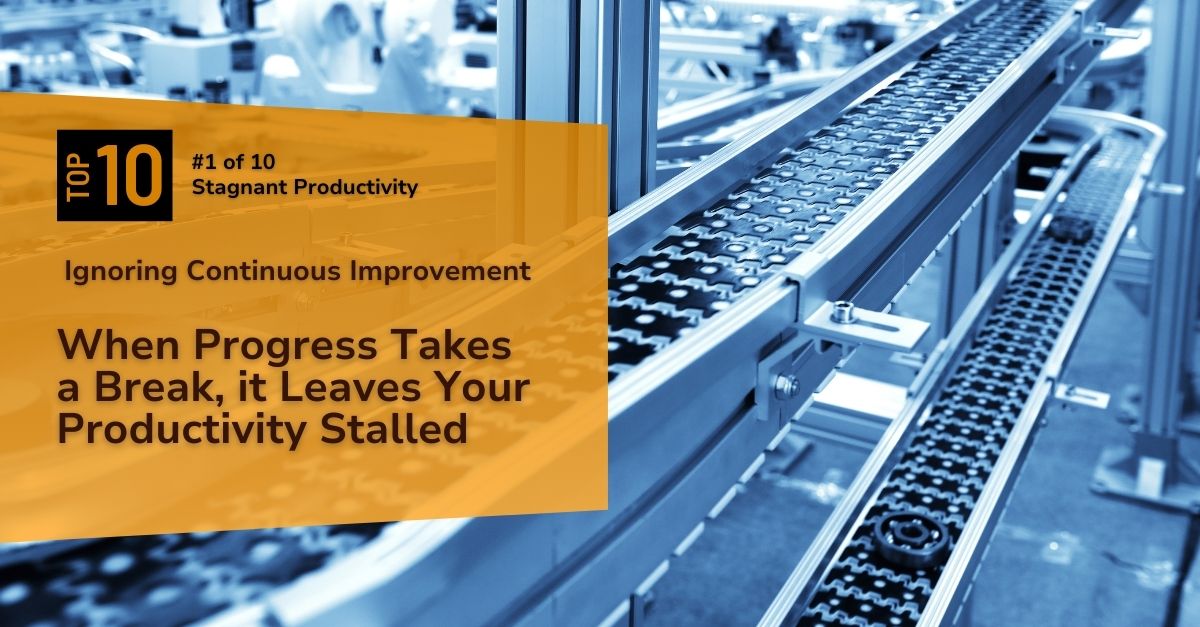
Continuous improvement is a cornerstone of sustained success in the manufacturing industry. When these practices are neglected, the impact on productivity is immediate and profound.
Left unchecked, these symptoms can lead to a cascading effect of inefficiencies, ultimately undermining the entire production process.
One such symptom is the subtle yet pervasive issue of process drift—where, over time, even well-established procedures deviate from their original design. Without the guiding hand of continuous improvement, this drift can go unnoticed until it significantly impacts productivity. For instance, a precision machining operation may experience slight variations in tool wear that, while initially minor, gradually lead to inconsistent product quality. Without regular monitoring and adjustment—a core tenet of continuous improvement—these variations can result in higher scrap rates, increased rework, and extended production cycles. This diminishes productivity, drives up costs, and erodes the company’s competitive edge.
Neglecting continuous improvement in such scenarios doesn’t just stall progress; it actively reverses it. The failure to regularly review and refine processes entrenches inefficiencies, making them more difficult to resolve over time. As these inefficiencies become normalized, they are often accepted as the status quo, further compounding the problem and making it harder to reignite the momentum needed for productivity growth.
Without continuous improvement, manufacturers risk falling behind, not just in output but in their ability to innovate and respond to market demands. The secondary symptoms of stagnant productivity—such as process drift—serve as a warning sign that an organization is losing its edge, signaling the urgent need to re-engage with continuous improvement practices before the damage becomes irreversible.
1Unaddressed Workflow Bottlenecks:
Workflow bottlenecks are a common issue on the shop floor, where delays in one process can cascade into significant productivity losses across the entire operation. When continuous improvement is neglected, these bottlenecks often go unnoticed or unaddressed, leading to a buildup of inefficiencies. Managers may find that tasks that should take minutes are instead taking hours, causing delays that ripple through the production line.
Mitigation Strategy:
To mitigate this issue, regular workflow analysis is essential. Tools like value stream mapping can help identify and address bottlenecks before they escalate. Encouraging a culture of continuous feedback from employees on the shop floor can also bring hidden issues to light, allowing for quicker resolution. By addressing bottlenecks as they arise, organizations can maintain smooth operations and prevent the productivity drain that comes with stagnation.
2Increase in Unplanned Downtime:
Unplanned downtime is a silent killer of productivity. Without continuous improvement practices, the root causes of unplanned downtime—such as equipment failure, lack of preventive maintenance, or process inefficiencies—often remain unaddressed. This can lead to frequent and prolonged interruptions in production, causing significant losses in both time and money.
Mitigation Strategy:
Implementing a robust preventive maintenance program is crucial to reducing unplanned downtime. Predictive analytics can help identify failures before they occur, allowing for timely maintenance. Additionally, training employees to quickly identify and respond to early signs of equipment issues can minimize downtime. By focusing on proactive rather than reactive maintenance, organizations can keep their operations running smoothly and avoid the pitfalls of stagnant productivity.
3Increased Process Variability:
Process variability is a major contributor to inconsistent product quality and inefficiency. Processes drift away from established standards when continuous improvement efforts are sidelined, leading to increased variability. This affects product quality and slows production as employees spend more time correcting errors and reworking products.
Mitigation Strategy:
Standardizing processes and regularly reviewing them for compliance can help reduce variability. Lean methodologies, such as Six Sigma, can be employed to identify and eliminate sources of variability. Continuous training for employees on process standards and the importance of adherence can further reinforce consistency. By maintaining tight control over processes, organizations can ensure that productivity remains high and quality standards are met.
4Plateaued Efficiency Metrics:
When continuous improvement is ignored, efficiency metrics such as cycle time, throughput, and overall equipment effectiveness (OEE) can plateau. This stagnation often goes unnoticed until it starts to impact the bottom line. Managers may struggle to understand why production goals are unmet, leading to frustration and finger-pointing rather than constructive problem-solving.
Mitigation Strategy:
Regularly reviewing and updating efficiency metrics is key to maintaining high productivity. Benchmarking against industry standards and setting ambitious yet achievable goals can motivate teams to push beyond current performance levels. Encouraging a culture of innovation where employees are rewarded for suggesting improvements can also drive efficiency gains. By continuously striving for better performance, organizations can avoid the trap of stagnation and keep productivity on an upward trajectory.
5Unoptimized Equipment Utilization:
Equipment that is underutilized or improperly utilized represents a significant waste of resources. Equipment utilization often goes unchecked without continuous improvement initiatives, leading to inefficiencies that drag down productivity. This can be particularly problematic in capital-intensive industries where equipment downtime or suboptimal performance can majorly impact output.
Mitigation Strategy:
Implementing equipment utilization tracking systems can help identify underutilized assets and areas for improvement. Regularly reviewing equipment performance data and adjusting production schedules or maintenance routines can ensure that all equipment is used to its full potential. Investing in training for operators to fully understand and leverage equipment capabilities can also lead to more efficient use. Optimizing equipment utilization is a critical step in maintaining high productivity levels.
6Diminished Agility in Operations:
Agility is key to staying competitive in a rapidly changing market. However, without a focus on continuous improvement, operations can become rigid and slow to adapt to new demands or challenges. This lack of agility can result in missed opportunities, as the organization is unable to pivot quickly in response to customer needs or market trends.
Mitigation Strategy:
Fostering a culture of continuous improvement encourages flexibility and adaptability in operations. Regular cross-functional meetings to discuss potential improvements and challenges can help teams stay agile. Investing in modular and scalable technologies that can easily be adjusted to meet changing demands is also crucial. Organizations can respond more effectively to market shifts and maintain their productivity by prioritizing agility.
7Increased Complexity in Simple Tasks:
Over time, even the simplest tasks can become overly complex if not regularly reviewed and streamlined. This complexity often arises from outdated procedures, redundant steps, or a lack of standardization. As a result, employees may spend more time navigating these complexities than actually performing productive work.
Mitigation Strategy:
Continuous process improvement involves regularly reviewing and simplifying tasks to remove unnecessary complexity. Implementing standard operating procedures (SOPs) and ensuring they are followed consistently can help maintain simplicity. Encouraging employees to suggest simplifications and providing training on efficient work methods can further reduce complexity. Simplifying tasks not only boosts productivity but also improves employee satisfaction.
8Escalating Maintenance Costs:
When maintenance is treated as an afterthought, costs can quickly spiral out of control. Neglecting continuous improvement in maintenance practices can lead to a reactive approach, where issues are only addressed after they result in equipment failure. This increases maintenance costs and contributes to unplanned downtime and lost productivity.
Mitigation Strategy:
Adopting a proactive maintenance strategy, such as predictive or preventive maintenance, can help control costs and reduce downtime. Regularly reviewing maintenance schedules and practices as part of a continuous improvement program ensures they remain effective and cost-efficient. Training maintenance staff in the latest techniques and technologies can also improve outcomes. Organizations can protect their productivity and profitability by keeping maintenance costs in check.
9Rising Waste and Scrap Rates:
Waste and scrap are often byproducts of inefficiencies in the production process. Without continuous improvement, these inefficiencies can grow, leading to higher rates of waste and scrap. This impacts material costs and reduces overall productivity as resources are diverted to dealing with defective products.
Mitigation Strategy:
Implementing lean manufacturing principles can help reduce waste and scrap by identifying and eliminating inefficiencies in the production process. Regularly reviewing production data and conducting root cause analysis of defects can also help pinpoint areas for improvement. Encouraging a culture of quality, where employees take ownership of their work and strive for zero defects, can further reduce waste and scrap. Reducing waste not only improves productivity but also supports sustainability goals.
10Overreliance on Outdated Practices:
Clinging to outdated practices is a sure way to fall behind in today’s competitive manufacturing environment. When continuous improvement is neglected, there is often a reluctance to adopt new technologies or methodologies, leading to stagnation. This overreliance on outdated practices can hinder productivity as newer, more efficient approaches are overlooked.
Mitigation Strategy:
Building a workplace culture of innovation and continuous learning is key to overcoming this issue. Encouraging employees to stay up-to-date with industry trends and providing opportunities for training and development, especially for critical frontline managers and supervisors, can help ensure that the organization always uses the best practices. Regularly reviewing and updating processes to incorporate new technologies and methodologies can increase productivity. By staying current, organizations can avoid the pitfalls of stagnation and remain competitive in the marketplace.
Conclusion for Manufacturing Operations Leaders
Stagnant productivity is a costly consequence of neglecting continuous improvement in manufacturing. The secondary symptoms—such as unaddressed workflow bottlenecks, increased process variability, and rising waste rates—are not just indicators of inefficiency but warning signs that your operation is on a downward trajectory. These issues can entrench themselves without proactive intervention, making recovery difficult and costly.
At POWERS, we understand the challenges manufacturers face in maintaining high levels of productivity and efficiency.
Our expertise in continuous improvement is designed to help organizations identify and address these secondary symptoms and build a robust framework that drives sustained productivity gains. By partnering with POWERS, your organization can regain its competitive edge and ensure long-term success.
How POWERS Can Help:
- Workflow Optimization: Identify and eliminate bottlenecks to streamline operations and enhance efficiency.
- Preventive Maintenance: Implement proactive strategies to reduce unplanned downtime and extend equipment lifespan.
- Process Standardization: Minimize variability to ensure consistent product quality and operational reliability.
- Waste Reduction: Develop initiatives to lower scrap rates and improve material efficiency.
POWERS can help your organization overcome the stagnation caused by neglecting continuous improvement by focusing on these critical areas. With our hands-on approach, we ensure that the improvements we help you implement are effective and sustainable, providing a measurable return on investment and positioning your organization for continued growth and success.
- Speak to an Expert: Call +1 678-971-4711 to discuss your specific challenges and goals.
- Email Us: Get tailored insights by emailing info@thepowerscompany.com
- Request an Assessment: Use our online contact form, and one of our expert manufacturing consultants will reach out to schedule an in-depth analysis of your operations.
Continue Reading from this Mastery Series
- Part 1 – When Progress Takes a Break, it Leaves Your Productivity Stalled
- Part 2 – Profit Erosion in the Production Line
- Part 3 – Quality Takes a Dive and Productivity Pays the Price
- Part 4 – When Morale Breaks Down So Does the Shop Floor
- Part 5 – When Innovation Pauses, Your Production Line Follows
- Part 6 – How Customer Loyalty Slips Through Your Fingers
- Part 7 – When Your Slice of the Market Becomes a Crumb
- Part 8 – When Opportunities Slip Through the Cracks
- Part 9 – Safety Shortsights and Their Costly Consequences
- Part 10 – Growth and Adaptation Slows to a Crawl