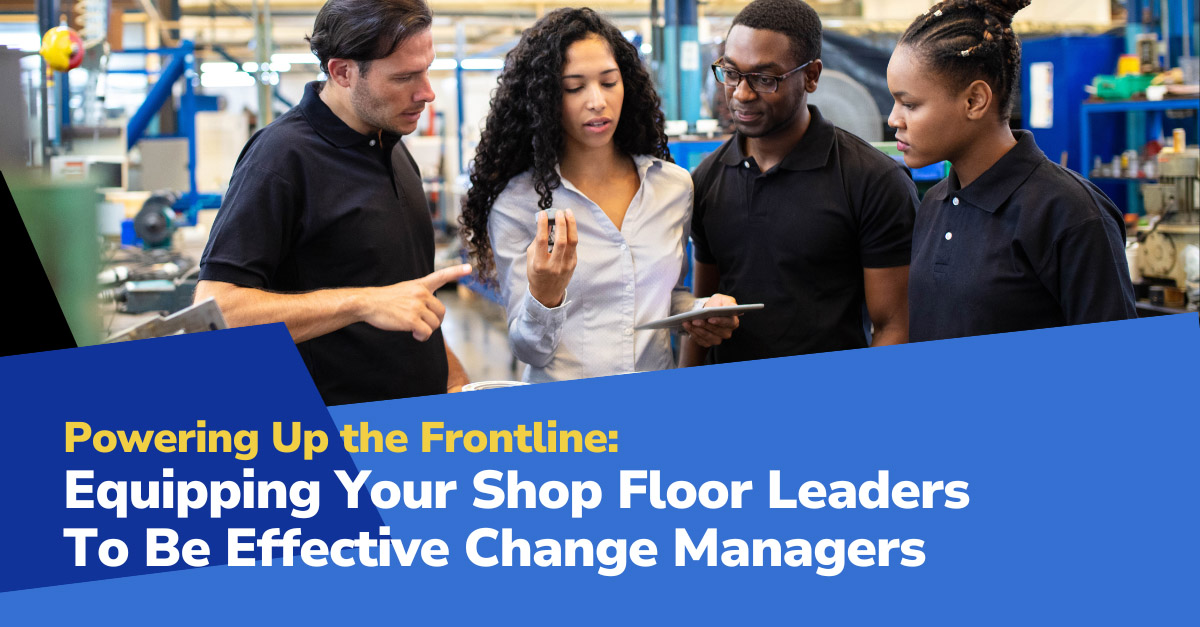
The manufacturing sector is in a perpetual state of flux, driven by technological advances, evolving market demands, and a dynamic global landscape.
For companies to not just survive but thrive in this environment, frontline managers and supervisors need to be adept change managers. The ripple effect is profound when these pivotal frontline leaders are equipped to usher in and manage change.
Change management in manufacturing refers to the structured approach and methodologies applied to transition individuals, teams, and processes from a current state to a desired future state. It encompasses strategies to help employees adapt to changes in the manufacturing environment, whether in technology, processes, or organizational structure.
Effective change management ensures that transitions are smooth, disruptions are minimized, and the desired benefits of the change are achieved, all while maintaining or improving operational efficiency.
It’s not just about navigating the choppy waters of transition but setting the sail toward unparalleled productivity and profitability.
Here are the top 10 gains awaiting manufacturers who empower their frontline to champion change:
1Seamless Process Integration:
By effectively managing change, frontline leaders can ensure that new processes and technologies are integrated seamlessly into the existing workflow. This results in fewer interruptions and a smoother operational cadence.
2Reduced Resistance to New Technologies:
Frontline managers skilled in change management can facilitate the adoption of innovative technologies. They can address concerns and ensure that their teams transition effectively, leading to faster returns on technological investments.
3Optimized Resource Allocation:
Change often requires a shift in resource allocation. Proficient change managers can foresee these requirements, ensuring resources are deployed where they are most impactful, thus maximizing productivity.
4Enhanced Employee Morale:
Changes can be unsettling for the workforce. Effective change management ensures transparent communication, alleviating anxieties and fostering a positive work environment, directly boosting productivity.
5Shorter Adjustment Periods:
Frontline managers trained in change management can expedite the adjustment phase. This means the organization reaches its optimal productivity levels post-change much quicker.
6Cost Savings:
Poorly managed change can be costly due to mistakes, delays, and resistance. By mitigating these challenges, proficient change managers can lead to significant cost savings.
7Greater Flexibility and Adaptability:
Equipped frontline managers ensure the manufacturing unit is not just reactive but proactive. They can anticipate market shifts and adjust swiftly, granting the manufacturer a competitive edge.
8Improved Quality Control:
Change can lead to quality enhancements, primarily when related to new technologies or processes. By effectively managing these changes, frontline leaders can ensure that quality improvements are realized and sustained.
9Risk Mitigation:
Every change comes with inherent risks. Skilled change managers can identify, assess, and mitigate these risks, ensuring that the transition does not compromise safety or operational integrity.
10Strengthened Stakeholder Trust:
Effective change management, driven by frontline leaders, builds trust among stakeholders, from employees to investors. This trust can lead to enhanced collaboration, investment, and customer loyalty.
Conclusions for Senior Leaders
The frontline of any manufacturing unit is its heartbeat, setting the rhythm for the entire operation. In a world where change is the only constant, the ability of this frontline to adapt, evolve, and lead change is pivotal.
Senior leaders have a profound role to play here – empowering their frontline managers with the tools, training, and trust to be effective change managers. In doing so, they’re not just equipping them to handle the challenges of today but setting the stage for the manufacturing triumphs of tomorrow.
The POWERS Difference
We are a dedicated and results-driven manufacturing productivity consulting firm uniquely positioned at the intersection of managing people and improving performance.
We partner with growth-oriented organizations to cultivate a work environment of innovation and excellence that fuels productivity, drives efficiency, strengthens competitive advantage, and fuels profitability.
One of the critical areas in which we enhance productivity is our focus on frontline leadership development.
Leveraging our deep industry expertise and innovative methodologies, we build synergies between people and processes, creating holistic, sustainable change that translates into measurable business outcomes.
Our team has helped executive leadership across many industries engage and develop their frontline supervisors and managers for rapid, sustainable, scalable performance improvement, increased competitive advantage, greater value, and a more robust bottom line.
To put our experienced team and proven track record to work for you, schedule an initial discovery and analysis by calling +1 678-971-4711 or emailing us at info@thepowerscompany.com.
Continue Reading from this Mastery Series
- Part 1 - Strategic Alignment that Bridges Daily Tasks with Broader Visions for Unified Organizational Success
- Part 2 - Crafting Clarity through Effective Communication and Active Listening
- Part 3 - Sharpening Decision-Making Prowess for Seamless Operations and Minimal Downtimes
- Part 4 - Championing Lean Principles for Streamlined Success and an Ever-Evolving Workplace
- Part 5 - Mastering Performance Management for Optimal Team Output and Growth
- Part 6 - How Leaders Well-Trained in the Soft Skills Transform Manufacturing Teams
- Part 7 - Strengthening Conflict Resolution Skills for Peak Productivity and Profitability Gains
- Part 8 - Unleashing Potential with Precision Time and Resource Management
- Part 9 - Safety First for Sustainable And Scalable Productivity And Profitability
- Part 10 - Equipping Your Shop Floor Leaders to Be Effective Change Managers