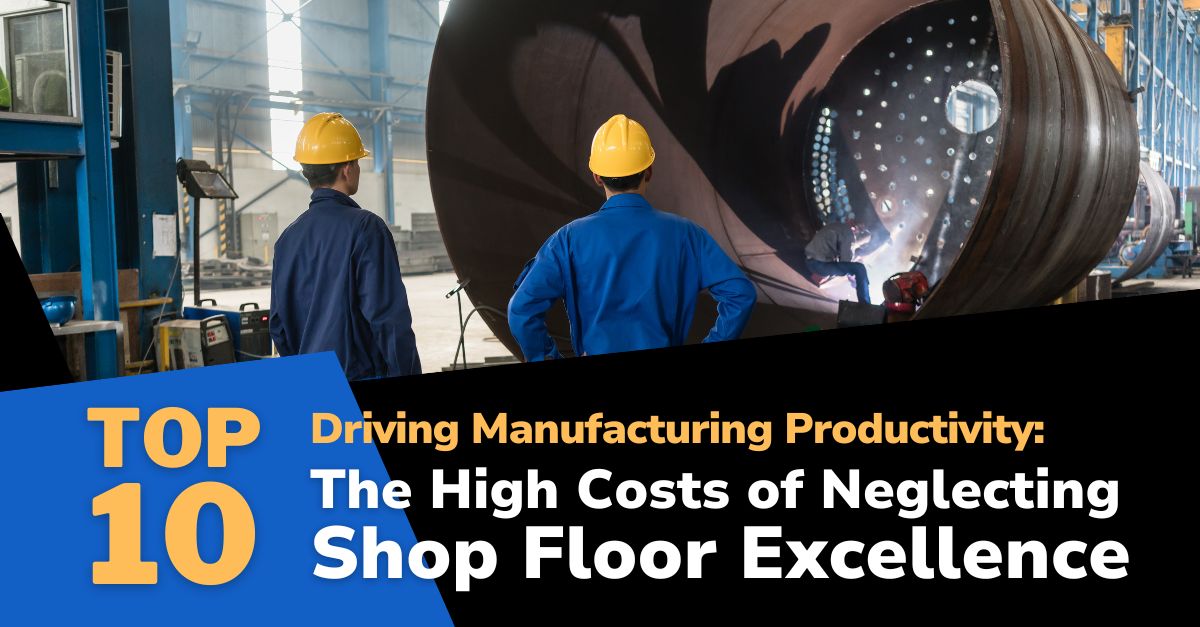
In the intricate dance of manufacturing, where the synchronization of tools, resources, and human expertise is paramount, Shop Floor Excellence (SFE) emerges as the maestro, conducting every aspect of factory operations towards peak efficiency and quality. It’s a holistic approach that transcends mere production targets, orchestrating a culture of perpetual advancement and precision in execution.
Leadership Vision and its Role in SFE
The symphony of SFE begins with leadership. A compelling vision from the top is crucial, as it sets the tempo for the entire organization. This vision must resonate at every level, fostering a culture of efficiency and unified direction, vital for navigating the complexities of modern manufacturing. Leadership in SFE is akin to the conductor of an orchestra, ensuring that each section plays in harmony toward a grand performance.
Accountability and Time Management
The rhythmic beats of effective shop floor management are routine accountability practices and structured frameworks for time management. Visual cues act as the score, guiding the workforce to effortlessly assess processes and adhere to standards, while a comprehensive understanding of efficient processes ensures that the production does not miss a beat.
The 10 Pillars of SFE
These principles of SFE are not standalone notes but are part of an intricate composition that forms the 10 Pillars of SFE:
1Continuous Improvement:
An insatiable appetite for betterment, assessing and addressing bottlenecks, and embracing feedback, ensuring the manufacturing process is always moving towards perfection.
2Lean Manufacturing:
A principle born from the famed Toyota Production System, focusing on reducing waste and non-value-adding processes to maintain a streamlined and responsive shop floor.
3Total Productive Maintenance (TPM):
A collaborative approach where every member, from CEOs to line workers, ensures optimal equipment functioning and minimal downtime.
4Workforce Engagement:
Moving beyond mere participation, SFE cultivates a workforce that’s not just skilled but emotionally invested in the organization’s mission.
5Visual Management:
Tools that provide clarity amidst the chaos, ensuring that goals, progress, and challenges are visible at a glance.
6Standardized Work:
The discipline of standardization minimizes anomalies, reduces errors, and lays the groundwork for iterative improvement.
7Data-Driven Decisions:
In the realm of SFE, data reigns supreme, with real-time analytics leading to informed, timely, and impactful decisions.
8Quick Changeover/SMED:
The ability to rapidly adapt to market changes, epitomized by the Single-Minute Exchange of Die system, enables swift production transitions.
9Built-in Quality:
In SFE, quality is not an afterthought but interwoven into every manufacturing stage.
10Safety:
A pillar recognizing the symbiotic relationship between excellence and a safe work environment.
What’s at Stake? The Cost of Neglecting SFE
Failing to embrace SFE can lead manufacturers to falter in these ten critical areas:
1Inefficient Assembly Line Setup:
When manufacturers overlook the need for a well-organized and agile assembly line, they risk creating inefficiencies that ripple throughout the entire production process. A poorly configured line can lead to significant production bottlenecks, where one slow process holds up the subsequent stages, resulting in increased cycle times and lead times. The absence of systems like SMED exacerbates this issue, prolonging equipment setup times and reducing responsiveness to customer demands and market changes.
2Inadequate Workforce Engagement:
A disengaged workforce is a silent drain on manufacturing performance. When employees are not actively participating in the company’s vision and operational improvements, their sense of ownership and accountability diminishes. This apathy can result in reduced operational efficiency, as employees are less likely to identify and solve problems proactively, leading to a higher incidence of mistakes and lower overall productivity.
3Neglect of Data-Driven Decisions:
Data is a critical asset in modern manufacturing, and neglecting to base decisions on solid data analytics can lead to suboptimal operational choices. Manufacturers may miss out on identifying patterns that could lead to cost savings or efficiency gains. Without leveraging data, decisions may be made on outdated information, leading to quality issues, increased scrap rates, and a loss of customer trust and revenue.
4Poor Quality Control:
Quality control is fundamental to manufacturing, and without a proactive approach integrated into each stage of the production process, manufacturers are likely to encounter higher defect rates. This lack of built-in quality can result in costly rework and scrap, and more importantly, it can damage the manufacturer’s reputation for reliability and lead to customer attrition.
5Safety Concerns:
Ignoring safety issues in pursuit of productivity gains is a disaster waiting to happen. Workplace accidents and injuries can result in direct costs such as medical expenses, compensation, and fines, as well as indirect costs like downtime, reduced morale, and the potential for increased insurance premiums. A safe work environment is essential for maintaining a productive workforce and minimizing unexpected disruptions to operations.
6Resistance to Change and Innovation:
Resistance to change is a significant barrier to improving efficiency and adopting new technologies. Manufacturers who cling to “the way things have always been done” will struggle to keep pace with competitors who leverage innovative technologies and processes. This can lead to an inability to scale operations or efficiently meet the market’s evolving needs.
7Ineffective Communication:
Poor communication can lead to misalignment of goals and misunderstandings between management and the shop floor and within different departments. This ineffective communication can cause errors, redundancies, and a lack of coordination, which are detrimental to efficient operations and can hurt project timelines and product rollouts.
8Lack of Continuous Improvement Culture:
Continuous improvement is the lifeblood of operational excellence. Without it, manufacturers can become stagnant, missing out on incremental gains that, over time, add up to significant competitive advantages. The absence of a culture that values and seeks out continuous improvement can lead to higher operational costs and a decreased ability to adapt to new challenges.
9Inefficient Energy and Material Usage:
Efficiency in resource utilization is critical to cost control and environmental sustainability. Manufacturers that do not prioritize efficiency in their energy and material usage may face higher operational costs and a larger environmental footprint, which can affect profitability, brand perception, and customer choice in an increasingly eco-conscious market.
10Poor Customer Focus:
In today’s market, customer needs and feedback are critical to the success of a product. Neglecting to align products with customer expectations can lead to decreased satisfaction and loyalty. Manufacturers that fail to focus on their customers may find it challenging to retain market share against competitors who are more attuned to customer needs and capable of adapting swiftly to feedback.
Conclusions for Senior Operations Leaders
Embracing the tenets of Shop Floor Excellence is not just a strategy but a necessity for manufacturers aiming to thrive in today’s cutthroat market. The perils of ignoring SFE are far-reaching, touching every aspect of production, from the intricacies of assembly line efficiency to the critical nuances of workforce morale and customer satisfaction.
As the manufacturing landscape continues to evolve with technological advancements and changing consumer demands, the commitment to SFE becomes the distinguishing factor between those who lead the industry and those who lag behind. By prioritizing SFE, manufacturers can not only sidestep the pitfalls of operational oversight but also chart a course toward enduring success and distinction in the global marketplace.
Forge the Future of Manufacturing with Shop Floor Excellence
The pathway to unparalleled manufacturing success is paved with the principles of Shop Floor Excellence.
For leaders who envision a future where every gear in their operation turns with precision and every employee contributes to a symphony of efficiency, the journey begins with SFE.
Unleashing the full potential of your manufacturing floor is not a distant dream—it’s a tangible reality that can be achieved by embodying the ethos of continuous improvement and operational harmony. When the focus shifts to cultivating a robust SFE culture, the benefits extend far beyond the shop floor, driving value, innovation, and competitive edge.
POWERS: The Blueprint for Operational Brilliance
At the heart of operational transformation lies the power of SFE. It’s the blueprint for turning challenges into opportunities and inefficiencies into strategic advantages. Integrating the 10 Pillars of SFE into your operation lays the foundation for a future where excellence is the norm, and every product that leaves your line is a testament to unmatched quality and craftsmanship.
The message is unequivocal for operation leaders poised to elevate their manufacturing capabilities: Adopting SFE is not optional—it’s imperative for sustained market leadership. Embrace the shift towards a culture prioritizing precision, engagement, and excellence. And for those ready to turn this vision into reality, our team is equipped to illuminate the path.
To begin your transformation and capitalize on the power of Shop Floor Excellence, reach out to our experts. Let’s discuss how SFE can redefine your production, enhance your profitability, and secure your position at the forefront of the industry.
Connect with us at +1 678-971-4711 or info@thepowerscompany.com to set the gears of excellence in motion today.
Continue Reading from this Mastery Series
- Part 1 - The Perils of Overlooking SFE in Assembly Line Setup
- Part 2 - A Lackluster Approach to Shop Floor Excellence Impacts Workforce Engagement —
- Part 3 - The Consequences of Sidestepping Data-Driven Decisions in Shop Floor Excellence
- Part 4 - Without Shop Floor Excellence, Product Quality Can Drop Like a Rock
- Part 5 - A Lack of Commitment to Shop Floor Excellence Can Lead to These 10 Safety Issues
- Part 6 - Shop Floor Excellence Makes Your Operation More Agile, Flexible, and Adaptable to Market Changes
- Part 7 - Bridging the Gap with Effective Communication in Shop Floor Excellence
- Part 8 - How Ignoring Shop Floor Excellence Undermines Continuous Improvement
- Part 9 - Tackling Inefficient Energy and Material Use with Shop Floor Excellence
- Part 10 - Enhancing Customer Focus Through Shop Floor Excellence