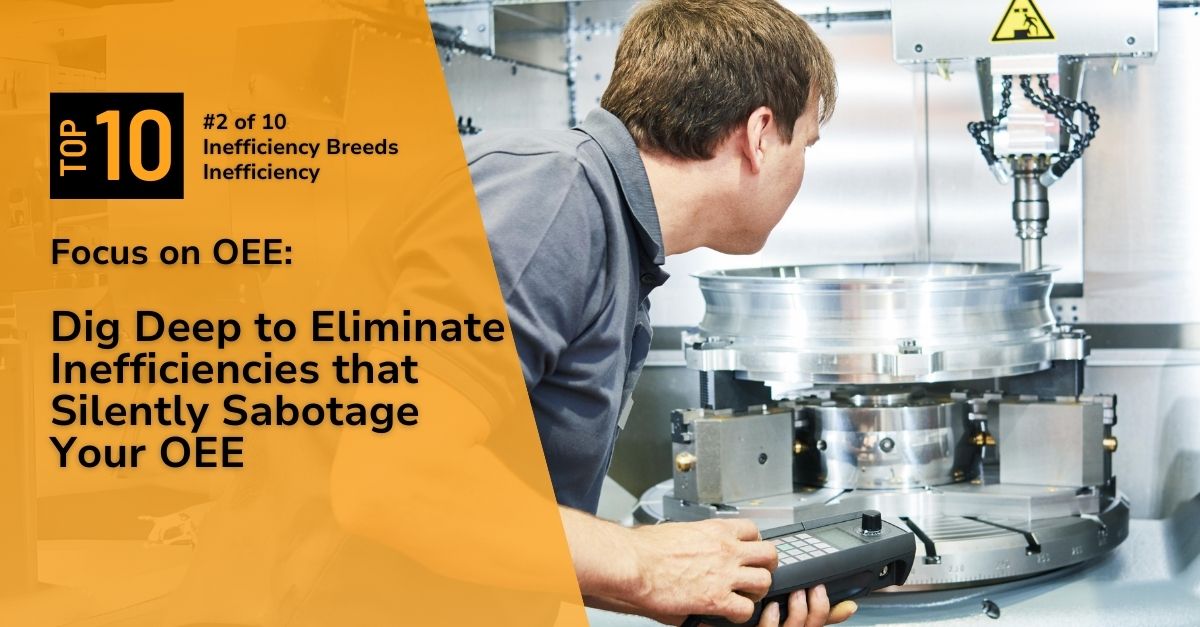
While Overall Equipment Effectiveness (OEE) is a critical metric in the relentless pursuit of manufacturing excellence, it only tells part of the story.
Actual efficiency gains come from ruthlessly exposing and eliminating the secondary symptoms of inefficiency – those small yet compounding detriments to production that can silently erode your OEE over time.
Major equipment breakdowns and lengthy changeovers often grab our attention, but the most insidious threats to OEE can hide beneath the surface. Digging deeper into the secondary symptoms of inefficiency—those small yet compounding detriments to production—is essential for maximizing OEE. If these underlying issues aren’t addressed, any gains in efficiency will be short-lived.
These inefficiencies manifest in inconsistent processes, operator frustration, and unbalanced production lines. They lead to variability in production times and, ultimately, a decline in overall output. Addressing these inefficiencies requires a deep dive into the anatomy of your shop floor and a granular examination of the daily realities that impact your operators and your bottom line.
1Inaccurate Production Scheduling:
Outdated or incomplete SOPs lead to inconsistent processes, rework, quality defects, and operator frustration. This creates variability in your cycle times and reduces your overall output.
Mitigation: Regularly review and update your SOPs, ensuring they reflect your current best practices. Involve operators directly in the creation and revision of SOPs. Train your team thoroughly on new procedures, and make those SOPs easily accessible during production.
2Unnecessary Complexity in Processes:
Overly intricate processes with too many steps or unnecessary bureaucracy create errors, delays, and confusion opportunities. This leads to longer cycle times and increased potential for quality issues.
Mitigation: Employ a critical eye to strip away non-value-added activities and streamline your processes wherever possible. Adopt visual management tools to simplify communication. Use value stream mapping to gain a holistic view of your processes.
3Obsolete or Redundant Equipment:
Aged, failing, or overly complex equipment leads to frequent breakdowns, slow cycle times, and quality problems. Redundant equipment can also occupy valuable floor space and cause unnecessary inventory costs.
Mitigation: Implement a robust preventive maintenance program along with a strategic equipment replacement plan. Consider modern equipment with smaller footprints or multiple capabilities. Conduct regular audits to identify and remove redundant assets.
4Inflexible Scheduling Processes:
Rigid scheduling that doesn’t account for last-minute changes or rush orders leads to production disruptions and inefficient resource use.
Mitigation: Develop a more adaptable scheduling system, possibly utilizing smaller batch sizes. Incorporate forecasting and demand visibility tools to anticipate changes. Build in some planned flexibility to accommodate rush requests.
5Batching Mentality:
Large production batches may seem efficient, but they often lead to excess inventory, longer lead times, and mask quality issues that surface late in the process.
Mitigation: Explore shifting to smaller, more frequent batches, reducing work-in-process inventory, and allowing faster response to customer needs and quality issues. Implement pull-based production systems where possible.
6“Hero” Culture:
A reliance on a few “star” employees to fix problems instead of addressing root causes leads to recurring breakdowns and bottlenecks. It hides process flaws and discourages knowledge sharing.
Mitigation: Standardize troubleshooting procedures and empower all operators with problem-solving skills. Document tribal knowledge and establish mentorship or cross-training programs. Reward preventative action, not just firefighting.
7Skills Mismatch:
Mismatches between required skill sets and those of your workforce lead to quality problems, delays, and frustrated employees. This can be particularly acute with the integration of new equipment.
Mitigation: Implement a skills assessment process for your team, identifying gaps and providing targeted training. Proactively plan your training schedule in alignment with equipment upgrades or process changes.
8Unreliable Suppliers:
This forces downtime, rushed reworking, or dissatisfied customers. Additionally, a lack of trust in your supply chain could lead to “safety stock” practices – ordering more inventory than necessary as insurance against disruptions, tying up capital and warehouse space.
Mitigation: Work on collaborative forecasting to create shared visibility of demand patterns. Consider implementing vendor-managed inventory (VMI) systems where appropriate, giving suppliers direct insight into your consumption patterns to facilitate more proactive replenishment.
9Ineffective Layout Changes:
Frequent layout changes without careful analysis can add travel time for materials and operators, increasing cycle times and creating workflow disconnects. Poorly designed layouts can also increase the risk of accidents or bottlenecks on the shop floor.
Mitigation: Before making changes, use simulation software to model the impact on material flow and throughput. Involve shop floor workers in the layout design process – they have unique perspectives on potential flow improvements. Pay attention to ergonomics and safety in new layouts, ensuring smooth operator interaction with equipment.
10Unbalanced Production Lines:
The Problem: Even if individual stations within a production line are efficient, imbalances between stations create bottlenecks. Slower stations will hold up the entire line, leading to wasted capacity and idle time. This can severely contribute to quality defects as upstream stations rush to keep up with downstream bottlenecks.
Mitigation: Conduct thorough line-balancing studies. Identify the slowest step (your “constraint”) and focus on improving that station’s throughput, whether through equipment upgrades, operator training, or process redesign. Use flexible workers who can be deployed to bottlenecks in real-time to maintain flow.
Conclusions for Senior Operations Leaders
The inefficiencies outlined in this post can seem deceptively minor, yet they exert a relentless drag on your OEE and your profitability. By proactively tackling these ‘secondary symptoms’, you not only boost your current performance and lay a solid foundation for sustained improvements. Addressing these issues is an investment in building a truly efficient, streamlined, and resilient manufacturing operation, ultimately translating to increased profitability and a competitive edge.
This focus will propel your manufacturing operation to new heights of efficiency and productivity.
How POWERS Can Help
At POWERS, we understand the challenges and complexities of achieving and sustaining operational excellence. We’re more than just consultants; we’ll partner with you on your OEE improvement journey. Our integrated approach can help you overcome the inefficiencies that silently chip away at your efficiency. We’ll begin by meticulously analyzing your production lines to pinpoint bottlenecks, identify capacity constraints, and uncover areas where outdated equipment is holding you back.
We’ll deploy powerful data analytics to reveal hidden patterns in your production data, pinpointing the root causes of inefficiency. From there, we’ll work closely with you to develop and implement customized strategies to address your specific challenges, streamline your processes, and elevate your OEE to new levels.
- Call: +1 678-971-4711
- Email: info@thepowerscompany.com
- Form: Request Assesment
Don’t let hidden inefficiencies continue to sabotage your manufacturing operation. Optimize your processes and achieve unprecedented levels of efficiency. Contact POWERS today and discover how our expertise can propel your company’s success.
Continue Reading from this Mastery Series
- Part 1 – The Hidden Costs Undermining Your OEE Score
- Part 2 - Dig Deep to Eliminate Inefficiencies that Silently Sabotage Your OEE
- Part 3 – How Guesswork Kills OEE
- Part 4 – When Nobody Takes Ownership OEE Suffers
- Part 5 – When “Pushing Production” Costs You OEE Points
- Part 6 – The Customer Connection: When Dissatisfaction Drains Your OEE
- Part 7 – Death by a Thousand Cuts: How Wear and Tear Steals From Your OEE
- Part 8 – Competitive Disadvantage: The Hidden Enemy of OEE Excellence
- Part 9 – How Missed Opportunities for Improvement Means Missed OEE Potential
- Part 10 – Is Stagnant Innovation Stagnating Your OEE Results