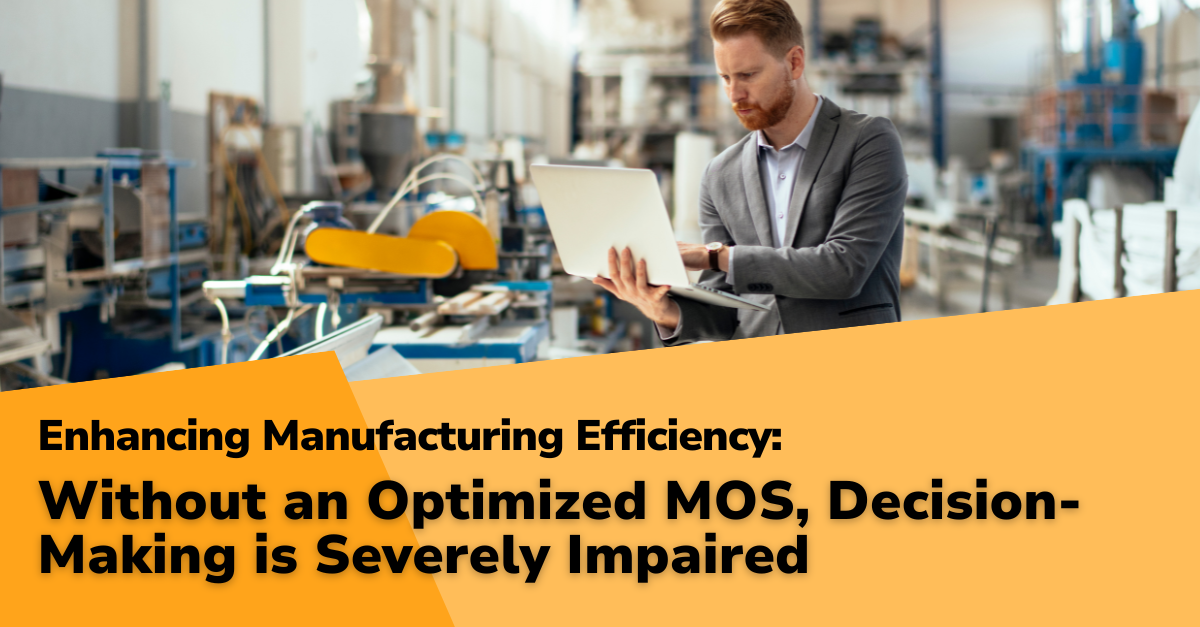
Without an effective MOS, both individual and organizational decision-making are severely impaired. This shortfall can lead to delayed responses, misaligned strategies, and ultimately, a compromise in both growth and sustainability.
As the fifth installment in our “Enhancing Manufacturing Efficiency” Mastery Series, this article zeroes in on the pivotal role of a Management Operating System (MOS) in shaping effective decision-making processes. Drawing on our lengthy experience, industry insights, and analysis, we delve into how a MOS’s absence or poor implementation can lead to suboptimal decision-making, impacting every facet of manufacturing operations from the production floor to the executive suite.
In the face of global competition, rapid technological advancements, and ever-evolving market demands, manufacturers increasingly recognize the importance of data-driven decision-making.
An MOS is the backbone of this approach, offering a structured, systematic method for collecting, analyzing, and utilizing data to guide strategic and operational decisions. However, when this system is absent or inadequately implemented, organizations navigate in the dark, relying on outdated methods or guesswork, leading to costly missteps and lost opportunities.
This exploration is more than an academic exercise; it critically evaluates the tangible impact of decision-making processes on manufacturing efficiency. By dissecting the top 10 ways a deficient MOS can impair decision-making, we aim to provide operational executives and stakeholders with the insights needed to recognize, rectify, and ultimately reap the benefits of a well-oiled MOS. This understanding is critical to ensuring operational success, long-term sustainability, and growth in an increasingly competitive and complex manufacturing landscape.
1Reduced Market Agility:
The absence of an effective MOS significantly hampers a manufacturer’s ability to make swift decisions, directly impacting responsiveness to consumer trends and supply chain dynamics. As reported in industry studies, companies with agile decision-making processes are often 30% more likely to have higher operational efficiency. Opportunties can be won on the speed of informed and effective decisions.
2Inefficient Resource Allocation:
A poorly implemented MOS can misallocate resources, impacting production costs, time-to-market, and ultimately, customer satisfaction. Studies suggest that optimal resource allocation can improve production efficiency by up to 25%, a target difficult to achieve without a robust MOS.
3Impaired Strategic Planning:
Without a comprehensive MOS, strategic planning may lack data-driven insights, resulting in strategies misaligned with market demands. This misalignment can lead to missed opportunities, which, according to a Harvard Business Review study, could impact annual revenue growth by up to 10%.
4Ineffective Crisis Management
Manufacturing firms struggle with practical crisis management without a robust MOS. This deficiency becomes particularly evident during unexpected events like supply chain disruptions or machinery breakdowns. Industry data suggests that effective crisis management can reduce recovery time and associated costs by up to 40%, highlighting the critical nature of an MOS in navigating unforeseen challenges.
5Inadequate Performance Tracking:
An MOS facilitates accurate tracking of key performance indicators (KPIs), essential for identifying improvement areas. Lack of effective performance tracking can obscure operational inefficiencies, potentially reducing overall productivity by up to 20%.
6Poor Financial Management:
Financial decisions without MOS-generated data can lead to budgetary inefficiencies and suboptimal capital allocation and investment choices. Research indicates that data-driven financial management can enhance revenue growth by 5-10% annually.
7Suboptimal Supply Chain Management:
An MOS facilitates effective supply chain management and ensures optimal inventory levels and timely procurement. In its absence, supply chain disruptions can increase operational costs by 10-15%, as reported by industry analysts. If the last few years have taught us anything in manufacturing, it’s that supply chain instability or outright disruptions can have lasting effects on customer loyalty and may shift buying habits permanently.
8Decreased Employee Productivity and Engagement:
Employee engagement and productivity are enhanced by clear, data-driven objectives provided by an MOS. According to workforce studies, the lack of such a system can lead to a 15% decrease in employee productivity. An optimized and efficient MOS can improve employee morale and help hire and retain the right talent, increasing long-term organizational stability.
9Diminished Innovation Capacity:
An MOS’s data insights are crucial for fostering innovation. As noted in technology and innovation reports, companies that leverage data for innovation are often 25% more likely to maintain a competitive edge in the market. In industries where margins are razor thin or competition is fierce, innovation can be the key to increased demand and higher profitability.
10Increased Risk Exposure:
Effective risk management, supported by an MOS, involves analyzing data to foresee and mitigate risks. A poorly implemented MOS can increase a company’s exposure to operational and market risks by up to 20%, affecting long-term sustainability and profitability.
Conclusions for Manufacturing Operations Decision Makers
The indispensable role of a well-structured Management Operating System in manufacturing cannot be overstated. The capacity to make well-informed, timely decisions sets industry leaders apart in a landscape marked by fierce competition, rapid technological change, and evolving market dynamics. Our exploration of the top 10 impacts of a deficient MOS on decision-making underscores the profound effect that such a system, or lack thereof, can have on a manufacturing organization’s efficiency, profitability, and long-term viability.
Unleash Peak Performance with POWERS
At POWERS, we understand the unique challenges and opportunities of optimizing manufacturing processes in today’s complex environment. Our approach is rooted not just in theory but in practical, real-world experience and a deep understanding of the nuances of manufacturing operations. We pride ourselves on identifying areas where a Management Operating System can be improved and or the implemention more tailored–practical solutions that drive tangible results.
- Tailored Implementation: We recognize that each manufacturing operation is unique. Our strategies are customized to fit our client’s specific needs and contexts, ensuring that the MOS solutions we propose are practical but also sustainable and scalable
- Data-Driven Insights Leveraging the latest in data analytics and industry benchmarks, POWERS provides deep and actionable insights, transforming data into a strategic asset for decision-making.
- Holistic Approach: Our focus goes beyond just the technical aspects of an MOS. We consider the human element, emphasizing leadership development, employee engagement, and a culture of continuous improvement.
- Sustained Performance Improvement: Our goal is to equip our clients with solutions and the capability to maintain and build upon these improvements. We focus on creating systems that deliver lasting value.
- Expertise and Experience: The POWERS team brings a wealth of experience and a track record of success in manufacturing efficiency. Our expertise is grounded in real-world applications, ensuring practical, executable strategies.
By recognizing the critical role of an MOS in decision-making and operational efficiency and implementing the POWERS approach, manufacturers can navigate the complexities of their industry more effectively. This enhances efficiency and profitability and positions them to adapt and thrive in an ever-changing global market.
Begin your journey towards unparalleled efficiency, quality, and profitability with POWERS. Connect with our team of experts, ready to guide you through every step of this transformative process. Connect with our experts at +1 678-971-4711 or reach out via email to info@thepowerscompany.com.
Continue Reading from this Mastery Series
- Part 1 - Identifying Key Inefficiencies in the Absence of a Management Operating System
- Part 2 - Top 10 Pitfalls: Lack of an MOS Derails Productivity
- Part 3 - Top 10 Quality Issues at Risk Without a Robust Management Operating System
- Part 4 - The High Cost of an Ineffective Management Operating System
- Part 5 - Without an Optimized Management Operating System, Decision-Making is Severely Impaired
- Part 6 - Scaling Challenges of an Inadequate Management Operating System
- Part 7 - The High Price of Low Engagement: Unpacking the Operational Impact of Employee Discontent
- Part 8 - Safeguarding Success: Decoding the Impact of Compliance and Safety Issues
- Part 9 - Examining the Cost of a Slow Response to Market Shifts
- Part 10 - Charting Success: Understanding the Costs of Losing Competitive Advantage