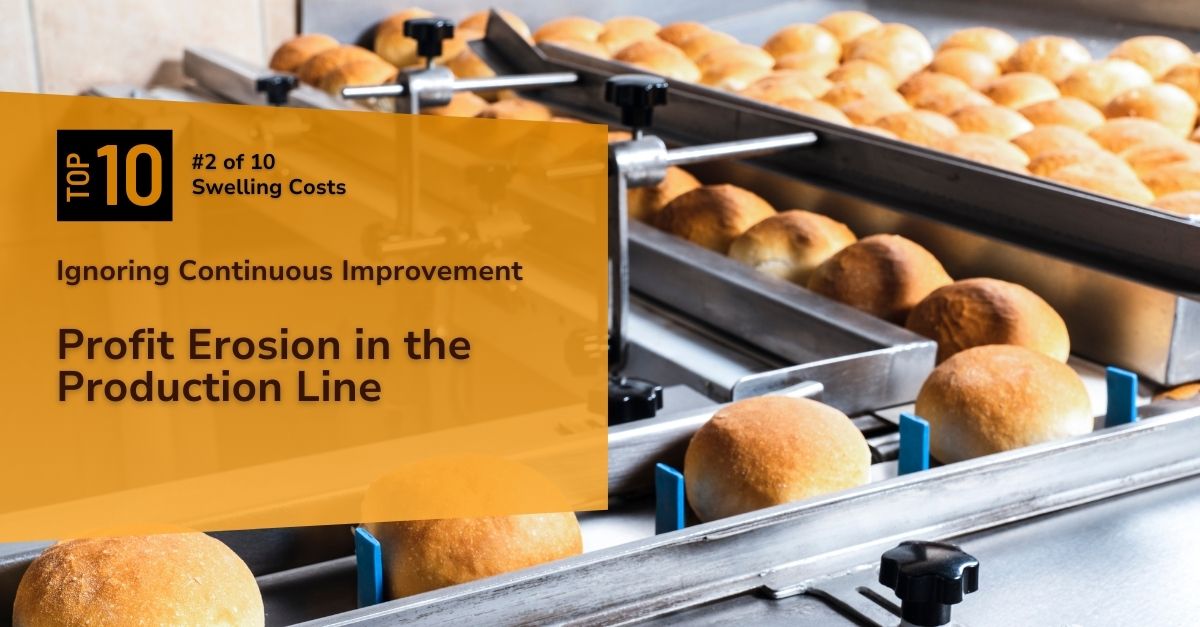
In manufacturing, the decision to ignore continuous improvement isn’t just a missed opportunity; it’s a direct path to escalating costs that erode profit margins and hamper productivity.
When this critical component is neglected, the consequences manifest in various ways, leading to swelling costs that managers on the shop floor face daily.
One less commonly discussed example is the gradual degradation of specialized equipment calibration. Over time, machinery that is not regularly calibrated begins to drift out of specification, leading to a cascade of minor issues. These issues can result in inconsistent production quality, increased material waste, and the need for frequent adjustments by operators. Without a continuous improvement program to monitor and correct these deviations, the cost of material waste alone can skyrocket, not to mention the added labor costs as operators spend more time troubleshooting and less time on productive tasks. This degradation is subtle, often going unnoticed until the cumulative impact has severely inflated costs.
For managers in the manufacturing sector, these overlooked problems can turn into significant financial drains, further complicating efforts to maintain efficiency and profitability on the shop floor. This post will explore the top 10 ways that ignoring continuous improvement leads to swelling costs, focusing on these secondary symptoms that, while less visible, are equally damaging to productivity and the bottom line.
1Increased Frequency of Minor Repairs:
When continuous improvement initiatives are sidelined, the maintenance of equipment often becomes reactive rather than proactive. This leads to an increased frequency of minor repairs that might seem insignificant at first glance. However, these small, recurring issues can quickly add up, consuming valuable time and resources. Managers often find themselves stuck in a cycle of fixing minor issues, leaving little time to address the root cause.
Mitigation Strategy: To mitigate this, it’s essential to implement a predictive maintenance strategy. By leveraging data and analytics to predict when equipment is likely to fail, companies can schedule repairs during planned downtime, reducing the frequency of minor repairs. Additionally, training operators to perform routine checks and simple maintenance can help catch potential issues before they escalate, thus lowering overall repair costs and improving productivity.
2Increased Overtime Due to Inefficient Processes:
Without continuous improvement, inefficiencies in processes remain unaddressed, leading to longer production times and, consequently, increased overtime. Managers may feel pressured to meet production targets, resorting to overtime as a quick fix. This not only inflates labor costs but also wears down employees, leading to burnout and reduced overall efficiency.
Mitigation Strategy: To combat this, companies should regularly review and optimize their production processes. Lean manufacturing techniques, such as value stream mapping, can help identify and eliminate inefficiencies. By streamlining processes, production can be completed within standard working hours, reducing the need for overtime. Moreover, fostering a culture where employees are encouraged to suggest process improvements can lead to innovative solutions that enhance efficiency and reduce costs.
3Unresolved Recurring Issues:
Recurring issues that are not properly addressed can become a significant drain on resources. When continuous improvement is neglected, these problems are often treated as isolated incidents rather than symptoms of a deeper issue. This leads to repeated downtime and repair costs, which could have been avoided with a more proactive approach.
Mitigation Strategy: Root cause analysis (RCA) should be at the core of any continuous improvement initiative. By identifying and addressing the underlying cause of recurring issues, companies can prevent them from reoccurring. Techniques like the Five Whys or Fault Tree Analysis can be particularly effective. Once the root cause is identified, implementing corrective actions and monitoring their effectiveness ensures that the issue is resolved permanently, reducing downtime and associated costs.
4Excessive Spare Parts Inventory:
In the absence of continuous improvement, companies often overcompensate for potential equipment failures by stocking excessive spare parts. This ties up capital in inventory that may not be used for years, if ever. The cost of holding excessive inventory includes not only the purchase price but also storage, insurance, and potential obsolescence.
Mitigation Strategy: Adopting a just-in-time (JIT) inventory system can help mitigate this issue. JIT reduces the need to hold large quantities of spare parts by aligning inventory levels with actual demand. By improving relationships with suppliers and utilizing predictive maintenance, companies can ensure that they have the necessary parts on hand when needed, without the burden of excessive inventory costs.
5Expensive Contract Labor Due to Lack of In-House Expertise:
When continuous improvement is neglected, the skills and expertise of in-house staff can stagnate, leading to an over-reliance on expensive contract labor. This is particularly true for specialized tasks that could have been handled internally with the right training and development programs in place. The cost of hiring external experts is often significantly higher than the cost of training employees to handle these tasks.
Mitigation Strategy: Investing in continuous training and development for in-house staff is key to reducing dependency on contract labor. By building a skilled workforce, companies can handle more tasks internally, leading to cost savings. Additionally, creating a knowledge-sharing culture where experienced employees mentor less experienced ones can help retain critical skills within the organization, reducing the need for external contractors.
6Escalated Material Costs from Poor Inventory Management:
Neglecting continuous improvement often leads to inefficient inventory management, resulting in escalated material costs. Poor planning and forecasting can cause shortages, forcing managers to purchase materials at premium prices to meet production deadlines. Over time, these additional costs erode profit margins.
Mitigation Strategy: Implementing an effective inventory management system, such as Material Requirements Planning (MRP), can help mitigate these costs. MRP systems integrate data from production schedules and inventory levels to optimize material purchasing. This ensures that materials are ordered in the right quantities at the right time, reducing the likelihood of shortages and the need for last-minute, expensive purchases.
7Underutilization of Operator Knowledge:
Operators often have a wealth of knowledge about the equipment and processes they work with daily. However, in a culture that neglects continuous improvement, this knowledge is often underutilized. Failing to tap into this resource can lead to missed opportunities for process improvements and cost savings.
Mitigation Strategy: Creating a culture that encourages operator input in continuous improvement initiatives can unlock significant value. Implementing suggestion programs, holding regular feedback sessions, and involving operators in problem-solving can lead to practical improvements that reduce costs and enhance productivity. Recognizing and rewarding operators for their contributions further reinforces the importance of their input.
8Inconsistent Quality Control Measures:
Inconsistent quality control measures are a common symptom of neglecting continuous improvement. Without a robust system in place, defects and errors can go unnoticed until they result in significant rework or scrap costs. Inconsistent quality not only increases production costs but also affects customer satisfaction and brand reputation.
Mitigation Strategy: To address this, companies should implement a standardized quality management system (QMS) that includes regular audits, training, and continuous monitoring. Tools such as Six Sigma can help identify and eliminate variations in the production process, ensuring consistent quality. Additionally, empowering employees to take ownership of quality at every stage of production can prevent defects from occurring in the first place, reducing the need for costly rework.
9Wasteful Overproduction:
Overproduction is one of the key wastes in manufacturing, and it often occurs when continuous improvement is not prioritized. Producing more than what is needed ties up resources in unsold inventory, leading to increased storage costs and potential write-offs if the products become obsolete.
Mitigation Strategy: Implementing lean manufacturing principles can help reduce overproduction. Techniques such as Kanban and demand-pull production ensure that goods are produced only when there is actual demand. This reduces the risk of excess inventory, lowers storage costs, and frees up resources for other value-adding activities. Continuous monitoring of production schedules and demand forecasts is essential to maintaining balance.
10Overly Complex Procedures:
Without continuous improvement, procedures can become overly complex, leading to inefficiencies and increased costs. Complex procedures often result from layering additional steps over time without reviewing their necessity. This complexity can confuse operators, slow down production, and increase the likelihood of errors.
Mitigation Strategy: Simplifying and standardizing procedures should be a continuous improvement priority. Regularly reviewing and streamlining processes can eliminate unnecessary steps, making procedures more straightforward and efficient. Involving operators in the simplification process ensures that the changes are practical and effective. Simplified procedures not only reduce costs but also improve productivity by enabling operators to work more efficiently.
Conclusion for Manufacturing Leadership
Ignoring continuous improvement in manufacturing isn’t just a decision to maintain the status quo; it’s a decision that invites escalating costs and erodes the very foundation of your operations. As we’ve explored, the consequences manifest not only in obvious ways but also through subtle, secondary symptoms that gradually inflate costs and drain productivity. From the frequent need for minor repairs to the underutilization of operator knowledge, these issues, if left unaddressed, can severely impact your bottom line.
At POWERS, we understand the intricate challenges that manufacturing managers face on the shop floor.
Our proven approach to continuous improvement is designed to tackle these exact issues head-on, driving both immediate and long-term benefits for your organization. We don’t just offer solutions; we partner with you to create a sustainable culture of continuous improvement that aligns with your unique operational needs.
With POWERS, you can expect:
- Reduced Maintenance Costs: By implementing predictive maintenance and root cause analysis, we help you minimize the frequency of repairs and extend equipment life.
- Optimized Labor Efficiency: Our process optimization techniques eliminate inefficiencies, reducing the need for overtime and ensuring that your workforce is focused on value-added activities.
- Streamlined Inventory Management: Through our inventory management solutions, we help you reduce excess inventory and manage materials more effectively, cutting down on unnecessary costs.
- Enhanced Operator Engagement: We empower your operators by integrating their insights into continuous improvement initiatives, leading to practical, impactful changes on the shop floor.
- Consistent Quality Control: By standardizing quality measures and eliminating process variability, we help you maintain high standards of production while reducing waste and rework.
- Simplified Procedures: Our approach to process simplification removes unnecessary complexity, making your operations more efficient and easier to manage.
By partnering with POWERS, you’re not just investing in solutions; you’re investing in a comprehensive strategy that enhances productivity, reduces costs, and drives sustainable growth. Let us help you transform these challenges into opportunities, ensuring your manufacturing operations not only survive but thrive in today’s competitive environment.
- Speak to an Expert: Call +1 678-971-4711 to discuss your specific challenges and goals.
- Email Us: Get tailored insights by emailing info@thepowerscompany.com
- Request an Assessment: Use our online contact form, and one of our expert manufacturing consultants will reach out to schedule an in-depth analysis of your operations.
Continue Reading from this Mastery Series
- Part 1 – When Progress Takes a Break, it Leaves Your Productivity Stalled
- Part 2 – Profit Erosion in the Production Line
- Part 3 – Quality Takes a Dive and Productivity Pays the Price
- Part 4 – When Morale Breaks Down So Does the Shop Floor
- Part 5 – When Innovation Pauses, Your Production Line Follows
- Part 6 – How Customer Loyalty Slips Through Your Fingers
- Part 7 – When Your Slice of the Market Becomes a Crumb
- Part 8 – When Opportunities Slip Through the Cracks
- Part 9 – Safety Shortsights and Their Costly Consequences
- Part 10 – Growth and Adaptation Slows to a Crawl