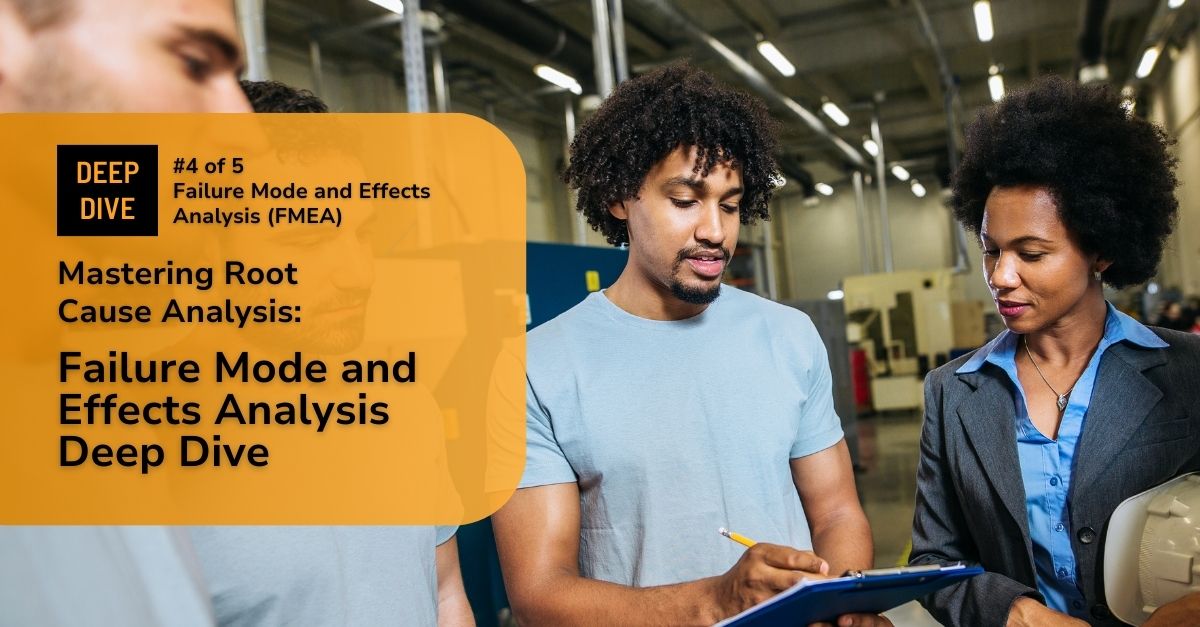
Proactively Identifying and Mitigating Potential Failures is crucial for maintaining operational efficiency and product quality.
Root Cause Analysis (RCA) tools play a vital role in this proactive approach, with Failure Mode and Effects Analysis (FMEA) being one of the most effective methods. FMEA (Failure Mode and Effects Analysis) is a proactive, structured process evaluation approach. Its purpose is to identify potential failure points, understand how they could occur, and assess the impact of each failure. This enables organizations to prioritize risk mitigation strategies and improve process reliability.
Due to its complex processes, stringent quality requirements, and high-stakes outputs, the manufacturing industry is particularly susceptible to failure’s consequences. Therefore, robust risk management practices like FMEA are essential to staying competitive and minimizing disruptions.
What is Failure Mode and Effects Analysis (FMEA)?
Failure Mode and Effects Analysis (FMEA) is a structured approach used to identify potential failure modes within a system, product, or process and to analyze the effects and causes of these failures. Originally developed by the U.S. military in the 1940s, FMEA has since been adopted across various industries, including automotive, aerospace, and manufacturing. The key principles of FMEA involve systematically assessing potential failures and their impacts and prioritizing them based on their severity, occurrence, and detectability.
There are several types of FMEA:
- Design FMEA (DFMEA): Focuses on potential failures in product design before the product is manufactured.
- Process FMEA (PFMEA): Concentrates on potential failures in manufacturing and assembly processes.
- System FMEA: Analyzes potential failures in complex systems, integrating both design and process perspectives.
Each type of FMEA serves a unique purpose, yet they all share the common goal of enhancing reliability and safety by anticipating and mitigating risks.
Why Use FMEA in Manufacturing?
Using FMEA in manufacturing brings numerous benefits that contribute to both short-term and long-term success:
- Proactive Failure Identification: By identifying potential failures before they occur, manufacturers can prevent costly downtime and product defects, ensuring smoother operations and higher customer satisfaction.
- Risk Assessment and Prioritization: FMEA helps prioritize risks based on their potential impact, ensuring that the most critical issues are addressed first. This strategic focus allows resources to be allocated effectively.
- Enhanced Product Quality and Reliability: Implementing FMEA leads to higher quality products and more reliable processes. By systematically addressing potential failures, manufacturers can enhance the durability and performance of their products.
- Cost Savings: By addressing potential failures early, manufacturers can save on costs associated with recalls, repairs, and warranty claims. Proactive risk management reduces the likelihood of expensive corrective actions later.
- Regulatory Compliance: Many industries require rigorous risk assessment and management practices. Implementing FMEA can help manufacturers meet regulatory standards and avoid non-compliance penalties.
The FMEA Process
The FMEA process involves several critical steps that ensure comprehensive risk assessment and mitigation:
Step 1Identify Failure Modes
Failure modes are the various ways in which a process or product can fail. Identifying these modes involves brainstorming sessions, historical data analysis, and expert input. Teams should consider every possible way a component, system, or process could fail, no matter how unlikely it might seem. Techniques like brainstorming, fishbone diagrams, and checklists can aid in this process.
Step 2Determine the Effects of Failures
Once failure modes are identified, the next step is to assess their impact. This involves determining the potential effects on the process, product, and end-user and categorizing the severity of these effects. The severity rating is typically assigned on a scale from 1 to 10, with 10 representing the most severe impact. It’s essential to consider both immediate and long-term effects on product performance, safety, and customer satisfaction.
Step 3Analyze Causes of Failures
Investigating the root causes of each failure mode is crucial. This step involves using tools like fishbone diagrams, 5 Whys analysis, and brainstorming to identify the underlying causes. Understanding why a failure might occur helps in developing effective mitigation strategies. Teams should explore all potential causes, including human error, material defects, process variability, and environmental factors.
Step 4Prioritize Risks
Risks are prioritized using the Risk Priority Number (RPN), which is calculated by multiplying the severity, occurrence, and detectability scores of each failure mode. The occurrence rating assesses how likely a failure is to happen, while the detectability rating evaluates how likely it is that the failure will be detected before it causes significant harm. By focusing on high-RPN issues, teams can address the most critical risks first. The formula for RPN is: RPN=Severity×Occurrence×Detectability.
Step 5Develop and Implement Mitigation Actions
Mitigation actions are developed to address the prioritized risks. This includes creating action plans, assigning responsibilities, and implementing the necessary changes to reduce or eliminate the risks. Effective actions might involve design modifications, process changes, additional inspections, or improved training. It’s important to document these actions and track their implementation to ensure accountability.
Step 6Review and Update FMEA
FMEA should be a living document, continuously reviewed and updated based on new data, feedback, and changes in the process or product. Regular reviews ensure that the FMEA remains relevant and effective. Changes in design, process improvements, new failure data, and customer feedback should all trigger a review of the FMEA. This continuous improvement loop helps maintain high standards and adapt to evolving conditions.
FMEA in Practice: Case Studies
Example 1Improving a Manufacturing Process Using FMEA
A manufacturing company used FMEA to identify potential failure modes in their assembly line. They discovered that certain components were prone to misalignment during assembly, leading to frequent defects. By analyzing the causes and effects of these failures, they implemented changes that reduced downtime by 30% and improved product quality. Specific actions included redesigning fixtures, implementing more precise alignment tools, and enhancing worker training.
Example 2Product Design Enhancement Through FMEA
A product design team used FMEA to evaluate a new product. They identified potential failure modes related to material fatigue and stress. By addressing these issues early in the design phase, they enhanced the product’s durability and performance, leading to higher customer satisfaction. The team conducted stress tests, selected more robust materials, and redesigned critical components to withstand higher loads and repeated use.
Example 3FMEA in Automotive Manufacturing
An automotive manufacturer applied FMEA to their braking system design. They identified potential failure modes such as brake pad wear, hydraulic leaks, and sensor malfunctions. By addressing these risks through improved materials, better sealing techniques, and redundant sensors, they enhanced the safety and reliability of their vehicles. This proactive approach also reduced warranty claims and boosted customer confidence.
Common Challenges and Solutions
- Overcoming Resistance to FMEA Implementation: Implementing FMEA can face resistance from employees who may view it as additional work or unnecessary. To overcome this, it is essential to communicate the benefits and provide training to ensure everyone understands the process and its importance. Highlighting success stories and involving employees in the process can foster buy-in and collaboration.
- Ensuring Comprehensive Failure Mode Identification: To ensure all potential failures are identified, cross-functional teams are involved, and historical data and expert input are used. Encourage open communication and a no-blame culture to capture insights from all stakeholders. Regularly updating checklists and leveraging lessons learned from past projects can also enhance the thoroughness of failure mode identification.
- Maintaining FMEA as a Living Document: Regularly review and update the FMEA based on new information and changes in the process or product. This ensures it remains effective and relevant. Establishing a schedule for periodic reviews and incorporating FMEA updates into change management processes can help maintain its accuracy.
- Training and Skill Development for Effective FMEA:: Provide ongoing training to employees to develop their skills in FMEA. This helps ensure the process is conducted thoroughly and accurately. Training programs should cover FMEA principles, tools, and techniques, as well as practical case studies. Encouraging certification and continuous learning can enhance the overall capability of the team.
Conclusion for Manufacturing Leadership
FMEA is an invaluable tool for the manufacturing industry, enabling proactive identification and mitigation of potential failures. By adopting FMEA, manufacturers can enhance product quality, improve process reliability, and achieve significant cost savings. Fostering a proactive culture of risk management through FMEA ensures continuous improvement and long-term success.
By integrating FMEA into the overall quality management system, manufacturers can build a resilient and agile.
How POWERS Can Help
At POWERS, we specialize in enhancing manufacturing productivity through tailored, results-based management consulting. Our unique approach, ‘Operationalizing Your Culture,’ aligns organizational culture with behaviors and skills that drive higher productivity and efficiency.
With substantial experience in operations, finance, and human resources, we work directly with leadership to implement effective root cause analysis techniques like FMEA. Our hands-on method ensures sustainable improvements and measurable ROI. Contact us today to see how we can help your organization proactively identify and mitigate risks, ensuring long-term success and operational excellence.
- Speak to an Expert: Call +1 678-971-4711 to discuss your specific challenges and goals.
- Email Us: Get tailored insights by emailing info@thepowerscompany.com
- Request an Assessment: Use our online contact form, and one of our productivity experts will reach out to schedule an in-depth analysis of your operations.
Continue Reading from this Mastery Series
- Part 1 – The 5 Whys Technique Deep Dive
- Part 2 – Utilizing the Fishbone Diagram Deep Dive
- Part 3 – Fault Tree Analysis (FTA) in the Manufacturing Industry
- Part 4 – Failure Mode and Effects Analysis (FMEA) Deep Dive
- Part 5 – Using Pareto Analysis to Uncover Productivity Killers