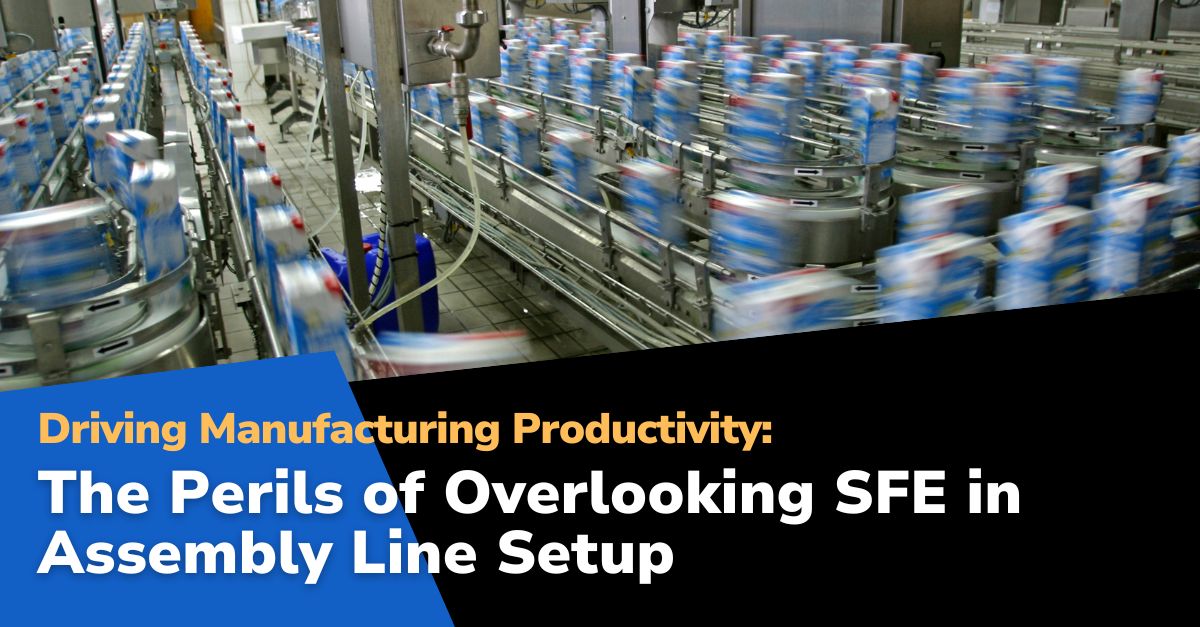
In the grand performance of manufacturing, each element on the shop floor plays a critical role. But without Shop Floor Excellence (SFE), the production line, much like a dancer out of step, can falter in its rhythm, causing a cascade of inefficiencies that resonate throughout the entire operation. In this first installment of our ten-part series, we expose the top 10 hidden costs of an inefficient assembly line setup, a misstep that can cripple even the most robust manufacturing operations.
1Production Delays:
An assembly line that is not optimized for efficiency can lead to significant production delays. Such delays extend the time to market, causing potential loss of sales and market opportunities and disrupting supply chain scheduling and customer satisfaction.
Solution: Implement real-time monitoring and predictive analytics to identify and rectify bottlenecks promptly.
2Increased Cycle Times:
Without SFE, cycle times can increase due to unbalanced workstations or inefficient workflow designs. Longer cycle times mean less output in the same amount of time, reducing the operation’s overall capacity to meet demand.
Solution: Optimize workstation layouts and processes for efficient workflow, reducing cycle times.
3Wasted Resources:
Inefficiencies in the assembly line can lead to higher materials and energy consumption. This results in increased operational costs and impacts the environment, contributing to unnecessary waste and carbon footprint.
Solution: Employ lean manufacturing principles to minimize waste and optimize resource utilization.
4Elevated Overhead Costs:
An inefficient assembly line often requires more labor, leading to elevated overhead costs. These increased expenses can eat into profit margins and make investing in other areas of the business difficult.
Solution: Streamline operations to reduce labor requirements and manage overheads effectively.
5Reduced Throughput:
A direct consequence of inefficient assembly line setups is diminished throughput. This decrease in production output can have a ripple effect, causing inventory shortages and harming the company’s ability to fulfill orders promptly.
Solution: Integrate advanced scheduling and planning tools to maximize production output.
6Lower Product Quality:
Disorganization and inefficiencies on the shop floor can lead to lapses in quality control. The result is an increased likelihood of product defects, customer complaints, and returns, all of which can damage a company’s reputation for quality.
Solution: Adopt strict quality control systems and continuous improvement practices to enhance product standards.
7Compromised Worker Safety:
A poorly designed assembly line can create hazardous work conditions. Inefficiencies can lead to cluttered workspaces, which increase the risk of accidents, affecting worker safety and leading to potential downtime and legal issues.
Solution: Design ergonomic and safety-conscious assembly lines to mitigate workplace hazards.
8Decreased Worker Morale:
Inefficient assembly lines can frustrate employees and reduce morale. When workers are not empowered with an efficient system, their engagement and productivity can decline, affecting the overall morale of the workforce.
Solution: Foster a culture of continuous improvement and employee engagement to boost morale and productivity.
9Inflexibility to Market Changes:
An assembly line that lacks flexibility due to poor setup cannot quickly adapt to changes in market demand or customization requests. This rigidity can cause a company to miss out on new opportunities and fail to meet customer needs.
Solution: Incorporate flexible manufacturing systems to quickly adapt to changing market demands.
10Diminished Brand Reputation:
Over time, the cumulative effect of these issues can erode a company’s brand reputation. In today’s competitive market, customers expect timely and quality products, and a failure to deliver due to an inefficient assembly line can lead to loss of customer trust and loyalty.
Solution: Focus on overall excellence in manufacturing processes to rebuild and maintain brand reputation.
Manufacturers can avoid these costly mistakes by recognizing and addressing the pitfalls of an inefficient assembly line setup. Embracing the SFE approach is essential for companies looking to stay in step with the demands of the modern market.
The POWERS Difference:
Synchronizing Your Shop Floor for Success
At POWERS, we understand that the backbone of manufacturing success lies in the precision and efficiency of the shop floor. Our comprehensive approach to SFE ensures that your assembly line meets targets and sets new standards for operational excellence. Our expertise guides manufacturers to create a symphony of efficiency, where every movement is purposeful, and every resource is optimized.
Join us in transforming your production line into a model of manufacturing excellence. Contact POWERS for an in-depth assessment and customized solutions that resonate with your unique manufacturing needs.
To step into the future of efficient manufacturing, reach out to our team at +1 678-971-4711 or email us at info@thepowerscompany.com. Let’s choreograph your operations to the rhythm of success.
Continue Reading from this Mastery Series
- Part 1 - The Perils of Overlooking SFE in Assembly Line Setup
- Part 2 - A Lackluster Approach to Shop Floor Excellence Impacts Workforce Engagement —
- Part 3 - The Consequences of Sidestepping Data-Driven Decisions in Shop Floor Excellence
- Part 4 - Without Shop Floor Excellence, Product Quality Can Drop Like a Rock
- Part 5 - A Lack of Commitment to Shop Floor Excellence Can Lead to These 10 Safety Issues
- Part 6 - Shop Floor Excellence Makes Your Operation More Agile, Flexible, and Adaptable to Market Changes
- Part 7 - Bridging the Gap with Effective Communication in Shop Floor Excellence
- Part 8 - How Ignoring Shop Floor Excellence Undermines Continuous Improvement
- Part 9 - Tackling Inefficient Energy and Material Use with Shop Floor Excellence
- Part 10 - Enhancing Customer Focus Through Shop Floor Excellence