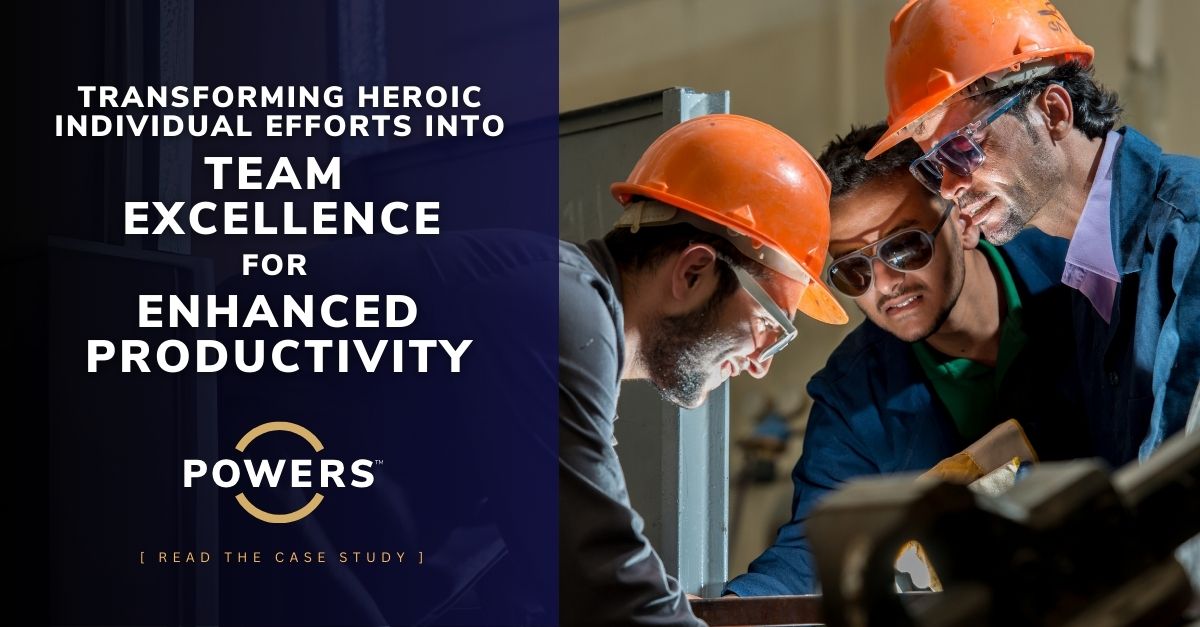
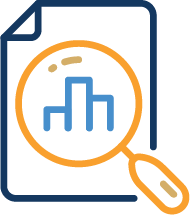
Project Overview
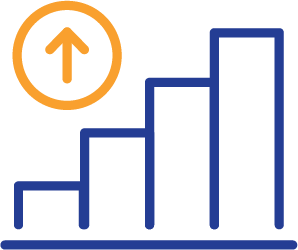
Performance Results
Our Story Begins
One of the largest food processors in the United States, a company that has not only grown remarkably but also achieved significant success over its storied history, faced a major challenge: maximizing operational capacity while struggling with excessive, unpredictable equipment downtime.
Their previous attempts to address this drag on productivity involved focusing on increasing the technical skills of their internal maintenance team and hiring experienced ‘outside contractor’ technicians when deemed necessary. This strategy ultimately proved ineffective. The internal maintenance team did, however, possess highly valuable pockets of tribal knowledge of critical machines but remained trapped in a reactive response cycle to equipment breakdowns.
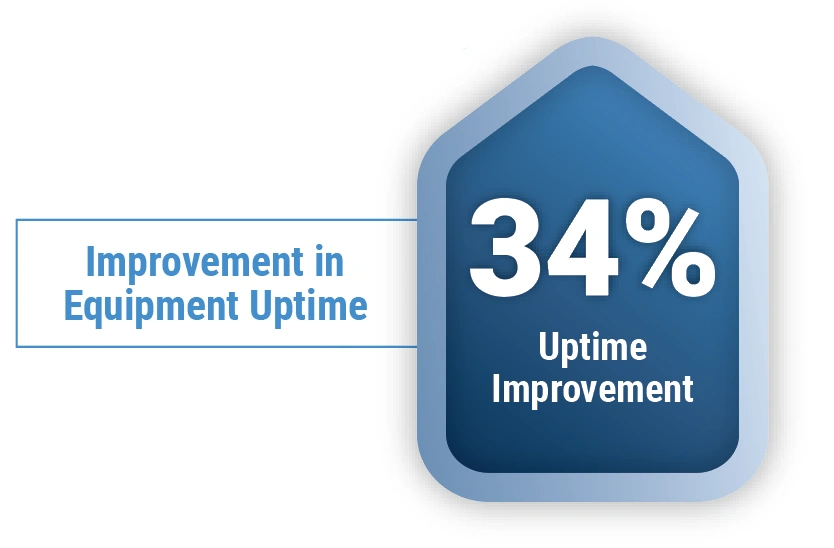
The company had grown so dependent upon these few highly skilled individuals for emergency responses to equipment failures that leadership began to recognize and reward this reactive ‘firefighting’ behavior, a practice that was in need of a strategic shift.
At this point, POWERS was engaged to help develop and implement a Maintenance Management Operating System focused on executing preventative and predictive equipment maintenance to improve reliability and uptime and increase operational capacity.
The Origin of ‘Superhero’ Joe the Mechanic
After we worked closely and daily alongside the maintenance team, it was apparent that a single technician stood out—Joe.
Joe was highly knowledgeable and skilled at quickly troubleshooting, correctly identifying sources, and creating solutions for equipment breakdowns.
Joe would do this better than technicians with 20+ years of service at the company. Joe’s ability to get machines up and running made him the gold standard from senior management, who commented, “Wish everyone was like Joe!”
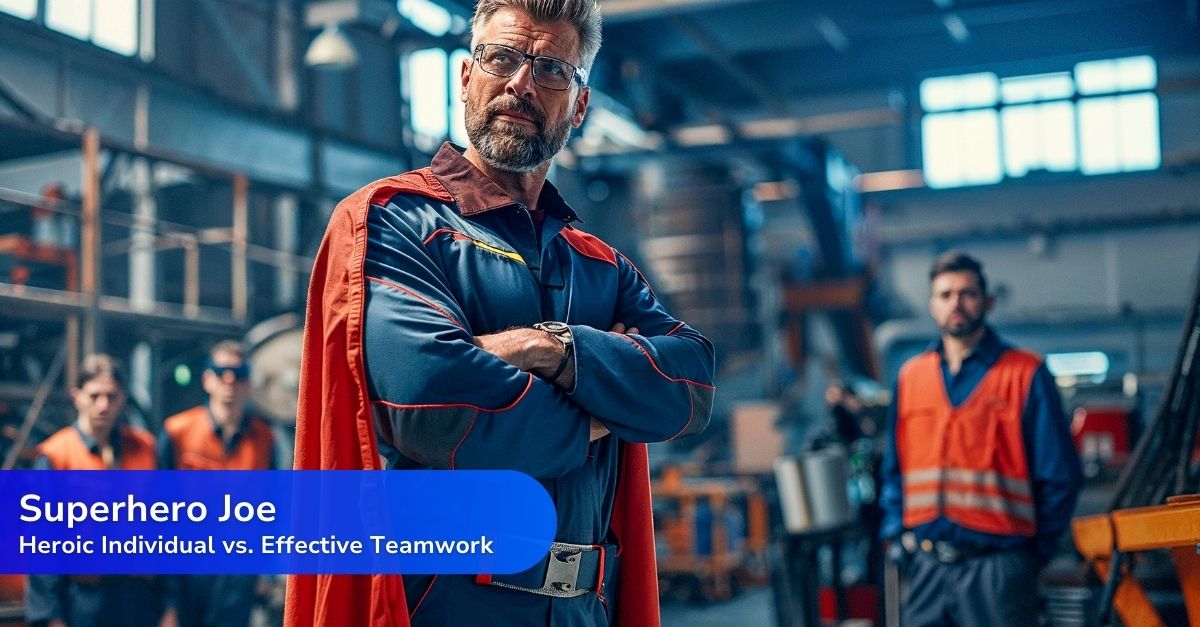
Read the Full Case Study Here
It was not uncommon for the Production team to praise Joe’s support and capabilities while blaming the rest of the department for machine failures and the lack of production associated with downtime.
It was time to find out what gave Joe his superpowers.
On a Monday, during one of the regular daily production update meetings, Joe came up in the discussion. Joe had been called in ‘again’ over the weekend (during his time off) to get a production line up and running.
Production leadership mentioned that the line was down for a few hours, and part of it was due to delays in contacting Joe and getting him in to ‘fix’ the equipment.
It turns out that calling Joe to come in during his time off was a regular occurrence. This maintenance ‘solution’ would happen as part of the regular work ‘plan,’ no matter the scope of the maintenance emergency or when it occurred. Constantly being called in to fix everyone’s problems earned Joe the title of ‘Superhero’ within the organization.
Joe’s reputation had permeated throughout the entire company to the point that when corporate executives and leadership visited the facility, they wanted to make sure they personally connected with Joe and recognized him for his superhero abilities and response.
However, this recognition also inadvertently created a culture of dependency on Joe, where other team members felt less responsible for their own roles in maintenance.
Joe loved the reputation and recognition he had gained, and like any great superhero, he had a direct hotline to the company’s top leadership.
Joe’s Superpowers Revealed!
Sitting down with Joe gave our team insight into why he was so good at his job and committed to doing it well. Joe explained that when he first joined the company, he had a fellow senior maintenance mechanic who took him under his wing and taught him all of the experience and knowledge he had gained over 25 years.
Joe’s new mentor had ‘seen it all’ as equipment and processes evolved during his tenure. He had learned new equipment as it came online. He engaged with OEMs when they visited the plant. He took every opportunity to educate himself and improve his skill set and knowledge whenever possible.
This mentor was the wellspring of Joe’s incredible wealth of knowledge, a fact that no one knew about or had ever bothered to question.
So, Who or What Was the Arch Nemesis to Improvement?
That insight led POWERS to examine how the maintenance department hired and onboarded new technicians. What we found, and it was alarming, was that the process was missing any formal or structured onboarding program for new maintenance hires. New team members were told to ‘do their best’ and to ask other techs for assistance when needed.
The Maintenance Manager stated, “We hired them because they have experience, so they should be able to do the job. If they can’t, we will find someone else. We don’t have time to babysit!”
This approach, while seemingly efficient, led to a lack of understanding and coordination among the maintenance team, hindering their ability to work together effectively.
This unsupportive, undirected leadership style drove a culture of separation between leadership and the mechanics and between Production (internal customers) and the entire Maintenance team.
The discussion between the Production and Maintenance teams was tenuous and even adversarial, with each blaming the other for the cause.
Maintenance would complain that the operators were untrained, causing excessive downtime due to their lack of knowledge of running equipment properly.
Production would blame Maintenance for not implementing proper preventative measures to ensure the equipment ran properly and did not require operator intervention outside their everyday responsibilities.
The discussion failed to uncover any root cause or create any corrective actions to improve the situation.
The Plot Thickens!
After the discussion, the data on preventative and predictive work completion history was reviewed. It was abundantly clear that a vicious self-perpetuating cycle of emergency work was taking resources away from performing preventative work. This cycle not only increased the risk of equipment failure but also reduced the overall productivity of the company.
The resulting equipment unreliability drove increased production schedules and took what few ‘windows’ of opportunity away from maintenance to gain access to the equipment.
Upon reviewing the PM data, it was discovered that Joe had the worst PM work completion percentage assigned to him within the maintenance department.
Never once had anyone approached him or discussed his failure to complete the preventative and predictive work assigned to him while other team members had been disciplined for that exact performance issue.
The answer was simple: Why would Joe focus on preventive and predictive maintenance when he was widely recognized and rewarded for being the downtime ‘Superhero?’
Or at least that was the message he was receiving and being reinforced by leadership all the way to the top! His reputation and recognition kept him committed to maintaining this position of need and dependency but ignored the most critical metric: uptime.
The ‘Aha’ Moment Lightbulb Goes On for Leadership
After getting perspectives from several partners, significant actions were facilitated for improvement, demonstrating the company’s commitment to change and improvement.
Leadership was made aware of their misguided and misdirected recognition and the behaviors that resulted from it, which went totally against their aim. They wanted preventative and predictive work to be executed to improve run time on equipment that they desperately needed to gain capacity for growing customer demand.
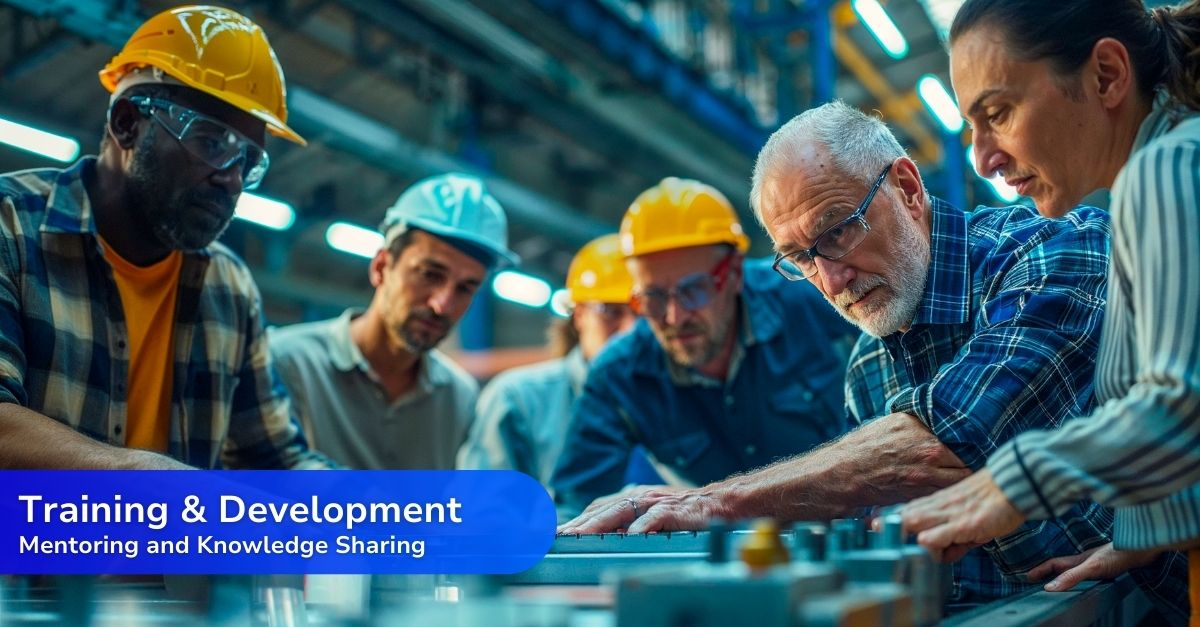
They were taken back and really had an ‘aha’ moment. They began to understand the importance and impact of reinforcing and rewarding the ‘right’ behaviors from their teams across the organization, all the way to the shop floor.
Joe’s vast knowledge and experience were transformed from ‘tribal knowledge’ to documented operating procedures, work instructions, training documents, and processes. This evolution of Joe’s role required effective communication from leadership and an emphasis on Joe’s continued and significant importance to the company.
Joe was still a ‘Superhero’ but with a different calling. He became the ‘Superhero’ of knowledge, working with the entire maintenance team to collect the information required to develop more effective preventative and predictive maintenance programs. He was an ‘insider’ and was able to bridge the cultural gap between frontline mechanics, operators, and leadership—the maintenance ambassador, so to speak.
Super Results That Speak for Themselves
Within three months, equipment uptime and reliability had improved by over 34%, allowing the facility to reduce production hours and providing the maintenance team with the planned and scheduled equipment access they needed to complete their preventative and predictive work.
Daily communications between Production (internal customers) and Maintenance began to focus on coordinated events for the plant’s overall success.
This new-found direction included providing machine operator training to assist in keeping equipment running correctly and to clearly understand when and where responsibilities shifted from Production to Maintenance.
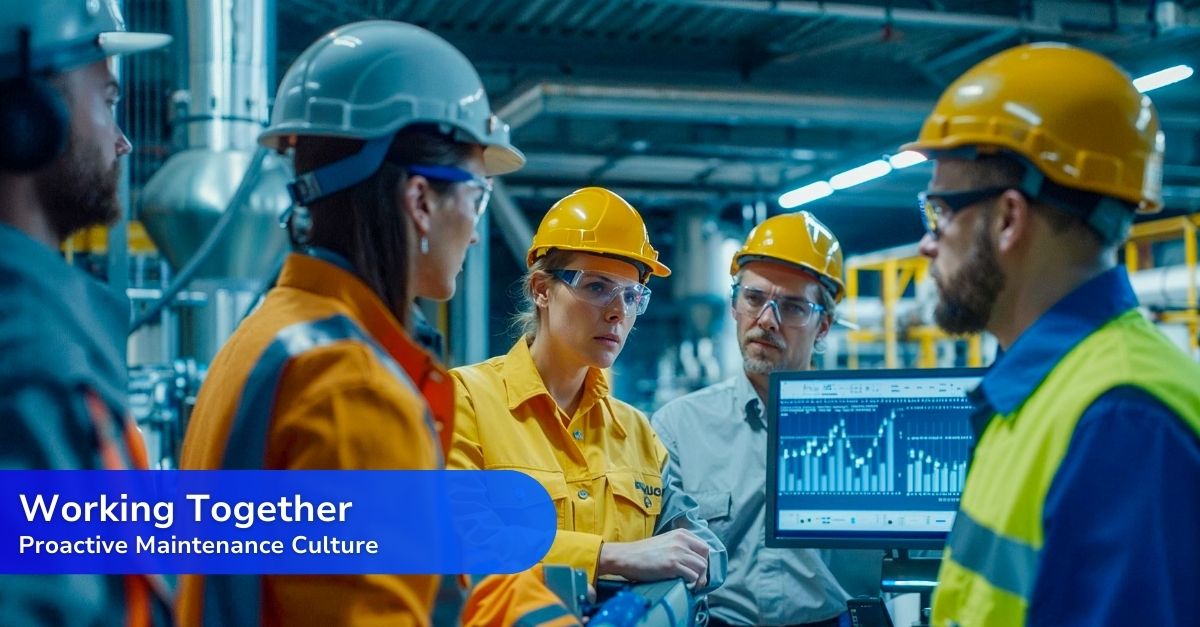
And What Became of Superhero Joe?
Joe was still a Superhero and recognized for his ‘super’ efforts in improving the plant’s performance and the resulting increased teamwork. He became the first point of contact when new maintenance team members were brought on board to ensure an accurate identification of their skills and training requirements.
In the end, Joe was offered a leadership role for his accomplishments, which he humbly turned down. For Joe, “My importance to this company is as a ‘doer,’ and besides, I am having way too much fun to give it up!” He added, “I always liked getting my hands dirty, and the leaders still listen to me!”
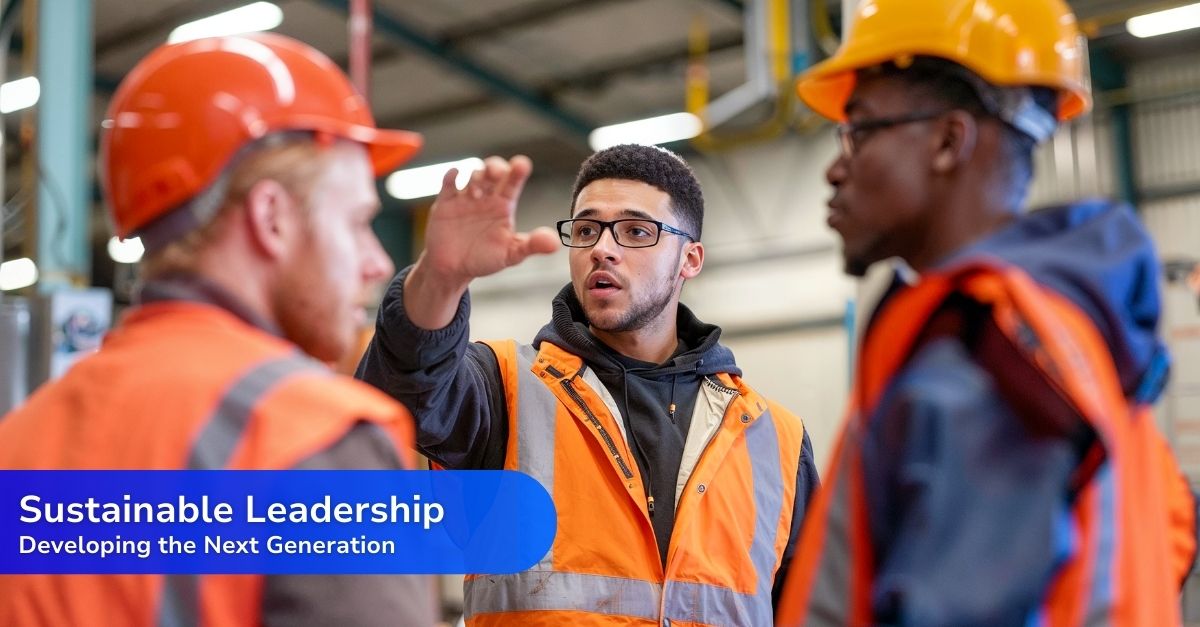