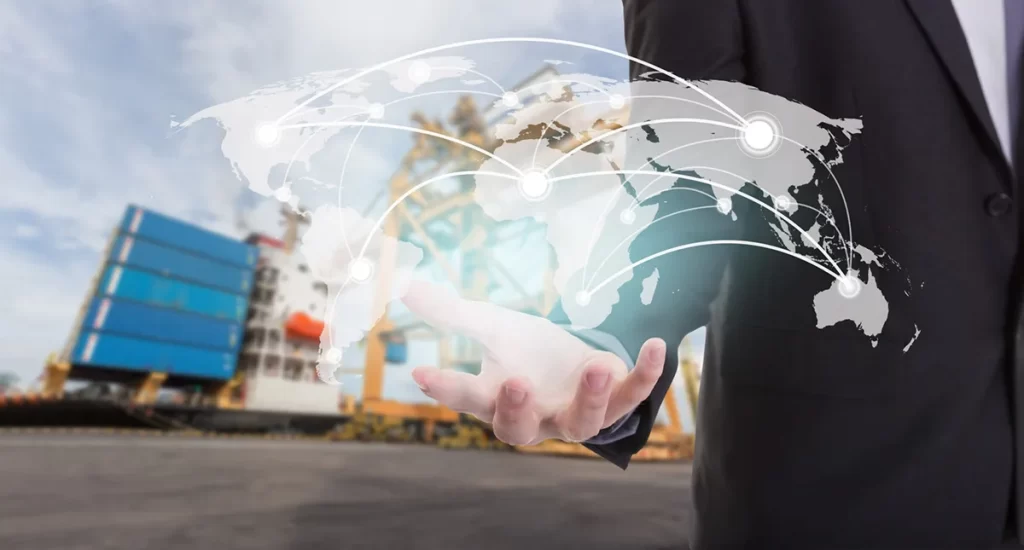
“The Covid-19 coronavirus has been a huge wake-up call. Businesses that had considered their supply chains to be resilient suddenly found out that they weren’t.”
Omera Khan
Professor of Supply Chain Management at Royal Holloway, University of London
Knowing your organization’s supply chain inside and out is no longer an option, but a mandate. Though many companies worldwide have made efforts to make supply chains more resilient in recent years, most did not factor a pandemic into their strategies and thus realized that they were not nearly as resilient as they thought. The Covid-19 outbreak upped pressure for supply chains on several fronts at once, from extreme demand spikes, extreme demand drops, sudden raw-material and parts-supply disruptions, and sudden labor force shortages due to risk of infection.
Unfortunately, some manufacturers took advantage of this, and Americans witnessed shortages of — and price gouging/profiteering on — protective household and medical products from disinfectant wipes to face masks. Now, 10 months into the pandemic and a spotlight on how demand spikes can lead to unfair practice and abuse, many consumers are looking at who and where they buy their products in a more critical and meaningful light.
Beyond the pandemic, increased interest in workplace diversity/inclusion, ethical human rights practices, and climate change and sustainability concerns have many consumers keeping their eye out to see how industries and companies around the world will start to more closely examine the cause-and-effect roles they play. According to Avery Dennison’s Market Insight Report, 67% of global C-Suite & Senior Leadership believe their customers actively consider or concern themselves with supply chain operations.
So, what can be learned from the Covid crisis to help your company to achieve more resilience? The most important, timely need is more transparency throughout the global supply chain, meaning visibility on a multi-tier scale. Most supply chains extend beyond 3-4 tiers, and it is extremely important for companies to understand who these suppliers are, where they are located, where they source from, company practices, and so on.
Beyond customer concerns, a better understanding of your supply chain means improved compliance with your own company policies and values. It can also reveal ways to operate more efficiently and cost-effectively. Last week, we offered recommendations on how to reevaluate your manufacturing processes as the pandemic continues. This week we’d like to offer ways your company can build resilient supply chains through better transparency practices during Covid and beyond.
Identify and Visualize Risks
The risk profile/vulnerability of a supply chain is generally assessed and cemented within the early stages of strategy development. Ensuring that the processes to achieve supply chain transparency and regular monitoring are embedded early on is a good, effective practice.
A reliable method of identifying and prioritizing supply chain risks is using Failure Modes and Effects Analysis scoring system. This will help your team assess risk severity, likelihood, frequency and detection.
Next step, you should create a visual depiction of product flow in terms of volume. The visualization should clearly convey any potential vulnerabilities or information gaps based on flow volumes and potential supply risks related to geographic areas all along your supply chain.
“The coronavirus pandemic has demonstrated to governments – yet again – how supply chains are vulnerable to far-away events in far-away places. Going forward, businesses can expect both regulatory and social pressure to ensure that they are more resilient to such shocks, with stocks maintained of critical products.”
Stephan Freichel
Professor of Distribution Logistics at Köln University of Applied Sciences
Shifting to Technology that Provides Holistic Data
Alexis Bateman, research scientist and director of MIT Sustainable Supply Chains at the MIT Center for Transportation and Logistics, defines Visibility as “accurately identifying and collecting data from all links in your supply chain.”
Transitioning out of the pandemic, companies of all sizes will face pressure to disclose data to the public that will allow stakeholders to hold them accountable. The only way to gain sufficient visibility over supply chains to meet these needs is through digitization. Enterprises need to be able to track and analyze supplier activity. Digitizing the connection between buyers and sellers enables companies to more effectively map out risks and gives them greater flexibility to pinpoint and onboard alternative providers should a key link in the chain come under pressure.
Digitizing supply-chain management will also improve the speed, accuracy, and flexibility of your processes. Being able to point back to a single “source of truth” will strengthen capabilities in anticipating risk, achieve greater visibility and coordination across the supply chain, and help your organization manage issues that arise along the way.
Improve Supplier Relationships
Post-covid, companies will need to reevaluate their supply chain risks and may need to redefine their supplier relationships. In the past, cost has been the primary driver for choosing suppliers. Moving forward, there will need to be a more refined cost/risk analysis that factors in transparency. This will be required for achieving “true” supply chain resilience and may include paying higher costs for local suppliers.
While technology and digitization will play a significant role in helping organizations gain transparency into factors like suppliers’ inventory, reliability, and speed, some aspects of improving visibility will rely on forming stronger relationships with suppliers.
As your company’s teams begin building relationships with suppliers, they can ask specific questions on pressing consumer issues — like sustainability, quality, labor ethics, COVID-19 compliance, etc. — with suppliers, rather than simply ordering from a company where you have no insight into their operations. And, as a bonus, as you build further trust with your vendors, they might become more forthright with any challenges they’re facing on their end. This will help both parties work out a solution before it escalates and affects operations.
For example, your data might not display any issues with your suppliers hitting their targets, but a supplier could be struggling to keep up internally. If they feel they can be transparent with you, they will raise the issue more readily, and you might be able to work out an arrangement such as reducing order sizes and spreading out delivery windows. This would likely be a better alternative to consumers receiving rushed orders with reduced quality.
“We are moving from an era marked by an emphasis on procurement for cost,
to an era marked by an emphasis on procurement for resilience.”
Richard Wilding
Professor of Supply Chain Strategy, Cranfield School of Management
Supply chain transparency not only helps your company maintain safety and quality requirements, but it also minimizes risks and builds customer confidence, which is more important than ever as we move through our new normal. While companies have a lot of options and resources when it comes to deciding how to improve transparency, it’s unlikely that they’ll be able to continue doing business per the status quo if they want to achieve resiliency.
At Powers, we recognize the need for manufacturers and supply chain workers not only to respond quickly to the challenges brought on by the COVID-19 crisis, but to also be prepared to normalize production when crises wane. Which is why we have implemented the Optimized Start-Up Program; a low-cost, high-value solution that enables your organization to deploy a small crew of industry trained experts and front-line leadership strategists to assist your team with an efficient and effective startup of new or existing production operations within your facility or factory.