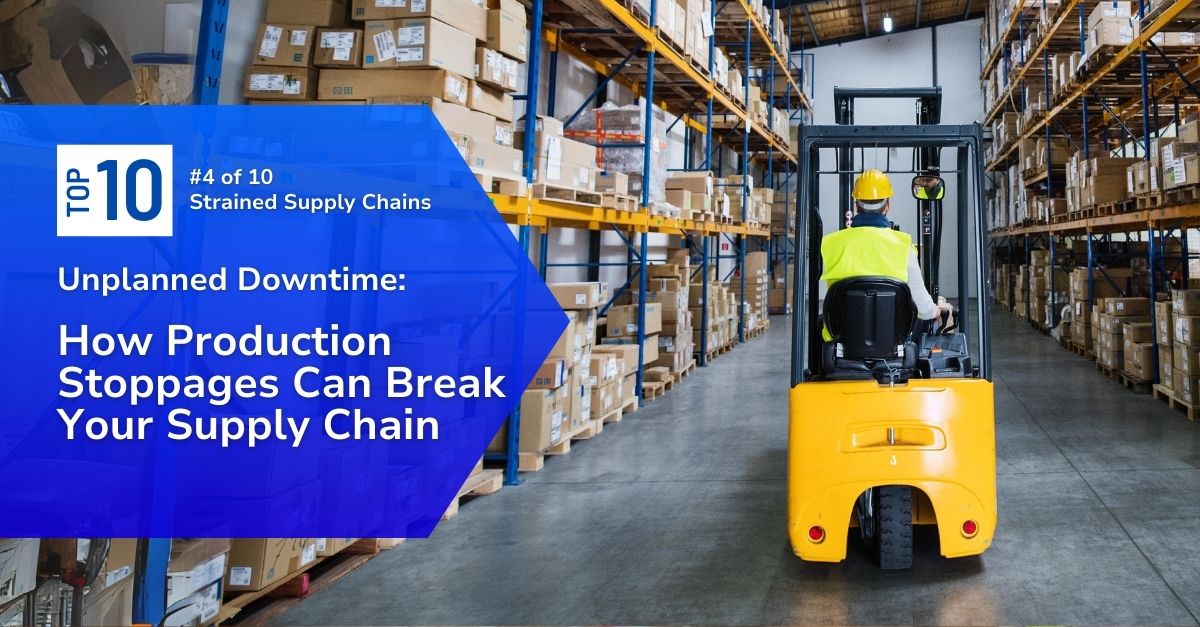
The complexities and dependencies within modern supply chains mean that even a short period of unplanned downtime is a significant disruptor in manufacturing, leading to widespread issues that can cause extensive disruptions, affecting everything from raw material availability to final product delivery.
For instance, consider the impact on specialized components that require precise timing and delivery coordination. If a manufacturer experiences unplanned downtime, the subsequent delay can throw off the entire production schedule, resulting in longer lead times and increased backorders. This can be particularly problematic for manufacturers relying on just-in-time inventory practices, where the margin for error is already slim.
In this fourth installment of our Unplanned Downtime Mastery Series, we explore the top 10 ways unplanned downtime leads to strained supply chains. We’ll focus on the granular issues real managers face on the shop floor, such as increased lead times, difficulty in forecasting demand, erosion of supplier trust, and inventory imbalances across locations. Each point will be thoroughly examined, providing insights into the specific challenges and offering practical mitigation strategies to enhance supply chain resilience and productivity.
1Increased Lead Times:
Unplanned downtime inevitably leads to increased lead times. When production halts unexpectedly, the time required to fulfill orders extends, causing delays across the supply chain. This affects not only the immediate customer but also creates a domino effect that disrupts subsequent production schedules and delivery commitments.
Mitigation: Implementing robust predictive maintenance systems can significantly reduce unplanned downtime. By utilizing sensors and IoT devices to monitor equipment health, potential issues can be identified and addressed before they cause a breakdown, thus maintaining consistent production schedules and minimizing lead times.
2Difficulty in Forecasting Demand:
Unplanned downtime complicates demand forecasting. When production is inconsistent, historical data becomes less reliable, making it challenging to predict future demand accurately. This inconsistency can lead to either overproduction or underproduction, both of which are detrimental to the supply chain.
Mitigation: Integrating advanced analytics and machine learning algorithms into demand forecasting can help mitigate these challenges. These tools can analyze a wide range of data inputs, including market trends and external factors, to provide more accurate demand forecasts even in the face of production variability.
3Erosion of Supplier Trust and Loyalty:
Frequent unplanned downtime can erode supplier trust and loyalty. Suppliers rely on consistent orders to manage their own production schedules and financial planning. When unplanned downtime disrupts this consistency, suppliers may seek more reliable partners, weakening the supply chain network.
Mitigation: Building strong, transparent relationships with suppliers can help mitigate this issue. Regular communication and sharing of production schedules, coupled with collaborative planning, can foster trust. Additionally, having backup suppliers can ensure continuity even when primary suppliers are affected.
4Inventory Imbalances Across Locations:
Unplanned downtime often results in inventory imbalances across different locations. Some warehouses may experience stockouts while others have excess inventory, leading to inefficiencies and increased costs related to transportation and storage.
Mitigation: Adopting an integrated inventory management system that provides real-time visibility across all locations can help balance inventory levels. This system can facilitate the redistribution of stock as needed and optimize inventory levels, reducing the costs associated with imbalances.
5Complexity in Synchronizing Supply Chain Partners:
The complexity of synchronizing various supply chain partners increases with unplanned downtime. When production schedules are disrupted, coordinating with suppliers, manufacturers, and distributors becomes more challenging, leading to misalignments and inefficiencies.
Mitigation: Leveraging supply chain management software that provides real-time updates and collaborative platforms can enhance synchronization among partners. These tools can help ensure all stakeholders are informed of changes and can adjust their plans accordingly, reducing the complexity of coordination.
6Supplier Dissatisfaction:
Supplier dissatisfaction can stem from the unpredictability caused by unplanned downtime. Suppliers depend on a steady flow of orders, and disruptions can strain their operations, leading to dissatisfaction and strained relationships.
Mitigation: Establishing long-term contracts with clear terms and conditions regarding order volumes and delivery schedules can provide suppliers with the stability they need. Additionally, having contingency plans and maintaining open lines of communication can help manage supplier expectations and satisfaction.
7Increased Transportation Costs:
Unplanned downtime can lead to increased transportation costs as companies rush to meet delayed delivery deadlines. Expedited shipping and frequent rescheduling can drive up costs significantly, impacting the overall profitability of the supply chain.
Mitigation: Optimizing logistics through route planning software and leveraging data analytics can help manage transportation costs effectively. These tools can identify the most cost-efficient routes and modes of transport, even when dealing with disruptions, thereby reducing the financial impact of increased transportation costs.
8Decreased Supplier Reliability:
Unplanned downtime affects supplier reliability, as suppliers may struggle to meet their own commitments when faced with irregular order patterns. This can lead to a vicious cycle of unreliability that disrupts the entire supply chain.
Mitigation: Developing strategic partnerships with key suppliers and involving them in the planning process can enhance reliability. Jointly developed contingency plans and regular performance reviews can ensure that both parties are prepared to handle disruptions more effectively.
9Unplanned Storage Costs for Idle Inventory:
Unplanned downtime often results in idle inventory that incurs additional storage costs. Warehouses may become overstocked with materials and products that cannot be processed, leading to increased storage fees and space utilization issues.
Mitigation: Implementing just-in-time (JIT) inventory practices can reduce the amount of idle inventory. By closely aligning production schedules with demand forecasts, companies can minimize excess stock and the associated storage costs. Additionally, utilizing flexible storage solutions such as third-party logistics providers can offer more cost-effective options.
10Increased Backorders:
Backorders increase when unplanned downtime disrupts production, leading to delays in fulfilling customer orders. This not only affects customer satisfaction but also adds administrative burdens and potential financial penalties.
Mitigation: Enhancing production flexibility through modular manufacturing systems can help mitigate backorders. These systems allow for quicker adjustments to production schedules and can accommodate changes more efficiently, reducing the incidence of backorders. Additionally, maintaining a buffer stock of critical items can help bridge the gap during downtime events.
Conclusion for Manufacturing Leadership
Unplanned downtime poses a substantial challenge to manufacturing operations, significantly straining supply chains and impacting overall productivity. The secondary symptoms—ranging from increased lead times and difficulty in forecasting demand to supplier dissatisfaction and increased transportation costs—highlight the complex and far-reaching consequences of these disruptions.
How POWERS Can Help
At POWERS, we specialize in transforming manufacturing productivity by addressing the root causes of unplanned downtime and its secondary symptoms. Our comprehensive approach includes:- Implementing Predictive Maintenance Systems: Utilizing advanced technologies to monitor equipment health and predict potential failures before they cause downtime.
- Leveraging Advanced Analytics: Employing machine learning and data analytics to improve demand forecasting, ensuring more accurate production planning and inventory management.
- Fostering Strong Supplier Relationships: Building trust and reliability with suppliers through transparent communication, collaborative planning, and strategic partnerships.
- Optimizing Inventory Management: Using integrated inventory management systems to balance stock levels across locations, reducing the costs associated with excess or insufficient inventory.
- Enhancing Logistics and Transportation: Utilizing route planning software and data analytics to manage transportation costs and ensure timely delivery, even in the face of disruptions.
Our tailored solutions and hands-on methodology help manufacturers mitigate the impact of unplanned downtime, leading to improved operational efficiency, enhanced supply chain resilience, and measurable productivity gains. By partnering with POWERS, you can ensure that your manufacturing operations are better equipped to handle disruptions and maintain a competitive edge in today’s dynamic market.
For more insights on how POWERS can help your organization improve productivity and mitigate the effects of unplanned downtime and discover the transformative solutions we offer.
- Speak to an Expert: Call +1 678-971-4711 to discuss your specific challenges and goals.
- Email Us: Get tailored insights by emailing info@thepowerscompany.com
- Request an Assessment: Use our online contact form, and one of our expert manufacturing consultants will reach out to schedule an in-depth analysis of your operations.
Continue Reading from this Mastery Series
- Part 1 – The Financial Burden of Breaking Down
- Part 2 – Eroding Maintenence Leading to Eroding Margins
- Part 3 – How Disrupted Production Leads to Unhappy Customers
- Part 4 –How Production Stoppages Can Break Your Supply Chain
- Part 5 – How Breakdowns Can Lead to Safety Shortcomings
- Part 6 – How Equipment Failures Drain Employee Drive
- Part 7 – How Constant Breakdowns Lead to Spiraling Maintenance Costs
- Part 8 – How Lost Production Time Leads to Lower Competitive Edge
- Part 9 – How Shop Floor Stoppages Lead to Regulatory Pitfalls
- Part 10 – How Missed Production Uptime Means Missed Opportunities