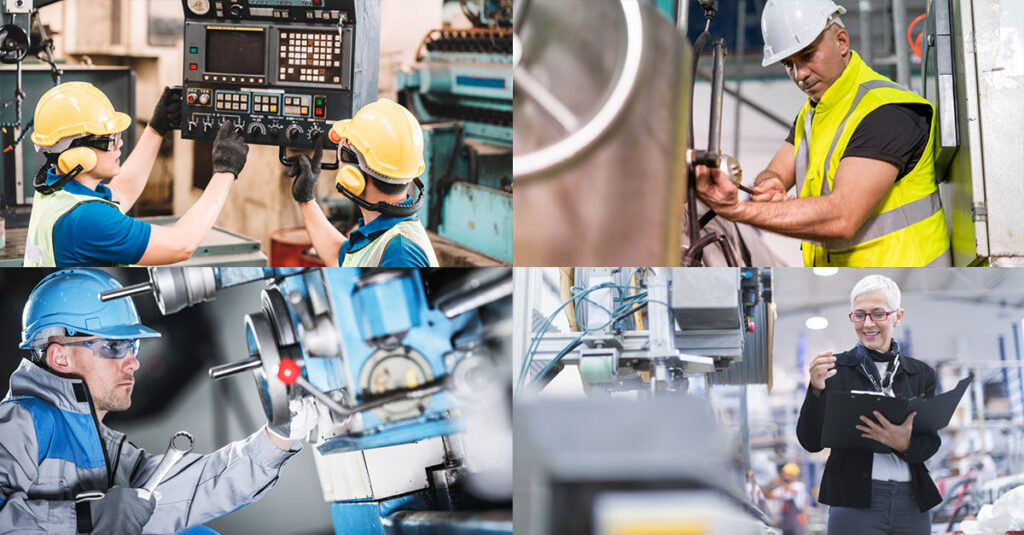
Maintenance, Repair, and Operations (MRO) has become pivotal in determining a company’s productivity and bottom-line performance in today’s rapidly evolving manufacturing environment. A healthy approach to MRO can pay massive dividends in your OEE (Overall Equipment Effectiveness).
As a leader in improving productivity for our manufacturing clients, POWERS has been focusing on bridging the gap between workplace culture and operational performance. A critical impact area for us is improving maintenance performance.
In this article, we’ll explore the top five things you can start today to improve your maintenance department, concentrating on fundamentals like Total Productive Maintenance (TPM), enhancing scheduling, labor and overtime hours, efficiency, and cost reduction. The net result? Improved uptime, throughput, capacity utilization, and profitability.
But first, let’s look at the different approaches typical to manufacturing maintenance. Before you can even build a plan to improve, it’s essential to understand where you’re at now.
Are you running your lines until they break? How’s your scheduling and staffing? Have you fully integrated maintenance with the entirety of your operation? Wherever you are, you can begin improving today.
Maintenance Approaches Compared
1Reactive Maintenance: Wait for It to Break
Reactive maintenance or the “run-to-failure” method is simple – you fix things when they break. Though this ‘when it breaks, we’ll fix it’ approach requires less planning, it can lead to unpredictable downtime, affecting productivity and increasing costs. It’s suitable for non-critical systems but not a good fit for mission-critical manufacturing processes.
2Preventive Maintenance: Scheduled Care
Preventive maintenance involves scheduling replacements at regular intervals before parts break. This approach can improve reliability but might lead to unnecessary replacements. A more systematic approach, such as TPM, integrates preventive maintenance with initiatives like continuous improvement and employee involvement to enhance efficiency.
3Usage-Based Maintenance: Time for a Change
Usage-Based maintenance is about replacing parts based on the machine’s usage. It offers a more tailored solution than preventive maintenance but requires accurate tracking of usage hours, and it might not account for unexpected failures.
4Condition-Based Maintenance: Detect and Respond
This approach replaces parts based on wear and tear. Continuously monitoring the equipment’s condition allows timely intervention, reducing unexpected downtime. It emphasizes real-time feedback, aligning well with POWERS’ focus on aligning culture and operational performance.
5Predictive Maintenance: Forecasting Failures
Predictive maintenance leverages historical data, often using AI and machine learning, to predict when a part will break. It effectively reduces downtime and costs, making it a suitable strategy for modern, data-driven manufacturing environments.
6Prescriptive Maintenance: Analyze, Predict, and Prescribe
The most advanced form, prescriptive maintenance, goes beyond predicting failures. Using sophisticated data analysis, it provides hypothetical outcomes to choose the best action, considering safety, quality, and timing of implementation.
Five Things to Start Today for a Better Maintenance Department
1Implement Total Productive Maintenance (TPM)
Total Productive Maintenance emphasizes the integration of maintenance with daily operations and production schedules. By encouraging employees to take ownership and become involved in maintaining equipment:
- Employee Training: Train and develop employees, especially your frontline leaders, to understand and recognize potential issues with machinery. Bridge any tactical or technical maintenance skills gaps. Encourage cross-training to create a versatile team that can identify and respond to maintenance needs.
- Create Maintenance Teams: Establish dedicated maintenance teams with a mix of specialists and generalists, ensuring that someone with the right expertise is always on hand.
- Continuous Improvement: Embed continuous improvement into the maintenance culture, routinely assessing procedures and performance and adapting to evolving needs and opportunities.
2Improve Scheduling and Coordination
Proper scheduling and coordination can drastically improve efficiency and reduce downtime:
- Utilize Scheduling Software: Implement scheduling software to create a real-time shared calendar that aligns with production timelines, helping to avoid conflicts.
- Encourage Communication: Foster collaboration between the maintenance and production teams to ensure everyone understands maintenance schedules and requirements.
- Review and Adjust: Regularly review scheduling effectiveness and adjust as needed to accommodate unexpected changes and improvements.
3Monitor Labor and Overtime Hours
Effective labor management leads to a more productive maintenance department:
- Track Overtime: Keep a close eye on overtime hours to understand if the current staffing levels are aligned with needs.
- Develop Shift Strategies:Consider various shift strategies to ensure coverage while providing rest and avoiding burnout.
- Analyze Performance:Analyze individual and team performance to identify areas where additional training or adjustments in scheduling might be needed.
4Evaluate Efficiency and Cost Reduction Opportunities
Cost reduction and efficiency are at the core of any successful maintenance strategy:
- Regular Audits: Conduct regular audits of the maintenance department to identify waste, inefficiencies, or opportunities for cost reduction.
- Implement Lean Practices: Consider applying Lean principles to streamline processes, reduce waste, and enhance overall efficiency.
- Invest in Quality Tools:Investing in the right tools and technology can improve the speed and quality of maintenance activities, leading to long-term cost savings.
5Integrate Technology Wisely
The wise integration of technology can transform maintenance operations:
- Implement IoT Sensors: Internet of Things (IoT) sensors can provide real-time data on equipment, helping in predictive and condition-based maintenance strategies.
- Utilize AI and Machine Learning: Use artificial intelligence (AI) and machine learning for predictive and prescriptive maintenance, leveraging vast amounts of data to make accurate predictions and suggest optimal solutions.
- Invest in Training:Ensure your team is well-trained in using new technology to avoid implementation challenges or resistance.
Conclusions for Business Leaders
Maintenance in manufacturing is no longer a side activity; it’s a strategic function that impacts overall productivity and profitability. Manufacturers can create a maintenance department aligned with organizational goals that delivers tangible financial benefits by understanding different approaches to maintenance and adopting practices like TPM, improved scheduling, labor management, and smart use of technology.
POWERS partners with manufacturers to build these connections, focusing on continuous improvement, workforce engagement, and strategic alignment. With our customized AMP (Advanced Maintenance Performance) solutions, manufacturers can transform their maintenance departments into a robust, efficiency-driven component of their success. Reach out to us at www.thepowerscompany.com to learn more.
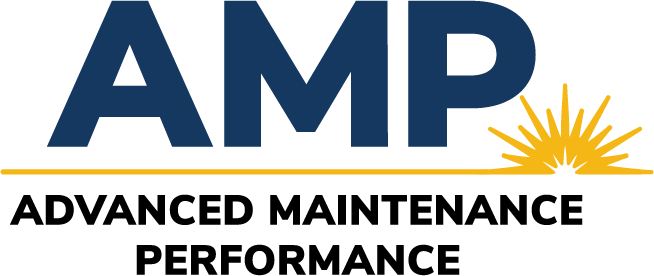
The POWERS Difference: AMP Up Your Maintenance Performance
Enhancing manufacturing operational performance is an intricate process that demands a comprehensive examination of the interwoven systems, processes, and behaviors that constitute the very core of an organization. It requires a keen eye that extends from the high-level strategic inputs to the tangible outputs, connecting executive decisions on the top floor with the day-to-day mechanics of the shop floor.
Among the myriad factors that drive an organization’s success, one critical aspect that stands prominently on the improvement agenda is the MRO, or Maintenance, Repair, and Operations. This segment is where inefficiencies and lapses can significantly erode the bottom line, making it a pivotal focus area for any operation aiming to enhance its financial and functional robustness.
Recognizing this critical need, we have embarked on a journey to offer a comprehensive solution to uplift maintenance performance. Our newly launched AMP (Advanced Maintenance Performance) Program is meticulously designed to rejuvenate both the tactical and technical dimensions of your maintenance operations.
Tactical Excellence
The tactical facet of our AMP Program emphasizes refining your strategic approach to maintenance. We dive deep into your Maintenance Management Operating System, optimizing how you leverage human resources and other assets dedicated to maintaining your essential equipment. By aligning strategies and fine-tuning processes, we ensure that your maintenance operations are not merely reactive but proactive and strategic, fostering resilience and efficiency.
Technical Mastery
Alongside the tactical improvements, our program accentuates the technical competencies required to maintain operational excellence. Our hands-on training encompasses vital areas such as Maintenance Fundamentals, Mechanical Concepts, Electrical Power, and Electrical Control.
Considering that nearly 60% of today’s manufacturing maintenance workforce might lack the requisite skills to keep assets and equipment at peak functionality, our program acts as a vital catalyst. By enhancing your maintenance team’s expertise, we unlock the barriers that hinder Overall Equipment Effectiveness (OEE), allowing for improved uptime, throughput, capacity, quality, and more.
Our AMP Program is not just a solution; it’s a transformational pathway designed to turn your maintenance department into a powerhouse of efficiency and effectiveness. We believe in empowering your team with the right tools, knowledge, and strategies to ensure that maintenance becomes a driving force of value rather than a cost center. Join us in this transformative journey and unlock the full potential of your maintenance operations.
To put our experienced team and proven track record to work for you, schedule an initial discovery and analysis by calling +1 678-971-4711, or emailing us at info@thepowerscompany.com