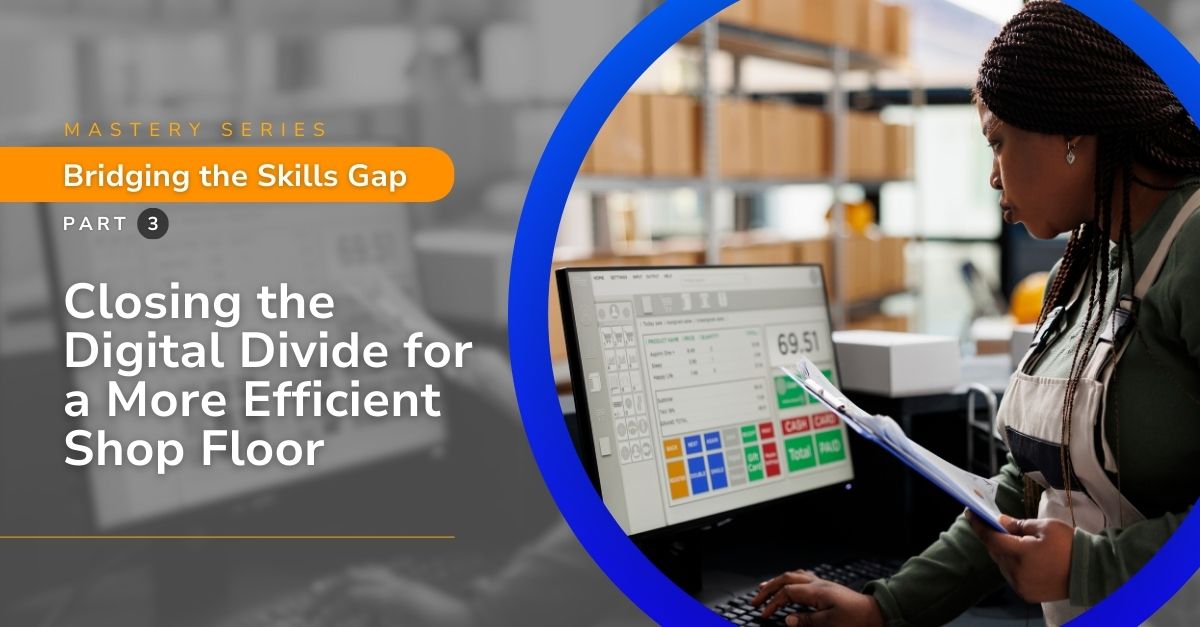
As manufacturing evolves into an increasingly digital landscape, the gap between skilled and unskilled workers continues to widen, mainly due to insufficient investment in upskilling.
While many companies focus on adopting cutting-edge tools, they often overlook the importance of upskilling their workforce to effectively use these new technologies.
This divide creates a host of secondary issues on the shop floor, significantly hampering productivity.
A less high-tech but equally impactful example of this digital divide is many workers’ struggle with digital document management systems. In many manufacturing environments, shift reports, maintenance logs, and safety protocols have moved from paper to digital formats.
When workers aren’t adequately trained to use these systems, critical documents can be mismanaged or improperly filed, leading to inefficiencies, delays, and mistakes. For instance, a worker might not update an equipment maintenance log correctly, causing the maintenance team to miss a crucial repair, leading to unplanned downtime. The issue here isn’t the complexity of the technology—it’s the workforce’s lack of familiarity with basic digital tools, which prevents them from streamlining daily operations.
This example illustrates one of many ways the widening digital divide affects productivity on the shop floor. Below are ten specific areas where an ever-widening skills gap in your workforce creates significant challenges. If not properly addressed, each can lead to inefficiencies and operational setbacks.
1Inability to Interpret Real-Time Data from IoT Devices:
The Internet of Things (IoT) has revolutionized manufacturing by providing real-time data to inform decisions, but without proper training, employees cannot often interpret this data effectively. This results in missed opportunities for preventive maintenance, optimizing energy consumption, or improving operational efficiency. When workers can’t act on IoT insights, it becomes just another set of numbers rather than a tool for improving operations.
Mitigation: Investing in IoT-specific training can bridge this knowledge gap. Provide hands-on workshops and regular refresher courses to help workers become comfortable interpreting and acting on data in real time. This empowers the workforce to make data-driven decisions that improve uptime and enhance productivity on the floor.
2Delayed Adoption of Cloud-Based Platforms:
Cloud-based platforms can streamline operations, improve collaboration, and provide scalability. However, when employees are unprepared to use these platforms effectively, adoption is delayed, often leading to inefficient manual processes that slow production. The resistance to cloud-based solutions also limits a company’s ability to maintain operational resilience in times of change.
Mitigation: Encourage a smooth transition by providing comprehensive training using cloud-based tools and platforms. Offering mentorship programs where skilled workers help train less-experienced employees can also accelerate adoption and reduce downtime associated with the learning curve. This accelerates efficiency and helps keep operations agile.
3Resistance to Using Advanced Software for Inventory Management:
Advanced inventory management systems have the potential to dramatically reduce errors and streamline logistics, but if employees are not comfortable using these tools, they revert to manual or outdated methods. This leads to inefficiencies, incorrect stock levels, and delays in fulfilling orders, hampering productivity across the board.
Mitigation: Regular training sessions, paired with real-time support during the early stages of implementation, can reduce resistance to new inventory systems. Implementing role-specific training modules ensures that employees at all levels understand how to use the software effectively. By eliminating knowledge gaps, productivity and accuracy in inventory management will increase.
4Inconsistent Data Entry in Digital Systems:
Digital systems are only as good as the data input into them. When employees are not properly trained to handle digital tools, data entry becomes inconsistent, leading to errors that can snowball into larger operational issues. Inconsistent data entry results in incorrect reporting, misinformed decision-making, and decreased operational efficiency.
Mitigation: Standardized training on data entry protocols and system usage should be mandatory across the workforce. This can be supplemented by user-friendly interfaces and automated error-checking mechanisms within the digital systems, reducing the likelihood of errors. This consistency in data entry will help ensure operational integrity and improved productivity.
5Inability to Troubleshoot Digital Manufacturing Equipment:
As more equipment becomes digitized, the inability to troubleshoot basic digital issues on the shop floor can cause unnecessary downtime. Workers without the skills to diagnose or fix simple digital errors must rely on specialists or external contractors, delaying problem resolution and slowing production.
Mitigation: Upskilling programs focused on basic troubleshooting of digital equipment should be implemented to empower workers to resolve minor issues independently. Combining online modules with hands-on workshops can help employees gain confidence in managing equipment problems, reducing costly delays.
6Reduced Efficiency in Implementing Remote Monitoring Systems:
Remote monitoring systems allow manufacturers to oversee multiple processes in real-time, reducing the need for constant manual checks. However, when workers are not trained to implement or use these systems, efficiency gains are negated, and manual monitoring continues to slow productivity.
Mitigation: Provide in-depth training on implementing and using remote monitoring tools, ensuring that employees can maximize the benefits of these systems. Ongoing support and a culture of continuous learning will enable smoother integration, leading to improved overall efficiency.
7Mismanagement of Big Data Analytics Projects:
Big data analytics can provide valuable insights that drive production, quality, and efficiency improvements. However, employees may misinterpret or mismanage the data without sufficient training in managing these projects, leading to misguided strategies or operational inefficiencies.
Mitigation: Offering targeted training in data analytics for manufacturing helps ensure that employees understand how to interpret and act on data insights. Collaborating with external experts to design easy-to-understand, practical courses will enhance employees’ ability to handle big data analytics effectively.
8Improper Usage of 3D Printing Technologies:
3D printing is transforming manufacturing, but its potential is underutilized when employees lack the training to use it correctly. Misusing 3D printers results in wasted materials, poor-quality prototypes, and longer production times. This improper usage can undermine the cost-saving benefits of the technology.
Mitigation: Comprehensive training programs that cover everything from the basics of operating 3D printers to advanced techniques for optimizing production should be implemented. Training should be combined with real-world practice to help employees become proficient in leveraging this transformative technology for maximum productivity.
9Inconsistent Follow-Up on Data-Driven Insights:
Inconsistent follow-up on data-driven insights can cause inefficiencies to persist despite having access to valuable data. This issue often arises when workers do not fully understand the importance of acting on insights or lack the training to do so effectively, causing productivity bottlenecks.
Mitigation: Developing a robust feedback loop that ensures follow-up actions based on data insights can mitigate this issue. Managers should regularly review key performance indicators (KPIs) and ensure employees understand how to act on the insights. Offering training on interpreting and implementing data-driven changes will improve operational efficiency.
10Difficulty in Digital Document Management and Sharing:
Digital document management systems can save time and reduce errors. Still, improper usage due to a lack of training often leads to mismanaged documents, version control issues, and inefficiencies in accessing critical information. This can slow down decision-making and disrupt the flow of operations.
Mitigation: Implement a digital literacy program that includes document management and training on sharing protocols. By ensuring that employees are well-versed in using digital systems for document control, you can significantly enhance your team’s efficiency, reducing time wasted searching for or correcting errors in documentation.
Conclusions for Operations Leaders
Neglecting investment in upskilling creates a widening digital divide that has far-reaching consequences in manufacturing. The secondary symptoms, such as inconsistent data entry, delayed adoption of technology, and mismanagement of advanced systems, all contribute to a decline in productivity.
When workers lack the skills to effectively use new tools or collaborate across departments, the result is inefficient operations, costly delays, and a failure to capitalize on digital transformation. Bridging this gap requires more than just training in technical competencies—it demands a focus on developing critical non-technical skills, such as communication and problem-solving, that are vital to modern manufacturing success.
By partnering with POWERS, you can empower your workforce to fully leverage digital advancements and drive sustainable productivity improvements. Our approach doesn’t just focus on skill development—it focuses on the alignment of behaviors and systems to create long-term operational excellence.
Here’s how POWERS can help:
- Provide comprehensive training programs that address both technical and non-technical skills.
- Implement customized strategies to reduce inefficiencies related to the digital divide.
- Facilitate smoother transitions to cloud-based and automated systems, minimizing downtime.
- Improve interdepartmental collaboration through targeted communication and problem-solving workshops.
- Optimize data management and digital tool usage to reduce errors and maximize output.
By closing the skills gap, POWERS enables manufacturers to boost productivity, reduce downtime, and stay competitive in an increasingly digital industry. Let us help you build a workforce prepared to meet tomorrow’s challenges.
- Speak to an Expert: Call +1 678-971-4711 to discuss your specific challenges and goals.
- Email Us: Get tailored insights by emailing info@thepowerscompany.com
- Request an Assessment: Use our online contact form, and one of our expert manufacturing consultants will reach out to schedule an in-depth analysis of your operations.
Continue Reading from this Mastery Series
- Part 1 – Why Automation Alone Won’t Boost Productivity
- Part 2 – Why Non-Technical Skills Are Increasingly the Key to Increasing Productivity
- Part 3 – The Widening Digital Divide is Leaving Some Companies in the Dust
- Part 4 – Lack of Upskilling Sabotages Problem-Solving, Decision Making, and Innovation
- Part 5 – The Link Between Upskilling and Employee Well-being
- Part 6 – Neglecting Upskilling Leaves Your Operation Vulnerable to Safety Issues
- Part 7 – How Neglecting Upskilling Erodes Legacy Knowledge and Hurts Productivity
- Part 8 – Failing to Upskill Frontline Leaders Can Derail Operations
- Part 9 – Skimping on Skills Training Sabotages the Bottom Line
- Part 10 – An Underdeveloped Workforce Means an Unscalable Operation