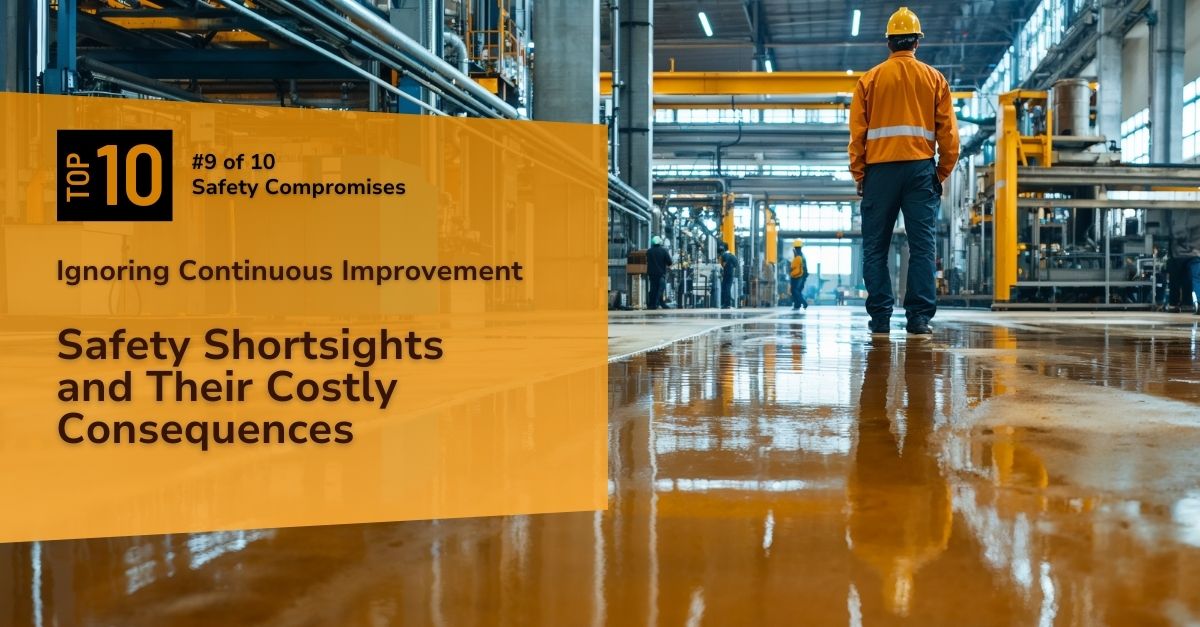
Continuous improvement is the cornerstone of any successful manufacturing operation. When this practice is neglected, the impact is most visibly felt in safety standards.
Over time, small lapses in safety procedures can accumulate, leading to significant hazards that compromise the well-being of workers and the efficiency of operations.
One less common yet critical example is the unnoticed deterioration of machine calibration processes. When calibration is ignored as part of continuous improvement, it can lead to subtle inaccuracies in machinery performance. These inaccuracies may not immediately present as major safety hazards but can cause tools to malfunction over time, leading to unexpected injuries or accidents. For instance, a poorly calibrated press might apply uneven force, increasing the likelihood of parts flying off at high speeds posing a significant danger to workers nearby. This kind of secondary symptom is often overlooked until it’s too late, with the root cause traced back to the lack of a systematic approach to continuous improvement.
The consequences of neglecting continuous improvement extend beyond these specific examples. Without ongoing efforts to enhance safety practices, manufacturing floors become breeding grounds for potential hazards. Each missed improvement opportunity increases the likelihood of accidents, delays, and inefficiencies, ultimately harming workers and the bottom line. This introduction sets the stage for exploring the top 10 ways neglecting continuous improvement leads to safety compromises and the resulting impact on productivity.
1Slower Emergency Response Times:
Responding quickly and effectively to emergencies is critical in a manufacturing setting. Without a focus on continuous improvement, emergency response protocols can become outdated or poorly executed, leading to slower response times. This can result in increased injury severity, prolonged downtime, and heightened employee anxiety, all negatively impacting productivity.
Mitigation Strategy: Improving emergency response times requires regular drills, updated training, and investment in new technologies such as real-time communication systems. Ensuring that all employees are well-versed in the latest protocols and that emergency plans are reviewed and refined regularly can dramatically reduce response times and improve overall safety.
2Inadequate Safety Inspections:
Routine safety inspections are essential to identifying potential hazards before incidents occur. When continuous improvement is neglected, these inspections can become perfunctory, missing critical issues that could compromise worker safety. Over time, this lax approach can allow small problems to escalate into serious safety risks, contributing to costly accidents and decreased productivity.
Mitigation Strategy: To counteract inadequate safety inspections, it’s vital to establish a culture of thoroughness and accountability. Implementing digital checklists and data analytics to track inspection results can help identify trends and ensure no safety is overlooked. Regularly rotating inspection responsibilities can also bring fresh perspectives and prevent complacency.
3Incomplete Machine Guarding:
Machine guarding is a fundamental safety measure, yet it’s often one of the first areas to suffer when continuous improvement is neglected. Incomplete or improperly maintained machine guards can expose workers to serious hazards, including amputations or other severe injuries. This endangers employees and leads to increased downtime and potential legal liabilities.
Mitigation Strategy: To address incomplete machine guarding, it’s crucial to integrate regular audits into the maintenance schedule. These audits should assess existing guards’ condition and identify gaps where improvements are needed. Involving machine operators in the process can also provide valuable insights and ensure that guards are functional and user-friendly.
4Outdated Safety Data Sheets (SDS):
Safety Data Sheets (SDS) are critical for informing workers about the hazards associated with chemicals and materials used on the shop floor. When SDS is outdated or inaccessible, employees may unknowingly expose themselves to dangerous substances, leading to health risks and potential OSHA violations. This can result in increased absenteeism, lower morale, and reduced productivity.
Mitigation Strategy: Maintaining up-to-date SDS requires a systematic approach. Companies should implement a digital SDS management system that allows easy updates and ensures all employees have quick access to the information they need. Regular training sessions can reinforce the importance of using SDS and help prevent accidental exposures.
5Unmonitored Exposure to Toxic Substances:
Exposure to toxic substances is a hidden danger on many manufacturing floors. Without continuous improvement, monitoring systems can fall by the wayside, allowing exposure levels to exceed safe limits. This can lead to chronic health issues for employees, increased sick leave, and potentially severe legal consequences for the company.
Mitigation Strategy: To mitigate the risk of unmonitored exposure, companies should invest in real-time air quality monitoring systems. These systems can detect harmful substances and alert workers to potential dangers before they cause harm. Regular health screenings and environmental assessments can help identify and address exposure risks before they impact worker health.
6Lack of Real-Time Safety Data Analytics:
Data analytics has become a powerful tool for identifying safety risks, but implementing these technologies often lags when continuous improvement is ignored. Without real-time safety data analytics, companies miss opportunities to predict and prevent accidents, leading to higher incident rates and lower productivity.
Mitigation Strategy: To harness the power of safety data analytics, companies should integrate sensors and data collection tools across the shop floor. Analyzing this data in real time allows for quick identification of trends and potential hazards, enabling proactive measures that prevent incidents before they occur. Continuous investment in data analytics technology ensures that safety practices evolve alongside industry advancements.
7Missed Correlations Between Data and Safety Incidents:
A significant risk of neglecting continuous improvement is the failure to connect the dots between seemingly unrelated safety incidents. Without a culture of continuous improvement, valuable data may be overlooked, leading to missed correlations that could otherwise inform preventative measures. This can result in repeated incidents and a culture of complacency.
Mitigation Strategy: Addressing this issue requires a more analytical approach to safety data. Companies can uncover hidden correlations between incidents by employing root-cause analysis techniques and encouraging cross-departmental collaboration. This proactive approach reduces the likelihood of repeat incidents and fosters a culture of continuous learning and improvement.
8Inconsistent Lockout/Tagout Practices:
Lockout/Tagout (LOTO) procedures ensure that machines are properly shut down during maintenance. However, when continuous improvement is neglected, these practices can become inconsistent, increasing the risk of accidental start-ups and serious injuries. This inconsistency can lead to fatal accidents, costly lawsuits, and significant downtime.
Mitigation Strategy: To ensure consistent LOTO practices, companies should standardize procedures across all departments and provide regular training to reinforce their importance. Additionally, implementing a digital LOTO management system can help track compliance and identify areas for improvement. Regular audits and employee feedback can also help fine-tune procedures and ensure they are followed correctly.
9Delayed Repairs on Critical Equipment:
Timely repairs are crucial to maintaining both safety and productivity. When continuous improvement is neglected, repair schedules often slip, leading to the prolonged use of faulty equipment. This increases the risk of accidents and causes frequent breakdowns, further disrupting production and reducing overall efficiency.
Mitigation Strategy: To avoid delayed repairs, companies should implement a predictive maintenance program that uses data to identify when equipment will likely fail. This allows for repairs to be scheduled during planned downtime, minimizing disruptions. Regular communication between maintenance teams and operators ensures that issues are reported and addressed promptly.
10Unreliable Alarms and Warning Systems:
Alarms and warning systems are critical for alerting workers to immediate dangers. However, if these systems are not regularly tested and maintained, they can become unreliable. This can lead to missed warnings, preventable accidents, and a loss of employee trust, all of which negatively impact productivity.
Mitigation Strategy: To ensure the reliability of alarms and warning systems, companies should schedule regular testing and maintenance. Upgrading to more advanced systems that offer real-time monitoring and self-diagnostics can also help prevent failures. Training employees to respond effectively to alarms further reinforces the importance of these systems and improves overall safety on the shop floor.
Conclusions for Operations Leaders
Safety is not just a compliance issue; it’s a critical component of productivity and operational efficiency in manufacturing. Neglecting continuous improvement in safety practices can lead to a series of secondary symptoms that compromise the well-being of workers and hinder productivity. From slower emergency response times to unreliable alarms, these issues accumulate over time, creating an unsafe work environment and negatively impacting the bottom line.
We work directly with your leadership team to identify and address the root causes of safety issues, implementing strategies that prevent accidents and enhance overall operational efficiency.
POWERS Can Help You:
- Safety Audits and Root Cause Analysis: Identify and resolve hidden safety risks through comprehensive audits and deep root cause analysis.
- Predictive Maintenance and Real-Time Monitoring: Implement data-driven maintenance programs and advanced monitoring systems to prevent safety hazards before they occur.
- Standardized Safety Procedures: Develop and enforce consistent safety protocols across all departments to ensure a unified approach to workplace safety.
- Targeted Employee Training: Provide ongoing, specialized training to keep employees up-to-date with the latest safety practices and protocols.
By partnering with POWERS, you can build a safer, more productive work environment where continuous improvement drives safety and efficiency. Our tailored solutions are designed to address the unique challenges of your operation, ensuring sustainable improvements and measurable ROI. Let us help you operationalize your safety culture and unlock the full potential of your workforce.
- Speak to an Expert: Call +1 678-971-4711 to discuss your specific challenges and goals.
- Email Us: Get tailored insights by emailing info@thepowerscompany.com
- Request an Assessment: Use our online contact form, and one of our expert manufacturing consultants will reach out to schedule an in-depth analysis of your operations.
Continue Reading from this Mastery Series
- Part 1 – When Progress Takes a Break, it Leaves Your Productivity Stalled
- Part 2 – Profit Erosion in the Production Line
- Part 3 – Quality Takes a Dive and Productivity Pays the Price
- Part 4 – When Morale Breaks Down So Does the Shop Floor
- Part 5 – When Innovation Pauses, Your Production Line Follows
- Part 6 – How Customer Loyalty Slips Through Your Fingers
- Part 7 – When Your Slice of the Market Becomes a Crumb
- Part 8 – When Opportunities Slip Through the Cracks
- Part 9 – Safety Shortsights and Their Costly Consequences
- Part 10 – Growth and Adaptation Slows to a Crawl