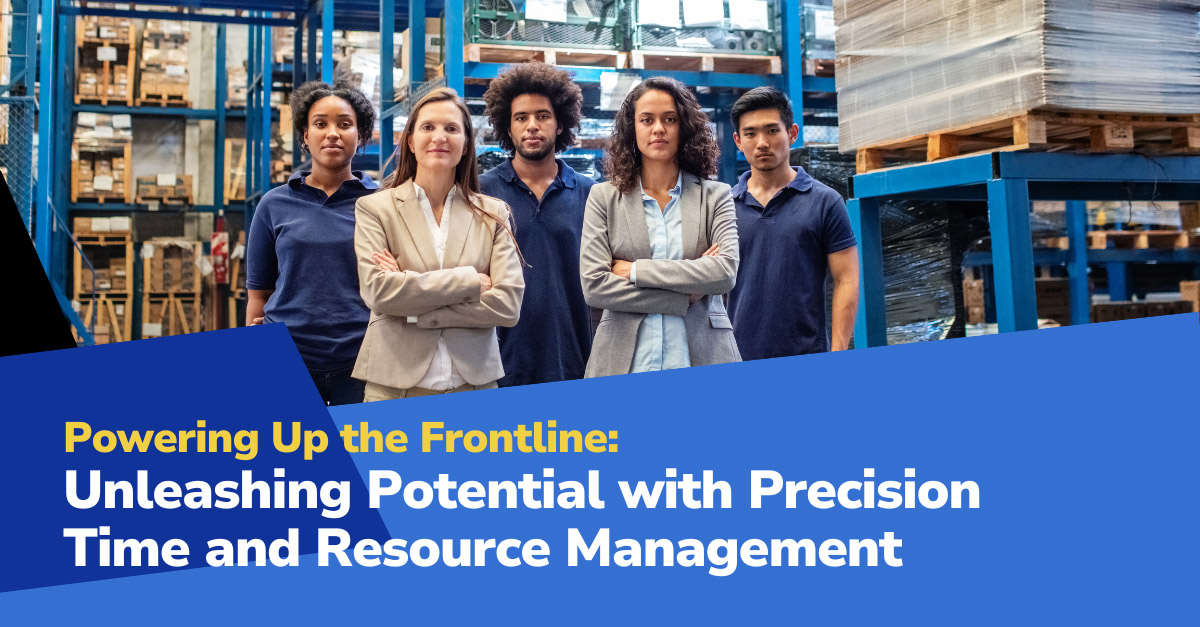
In the fast-paced world of large-scale manufacturing, every second counts, and every resource is invaluable. The industry's frontrunners recognize that the backbone of their success lies not just in the machines they employ or the technologies they adopt but in the seamless orchestration of time and resource allocation.
By equipping your frontline leaders with the skills to master this delicate balancing act and safeguard their production timelines, you can carve a pathway to unparalleled productivity and profitability.
With this backdrop, let’s dive into the top 10 productivity and profitability gains these manufacturers can tap into by optimizing time and resource management.
1Increased Throughput:
Efficient time management and resource allocation can boost the production line’s manufacturing rate and move products through the production line, leading to higher output in shorter time frames.
2Cost Savings:
Proper allocation of resources can lead to reduced waste, meaning fewer resources are squandered or underutilized. This directly translates to significant cost savings.
3Shorter Lead Times:
Efficient time management can result in quicker turnarounds for product orders, ensuring that customers receive their products faster and enhancing customer satisfaction.
4Enhanced Machine Utilization:
Effective allocation of resources ensures that machinery and equipment are used to their full potential, reducing idle times and prolonging the lifespan of the machines.
5Reduced Overtime Costs:
By managing schedules efficiently, manufacturers can reduce the need for employees to work overtime, leading to decreased labor costs.
6Optimized Inventory Levels:
Efficient resource allocation can lead to just-in-time production and reduced inventory holding costs. Manufacturers can minimize overstock or stockouts, leading to optimized inventory levels.
7Improved Quality Control:
By allocating adequate time and resources to quality checks, manufacturers can ensure higher product quality, reducing defects, returns, and associated costs.
8Enhanced Scalability:
With optimized time and resource management, large-scale manufacturers are better poised to scale their operations up or down based on market demand, ensuring flexibility and agility.
9Increased Profit Margins:
Reductions in wasted resources, unnecessary overtime, and inefficiencies can lead to cost savings and increased revenues, thus boosting overall profit margins.
10Higher Employee Morale and Productivity:
An efficiently managed work environment reduces stress and burnout. Employees who have clarity on schedules and resource availability are more motivated, leading to higher productivity and job satisfaction.
Conclusions for Senior Leader
In essence, for large-scale manufacturers, the meticulous management of time and resources is not just about maintaining the status quo but about unlocking significant gains in productivity and profitability.
The POWERS Difference
We are a dedicated and results-driven manufacturing productivity consulting firm uniquely positioned at the intersection of managing people and improving performance.
We partner with growth-oriented organizations to cultivate a work environment of innovation and excellence that fuels productivity, drives efficiency, strengthens competitive advantage, and fuels profitability.
One of the critical areas in which we enhance productivity is our focus on frontline leadership development.
Leveraging our deep industry expertise and innovative methodologies, we build synergies between people and processes, creating holistic, sustainable change that translates into measurable business outcomes.
Our team has helped executive leadership across many industries engage and develop their frontline supervisors and managers for rapid and sustained performance improvement, increased competitive advantage, greater value, and a stronger bottom line.
To put our experienced team and proven track record to work for you, schedule an initial discovery and analysis by calling +1 678-971-4711 or emailing us at info@thepowerscompany.com.
Continue Reading from this Mastery Series
- Part 1 - Strategic Alignment that Bridges Daily Tasks with Broader Visions for Unified Organizational Success
- Part 2 - Crafting Clarity through Effective Communication and Active Listening
- Part 3 - Sharpening Decision-Making Prowess for Seamless Operations and Minimal Downtimes
- Part 4 - Championing Lean Principles for Streamlined Success and an Ever-Evolving Workplace
- Part 5 - Mastering Performance Management for Optimal Team Output and Growth
- Part 6 - How Leaders Well-Trained in the Soft Skills Transform Manufacturing Teams
- Part 7 - Strengthening Conflict Resolution Skills for Peak Productivity and Profitability Gains
- Part 8 - Unleashing Potential with Precision Time and Resource Management
- Part 9 - Safety First for Sustainable And Scalable Productivity And Profitability
- Part 10 - Equipping Your Shop Floor Leaders to Be Effective Change Managers