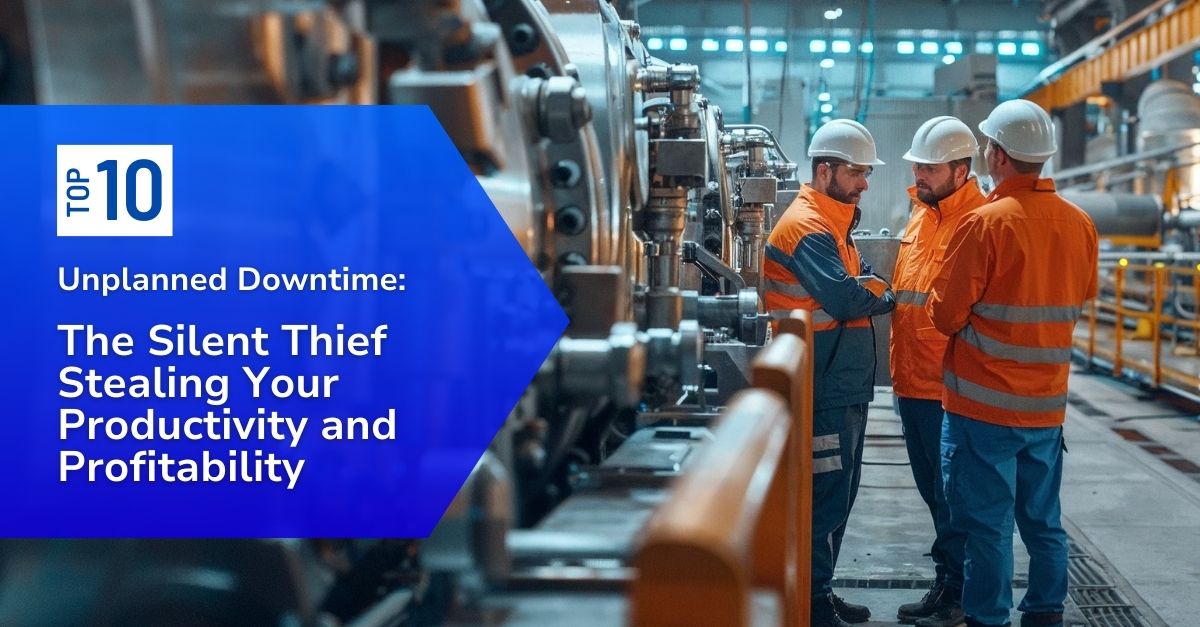
Every component and process in the complex manufacturing ecosystem is meticulously interconnected to maximize efficiency and output.
Yet, even the most well-oiled machines can experience unexpected hiccups. Unplanned downtime, the unscheduled interruption of production, is a pervasive and costly menace that can throw even the most robust operations into disarray.
What Exactly is Unplanned Downtime?
In essence, unplanned downtime refers to any period when production ceases unexpectedly. This could be due to a myriad of factors, ranging from equipment malfunctions and human error to unforeseen supply chain disruptions.
Unlike planned downtime, which is scheduled for maintenance and upgrades, unplanned downtime is a disruptive force that can derail production schedules, strain resources, and compromise your bottom line.
The Staggering Cost of Unplanned Downtime
The financial toll of unplanned downtime is staggering. A study referenced in IIoT World reveals that unplanned downtime can cost a company an astonishing $260,000 per hour.
This figure encompasses the immediate loss of production and the cascading effects that ripple through the entire organization, including wasted labor, delayed shipments, and the cost of expedited repairs. For manufacturers operating on tight margins, these losses can quickly erode profitability and compromise long-term sustainability.
A closer look at the data reveals that unplanned downtime accounts for a significant portion of overall equipment effectiveness (OEE) losses. According to IndustryWeek, unplanned downtime can reduce OEE by as much as 20%, translating to substantially reduced output and revenue.
The Top 10 Consequences of Unplanned Downtime
Unplanned downtime isn’t just a financial drain; it’s a multi-headed hydra that wreaks havoc on various facets of your manufacturing operation. Here are the top 10 consequences, each of which will be explored in greater detail in subsequent articles of the POWERS Mastery Series:
1Financial Loss:
The immediate and most apparent consequence encompassing lost production, labor costs, and potential penalties for missed deadlines.
2Eroded Profit Margins:
The cumulative effect of lost production and increased costs can significantly eat into profit margins, making investing in growth and innovation harder.
3Damaged Customer Relationships:
Delayed deliveries and inconsistent product availability can erode customer trust and loyalty, potentially driving them to competitors.
4Strained Supply Chains:
Unplanned downtime can disrupt the flow of materials and components, causing bottlenecks and delays that ripple through the entire supply chain.
5Increased Safety Risks:
Rushed restarts and shortcuts to compensate for lost time can increase the risk of accidents and injuries.
6Reduced Employee Morale:
Workers may experience frustration and uncertainty when faced with unexpected stoppages, decreasing productivity and engagement, especially with vital frontline supervisors, managers, and operators.
7Increased Maintenance Costs:
Frequent unplanned downtime can strain equipment, leading to accelerated wear and tear and higher maintenance costs.
8Lost Competitive Advantage:
Inability to meet customer demands promptly can erode your competitive edge, allowing rivals to gain market share.
9Regulatory Non-Compliance:
In some industries, unplanned downtime can result in violations of regulatory standards, leading to fines and penalties.
10Missed Opportunities:
The resources consumed in dealing with unplanned downtime could be better invested in growth initiatives, such as new product development or market expansion.
The Path to Prevention
While unplanned downtime poses a significant challenge, it’s not insurmountable. Manufacturers can significantly reduce the frequency and impact of these disruptions by correctly identifying and understanding the root causes, as we covered in our previous Mastery Series, and implementing proactive corrective measures based on real-time data.
In the upcoming articles of the POWERS Mastery Series, we will explore each of these consequences, exploring their nuances and providing actionable solutions for mitigating their impact.
We will also discuss the most common causes of unplanned downtime and outline proven strategies for prevention, including predictive maintenance, robust equipment monitoring, and effective training programs.
Stay tuned for the next post in the POWERS Mastery Series: The Financial Impact of Unplanned Downtime: A Deep Dive into the Numbers.
Don’t let unplanned downtime steal your productivity and profits. Take the first step towards a more resilient and efficient manufacturing operation.
Schedule a free consultation with a POWERS expert to assess your downtime risks and discover how our proven methodologies and cutting-edge technology can help minimize disruptions, optimize production, and achieve sustainable success.
Call +1 678-971-4711 to discuss your specific challenges and goals. Email us at info@thepowerscompany.com. Or, use our online contact form and one of our expert manufacturing consultants will contact you to schedule an in-depth analysis of your operations.
Your path to mitigating unplanned downtime starts here.