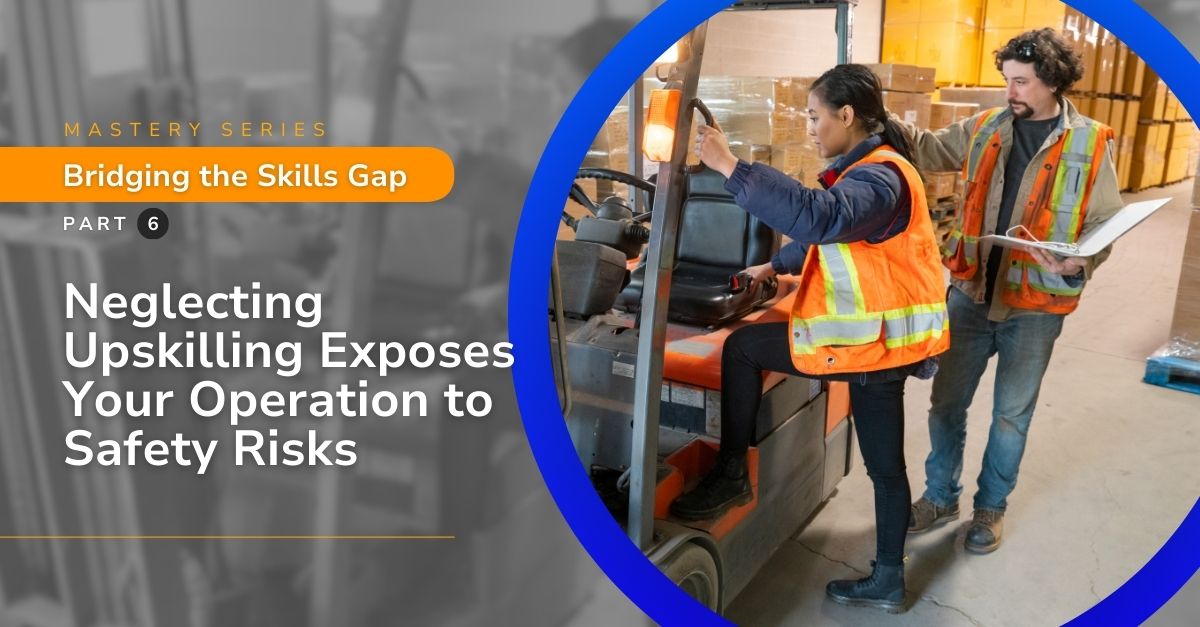
In an industry where safety is paramount, failing to keep your workforce up-to-date with the latest safety protocols and regulations can have catastrophic consequences.
Workers untrained in the latest safety measures struggle to keep up with new standards, leading to hidden but costly issues on the shop floor. These secondary symptoms can compound over time, making it harder for teams to adapt and managers to maintain efficiency.
For example, a common issue many manufacturing managers face is the improper handling of hazardous materials. Employees not regularly trained on updated handling procedures may default to older, less stringent methods, increasing the likelihood of safety violations.
One less common but critical consequence of this neglect is the failure to correctly calibrate new safety equipment. When protocols change and require updated use or calibration of safety devices—such as gas detectors or automated shut-off systems—workers lacking the necessary training may misconfigure them. This results in inaccurate readings or delayed emergency responses, which can cause avoidable production downtime or even accidents.
The impact of failing to adapt to new safety protocols creates layers of inefficiencies that experienced managers have to address daily.
Let’s examine how neglecting upskilling in the context of safety regulations leads to tangible productivity losses on the shop floor. The effects are felt across the entire organization, from longer lead times in resolving safety issues to an increased frequency of minor violations.
This post uncovers ten ways that neglecting investment in upskilling leads to difficulty adapting to new safety protocols and regulations and how these granular challenges manifest on the shop floor.
1Confusion Around Safety Hierarchy and Escalation Procedures:
When employees lack proper training, confusion about safety hierarchy and the correct procedures for escalating safety concerns often arises. Without a clear understanding of whom to report issues to and when, safety problems can go unaddressed, leading to unresolved risks and inefficient response times.
Mitigation: Implementing a structured upskilling program that emphasizes the organization’s safety hierarchy and escalation protocols can help eliminate confusion, especially in high-stress situations like injuries. By offering workshops or refresher courses on safety reporting structures, employees can better understand who to approach in emergencies, resulting in more effective safety management.
2Inaccurate Reporting of Near-Miss Incidents:
Inadequate training in modern safety protocols can lead to inaccurate or incomplete reporting of near-miss incidents. When unreported or poorly documented, these incidents prevent organizations from identifying potential hazards that could lead to serious accidents down the line, ultimately affecting productivity through safety-related disruptions.
Mitigation: Establishing comprehensive training on near-miss reporting can ensure that employees accurately document potential hazards. This approach helps identify risk areas before they escalate, ultimately reducing the number of safety incidents and their negative impact on productivity.
3Decreased Ability to Pass Regulatory Inspections:
A workforce untrained in the latest safety regulations is less likely to be prepared for regulatory inspections, leading to failed audits, fines, and costly shutdowns. These disruptions damage a company’s reputation and lead to operational delays.
Mitigation: Regular upskilling sessions focused on regulatory changes and compliance can prepare employees for audits. Organizations can reduce the risk of failing inspections by training workers on existing and updated regulations and maintaining continuous productivity.
4Increased Frequency of Minor Safety Violations:
Without proper training, employees may unknowingly commit minor safety violations, such as incorrect equipment handling or failing to wear PPE. These infractions can also unwittingly communicate a lax attitude when it comes to safety. While these violations might not result in immediate accidents, they create ongoing safety risks that can accumulate into larger problems, impacting long-term productivity.
Mitigation: Routine safety drills and workshops can remind employees of the importance of adhering to even minor safety regulations. Reinforcing the proper use of equipment and PPE through targeted training can help prevent these violations and safeguard productivity by maintaining a safer work environment.
5Delayed Response Times to New Hazard Warnings:
A workforce unfamiliar with updated hazard warning systems or safety protocols will struggle to respond promptly to new risks. Delayed reactions to potential hazards can lead to increased downtime and greater exposure to workplace accidents, which hampers operational efficiency.
Mitigation: A proactive training program that covers the identification and response to new hazard warnings can improve response times. By regularly updating employees on hazard recognition and mitigation strategies, organizations can significantly reduce downtime caused by safety concerns.
6Longer Lead Times for Resolving Safety-Related Issues:
When employees are not properly trained to troubleshoot safety-related issues, it often results in longer lead times for resolving these problems. This can cause extended production delays and missed deadlines, especially in industries where safety is tightly intertwined with operational workflows.
Mitigation: Upskilling employees on troubleshooting techniques for safety issues can shorten lead times and keep production on schedule. Training workers to independently identify and resolve safety risks can reduce bottlenecks and allow quicker recovery from safety-related disruptions.
7Inconsistent Use of Personal Protective Equipment (PPE):
A workforce lacking up-to-date training on the proper use of PPE is more likely to misuse or inconsistently wear required safety gear. This inconsistency increases the likelihood of workplace injuries, leading to unplanned downtime and decreased productivity as operations are paused for accident investigations and corrective actions.
Mitigation: Introducing regular, hands-on PPE training sessions ensures employees understand when and how to use their equipment. Reinforcing PPE protocols through ongoing education can prevent accidents, thus maintaining uninterrupted productivity.
8Misinterpretation of Updated Safety Guidelines:
New safety guidelines can be complex, and employees who have not been properly trained to understand these updates are at risk of misinterpreting them. This can result in improper execution of safety protocols, leading to accidents, fines, or shutdowns that derail productivity.
Mitigation: Offering comprehensive training programs to clarify new safety guidelines ensures that employees fully understand and correctly implement them. This approach reduces the risk of accidents and keeps operations running smoothly.
9Over-reliance on Outdated Safety Practices:
When employees are not regularly updated on new safety standards, they tend to rely on outdated practices that may no longer be effective or compliant. This over-reliance can result in unsafe working conditions, higher accident rates, and diminished productivity due to frequent stoppages and investigations.
Mitigation: Regular safety refreshers and upskilling programs that replace outdated practices with current, compliant methods can eliminate this over-reliance. Keeping the workforce updated on the latest safety standards minimizes risks and promotes a safer, more productive workplace.
10Higher Likelihood of Safety-Related Downtime:
When safety protocols are misunderstood or poorly implemented due to a lack of upskilling, the likelihood of safety-related downtime increases, this downtime directly impacts productivity and profitability, whether from accidents, near-miss investigations, or regulatory shutdowns.
Mitigation: Consistent investment in safety training and upskilling ensures that employees are well-versed in current safety protocols, reducing the chances of safety-related incidents that lead to downtime. A well-trained workforce keeps operations running smoothly and efficiently, minimizing interruptions due to safety concerns.
Conclusions for Operations Leaders
Neglecting to invest in upskilling creates an environment where safety protocols and regulations are poorly understood, leading to numerous challenges on the shop floor. When workers cannot adapt to new safety measures, managers are forced to deal with longer response times, inconsistent compliance, and more frequent safety violations, which negatively impact productivity. These seemingly small, secondary symptoms accumulate over time, creating significant disruptions that hinder the operational efficiency of the entire organization.
By working closely with your team, POWERS ensures that continuous employee development in the mission-critical area of safety training is integrated into the company’s overall operational strategy, leading to improved compliance and reduced downtime.
With POWERS, manufacturing organizations can experience:
- Faster adaptation to new safety protocols and regulations, minimizing downtime and disruptions.
- Improved compliance with safety standards, ensuring seamless regulatory inspections.
- More consistent use of updated safety practices and equipment, reducing safety violations.
- Streamlined processes for identifying and resolving safety issues, boosting overall productivity.
Our hands-on approach and deep expertise in manufacturing operations ensure that your workforce is fully prepared to meet today’s safety challenges while boosting productivity. By investing in upskilling, you can avoid the costly consequences of safety-related disruptions and set your team up for long-term success.
To learn more about how POWERS can help your organization stay compliant, efficient, and safe, contact us today to begin transforming your safety culture.
- Speak to an Expert: Call +1 678-971-4711 to discuss your specific challenges and goals.
- Email Us: Get tailored insights by emailing info@thepowerscompany.com
- Request an Assessment: Use our online contact form, and one of our expert manufacturing consultants will reach out to schedule an in-depth analysis of your operations.
Continue Reading from this Mastery Series
- Part 1 – Why Automation Alone Won’t Boost Productivity
- Part 2 – Why Non-Technical Skills Are Increasingly the Key to Increasing Productivity
- Part 3 – The Widening Digital Divide is Leaving Some Companies in the Dust
- Part 4 – Lack of Upskilling Sabotages Problem-Solving, Decision Making, and Innovation
- Part 5 – The Link Between Upskilling and Employee Well-being
- Part 6 – Neglecting Upskilling Leaves Your Operation Vulnerable to Safety Issues
- Part 7 – How Neglecting Upskilling Erodes Legacy Knowledge and Hurts Productivity
- Part 8 – Failing to Upskill Frontline Leaders Can Derail Operations
- Part 9 – Skimping on Skills Training Sabotages the Bottom Line
- Part 10 – An Underdeveloped Workforce Means an Unscalable Operation