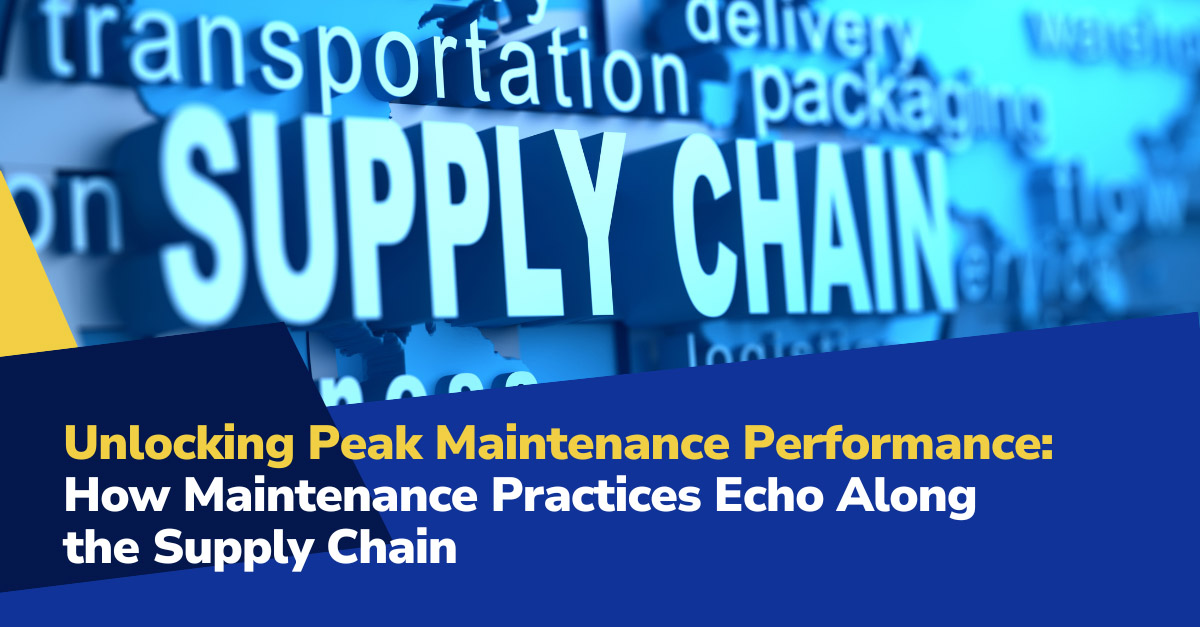
Return on Assets (ROA) stands as a critical barometer of operational efficiency and financial health in the intensely competitive manufacturing arena. It’s more than a number; it’s a reflection of how effectively a company uses its assets to generate profits. However, lurking in the background, often underappreciated, is the role of maintenance in shaping this vital metric. Poor or non-existent maintenance practices can significantly dent ROA. In the fifth article of our series, “Unlocking Peak Manufacturing Maintenance Performance,” we examine the top 10 ways maintenance standards and practices directly influence ROA in manufacturing.
Understanding ROA: Maintenance as a Financial Catalyst
ROA, calculated by dividing a company’s net income by its total assets, offers a clear window into how well its resources are being utilized to produce profits. In manufacturing, where assets predominantly include machinery and equipment, maintenance emerges as a pivotal player in preserving and maximizing these assets’ value.
Exploring the Top 10 Maintenance Factors Impacting ROA:
1Escalated Downtime Costs:
Subpar maintenance can increase unplanned downtime by 15-30%, translating to significant production hours losses. Each hour of downtime is an hour where assets are not generating revenue, directly lowering ROA.
2Soaring Repair and Replacement Expenditures:
Neglected maintenance often leads to a 50% rise in repair costs and a 30-50% increase in the frequency of equipment replacements. This inflates expenses and means diverting capital to replace assets rather than investing in growth opportunities.
3Diminished Equipment Efficiency:
When equipment isn’t maintained, its efficiency can drop by up to 20%. This decrease means assets are not being used to their full potential, negatively impacting production output and profitability.
4Quality Control Compromises:
A 10-20% increase in defect rates due to poor maintenance results in additional rework and quality control costs. These added expenses reduce the profit generated per asset, negatively affecting ROA.
5Safety-Related Financial Burdens:
A 10-20% rise in safety incidents due to poor maintenance can lead to expensive legal liabilities, compensation, and fines, all of which decrease net income and, thus, ROA.
6Elevated Energy Bills:
Inefficiently running machinery can consume up to 30% more energy, leading to higher operational costs. These increased costs reduce the profitability per asset.
7Inventory Management Disruptions:
Inaccuracies in inventory, heightened by 5-10% due to maintenance issues, can cause delays and additional costs, impacting the efficiency of asset utilization.
8Labor Cost Inflation:
A lack of proper maintenance can necessitate up to 30% more overtime labor, leading to increased wage expenses that reduce net income and ROA.
9Extended Production Cycle Times:
Poorly maintained equipment can prolong cycle times by 5-15%, leading to reduced throughput and less efficient use of assets.
10Regulatory Compliance Expenditures:
Maintenance lapses can increase non-compliance risk by 5-20%, potentially resulting in fines and operational stoppages that adversely affect profitability and asset utilization.
The POWERS Strategy:
Elevating ROA through Maintenance Excellence
At POWERS, we recognize that maintenance is not just about keeping equipment running; it’s about strategic asset optimization. Our Advanced Maintenance Performance (AMP) program is tailored to enhance your maintenance protocols, thereby improving ROA by ensuring that your assets are utilized efficiently and effectively.
Our comprehensive approach involves meticulously analyzing your current maintenance strategies and their impact on ROA.
We provide specialized training and strategic planning, focusing on enhancing your equipment’s efficiency, reliability, and lifespan. By optimizing these aspects, we aim to boost your net income and ROA, turning your maintenance operations into a key driver of financial success.
To discover how optimized maintenance can transform your company’s ROA, download our FREE Maintenance Assessment Guide. Embark on a journey towards maximizing asset value and bolstering your bottom line.
Contact the POWERS team at +1 678-971-4711 or email info@thepowerscompany.com for a comprehensive consultation to reshape how you view maintenance and asset management.
Continue Reading from this Mastery Series
- Part 1 - The Critical Link Between Maintenance and OEE
- Part 2 - How Maintenance Practices Shape Product Quality
- Part 3 - How Poor Maintenance Standards and Practices Impact Schedule Adherence
- Part 4 - How Maintenance Practices Echo Along the Supply Chain
- Part 5 - The Impact of Maintenance on Maximizing Return on Assets (ROA) in Manufacturing
- Part 6 - Poor Maintenance Practices Lead to Out-of-Control Operational Costs
- Part 7 - Navigating the Safety and Compliance Minefield in Manufacturing
- Part 8 - The High Cost of Overlooking Maintenance in Manufacturing Strategic Planning
- Part 9 - Poor Maintenance Practices Are a Hindrance to Technological Innovations
- Part 10 - Overcoming the ‘Reactive’ or ‘Run Till it Breaks’ Pitfall