Manufacturing Mastery Series
Dive into the heart of operational excellence with our Manufacturing Mastery Series. This collection is designed to unfold the complexities of manufacturing, enhancing systems, processes, and behaviors critical for success.
Operational Agility
A rigid operation can spell disaster for a business. Today, operational agility isn’t optional—it’s the foundation for steering through the twists and turns of the modern business environment. But what does operational agility truly entail? It’s more than just reacting to change; it’s about cultivating a forward-thinking approach, viewing change as a chance to grow, and empowering your organization to tackle challenges with strength and accuracy.
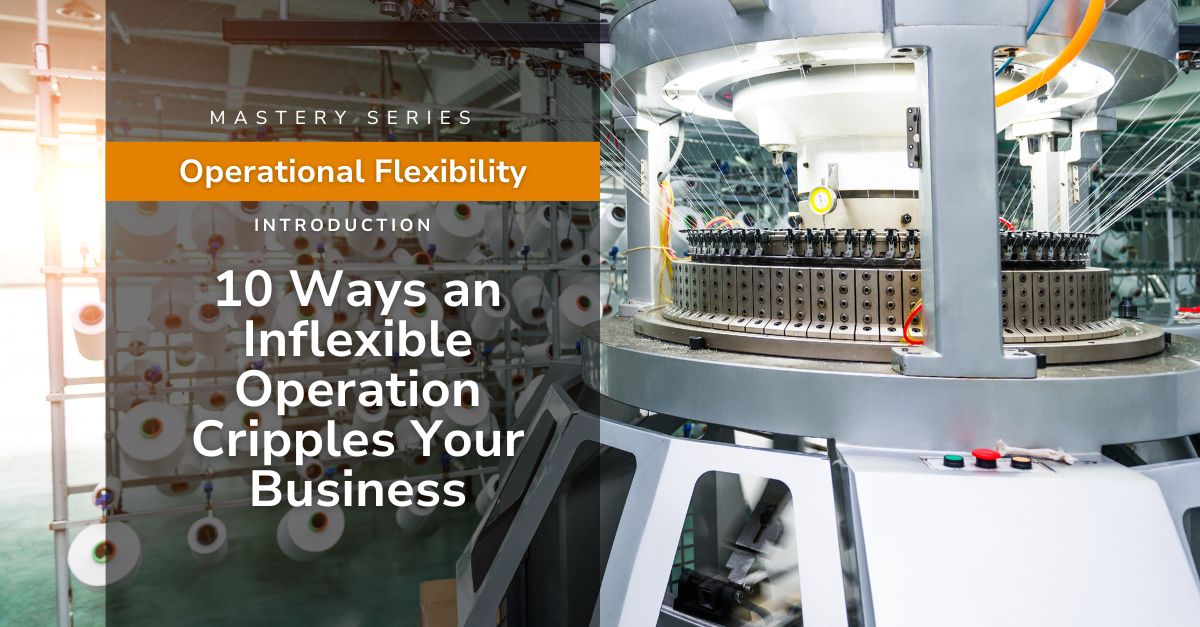
The Risk of Rigidity: 10 Ways an Inflexible Operation Cripples Your Business
- Part 1 – How Stubborn Systems Sabotage Competitive Advantage
- Part 2 – Unadaptable Workflows Lead to Talent Turnover
- Part 3 – Why Inflexible Operations Fail to Innovate
- Part 4 – How Operational Inflexibility Undermines Your Resilience
- Part 5 – When Rigid Operations Cause Decision-Making Bottlenecks
- Part 6 – How Inflexibility Obstructs Collaboration
- Part 7 – How Inflexible Operations Sabotages Scaling Initiatives
- Part 8 – How Inflexible Operations Fuel Resistance to Change
- Part 9 – How Inflexible Operations Leave You Vulnerable to Cyber Threats
- Part 10 – Why Operational Inflexibility Undermines Your Brand Reputation
Cost Reduction
Cost control is the backbone of a thriving manufacturing operation. While major expenses like labor and raw materials often receive careful attention, hidden profit leaks quietly erode profitability and threaten long-term business viability. This Mastery Series dives into these often-overlooked costs, shedding light on subtle drains that undermine financial performance. By identifying and addressing these hidden challenges, manufacturers can optimize efficiency, protect margins, and secure sustainable growth.
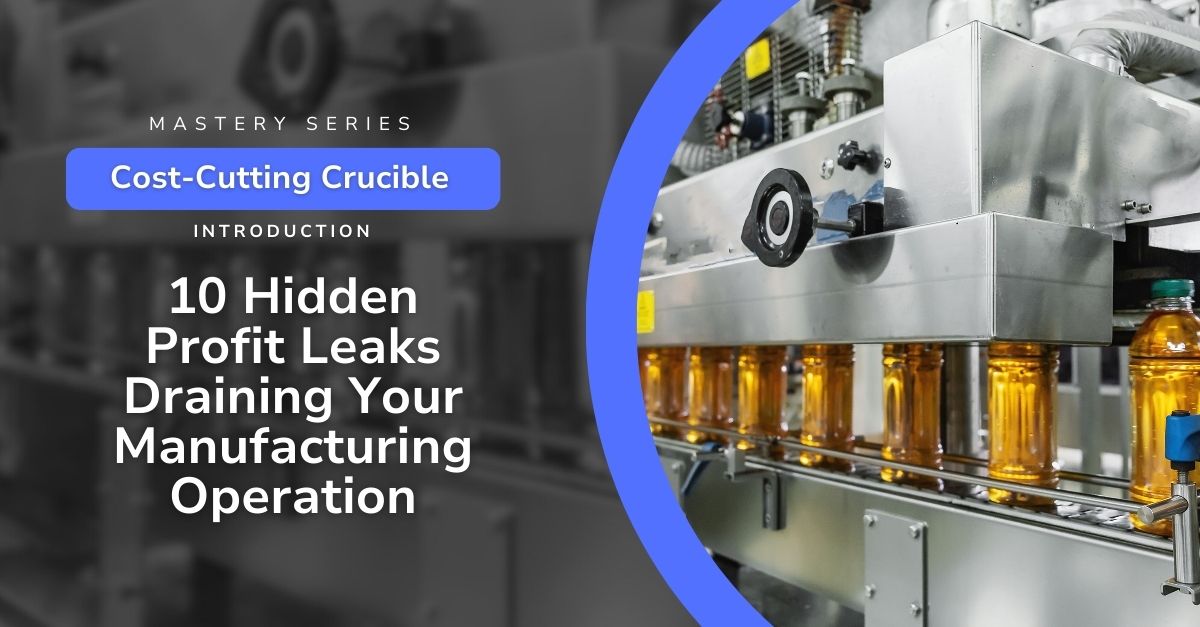
The Cost-Cutting Crucible: 10 Hidden Profit Leaks Draining Your Manufacturing Operation
- Part 1 – How Poor Scheduling Burns Through Your Profit Margins
- Part 2 – How Hidden Energy Wastes Burn Through Your Bottom Line
- Part 3 – How Dead Weight in Your Safety Stock Undermines Your Bottom Line
- Part 4 – The Hidden Costs of Ignoring Preventive Maintenance Programs
- Part 5 – Mismatched Skills and Wasted Workforce Potential
- Part 6 – Poor Quality Control is Dragging Down Your Productivity and Profits
- Part 7 – Being Slow to Market Undermines Your Bottom Line
- Part 8 – Supplier Missteps That Drain Profitability
- Part 9 – The Cost of Continuing to Use Manual Processes
- Part 10 – The Financial Fallout of Fragmented Compliance
Digital Transformation and Industry 4.0
We are now in the era of Industry 4.0, where smart factories, interconnected systems, and data-driven decision-making are reshaping how we design, produce, and deliver goods. For large-scale manufacturers, the time to embrace digital transformation is not in the distant future—it’s now. It’s a mandate for survival and growth in an increasingly competitive global market.
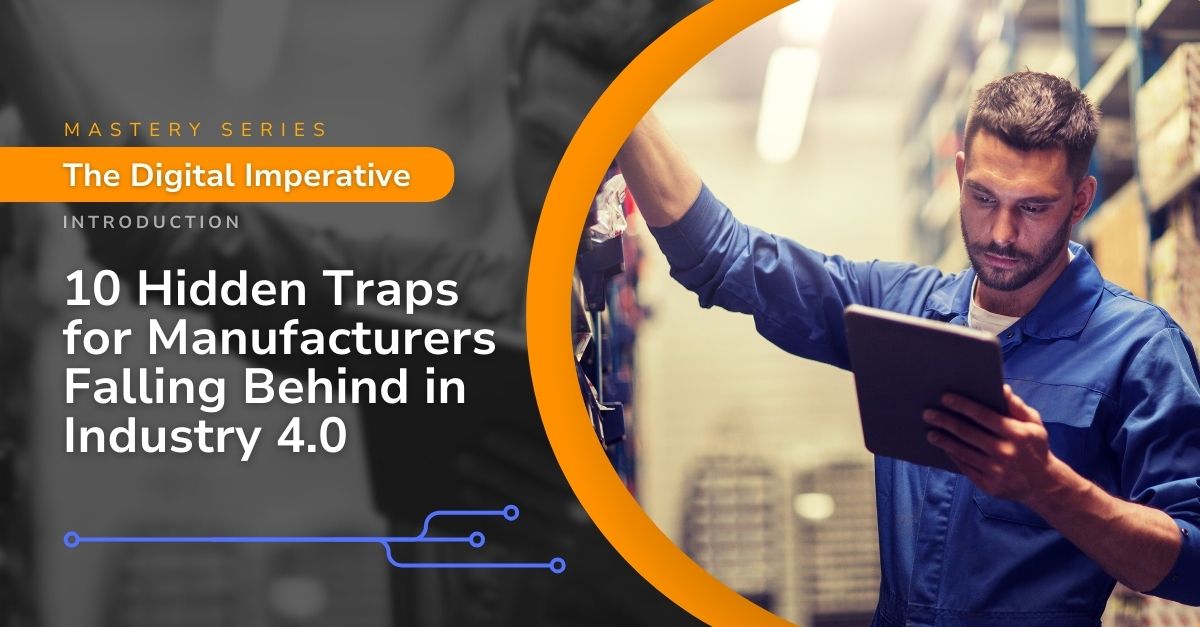
The Digital Imperative: 10 Hidden Traps for Manufacturers Falling Behind in Industry 4.0
- Part 1 – Outdated Tech is Weakening Your Talent Pipeline
- Part 2 – How Legacy Systems Sabotage Your Cybersecurity and Productivity
- Part 3 – How Ignoring Digital Tools Leaves You Vulnerable to Downtime
- Part 4 – When Digital Stagnation Leads to Poor Communication and Production Chaos
- Part 5 – The Real Cost of Trying to Keep Up in the Market Without Digital Transformation
- Part 6 – Missing Out on Real-Time Data Drains Productivity and Profit
- Part 7 – How Failing To Go Digital Jeopardizes Regulatory Compliance
- Part 8 – How Outdated Inventory Practices Sabotage Your Operations
- Part 9 – Limited Customization Options are Driving Your Customers Away
- Part 10 – The Productivity Trap of Failing to Scale Digital Initiatives
Upskilling and Reskilling
A stagnant workforce in the manufacturing industry not only exacerbates the skilled labor shortage but also threatens long-term competitiveness, making upskilling and reskilling essential strategies to address current and future challenges in productivity, innovation, and adaptation to technological advancements.
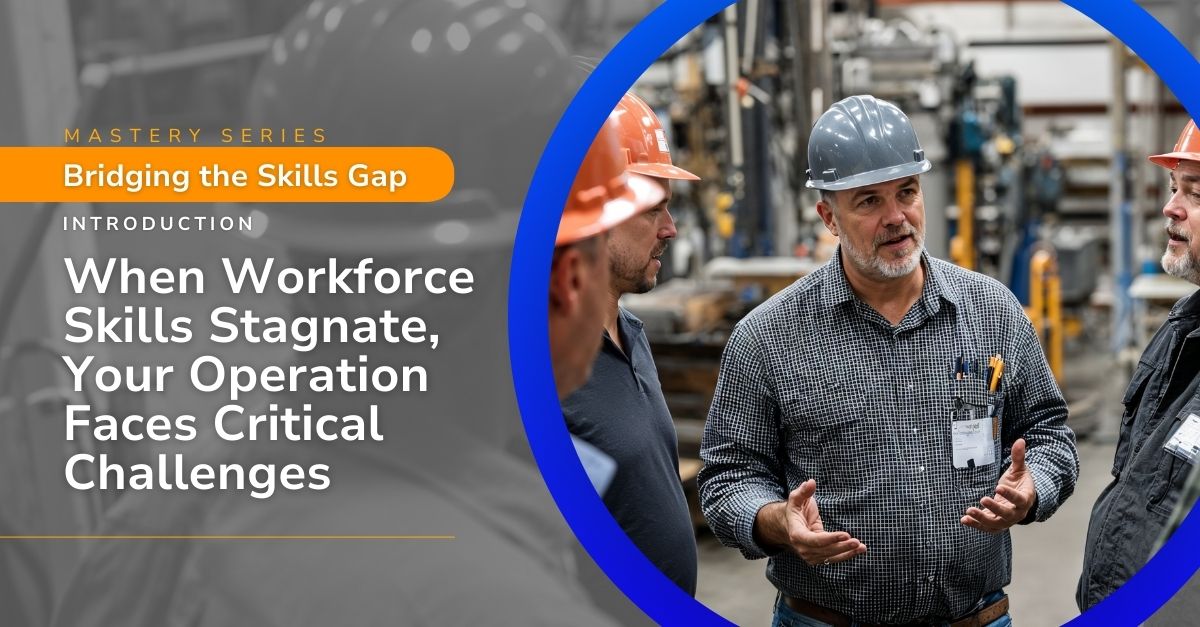
Bridging the Skills Gap: Addressing 10 Critical Challenges of a Stagnant Workforce in Manufacturing
- Part 1 – Why Automation Alone Won’t Boost Productivity
- Part 2 – Why Non-Technical Skills Are Increasingly the Key to Increasing Productivity
- Part 3 – The Widening Digital Divide is Leaving Some Companies in the Dust
- Part 4 – Lack of Upskilling Sabotages Problem-Solving, Decision Making, and Innovation
- Part 5 – The Link Between Upskilling and Employee Well-being
- Part 6 – Neglecting Upskilling Leaves Your Operation Vulnerable to Safety Issues
- Part 7 – How Neglecting Upskilling Erodes Legacy Knowledge and Hurts Productivity
- Part 8 – Failing to Upskill Frontline Leaders Can Derail Operations
- Part 9 – Skimping on Skills Training Sabotages the Bottom Line
- Part 10 – An Underdeveloped Workforce Means an Unscalable Operation
Continuous Improvement
In manufacturing, progress isn’t just a luxury—it’s a necessity. A culture of continuous improvement isn’t about making small tweaks; it’s about fostering a mindset where every employee, from the shop floor to the C-suite, is constantly seeking ways to do things better, faster, and smarter.
- Part 1 – When Progress Takes a Break, it Leaves Your Productivity Stalled
- Part 2 – Profit Erosion in the Production Line
- Part 3 – Quality Takes a Dive and Productivity Pays the Price
- Part 4 – When Morale Breaks Down So Does the Shop Floor
- Part 5 – When Innovation Pauses, Your Production Line Follows
- Part 6 – How Customer Loyalty Slips Through Your Fingers
- Part 7 – When Your Slice of the Market Becomes a Crumb
- Part 8 – When Opportunities Slip Through the Cracks
- Part 9 – Safety Shortsights and Their Costly Consequences
- Part 10 – Growth and Adaptation Slows to a Crawl
Unplanned Downtime
Unplanned downtime isn’t just a financial drain; it’s a multi-headed hydra that wreaks havoc on various facets of your manufacturing operation. Here are the top 10 consequences, each of which will be explored in greater detail in subsequent articles of the POWERS Mastery Series:
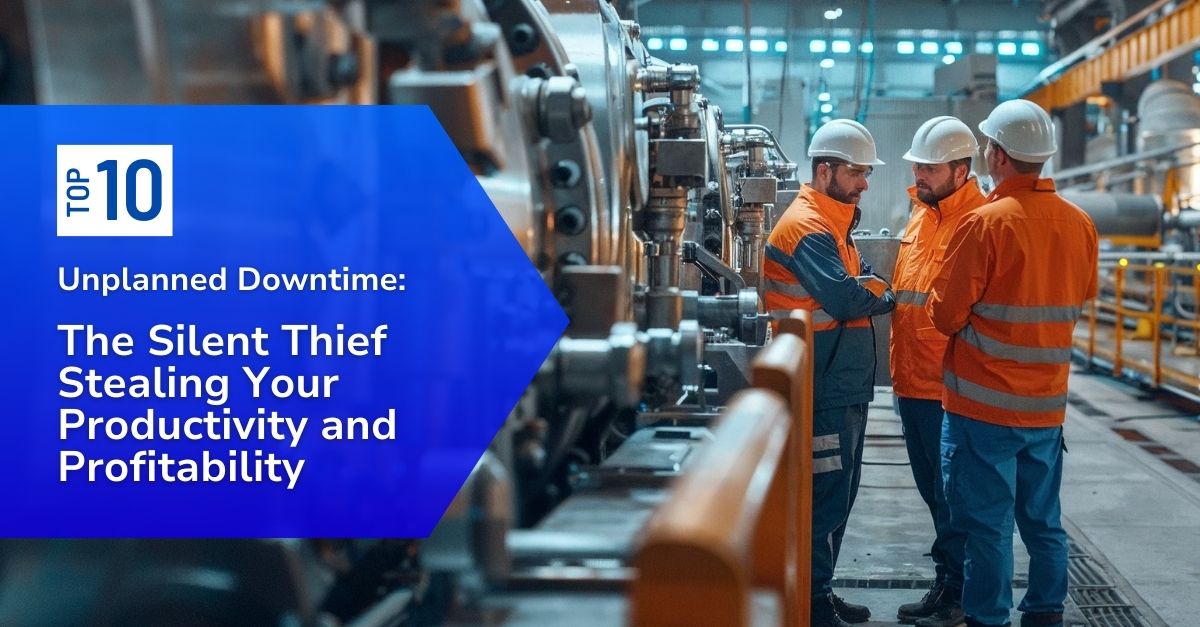
Unplanned Downtime: The Silent Thief Stealing Your Productivity and Profitability
- Part 1 – The Financial Burden of Breaking Down
- Part 2 – Eroding Maintenence Leading to Eroding Margins
- Part 3 – How Disrupted Production Leads to Unhappy Customers
- Part 4 –How Production Stoppages Can Break Your Supply Chain
- Part 5 – How Breakdowns Can Lead to Safety Shortcomings
- Part 6 – How Equipment Failures Drain Employee Drive
- Part 7 – How Constant Breakdowns Lead to Spiraling Maintenance Costs
- Part 8 – How Lost Production Time Leads to Lower Competitive Edge
- Part 9 – How Shop Floor Stoppages Lead to Regulatory Pitfalls
- Part 10 – How Missed Production Uptime Means Missed Opportunities
Root Cause Analysis
RCA is a structured problem-solving methodology that goes beyond addressing surface-level symptoms. It delves deeper into the core issues that contribute to recurring problems. Identifying and rectifying the root causes can prevent future occurrences, improve operational efficiency, and enhance overall performance.
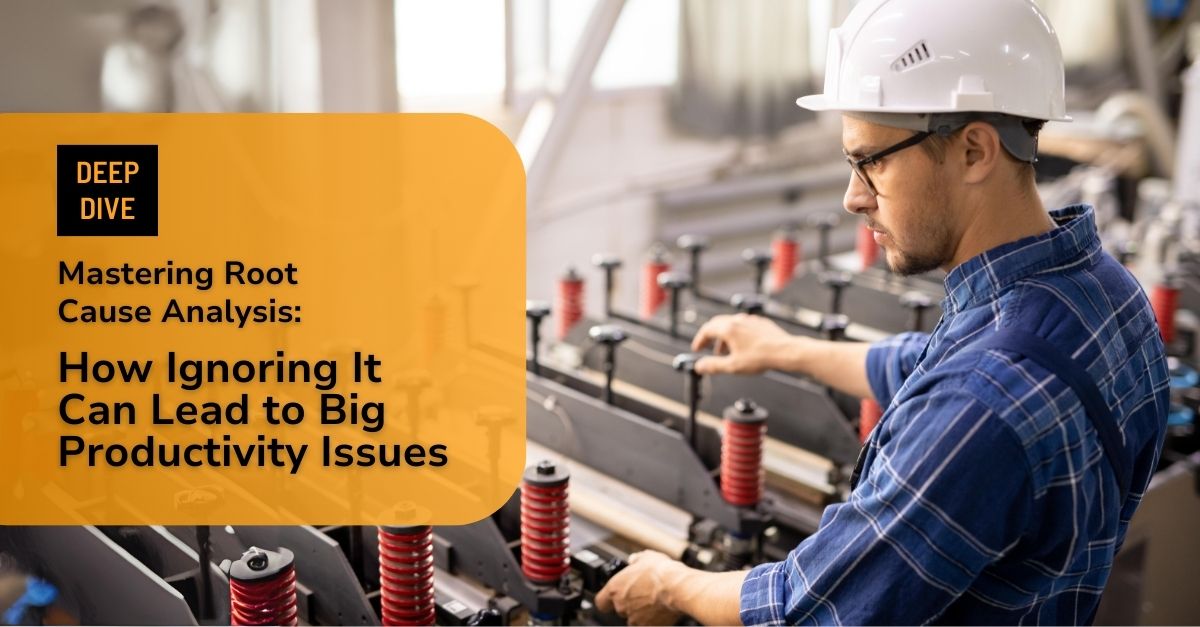
Mastering Root Cause Analysis: How Ignoring It Can Lead to Big Productivity Issues
Productivity
Productivity is a crucial indicator of manufacturing operational health. But productivity is more than just efficiency. Efficiency focuses on doing things right – minimizing waste and maximizing resource usage. Productivity takes a broader view, measuring the overall output achieved in relation to the resources invested. A highly efficient process still has low productivity if it can’t produce a significant volume of goods.
- Part 1 – Without Top Talent, Top Productivity is Elusive
- Part 2 – How Blind Spots in Cost Analysis Hide Your Productivity Struggles
- Part 3 – When Supply Chain Issues Deliver A Productivity Hit
- Part 4 – Environmental Threats that Threaten Your Productivity
- Part 5 – Don’t Let Scaling Up Bring Down Your Productivity
- Part 6 – How Vulnerabilities to Disruptions Undermine Productivity
- Part 7 – Why Ignoring TPM Means Missing Out on Productivity Goals
- Part 8 – How Poor Training and Development Creates Productivity Shortfalls
- Part 9 – How Delayed NPIs Lead to Productivity Misses
- Part 10 – How Inaccurate Data Obscures Productivity Insight
Overall Equipment Effectiveness (OEE)
- Part 1 – The Hidden Costs Undermining Your OEE Score
- Part 2 - Dig Deep to Eliminate Inefficiencies that Silently Sabotage Your OEE
- Part 3 – How Guesswork Kills OEE
- Part 4 – When Nobody Takes Ownership OEE Suffers
- Part 5 – When “Pushing Production” Costs You OEE Points
- Part 6 – The Customer Connection: When Dissatisfaction Drains Your OEE
- Part 7 – Death by a Thousand Cuts: How Wear and Tear Steals From Your OEE
- Part 8 – Competitive Disadvantage: The Hidden Enemy of OEE Excellence
- Part 9 – How Missed Opportunities for Improvement Means Missed OEE Potential
- Part 10 – Is Stagnant Innovation Stagnating Your OEE Results
Capacity Utilization
The Untapped Potential Mastery Series emphasizes that neglecting capacity utilization practices can result in higher costs due to inefficiencies, underproduction, and wasted resources. To optimize production and profitability, businesses must prioritize equipment maintenance, production scheduling, and workforce training.
- Part 1 – The Price of Lost Revenue and Profit Resulting from Underutilized Capacity
- Part 2 – How Rising Production Costs Hide Your Factory’s True Potential
- Part 3 – Poorly Managing Resources is Stealing Your Profits
- Part 4 – Break the Quality Struggle Cycle to Fix This Shop Floor Frustration
- Part 5 – From Chaos to Capacity: How to Tame Turnover and Optimize Your Operations
- Part 6 – Manufacturing Nightmares: When Your Shop Floor Can’t Keep Up
- Part 7 – When Supply Chain Disruptions Reveal Your True Capacity
- Part 8 – Unlocking Efficiency When Sustainability Meets the Shop Floor
- Part 9 – Understaffed and Underperforming on the Shop Floor
- Part 10 – How Blind Spot Vulnerabilities Impact Your Shop Floor’s Efficiency
Profitability
The Maximizing Profitability Mastery Series stresses that ignoring profitability-focused practices leads to higher costs due to waste, inefficiencies, and energy use. To optimize profits, businesses must prioritize regulatory compliance, customer preferences, talent, supply chain strength, and innovation.
- Part 1 - How Runaway Costs Derail Manufacturers’ Drive for Sustainability
- Part 2 - Tackling Excessive Waste Management Issues in Manufacturing
- Part 3 - Mastering Resource Efficiency in the Quest for Manufacturing Excellence
- Part 4 - The Impact of Unmitigated High Energy Costs on Manufacturers
- Part 5 - How the Complexities of Regulatory Compliance Can Erode Margins
- Part 6 - Navigating the Challenges of Reduced Market Competitiveness for Sustained Profitability
- Part 7 - Don’t Let Preferences Pull You Under
- Part 8 - Low Talent Investment is Undermining Your Bottom Line
- Part 9 - Don’t Let Supply Chain Vulnerabilities Bleed Your Profits
- Part 10 - Outsmart the Competition and Protect Your Profits
Management Operating System (MOS)
In the constantly shifting manufacturing landscape, excelling in operational efficiency and cost management is pivotal. Adopting a comprehensive Management Operating System (MOS), or increasing compliance and proficiency with an existing MOS, is fundamental to achieving these goals.
- Part 1 - Identifying Key Inefficiencies in the Absence of a Management Operating System
- Part 2 - Top 10 Pitfalls: Lack of an MOS Derails Productivity
- Part 3 - Top 10 Quality Issues at Risk Without a Robust Management Operating System
- Part 4 - The High Cost of an Ineffective Management Operating System
- Part 5 - Without an Optimized Management Operating System, Decision-Making is Severely Impaired
- Part 6 - Scaling Challenges of an Inadequate Management Operating System
- Part 7 - The High Price of Low Engagement: Unpacking the Operational Impact of Employee Discontent
- Part 8 - Safeguarding Success: Decoding the Impact of Compliance and Safety Issues
- Part 9 - Examining the Cost of a Slow Response to Market Shifts
- Part 10 - Charting Success: Understanding the Costs of Losing Competitive Advantage
Shop Floor Excellence
In the intricate dance of manufacturing, where the synchronization of tools, resources, and human expertise is paramount, Shop Floor Excellence (SFE) emerges as the maestro, conducting every aspect of factory operations towards peak efficiency and quality. It’s a holistic approach that transcends mere production targets, orchestrating a culture of perpetual advancement and precision in execution.
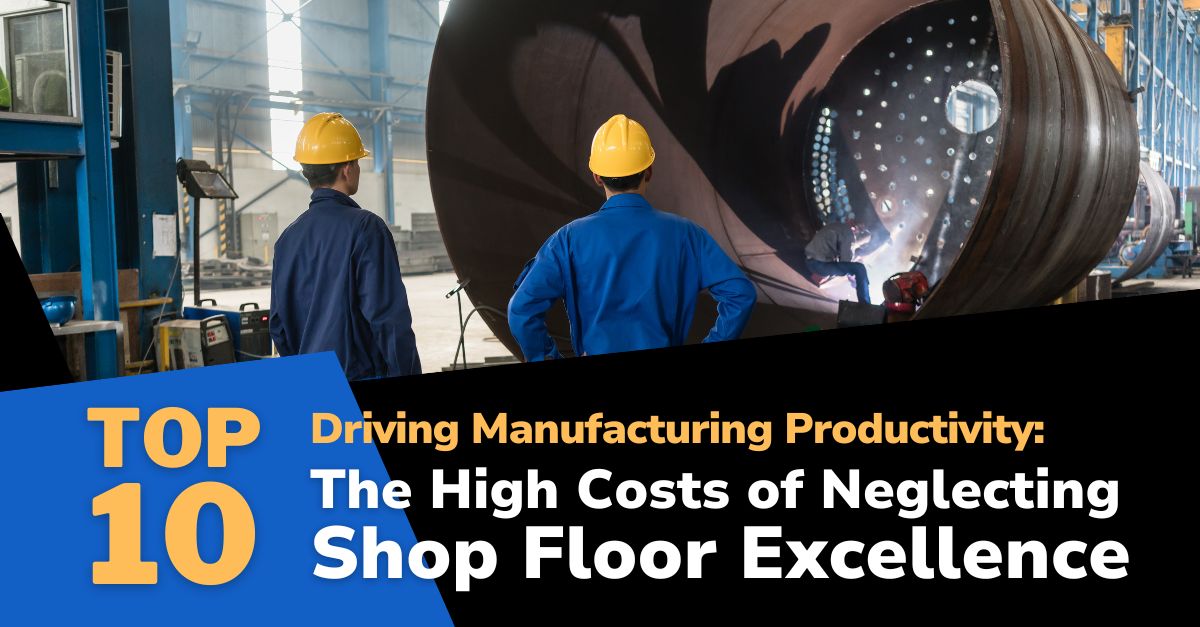
Mastering the Manufacturing Dance: The High Stakes of Overlooking Shop Floor Excellence
- Part 1 - The Perils of Overlooking SFE in Assembly Line Setup
- Part 2 - A Lackluster Approach to Shop Floor Excellence Impacts Workforce Engagement —
- Part 3 - The Consequences of Sidestepping Data-Driven Decisions in Shop Floor Excellence
- Part 4 - Without Shop Floor Excellence, Product Quality Can Drop Like a Rock
- Part 5 - A Lack of Commitment to Shop Floor Excellence Can Lead to These 10 Safety Issues
- Part 6 - Shop Floor Excellence Makes Your Operation More Agile, Flexible, and Adaptable to Market Changes
- Part 7 - Bridging the Gap with Effective Communication in Shop Floor Excellence
- Part 8 - How Ignoring Shop Floor Excellence Undermines Continuous Improvement
- Part 9 - Tackling Inefficient Energy and Material Use with Shop Floor Excellence
- Part 10 - Enhancing Customer Focus Through Shop Floor Excellence
Maintenance Performance
One of the vital signs of a healthy manufacturing operation is its Overall Equipment Effectiveness (OEE). This critical measure tells you how well your equipment performs by combining three essential metrics: availability, performance, and quality.
- Part 1 - The Critical Link Between Maintenance and OEE
- Part 2 - How Maintenance Practices Shape Product Quality
- Part 3 - How Poor Maintenance Standards and Practices Impact Schedule Adherence
- Part 4 - How Maintenance Practices Echo Along the Supply Chain
- Part 5 - The Impact of Maintenance on Maximizing Return on Assets (ROA) in Manufacturing
- Part 6 - Poor Maintenance Practices Lead to Out-of-Control Operational Costs
- Part 7 - Navigating the Safety and Compliance Minefield in Manufacturing
- Part 8 - The High Cost of Overlooking Maintenance in Manufacturing Strategic Planning
- Part 9 - Poor Maintenance Practices Are a Hindrance to Technological Innovations
- Part 10 - Overcoming the ‘Reactive’ or ‘Run Till it Breaks’ Pitfall
Frontline Leadership Development
In an era of rapidly evolving markets and customer preferences, manufacturing giants have an unprecedented opportunity to surge ahead of the competition. The secret isn’t just in state-of-the-art machinery or AI algorithms, but in empowering frontline managers and supervisors with the vision and tools they need for strategic alignment.
- Part 1 - Strategic Alignment that Bridges Daily Tasks with Broader Visions for Unified Organizational Success
- Part 2 - Crafting Clarity through Effective Communication and Active Listening
- Part 3 - Sharpening Decision-Making Prowess for Seamless Operations and Minimal Downtimes
- Part 4 - Championing Lean Principles for Streamlined Success and an Ever-Evolving Workplace
- Part 5 - Mastering Performance Management for Optimal Team Output and Growth
- Part 6 - How Leaders Well-Trained in the Soft Skills Transform Manufacturing Teams
- Part 7 - Strengthening Conflict Resolution Skills for Peak Productivity and Profitability Gains
- Part 8 - Unleashing Potential with Precision Time and Resource Management
- Part 9 - Safety First for Sustainable And Scalable Productivity And Profitability
- Part 10 - Equipping Your Shop Floor Leaders to Be Effective Change Managers