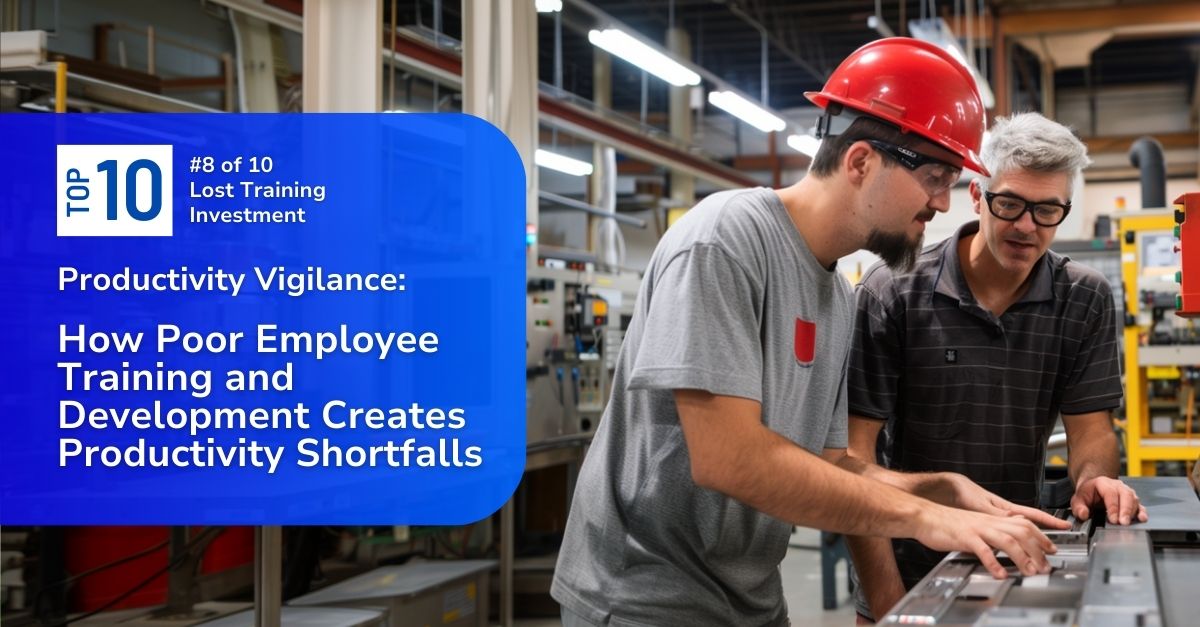
When employee training and development is neglected or ineffective, especially with your frontline leaders, the resulting issues travel throughout the production process.
For instance, consider a scenario where inadequate training leads to improper calibration of advanced machinery. An operator without proper training may not recognize when equipment is out of calibration, leading to subtle but consistent production errors. These errors can go unnoticed until they reach the quality control stage, resulting in a high rate of rejections and rework. This extends production cycles and increases waste and costs, ultimately lowering overall productivity.
Addressing such challenges requires a keen understanding of how lost training investment affects every facet of manufacturing. Longer production cycles are a particularly critical issue, as they delay product delivery, disrupt schedules, and increase labor and operational costs. The following sections will explore ten granular issues stemming from longer production cycles due to lost training investment, offering insights into how experienced managers can tackle these challenges on the shop floor. Each point highlights specific problems and provides actionable mitigation strategies to enhance productivity.
1Improper Handling of Machinery:
Improper handling of machinery is a common issue when training is inadequate or ineffective. Employees who lack proper training might misuse equipment, leading to frequent breakdowns and inefficient production processes. These breakdowns extend production cycles as machinery needs frequent repairs or replacements, significantly slowing down manufacturing operations. This improper handling can also pose safety risks, which further complicate productivity.
Mitigation: To mitigate this, implementing a robust, continuous training program is crucial. Managers should ensure that all employees receive comprehensive machinery operation and maintenance training. Regular refresher courses and practical hands-on sessions can help reinforce proper handling techniques. Additionally, adopting a mentorship system where experienced operators guide new hires can ensure that knowledge is transferred effectively and continuously.
2Higher Frequency of Quality Control Rejections:
Without effective training, employees may not fully understand the quality standards required, leading to a higher frequency of quality control rejections. This issue prolongs production cycles as defective products need to be reworked or discarded, wasting time and resources. The cumulative effect is a slowdown in overall production throughput and an increase in costs.
Mitigation: Addressing this problem involves enhancing quality control training and integrating quality checks into the daily workflow. Managers should focus on detailed training programs emphasizing the importance of quality standards and teaching employees how to identify and prevent defects early in production. Implementing a feedback loop where employees receive immediate feedback on quality issues can also help minimize errors.
3Slower Troubleshooting and Problem Resolution:
Inadequate training often results in employees struggling with troubleshooting and problem resolution. When issues arise on the production floor, untrained staff may take longer to identify and resolve these problems, extending production cycles and causing delays. This slow response affects current productivity and can escalate minor issues into major disruptions.
Mitigation: To improve troubleshooting skills, managers should provide targeted training focused on common issues and effective problem-solving techniques. Encouraging a culture of continuous improvement and learning can also be beneficial. Implementing standard operating procedures (SOPs) for troubleshooting and creating a knowledge base of common problems and solutions can speed up the resolution process and reduce downtime.
4Reduced Experimentation with Process Optimization:
When employees are not properly trained or developed, they are less likely to engage in experimentation with process optimization. Fear of failure or lack of knowledge can deter them from trying new methods or technologies that could enhance productivity. This resistance to change results in stagnant processes that do not evolve or improve, leading to longer production cycles.
Mitigation: Encouraging a culture of experimentation and innovation is key to overcoming this challenge. Managers should provide training that not only covers existing processes but also teaches employees about new technologies and methodologies. Creating a safe environment where employees can test new ideas without fear of repercussions can foster innovation. Recognizing and rewarding successful process improvements can also motivate employees to experiment more freely.
5Difficulty Implementing New Technologies:
The introduction of new technologies can be a significant productivity booster. However, employees may struggle to adopt and effectively use these technologies without proper training. This difficulty can lead to implementation delays and underutilization of new tools, extending production cycles and reducing potential productivity gains.
Mitigation: Comprehensive training programs tailored to the specific technology should be developed to facilitate the smooth implementation of new technologies. Involving employees early in the selection and implementation process can also help in identifying potential challenges and tailoring training to address them. Continuous support and training updates as technologies evolve are essential to ensure sustained productivity improvements.
6Slower Onboarding of New Hires:
The onboarding process for new hires can significantly impact production cycles. When training investments are lacking, onboarding becomes slow and ineffective, leaving new employees ill-prepared to contribute efficiently. This delay in achieving full productivity extends production cycles and places additional strain on existing staff.
Mitigation: Improving the onboarding process requires a structured and comprehensive training program. Managers should develop standardized onboarding procedures covering all the job’s essential aspects. Pairing new hires with experienced mentors can accelerate learning and integration into the team. Regular check-ins and feedback during the initial months can help address any gaps in training and ensure new employees become productive more quickly.
7Longer Production Cycles:
One of the most direct effects of lost training investment is the elongation of production cycles. Employees who are not adequately trained work less efficiently, leading to longer time frames for completing tasks. This inefficiency accumulates across the production process, resulting in delayed deliveries and reduced overall productivity.
Mitigation: To combat this, investing in continuous training and development programs is essential. Managers should conduct regular assessments to identify training needs and gaps. Implementing lean manufacturing principles and focusing on continuous improvement can help streamline processes and reduce production cycle times. Ensuring that employees are cross-trained can also provide flexibility in the production process, enabling quicker responses to changing demands.
8Higher Recruiting and Training Costs:
Lost training investment often results in higher recruiting and training costs. As employees leave due to dissatisfaction or a lack of growth opportunities, recruiting and training new hires becomes more frequent and costly. This revolving door effect extends production cycles as new employees take time to reach full productivity.
Mitigation: Reducing turnover through better training and career development opportunities can mitigate this issue. Managers should focus on creating a positive work environment where employees feel valued and see clear paths for advancement. Offering competitive benefits and continuous learning opportunities can enhance employee retention and reduce the need for constant recruiting and training, thereby maintaining consistent productivity levels.
9Increased Dependence on Temporary and Contractors:
Inadequate training can lead to increased dependence on temporary workers and contractors to fill skill gaps. While this might seem like a quick fix, temporary staff often require additional training and are less familiar with the company’s processes, leading to inefficiencies and longer production cycles.
Mitigation: Investing in the upskilling and reskilling of permanent employees is crucial to reducing reliance on temporary workers. Managers should identify skill gaps and provide targeted training to address them. Building a versatile and well-trained workforce can ensure the company has the necessary in-house skills, reducing the need for temporary solutions and maintaining higher productivity levels.
10Difficulty Justifying Additional Investments in Training and Development:
When the impact of lost training investment is not immediately visible, it can be challenging to justify further investments in training and development. This creates a vicious cycle where the lack of investment leads to longer production cycles and reduced productivity, which in turn makes it harder to argue for the necessary funds for training.
Mitigation: Demonstrating the return on investment (ROI) of training programs can help secure additional funding. Managers should track key performance indicators (KPIs) related to training, such as improvements in production cycle times, quality control pass rates, and employee retention rates. Presenting data-driven evidence of the positive impact of training can make a compelling case for continued and increased investment in employee development.
Conclusion: Breaking the Cycle of Lost Training Investment
The unseen costs of lost training investment can quietly erode a manufacturing operation from the inside out.
Investing in comprehensive, ongoing training programs is not merely an expense but a strategic investment that pays dividends in the form of:
- Reduced Downtime: Skilled workers can quickly troubleshoot and resolve issues, minimizing costly delays and maximizing machine uptime.
- Improved Quality: Well-trained employees understand and adhere to quality standards, reducing defects, rework, and customer complaints.
- Increased Productivity: Confident, knowledgeable workers can optimize processes, experiment with new methods, and readily adapt to new technologies.
How POWERS Can Help
At POWERS, we understand the critical link between training and productivity, especially when it comes to your frontline leadership. Our Productivity Vigilance Mastery Series, of which this post is a part, is designed to equip operations leaders with the tools and strategies they need to identify and address the hidden productivity killers lurking in their operations.
Through our comprehensive approach, we help manufacturers:
- Assess Training & Development Needs: Identify skill gaps and develop targeted training programs that address the specific needs of your workforce.
- Optimize Training Delivery: Implement effective training methods that maximize engagement, knowledge retention, and on-the-job application.
- Measure Training Impact: Track key performance indicators to quantify the impact of training on productivity, quality, and overall operational efficiency.
- Foster a Culture of Continuous Learning: Create an environment where learning is valued and encouraged, enabling your workforce to adapt and grow continually.
By partnering with POWERS, you can break the lost training investment cycle and unlock your workforce’s full potential. Contact us today to learn how we can help you achieve your productivity goals.
- Speak to an Expert: Call +1 678-971-4711 to discuss your specific challenges and goals.
- Email Us: Get tailored insights by emailing info@thepowerscompany.com
- Request an Assessment: Use our online contact form, and one of our expert manufacturing consultants will reach out to schedule an in-depth analysis of your operations.
Remember: The true cost of lost employee training and development investment is not just the money you spend but also the productivity you lose. Invest in your people and their knowledge, and watch your manufacturing operations thrive.
Continue Reading from this Mastery Series
- Part 1 – Without Top Talent, Top Productivity is Elusive
- Part 2 – How Blind Spots in Cost Analysis Hide Your Productivity Struggles
- Part 3 – When Supply Chain Issues Deliver A Productivity Hit
- Part 4 – Environmental Threats that Threaten Your Productivity
- Part 5 – Don’t Let Scaling Up Bring Down Your Productivity
- Part 6 – How Vulnerabilities to Disruptions Undermine Productivity
- Part 7 – Why Ignoring TPM Means Missing Out on Productivity Goals
- Part 8 – How Poor Training and Development Creates Productivity Shortfalls
- Part 9 – How Delayed NPIs Lead to Productivity Misses
- Part 10 – How Inaccurate Data Obscures Productivity Insight