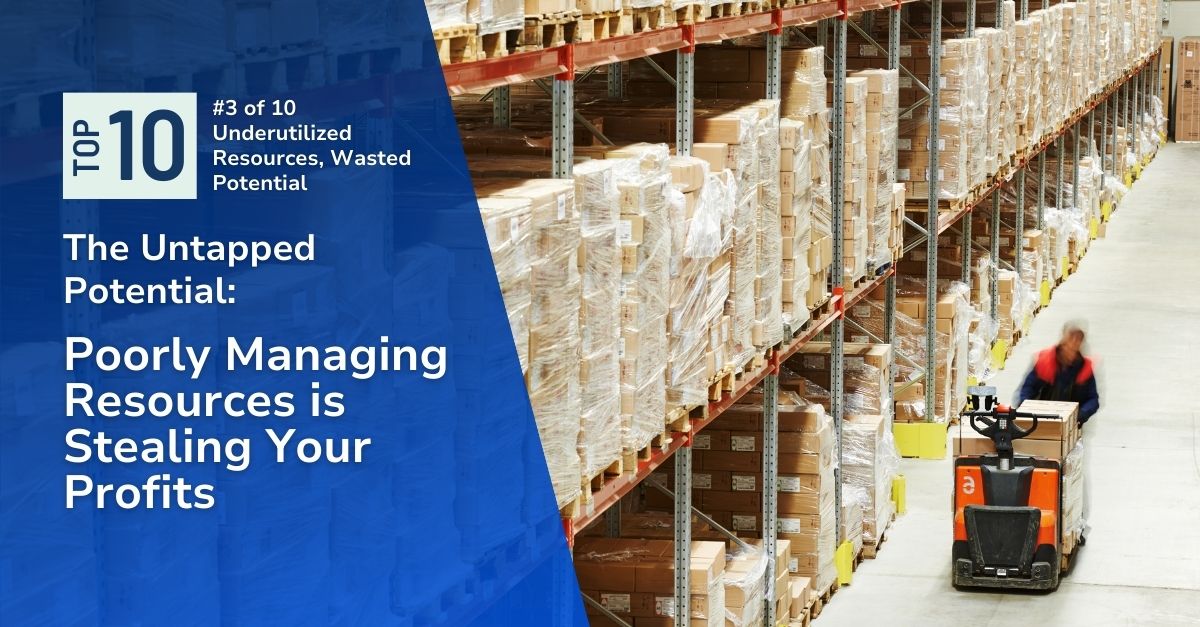
The manufacturing shop floor is a symphony of machines, materials, and human expertise. When each element is in perfect harmony, the result is a masterpiece of efficiency and output.
However, when resources are mismanaged – a core symptom of chronic capacity underutilization – the entire orchestration descends into chaos. Missed deadlines, costly errors, and stressed employees become the norm, eroding profitability and hindering a manufacturer’s ability to thrive in a competitive landscape.
The ripple effect of poorly managed resources like mismatched tools, wasted labor, and insufficient inventory goes far beyond slowing production lines. These issues have the power to sabotage innovation, strain customer relationships, and ultimately leave manufacturers vulnerable to market disruptions.
If you suspect your production processes are falling short of their true potential, you’re likely contending with the fallout of poor resource allocation.
This blog post deeply explores the top ten problems plaguing manufacturers due to inefficient resource management. We’ll dissect the domino effect these problems trigger on the shop floor, hampering day-to-day operations. But more importantly, we’ll provide you with proven strategies and insights to break this cycle. By optimizing your resource allocation, you’ll unlock hidden capacity, drive productivity gains, and position your manufacturing operation for sustained success.
1Difficulty Scaling Production:
Negative Impact: When resources are poorly allocated, manufacturers often lack the flexibility to scale production up or down efficiently. This can lead to missed opportunities during periods of high demand and production bottlenecks during slow periods.
Positive Step: Implement capacity planning strategies that factor in variable lead times, buffer stock levels, and machine capabilities. Conduct regular reviews and adjustments to ensure your production plan reflects current market demands.
2Frequent Tool Changes and Machine Setups:
Negative Impact: Inefficient resource allocation can lead to the wrong tools and equipment being assigned to specific jobs. This necessitates frequent tool changes and machine setups, significantly impacting production speed and overall throughput.
Positive Step: Conduct a thorough analysis of production requirements and ensure the appropriate equipment and tooling are readily available for each job. Implement standardized setups and invest in quick-change tooling systems.
3Inadequate Inventory Buffers:
Negative Impact: Resource mismanagement often leads to a lack of buffer stock, leaving the production line vulnerable to disruptions caused by material shortages, supplier delays, or unexpected equipment failures.
Positive Step: Establish safety stock levels for critical materials based on historical usage data and lead times. Implement collaborative forecasting and planning with suppliers to ensure a smooth flow of materials.
4Expedited Shipping and Rush Orders:
Negative Impact: Poor resource allocation can make it difficult to meet standard lead times, increasing expedited shipping and rush orders. These expedited orders disrupt production schedules and create a ripple effect of delays throughout the manufacturing process.
Positive Step: Improve capacity planning and lead time accuracy. Clearly communicate realistic lead times to customers and offer incentives for early orders.
5Overtime Pay and Burnout:
Negative Impact: When production inefficiencies arise due to poor resource allocation, shop floor employees are often forced to work overtime to meet deadlines. This can lead to employee burnout, decreased morale, and increased absenteeism.
Positive Step: Optimize production processes to reduce reliance on overtime. Cross-train employees to ensure they can effectively cover for absent colleagues. Invest in employee wellness programs to combat burnout.
6Reactive Work Prioritization:
Negative Impact: When resources are stretched thin, planning and prioritizing production tasks is difficult. Instead, manufacturers are forced to react to urgent issues as they arise, leading to a chaotic and inefficient work environment.
Positive Step: Implement a clear and well-defined work prioritization system. Develop a production schedule that factors in buffer times and potential disruptions. Empower shop floor managers to make informed decisions about task prioritization.
7Inconsistent Product Quality:
Negative Impact: Poor resource allocation can lead to inconsistencies in product quality. When employees are rushed or overworked, or when the wrong tools and equipment are used, the risk of errors and defects increases.
Positive Step: Standardize work processes and provide clear work instructions. Invest in operator training and error-proofing techniques. Implement robust quality control measures at every stage of production.
8Difficulty in Accommodating Short-Notice Orders:
Negative Impact: When resources are mismanaged, it becomes nearly impossible to accommodate last-minute orders without severe disruptions to the production schedule. Manufacturers lose the opportunity to secure additional revenue and potentially strain customer relationships.
Positive Step: Analyze historical order patterns to forecast potential short-notice demand. Reserve a certain level of production capacity for unexpected orders. Negotiate flexible lead times with customers where possible.
9Wasted Rework and Scrap:
Negative Impact: Poorly managed resources increase the time and materials wasted on rework and scrap. Rushed production, improper tooling, and inadequate quality control measures can contribute to this.
Positive Step: Implement root cause analysis to identify and address the primary causes of rework and scrap. Invest in operator training and preventative maintenance to reduce the chances of defects.
10Lack of Data Visibility for Decision-Making:
Negative Impact: When manufacturers can’t track key metrics such as machine utilization, labor hours, and inventory levels, making informed decisions about resource allocation becomes impossible. This creates a continuous cycle of inefficiency driven by guesswork rather than data.
Positive Step: Invest in data collection and analytics tools, such as manufacturing execution systems and shop floor dashboards. Implement regular data reviews to guide continuous improvement and strategic resource decisions.
Conclusion
The secondary symptoms of poorly allocated resources may seem like isolated incidents on the shop floor, but in reality, they are interconnected symptoms of a deeper systemic problem. When manufacturers fail to address the root causes of these issues, they continue to pay the price in lost productivity, decreased profits, and reduced competitiveness.
It’s time to break this costly cycle.
Manufacturers unlock a vast wellspring of untapped potential by proactively identifying and addressing the granular inefficiencies caused by resource mismanagement.
This means increased throughput, improved on-time delivery, and a significantly better bottom line.
Your Partner in Transforming Hidden Capacity
At POWERS, we understand the complexities of manufacturing resource allocation. We’ve witnessed the challenges manufacturers face when production capacity is poorly utilized. Our team of experts has decades of experience helping manufacturers optimize their processes, streamline resource management, and achieve breakthrough gains in efficiency.
We offer a range of services tailored to the unique needs of manufacturers, including
- Capacity Analysis and Planning: This is a comprehensive assessment of your current capacity levels, identifying bottlenecks and areas for improvement, such as those related to frequent tool changes, inadequate inventory buffers, and reactive work prioritization.
- Resource Optimization: Strategic recommendations and implementation support to improve resource allocation, scheduling, and flow, including mitigating issues like expediting shipping and rush orders, overtime pay and burnout, and difficulty in accommodating short-notice orders.
- Data Analytics and Visualization: Real-time insights into production performance, empowering data-driven decision-making about resource use, including pinpointing causes of inconsistent product quality and wasted rework and scrap.
If you’re ready to unlock your manufacturing operation’s true potential, we invite you to contact POWERS today. Let’s work together to transform your shop floor into a powerhouse of productivity and profitability.
Optimize your manufacturing processes and achieve unprecedented efficiency. Contact POWERS today to learn how our expertise can drive your company’s success. Let’s start the conversation: +1 678-971-4711 or info@thepowerscompany.com.
Continue Reading from this Mastery Series
- Part 1 – The Price of Lost Revenue and Profit Resulting from Underutilized Capacity
- Part 2 – How Rising Production Costs Hide Your Factory’s True Potential
- Part 3 – Poorly Managing Resources is Stealing Your Profits
- Part 4 – Break the Quality Struggle Cycle to Fix This Shop Floor Frustration
- Part 5 – From Chaos to Capacity: How to Tame Turnover and Optimize Your Operations
- Part 6 – Manufacturing Nightmares: When Your Shop Floor Can’t Keep Up
- Part 7 – When Supply Chain Disruptions Reveal Your True Capacity
- Part 8 – Unlocking Efficiency When Sustainability Meets the Shop Floor
- Part 9 – Understaffed and Underperforming on the Shop Floor
- Part 10 – How Blind Spot Vulnerabilities Impact Your Shop Floor’s Efficiency