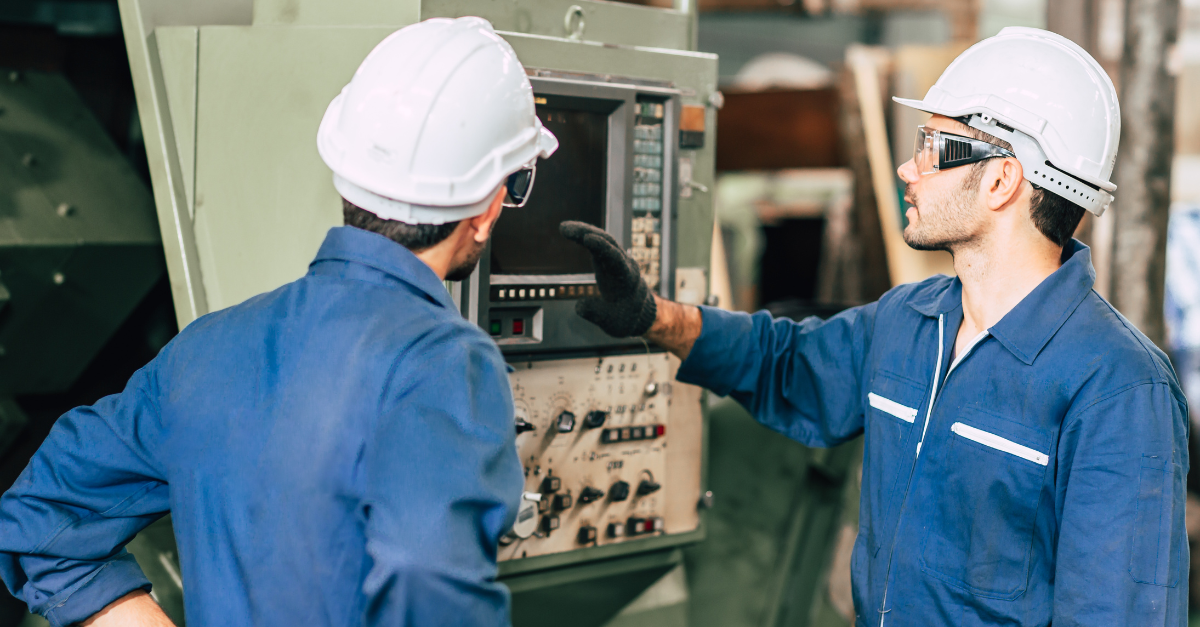
Improving OEE, ROA, equipment reliability, quality, and production uptime requires a systematic and proactive approach to maintenance. Here are 7 steps to improve maintenance performance and drive productivity and profitability.
Maintenance performance is a critical factor that impacts a manufacturing business’s overall productivity and profitability. Effective maintenance practices can improve Overall Equipment Effectiveness (OEE), Return on Assets (ROA), equipment reliability, product quality, and production uptime. Conversely, poor maintenance practices can lead to decreased performance in these critical production metrics and negatively impact the productivity and profitability of the business.
To understand the impact of maintenance performance, it is crucial to understand the key maintenance metrics that drive productivity and profitability in a manufacturing setting: OEE, ROA, reliability, quality, and uptime.
What is OEE (Overall Equipment Effectiveness) in Manufacturing?
Overall Equipment Effectiveness (OEE) is a performance metric used in manufacturing to evaluate the efficiency of equipment and processes. It measures the degree to which manufacturing assets are being utilized to produce high-quality products at maximum output with minimal waste or downtime.
OEE is calculated using three factors: Availability, Performance, and Quality. Availability measures the amount of time the equipment is running versus the total time it is available. Performance measures the rate at which the equipment is producing products compared to the theoretical maximum. Finally, quality measures the number of products produced that meet the required standards compared to the total number of products produced.
The formula for calculating OEE is: (Availability %) x (Performance %) x (Quality %) = OEE
For example, (Availability= 83.3%) x (Performance=87.2%) x (Quality=90.7%) = OEE=65.9%
Each of the three components of the OEE (Availability, Performance, Quality) points to an aspect of the process that can be targeted for improvement. OEE may be applied to any individual work center or rolled up to department or plant levels. Measuring OEE also allows for drilling down for very specific analysis, such as a particular part, shift, or any other parameters. It is unlikely that any manufacturing process can run at 100% OEE. Many manufacturers benchmark their industry to set a challenging target. 85% is not uncommon.
Manufacturers use OEE to identify areas where productivity can be improved, and waste can be reduced. It is a valuable tool for continuous improvement, allowing companies to set performance targets and track progress toward those targets over time. OEE can also identify which equipment and processes are most effective and efficient, allowing companies to allocate resources to areas with the highest return on investment.
What is ROA (Return on Assets), and How is it Used to Determine Business Financial Health?
Return on Assets (ROA) is a financial metric used to measure a company’s profitability in relation to its total assets. ROA is calculated by dividing the company’s net income by its total assets. The resulting percentage shows how efficiently a company uses its assets to generate profits.
ROA is a significant financial metric for manufacturing businesses because it can help gauge the business’s overall health. A higher ROA indicates that a company is using its assets more effectively to generate profits, while a lower ROA may suggest that the company is not using its assets efficiently and may need to improve its operations.
ROA can be a particularly useful metric for manufacturing businesses because manufacturing operations typically require significant investments in assets such as machinery, equipment, and inventory. By measuring the return on these assets, companies can evaluate the effectiveness of their manufacturing operations and identify areas where they can improve efficiency and profitability.
For example, investors or analysts may compare the ROA of one manufacturing business to that of another to determine which company is performing better.
It’s important to note that ROA is just one of many financial metrics used to evaluate the performance of manufacturing businesses. Other metrics may include gross margin, operating margin, and return on investment (ROI). Each of these metrics provides a different perspective on the financial health of a business and can be used in conjunction with ROA to better understand a company’s performance.
Overall, ROA is a valuable financial metric for manufacturing businesses that can help them evaluate their profitability and identify areas for improvement. By tracking ROA over time and comparing it to industry benchmarks, manufacturing businesses can ensure that they are using their assets efficiently and operating in a financially sustainable manner.
What is Equipment Reliability, and How Does it Impact a Manufacturing Business?
Equipment reliability measures how often manufacturing equipment functions as intended without failure or breakdown. It is vital to ensure consistent production output and that product quality is maintained. In addition, a reliable manufacturing operation can minimize downtime, reduce maintenance costs, and increase efficiency, which can positively impact a business’s overall financial performance.
Measuring equipment reliability typically involves tracking data such as the frequency and duration of equipment failures, the number of repairs required, and the overall uptime of equipment. One commonly used metric for measuring equipment reliability is Mean Time Between Failures (MTBF), which is the average time between equipment failures. Another metric is Mean Time to Repair (MTTR), the average time required to repair equipment after a failure.
Equipment reliability is critical for manufacturing businesses because equipment failures can result in unplanned downtime, which can have significant financial consequences. Downtime can cause delays in production schedules, reduce productivity, and increase costs associated with maintenance and repairs. In addition, equipment failures can lead to lower product quality, customer complaints, and lost revenue.
In contrast, a reliable manufacturing operation can reduce the risk of downtime and the associated costs. Equipment reliability can also improve production efficiency by reducing frequent repairs and maintenance, freeing up resources, and improving overall operational performance. This, in turn, can result in increased production capacity and faster time to market, which can positively impact the financial performance of a business.
Improving equipment reliability can involve several strategies, including preventive maintenance, predictive maintenance, and continuous improvement.
Preventive maintenance involves conducting regular maintenance activities on equipment to prevent failures before they occur. Predictive maintenance involves using data and analytics to predict when equipment failures are likely to occur, allowing for proactive maintenance and repair activities. Finally, continuous improvement involves identifying and addressing the root causes of equipment failures to improve overall reliability over time.
Overall Maintenance Performance Can Have a Significant Effect on Quality
In a manufacturing setting, quality measures how well a product meets the established standards and specifications for design, performance, reliability, safety, and other attributes. Quality is critical in manufacturing because it directly impacts customer satisfaction, product reliability, and the business’s reputation.
Quality in manufacturing can be achieved through various techniques, including quality control, quality assurance, and continuous improvement.
Quality control involves monitoring and inspecting products during and after production to ensure they meet established quality standards.
Quality assurance involves setting quality standards and processes to ensure that products consistently meet these standards. Finally, continuous improvement involves analyzing data and feedback to identify areas for improvement and implement changes to improve product quality.
Manufacturing businesses use various quality metrics to measure and evaluate product quality. These metrics include defect rates, scrap rates, rework rates, and customer satisfaction rates. Defect rates measure the number of defective products produced compared to the total number of products produced. Scrap rates measure the amount of material wasted during production due to defects or other issues. Rework rates measure the time and resources required to correct product defects. Customer satisfaction rates measure how well the product meets customer expectations.
Manufacturing businesses strive to achieve high levels of product quality to ensure customer satisfaction and maintain a competitive advantage in the market. Quality is essential not only for meeting customer expectations but also for ensuring the safety and reliability of the product. In addition, a product with high levels of quality can help a manufacturing business build a strong brand reputation and establish a loyal customer base.
Product Quality can be Adversely Impacted by Poor Maintenance Performance in Several Ways.
1Increased Downtime:
2Reduced Productivity:
3Increased Scrap and Rework:
4Safety Issues:
5Inconsistent Quality:
Uptime is Another Critical Measure of Maintenance Performance
Uptime measures how long manufacturing equipment or systems are operating and available for production. It is typically expressed as a percentage of the total time that the equipment or system is available for use. Uptime is an essential metric for manufacturing performance, productivity, and profitability because it measures the effectiveness of the manufacturing process and the ability to produce products as efficiently as possible.
High uptime is desirable in manufacturing because it indicates that the equipment or systems are operating efficiently and effectively, which can result in higher production volumes and better-quality products. On the other hand, low uptime can indicate that the equipment is not functioning as efficiently or effectively as it could, resulting in lower production volumes and reduced profitability.
Uptime is often used with other manufacturing metrics, such as overall equipment effectiveness (OEE), which combines availability, performance, and quality: all measures to determine the manufacturing process’s overall efficiency. Uptime can also be used to track the performance of individual equipment or systems, allowing manufacturers to identify areas for improvement and allocate resources accordingly.
Manufacturing companies can use strategies such as preventive maintenance, predictive maintenance, and continuous improvement to improve uptime. Preventive maintenance involves conducting regular maintenance activities on equipment to prevent failures before they occur. Predictive maintenance involves using data and analytics to predict when equipment failures are likely to occur, allowing for proactive maintenance and repair activities. Finally, continuous improvement involves identifying and addressing the root causes of equipment failures to improve overall reliability over time.
Improve Your Maintenance Performance and Improve the Financial Health of Your Business
Improving OEE, ROA, equipment reliability, quality, and production uptime requires a systematic and proactive approach to maintenance. Manufacturers can take the following steps to improve their maintenance performance and drive productivity and profitability:
1Implement a proactive maintenance program:
2Invest in maintenance training:
3Implement a maintenance management system:
4Promote a continuous improvement culture:
5Collaborate with suppliers and partners:
6Invest in technology:
7Measure and track performance:
Conclusions for Business Leaders
Maintenance performance is a critical factor that impacts a manufacturer’s overall productivity and profitability. By implementing a proactive maintenance program, investing in maintenance training, implementing a maintenance management system, promoting a culture of continuous improvement, collaborating with suppliers and partners, investing in technology, and measuring and tracking performance, manufacturers can improve their maintenance performance and drive productivity and profitability.
POWERS AMP (Advanced Maintenance Performance) Program
Our POWERS AMP (Advanced Maintenance Performance) Program improves both the tactical and technical aspects of maintenance in your operation. On the tactical side, we focus on improving your strategic approach to maintenance and your Maintenance Management Operating System: how you manage the people and resources devoted to maintaining your assets and equipment.
We also focus on the technical aspects of maintenance and provide hands-on training in Maintenance Fundamentals, Mechanical Concepts, Electrical Power, and Electrical Control.
Nearly 60% of the current manufacturing maintenance workforce does not possess the skills and training necessary to keep the assets and equipment functioning at optimum levels. Improving your maintenance team’s skills unlocks OEE (Overall Equipment Effectiveness) bottlenecks in uptime, throughput, capacity, quality, and more.
The POWERS Difference
At POWERS, we focus on Leadership Engagement and Development to transform operational performance and prepare your leaders for the future. We help you build a performance culture that operates at peak levels to lower costs, increase productivity, build agility, and sustain that performance over the long haul.
Our team has helped executive leadership across many industries operationalize their culture for rapid and sustained performance improvement, increased competitive advantage, greater value, and a stronger bottom line.
Find out about our new AMP (Advanced Maintenance Performance) Program and put our experienced team and proven track record to work for you. Schedule an initial discovery and analysis by calling +1 678-971-4711 or emailing us at info@thepowerscompany.com.