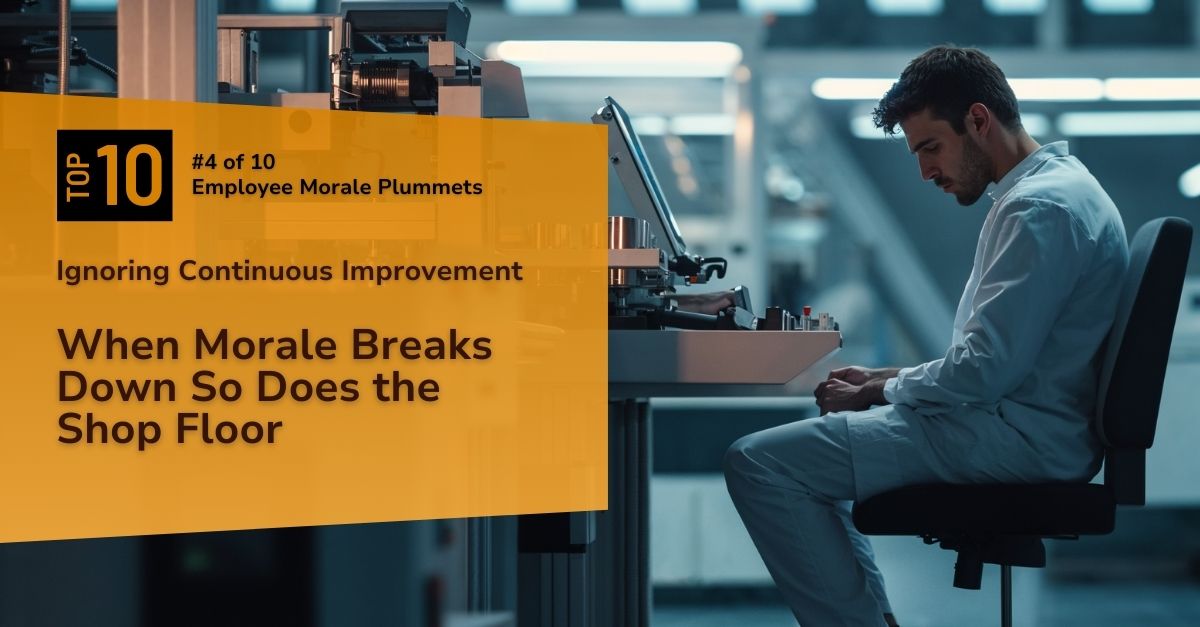
When a company neglects continuous improvement, the consequences go beyond operational inefficiencies. In the manufacturing sector, where precision, teamwork, and consistent output are crucial, ignoring continuous improvement can directly impact employee morale.
Take, for example, the situation in a mid-sized manufacturing plant that had experienced steady growth for years. As the company focused on scaling production, leadership gradually shifted away from continuous improvement programs that once empowered employees to suggest and implement process improvements. Over time, this shift led to a stagnation in employee skill development and a growing sense of disconnection from the company’s goals.
One of the less common symptoms of this neglect was a noticeable decline in employees’ willingness to take ownership of routine maintenance tasks—something that had previously been a point of pride on the shop floor.
Without reinforcing continuous improvement principles, workers began to view these tasks as burdensome rather than opportunities for contributing to operational excellence. The result was a slow but steady increase in unplanned downtime as small maintenance issues were left unaddressed until they became significant problems.
The ten points outlined in this post will delve into these secondary symptoms, providing insights into managers’ granular challenges and strategies to mitigate these issues before they undermine the entire manufacturing operation.
1Diminished Initiative for Process Improvements:
Employees may feel their ideas and contributions are undervalued when continuous improvement is sidelined. This leads to a diminished initiative for suggesting process improvements. Over time, employees become disengaged, thinking, “Why bother?” This lack of initiative stifles innovation and causes productivity to plateau as existing inefficiencies go unaddressed.
Mitigation Strategy: To reignite initiative, management must actively solicit employee input and create structured avenues for idea-sharing. Implementing a reward system for practical suggestions can also encourage participation. Managers should ensure that every idea, even those not immediately actionable, is acknowledged and appreciated to foster a culture of continuous improvement.
2Stagnation in Skill Development:
Continuous improvement often involves upskilling employees to adapt to new processes or technologies. When continuous improvement is ignored, employees miss opportunities to develop new skills. This stagnation leads to frustration and a sense of being “left behind,” negatively affecting morale and productivity as employees struggle to keep up with industry advancements.
Mitigation Strategy: Investing in regular training sessions and cross-training opportunities can help maintain and enhance employee skills. Encouraging a learning culture where employees are rewarded for acquiring new skills can revitalize morale. Managers should tailor training programs to individual career goals, ensuring employees see the value in their development.
3Higher Turnover Rates:
Neglecting continuous improvement can lead to a work environment where employees feel unchallenged and undervalued. This often results in higher turnover rates as employees seek growth opportunities elsewhere. High turnover disrupts team cohesion, increases recruitment costs, and diminishes productivity as new hires require time to reach full efficiency.
Mitigation Strategy: To combat high turnover, management should focus on career development and growth opportunities within the organization. Regularly conducting stay interviews can help identify and address employee concerns before they lead to resignations. Offering clear pathways for advancement and recognizing contributions can also improve retention rates.
4Loss of Trust in Management:
When management neglects continuous improvement, it sends a message that they are not invested in the company’s long-term success or the welfare of its employees. This leads to a loss of trust, where employees become skeptical of management’s decisions, disengaged, and less likely to go above and beyond in their roles.
Mitigation Strategy: Rebuilding trust requires transparency and consistent communication from management. Involving employees in decision-making processes and providing regular updates on company performance and continuous improvement initiatives can restore faith. Managers should be open to feedback and commit to acting on employee concerns.
5Decline in Quality of Work:
As morale declines, so does the quality of work. Employees who are disengaged or feel their efforts are not recognized are less likely to put in the extra effort to maintain high standards. This decline in quality can result in increased error rates, rework, and customer dissatisfaction, all negatively impacting productivity.
Mitigation Strategy: To improve work quality, management should set clear expectations and provide regular feedback. Recognizing and rewarding high-quality work can motivate employees to maintain standards. Implementing peer review processes and quality circles can also ensure employees take ownership of their work and strive for excellence.
6Reduced Alignment with Company Values:
Continuous improvement is closely tied to a company’s core values: innovation, excellence, and customer satisfaction. When continuous improvement is neglected, employees may become disconnected from these values, leading to a workforce that operates on autopilot rather than purposefully. This lack of alignment can result in inconsistent performance and a decline in overall productivity.
Mitigation Strategy: Reinforcing company values through regular communication and leadership modeling is crucial. Managers should integrate continuous improvement efforts with company values, showing employees how their work contributes to the mission. Engaging employees in value-based initiatives, such as customer-focused projects, can reignite their connection to the company’s purpose.
7Decreased Willingness to Train New Hires:
A key aspect of continuous improvement is knowledge sharing. When morale is low, experienced employees may be less willing to train new hires, seeing it as a burden rather than an opportunity to contribute to the team’s success. This reluctance leads to longer onboarding times and a steep learning curve for new employees, negatively affecting overall productivity.
Mitigation Strategy: To encourage knowledge sharing, management should recognize and reward employees who actively train new hires. Creating mentorship programs can also facilitate knowledge transfer and help new employees integrate more quickly. By fostering a supportive environment, seasoned employees are more likely to view training as a valued contribution.
8Poor Cross-Departmental Collaboration:
Morale-driven disengagement often leads to siloed behavior, where departments work in isolation rather than collaboratively. Poor cross-departmental collaboration can result in miscommunications, duplicated efforts, and a lack of innovation, all hindering productivity.
Mitigation Strategy: Improving collaboration requires breaking down silos and encouraging teamwork across departments. Regular cross-functional meetings and joint projects can help build relationships and improve communication. Managers should emphasize the importance of collaboration in achieving company-wide goals and recognize teams that work well together.
9Lack of Ownership of Tasks:
Employees may feel less accountable for their work when continuous improvement is overlooked. A lack of ownership often leads to tasks being completed with minimal effort, resulting in missed deadlines, subpar results, and increased oversight needed from managers, all of which drag down productivity.
Mitigation Strategy: To foster ownership, management should clearly define roles and responsibilities and empower employees to make decisions within their scope of work. Encouraging autonomy and providing opportunities for employees to lead projects can increase their sense of ownership. Regular check-ins and accountability measures can also ensure that tasks are completed with the necessary attention to detail.
10Resistance to Change:
Continuous improvement involves change, whether adopting new technologies, refining processes, or shifting strategies. Employees become accustomed to the status quo when continuous improvement is neglected and may resist change when necessary. This resistance can delay implementations, cause friction, and reduce the overall effectiveness of improvement initiatives.
Mitigation Strategy: Addressing resistance to change requires a proactive approach. Managers should involve employees early in the change process, clearly communicating the reasons for change and the benefits it will bring. Providing training and support during transitions can also ease concerns. Managers can minimize resistance and ensure smoother implementations by framing change as a positive and necessary evolution rather than a threat.
Conclusions for Operations Leaders
Neglecting continuous improvement in the manufacturing sector leads to more than just operational inefficiencies—it strikes at the core of what keeps a workforce motivated and engaged.
When continuous improvement is sidelined, employees feel their contributions are not valued, leading to a pervasive disengagement. This erosion of morale doesn’t just affect individual performance; it sets off a chain reaction of issues that can ripple throughout the organization.
The impacts are far-reaching, from a noticeable drop in initiative, where employees stop suggesting process improvements, to a growing resistance to change. Employees may become complacent, only doing the bare minimum, which stifles innovation and reduces the overall effectiveness of operations.
Over time, these issues compound, resulting in decreased productivity, higher turnover, and a work environment where employees feel disconnected from the company’s goals.
How POWERS Can Help
At POWERS, we recognize that a thriving workforce is at the heart of any successful continuous improvement strategy. Our approach goes beyond process optimization, focusing on re-engaging your employees and fostering a workplace culture that drives sustained productivity. We can help your organization by:
- Rebuilding Trust and Engagement: We help reestablish trust between management and employees through transparent communication and creating clear channels for idea-sharing.
- Enhancing Skill Development and Ownership: Our targeted training programs empower employees to continuously develop their skills and take ownership of their roles, leading to higher quality work and reduced turnover.
- Facilitating Cross-Departmental Collaboration: We break down silos and encourage teamwork across departments, improving communication and operational efficiency.
- Managing Change Effectively: Our change management strategies reduce resistance, ensuring smooth transitions during continuous improvement initiatives.
POWERS is dedicated to helping your manufacturing organization maintain a continuous improvement culture that enhances morale and productivity. Let us partner with you to implement strategies that elevate your people and processes, ensuring long-term success.
- Speak to an Expert: Call +1 678-971-4711 to discuss your specific challenges and goals.
- Email Us: Get tailored insights by emailing info@thepowerscompany.com
- Request an Assessment: Use our online contact form, and one of our expert manufacturing consultants will reach out to schedule an in-depth analysis of your operations.
Continue Reading from this Mastery Series
- Part 1 – When Progress Takes a Break, it Leaves Your Productivity Stalled
- Part 2 – Profit Erosion in the Production Line
- Part 3 – Quality Takes a Dive and Productivity Pays the Price
- Part 4 – When Morale Breaks Down So Does the Shop Floor
- Part 5 – When Innovation Pauses, Your Production Line Follows
- Part 6 – How Customer Loyalty Slips Through Your Fingers
- Part 7 – When Your Slice of the Market Becomes a Crumb
- Part 8 – When Opportunities Slip Through the Cracks
- Part 9 – Safety Shortsights and Their Costly Consequences
- Part 10 – Growth and Adaptation Slows to a Crawl